Introduce about sheet metal machines guide,Qulity,Cost,Supplier,Certification,Market,Tips,FAQ
Sheet metal machines guide provides information on various types of machines used for cutting, bending, and forming sheet metal. These machines are essential for manufacturing industries that work with metal fabrication.
When considering the quality of sheet metal machines, it is important to look for machines that are durable, accurate, and efficient. High-quality machines will provide consistent results and require less maintenance, ultimately saving time and money in the long run.
Cost is another important factor to consider when purchasing sheet metal machines. While it is important to find machines that fit within your budget, it is also crucial to consider the long-term costs of maintenance and operation.
There are several suppliers of sheet metal machines in the market, each offering a range of products to choose from. It is important to research different suppliers and compare their offerings to find the best machine for your needs.
Certification is also a key consideration when purchasing sheet metal machines. Look for machines that are certified by industry standards to ensure they meet quality and safety requirements.
The market for sheet metal machines is growing, with increasing demand for advanced technology and automation. Stay informed on industry trends and advancements to make informed purchasing decisions.
Tips for buying sheet metal machines include setting a budget, assessing production needs, and consulting with industry experts for recommendations.
Frequently asked questions about sheet metal machines include inquiries about maintenance, operation, and troubleshooting common issues. Reviewing user manuals and getting training from suppliers can help answer these questions.
Types of sheet metal machines
There are several types of sheet metal machines that are used in the fabrication and forming of sheet metal. These machines are designed to cut, shape, and bend sheet metal to create a wide range of products. Some common types of sheet metal machines include:
1. Shearing machines: These machines are used for cutting sheet metal into desired shapes and sizes. They work by applying a significant amount of force to a specific area of the metal, causing it to fracture and separate.
2. Bending machines: Bending machines are used to bend sheet metal into various angles and shapes. They can perform simple bends as well as complex curves. Bending machines use a range of tools such as press brakes, folder machines, and rotary benders.
3. Rolling machines: Also known as roll formers or roll bending machines, these machines are used to roll sheet metal into cylindrical or conical shapes. They work by passing the sheet metal through a series of rollers that gradually shape the metal into the desired form.
4. Punching machines: Punching machines are used to create holes or other shapes in sheet metal. They use a punch and die set that is designed to cut through the metal with precision. Different types of punches can be used to create various hole shapes, such as round, square, or rectangular.
5. Notching machines: Notching machines are used to create notches or grooves in sheet metal. These machines are commonly used in the fabrication of ductwork and other similar applications. Notching machines use a cutting tool that removes material from the edge of the sheet metal to create the desired shape.
6. Laser cutting machines: Laser cutting machines use a high-powered laser beam to cut through sheet metal. These machines are highly accurate and precise, allowing for complex shapes and intricate designs to be easily created. Laser cutting machines are commonly used in industries such as automotive, aerospace, and electronics.
Overall, sheet metal machines play a crucial role in the manufacturing and fabrication processes. They enable the efficient and precise shaping of sheet metal, allowing for the creation of a wide range of products and components.
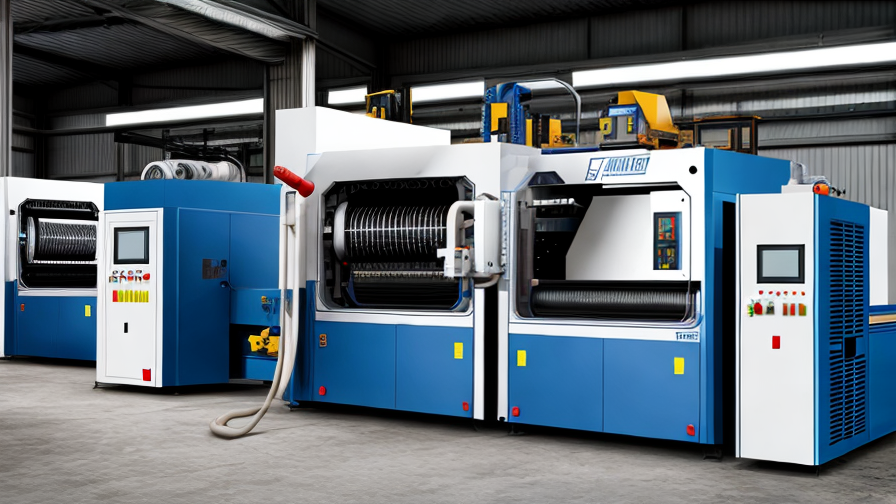
Pros and Cons of Using sheet metal machines
Sheet metal machines are highly versatile tools that offer a wide range of benefits for various industries. However, like any manufacturing equipment, they also have certain drawbacks. Here are some pros and cons of using sheet metal machines:
Pros:
1. Increased productivity: Sheet metal machines, such as shears, press brakes, and roll formers, automate the production process, allowing for higher output and faster production times. This leads to increased productivity and efficiency in manufacturing operations.
