Types and Applications of mold components
Mold components are essential tools used in the production of molded parts. These components are available in various shapes, sizes, and materials, and they serve different purposes in the molding process. Some of the common types of mold components include ejector pins, core pins, cavity inserts, and sprue bushings.
Ejector pins are used in the mold to eject the finished part from the mold once it has been formed. Core pins are designed to create holes and other complex features in the molded part. Cavity inserts are used to create complex geometries in the molded part, while sprue bushings are used to control the amount of material that enters the mold.
Other types of mold components include cooling components, which help control the temperature of the mold during production, and alignment components, which ensure that the mold halves are aligned correctly during the molding process.
In terms of applications, mold components are used in various industries, including automotive, aerospace, medical device, and consumer goods. For example, in the automotive industry, mold components are used to produce various parts, such as dashboards, seat frames, and fenders. In the aerospace industry, mold components are used to produce complex parts, such as turbine blades and engine components. In the medical device industry, mold components are used to produce devices such as syringes, catheters, and surgical instruments. In the consumer goods industry, mold components are used to produce items such as toys, housewares, and electronic products.
In conclusion, mold components are essential tools in the production of molded parts, and they serve different purposes in the molding process. They are available in various types and materials, and they are widely used in various industries to produce a wide range of products.
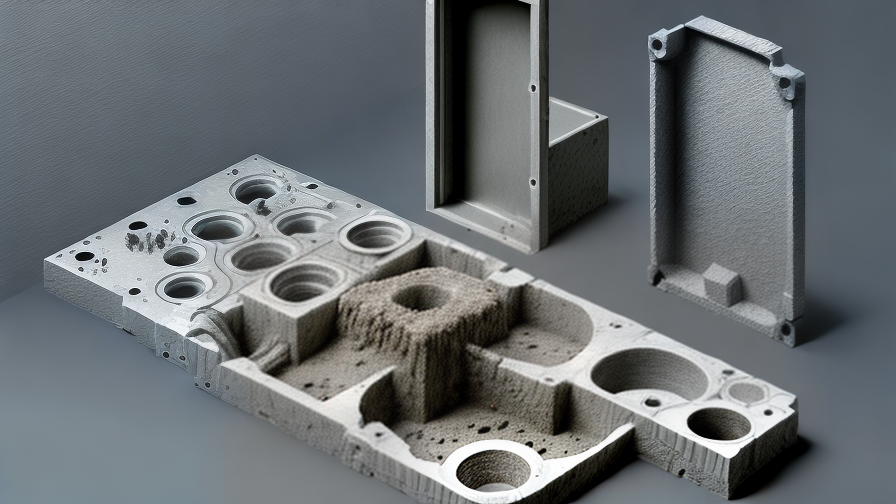
Benefits and Feature of Utilizing mold components
Mold components are essential parts of any mold-making process. They are the building blocks of the mold and play a crucial role in the overall quality of the finished product. Utilizing mold components can offer several benefits, including:
1. Improved accuracy: Mold components are designed to precise specifications, ensuring consistency and accuracy in the production process. This results in high-quality finished products with consistent dimensions that meet the required tolerances.
2. Reduced lead times: Utilizing mold components can significantly reduce lead times in mold-making processes. Since the components are pre-manufactured, they are readily available, reducing production time and costs.
3. Enhanced durability: Mold components are made from high-quality materials, such as tool steel and carbide, making them strong and durable. These materials can withstand the harsh conditions of the molding process, extending the life of the mold.
4. Increased versatility: Mold components offer a wide range of options, including standard and custom-made components, allowing for greater versatility in the molding process.
5. Simplified maintenance: Mold components are designed for easy maintenance and repair. They are easy to remove and replace, reducing downtime and maintenance costs.
Some of the features of mold components include:
1. Standardization: Mold components are standardized, ensuring compatibility with other components and making it easier to replace or upgrade parts.
2. Precision: Mold components are designed with precision, meeting strict tolerances and maintaining consistency in the molding process.
3. Customizable: Mold components can be customized, enabling manufacturers to create molds that suit their specific needs and requirements.
4. Compatibility: Mold components are compatible with various molding techniques, including injection molding, blow molding, and extrusion.
5. Cost-effective: Mold components offer a cost-effective solution to mold-making, allowing manufacturers to reduce production costs and improve profitability.
In summary, utilizing mold components can offer several benefits, including improved accuracy, reduced lead times, enhanced durability, increased versatility, and simplified maintenance. These components are also standardized, precise, customizable, compatible, and cost-effective, making them an essential part of any successful mold-making process.
The Process of mold components
The process of mold components involves several steps that are essential for producing high-quality molds. These steps include design, mold-making, and finishing.
Design is the first step in the process of mold components. The designer will create a detailed blueprint of the mold components, which will include the shape and size of each component. They will also consider factors such as the material to be used and the intended use of the mold.
Once the design is complete, mold-making can begin. This step involves using a specialized machine to create the mold components, usually from metal or plastic. The machine uses computer-aided design (CAD) software to precisely cut and shape the components to match the design.
Finishing is the final step in the process of mold components. This step involves polishing the mold components to create a smooth, glossy finish. The finishing process may also include the addition of any necessary markings or labels to the components.
Throughout the process of mold components, quality control is essential. Each component must be carefully inspected to ensure that it meets the required specifications and will function correctly. Any defects or imperfections in the components can lead to the molding process producing defective parts.