2. Precision and accuracy: Sheet metal machines are designed to provide precise and accurate results, ensuring consistent quality and minimal error rates. This is particularly important when it comes to complex fabrication tasks that require precise measurements and alignments.
3. Improved safety: Many sheet metal machines are equipped with safety features, such as emergency stop buttons and safety guards, to ensure the protection of operators. These safety mechanisms minimize the risk of accidents and injuries in the workplace.
4. Cost savings: By utilizing sheet metal machines, manufacturers can achieve cost savings in various ways. These machines streamline the production process, reducing labor costs and minimizing material wastage. Additionally, they allow for bulk production, which often leads to better pricing from suppliers.
5. Versatility: Sheet metal machines can perform various tasks, including cutting, bending, molding, and forming, making them highly versatile tools. They can work with a wide range of sheet metal materials, including steel, aluminum, and copper, thereby catering to diverse manufacturing needs.
Cons:
1. Initial investment: Sheet metal machines can be expensive to purchase, which may pose a barrier for small businesses or startups. The cost of acquiring and maintaining these machines, including training operators, upkeep, and repairs, can be substantial.
2. Limited flexibility: While sheet metal machines offer versatility, they may have limitations in terms of the size, complexity, and unique requirements of certain fabrication projects. Customization or adapting to non-standard specifications may be challenging or even impossible for some machines.
3. Skilled operators required: Operating sheet metal machines requires skilled personnel with expertise in machine programming, maintenance, and troubleshooting. Finding and training skilled operators can be time-consuming and costly.
4. Space requirements: Sheet metal machines typically require a dedicated space within the manufacturing facility due to their size and complexity. This may require additional planning and adjustments to the layout of the workspace, potentially leading to space constraints.
5. Maintenance and repairs: Sheet metal machines need regular maintenance to ensure optimal performance and prevent breakdowns. This involves scheduled inspections, lubrication, and replacing worn-out parts. Repairs, especially for complex machines, may require specialized expertise and resources, causing downtime and additional costs.
In conclusion, sheet metal machines offer significant advantages in terms of productivity, precision, safety, cost savings, and versatility. However, the initial investment, limited flexibility, requirement for skilled operators, space constraints, and maintenance needs should also be taken into consideration when deciding to incorporate these machines into a manufacturing operation.
sheet metal machines Reference Specifications (varies for different product)
Sheet metal machines are tools used for cutting, bending, and forming metal sheets into various shapes and sizes. These machines are essential in the manufacturing industry for producing a wide range of products such as car parts, appliances, and metal enclosures.
Some common types of sheet metal machines include:
1. Shearing machines – used for cutting metal sheets into desired lengths or shapes. These machines can be hydraulic, mechanical, or electric-powered, with cutting capacities ranging from a few millimeters to several meters.
2. Press brakes – used for bending metal sheets into various angles and shapes. These machines can be manual, hydraulic, or CNC-controlled, offering high precision in bending operations.
3. Roll forming machines – used for shaping metal sheets into continuous profiles such as tubes, channels, or angles. These machines consist of several rollers that gradually bend the metal sheet into the desired shape.
4. Punching machines – used for creating holes or slots in metal sheets. These machines can be mechanical or hydraulic, with varying punching capacities and speeds depending on the requirements.
When selecting a sheet metal machine, it is important to consider factors such as the material type and thickness, desired output, and budget constraints. Additionally, it is crucial to follow the manufacturer’s specifications for proper usage, maintenance, and safety precautions. By choosing the right sheet metal machine for the job, manufacturers can optimize their production processes and achieve high-quality results.
Applications of sheet metal machines
Sheet metal machines play a crucial role in various industries for shaping and manipulating sheet metal into the desired forms. These machines are highly versatile and can be utilized in a wide range of applications. Here are some of the key applications of sheet metal machines:
1. Automotive Industry: Sheet metal machines are extensively used in the automotive sector to manufacture automobile parts such as body panels, chassis, frames, and exhaust systems. These machines enable accurate and efficient shaping of the metal to meet the specific requirements of each component.
2. HVAC Systems: Heating, ventilation, and air conditioning (HVAC) systems rely on sheet metal machines for the fabrication of air ducts, vents, and other components. The machines ensure precise folding, bending, and cutting of sheet metal to create ductwork that is vital for efficient airflow and temperature control.
3. Construction Industry: Sheet metal machines find wide application in the construction sector for manufacturing roofing materials, gutters, flashing, and other exterior components. The machines help in creating precise bends, folds, and cuts to ensure the durability and functionality of these construction elements.
4. Industrial Equipment: Various industrial equipment such as enclosures, cabinets, and control panels are produced using sheet metal machines. These machines enable the accurate shaping and assembly of metal parts to create sturdy and secure enclosures for industrial machinery.
5. Aerospace Industry: Sheet metal machines are utilized in the aerospace sector to fabricate components such as aircraft skins, panels, and structures. The machines allow for the precise forming and cutting of lightweight yet strong materials like aluminum and titanium, crucial for meeting aerospace safety and performance standards.
6. Electronics Manufacturing: Sheet metal machines play a vital role in the production of electronic enclosures and chassis. These machines enable intricate cutting and bending of sheet metal to create precise housing for electronic components, ensuring their protection and proper functioning.
7. Furniture Manufacturing: The furniture industry extensively uses sheet metal machines to produce frames, legs, and other metal components. These machines provide the required precision and efficiency to create durable and aesthetically pleasing metal parts for furniture pieces.
In conclusion, sheet metal machines find applications in a diverse range of industries including automotive, construction, aerospace, electronics, and furniture manufacturing. Their versatility, precision, and efficiency make them essential tools for shaping sheet metal into various components and structures required in these industries.
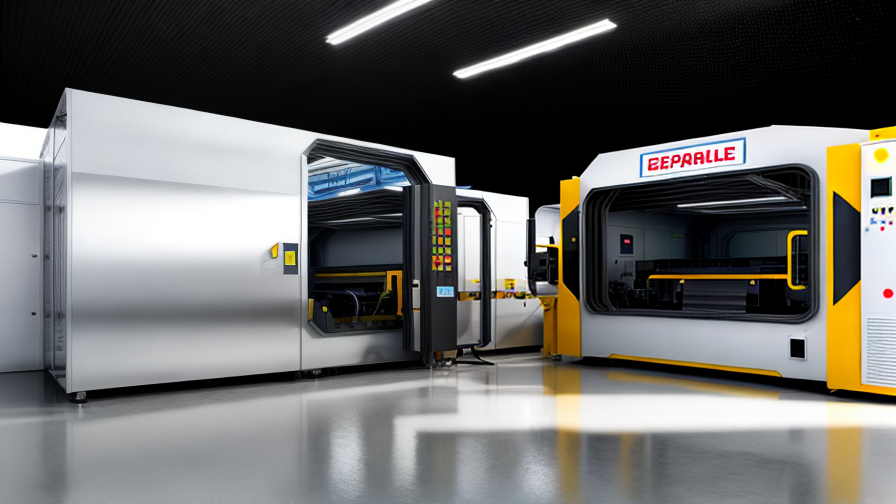
The Work Process and how to use sheet metal machines
The work process involved in using sheet metal machines can be summarized in a few key steps. These machines are used in various industries for cutting, shaping, and forming sheet metal into desired shapes and sizes. Here is a brief overview of the work process:
1. Material Preparation: The first step is to prepare the sheet metal for processing. This involves measuring and marking the sheet metal with the required dimensions using tools like rulers, calipers, and scribes.