Overall, the process of mold components is a complex and precise one that requires skilled professionals and specialized equipment. By following each step carefully and ensuring quality control throughout the process, manufacturers can produce high-quality molds that will be effective for years to come.

How to use mold components
Mold components are essential parts used in the injection molding process. They play a critical role in ensuring that molded parts are accurate, consistent, and of high quality. To use Mold components, several steps must be followed.
First, always ensure that the mold components are correctly assembled and installed in the injection molding machine. This is because any misalignment or incorrect installation can result in defects in the final product.
Secondly, choose the right mold components for the specific application. For instance, different manufacturing processes may require different gate types, ejection systems, and cooling systems. So, it’s essential to choose mold components that fit perfectly into the design specifications.
Thirdly, regularly clean and maintain mold components. Keeping all components clean and lubricated is crucial to ensure that they function smoothly and last longer. This can be done by using lubricants and sprays that are suitable for plastic injection molding applications.
Lastly, during the injection molding process, ensure that the injection molding machine’s settings are correctly adjusted to suit the mold components. Set the appropriate temperature, pressure, and time to ensure a consistent flow of plastic material into the mold and avoid defects in the final product.
In conclusion, mold components are essential parts in plastic injection molding applications. Following proper installation, selecting the right components, cleaning and maintenance, and adjusting the machine settings can ensure consistent and high-quality molded parts.
mold components Manufacturer,Supplier and Wholesale
As a mold components manufacturer, supplier, and wholesaler, our company provides high-quality products to meet the demands of the mold-making industry. We specialize in designing and producing precision mold components such as core pins, ejector pins, sleeves, and hot runner systems. Our products are used in various applications, including medical, automotive, aerospace, and consumer products.
Our manufacturing process utilizes the latest technologies and equipment, ensuring that our products meet or exceed industry standards. We source only high-quality materials from trusted suppliers, ensuring that our components are durable, long-lasting, and perform optimally.
As a supplier, we work closely with our clients to understand their needs and provide customized solutions that fit their specific requirements. We offer a range of services, including custom mold design, prototyping, and production runs. Our team of experienced engineers can assist in the development of new products, from concept to final production.
As a wholesaler, we offer competitive pricing on our products, allowing our clients to reduce costs while maintaining high-quality standards. Our products are available in a variety of sizes and configurations to meet different mold-making needs.
Our commitment to quality, reliability, and innovation has made us a trusted partner for many mold-making companies. We strive to exceed our clients’ expectations at all times, providing exceptional customer service and timely deliveries.
In summary, our company is a one-stop-shop for all mold component needs, offering high-quality products, customized solutions, and exceptional customer service at competitive prices. Contact us today to learn more about our products and services.

mold components Price
Mold components refer to a variety of small parts used in the process of plastic injection molding. They are crucial to the overall success of the molding process, as they aid in the formation of the final product. When it comes to pricing, mold components can range from a few cents per piece to a few hundred dollars. The cost factors that influence the pricing of mold components include the type of material, complexity of design, and quantity needed.
The most commonly used mold component materials are steel, aluminum, and brass. These materials are selected based on their durability and ability to withstand the high temperatures and pressure involved in the injection molding process. Steel mold components are generally the most expensive due to their high durability and long lifespan. Aluminum and brass mold components, on the other hand, are more affordable but do not last as long as steel.
The complexity of the mold component design is another factor that affects the price. More intricate designs require specialized equipment and additional raw materials, leading to higher production costs. For example, a simple ejector pin may only cost a few cents, but a complex core side lifter can cost hundreds of dollars due to its complexity.
The quantity of mold components ordered also plays a role in determining the price. Manufacturing mold components on a large scale reduces per-unit production costs due to economies of scale. As a result, customers who order in large quantities can receive discounts and lower prices.
In conclusion, the price of mold components varies widely and depends on several factors such as material, complexity of design, and quantity needed. When sourcing mold components, it is important to consider the balance between price and quality to ensure a successful injection molding process and the production of quality plastic parts.
FAQ sourcing mold components manufacturer from China with multiple answers
1. Why should I source mold components from China?
There are several reasons to source mold components from China. Firstly, China is known for its cost-effective manufacturing capabilities, providing cost savings for businesses by sourcing from China. Secondly, China has a large number of skilled workers who excel in creating high-quality components for molds.
2. What are the most commonly sourced mold components from China?
The most commonly sourced mold components from China include inserts, ejector pins, guide pins, lifts, and bushings.
3. How do I choose a reliable mold components manufacturer in China?
To choose a reliable mold components manufacturer in China, you should look for a company with a good reputation, experience in the industry, and the necessary certifications. You can also check their customer reviews and quality control processes.
4. What are the lead times for sourcing mold components from China?
The lead times for sourcing mold components from China can vary depending on the complexity of the component, the quantity required, and the manufacturer’s production capacity. It typically ranges from 3-6 weeks.
5. How can I ensure the quality of the mold components I source from China?
To ensure the quality of the mold components sourced from China, it is recommended to conduct regular factory visits and inspections, request quality control reports, and work with a trusted third-party inspection agency.
6. How do I manage communication and language barriers with Chinese manufacturers?
To manage communication and language barriers with Chinese manufacturers, it is recommended to have a clear and concise communication plan, use a translator or interpreter, and make use of visual aids such as diagrams and pictures.
7. What types of payment methods are accepted by Chinese mold components manufacturers?
Most Chinese mold components manufacturers accept payment methods such as wire transfer, PayPal, and credit cards. It is recommended to choose a payment method that offers protection for both parties.