2. Machine Setup: The next step is setting up the sheet metal machine. This includes adjusting various parameters such as the speed, depth of cut, and angle depending on the specific operation to be performed.
3. Machine Operation: Once the machine is set up, the operator feeds the sheet metal into the machine, ensuring proper alignment. The machine then performs the operation, such as cutting, shearing, bending, or forming, according to the set parameters.
4. Quality Control: Throughout the process, it is important to monitor the output for quality. Inspection and measurement tools like gauges, micrometers, and visual inspections are used to ensure the accuracy and precision of the machined sheet metal.
5. Finishing: After the desired operation is completed, the sheet metal may require additional finishing processes like deburring, sanding, polishing, or coating to remove sharp edges, improve surface finish, or provide protection against corrosion.
6. Maintenance: Regular maintenance of the sheet metal machine is crucial for its optimal performance and longevity. This includes lubricating moving parts, replacing worn-out components, and cleaning to prevent any buildup of debris or particles.
To effectively use sheet metal machines, operators and technicians should have a thorough understanding of machine controls, safety procedures, and the specific techniques required for different operations. Training programs, manuals, and hands-on experience are commonly used methods to gain proficiency in operating these machines.
In conclusion, the work process of using sheet metal machines involves material preparation, machine setup, machine operation, quality control, finishing, and maintenance. Through proper training and experience, operators can effectively utilize these machines to shape sheet metal into desired forms, meeting specific requirements and quality standards.
Quality Testing Methods for sheet metal machines and how to control the quality
Testing sheet metal machines for quality is crucial to ensure safe and efficient operations. Several testing methods are employed to control the quality of sheet metal machines:
1. Visual Inspection: This involves a thorough examination of the machine to identify any visible defects such as dents, scratches, improperly aligned parts, or welding issues.
2. Measurement and Accuracy Testing: Utilizing precision measurement tools, critical dimensions are assessed to ensure they meet the specified tolerances. This can include verifying the accuracy of cutting, bending, or punching operations.
3. Performance Testing: The machine is tested under simulated operating conditions to evaluate its performance and functionality. This can involve running the machine at different speeds, loads, or executing a specific task to confirm it performs as intended.
4. Material Testing: The raw materials used in the fabrication of sheet metal machines need to meet certain quality standards. Material testing methods such as hardness testing, tensile strength evaluation, or chemical analysis might be employed to ensure the materials are of appropriate quality.
5. Safety Testing: Safety aspects of sheet metal machines are assessed using various methods. This can include checking emergency stop mechanisms, securing safety guards, evaluating electrical safety measures, and confirming the compliance of the machine with relevant safety standards.
To control the quality of sheet metal machines effectively, several steps must be taken:
1. Establishing Quality Standards: Clearly define the quality criteria and specifications that the machines must meet.
2. Adhering to Design and Manufacturing Standards: Ensure the machines are designed and manufactured according to industry standards and best practices.
3. Implementing Quality Control Processes: Introduce a robust quality control process throughout the manufacturing cycle that includes regular inspections and testing at each step.
4. Continuous Improvement: Regularly analyze the testing results and customer feedback to identify areas for improvement in design, manufacturing, or quality control processes.
5. Employee Training and Engagement: Provide comprehensive training to the staff involved in the manufacturing of sheet metal machines, ensuring they are aware of quality requirements and their role in maintaining quality standards.
6. Documentation and Traceability: Maintain detailed records of inspections, tests, and any corrective actions taken. This enables traceability and analysis of the quality control process.
By employing these testing methods and implementing effective quality control measures, sheet metal machine manufacturers can ensure the delivery of top-quality machines that meet customer expectations, optimize productivity, and enhance safety.
sheet metal machines Sample Policy and Post-Purchase Considerations for sheet metal machines from China
Sample Policy:
1. Quality Assurance: All sheet metal machines purchased from China should meet the required quality standards and specifications as agreed upon in the purchase agreement. The supplier must provide inspection reports and certificates of conformity to ensure the quality of the machines.
2. Warranty: A minimum warranty period of one year should be provided by the supplier for all sheet metal machines. This warranty should cover any manufacturing defects or operational issues that may arise during the specified period.
3. Technical Support: The supplier should provide comprehensive technical support for the sheet metal machines, including installation, training, and troubleshooting assistance. Any necessary documentation, such as user manuals and maintenance guides, should be provided in English or the language acceptable to the buyer.
4. Spare Parts Availability: The supplier should ensure the availability of spare parts for the sheet metal machines for a reasonable period (usually 5-10 years) after the purchase. This should include facilitating easy and prompt access to spare parts, either from their own inventory or through reliable local distributors.
5. Return and Exchange Policy: In case of any major defects or discrepancies, a clear return and exchange policy should be laid down. The supplier should be responsible for the cost of shipping and replacing the faulty sheet metal machines or components.
Post-Purchase Considerations:
1. Operator Training: Arrange for appropriate training of the operators to ensure safe and efficient usage of the sheet metal machines. This can be done through in-person training sessions, video tutorials, or user manuals provided by the supplier.
2. Regular Maintenance and Servicing: Regularly maintain and service the sheet metal machines as per the manufacturer’s guidelines. This will help prolong their lifespan and ensure optimal performance.
3. Quality Control: Implement strict quality control measures to monitor the performance and quality of the sheet metal machines over time. This can include periodic inspections, performance evaluations, and feedback collection from operators.
4. Supplier Relationship: Maintain a good relationship with the supplier for continued support and assistance. Regular communication regarding any issues, updates, or spare parts requirements will help enhance the overall experience with the sheet metal machines.
5. Keep Up with Technological Advancements: Stay updated with advancements in sheet metal machinery technology to ensure the competitiveness and efficiency of your operations. This may include attending industry exhibitions, subscribing to relevant newsletters, and engaging in continuous learning.
By following these sample policies and post-purchase considerations, you can minimize risks associated with purchasing sheet metal machines from China and maximize the value and performance of your equipment.
Sourcing sheet metal machines from China: Opportunities, Risks, and Key Players
When sourcing sheet metal machines from China, there are both opportunities and risks to consider.
Opportunities:
1. Cost savings: China is known for its low labor costs and manufacturing capabilities, allowing for competitive pricing on sheet metal machines.
2. Wide variety of options: China has a wide range of manufacturers offering various types of sheet metal machines to choose from.
3. Technological advancements: Chinese manufacturers are constantly investing in research and development to improve the quality and efficiency of their machines.
Risks:
1. Quality concerns: There may be issues with the quality of sheet metal machines sourced from China, so it’s important to thoroughly vet suppliers and conduct quality control inspections.
2. Intellectual property theft: China has a reputation for intellectual property theft, so it’s crucial to protect your designs and technology when sourcing machines from there.
3. Communication and logistics challenges: There may be language barriers and logistical challenges when working with Chinese suppliers, so clear communication and detailed contracts are essential.
Key players:
1. Amada Holdings: A leading Japanese manufacturer with a strong presence in China.
2. Trumpf: A German company that has a significant manufacturing base in China.
3. HACO: A Belgian manufacturer that also operates in China.
In conclusion, sourcing sheet metal machines from China can offer cost savings and a wide variety of options, but it’s important to be aware of quality concerns, intellectual property risks, and communication challenges. Working with reputable suppliers and conducting thorough due diligence can help mitigate these risks and ensure a successful sourcing process.
How to find and select reliable sheet metal machines manufacturers in China,use google search manufacturers and suppliers
When searching for reliable sheet metal machine manufacturers in China, utilizing Google search is an efficient and effective approach. Follow the steps below to find and select trustworthy manufacturers and suppliers:
1. Begin by conducting a search on Google using specific keywords related to sheet metal machines, such as “sheet metal machine manufacturer China” or “reliable sheet metal machinery supplier.”
2. Review the search results and visit the official websites of potential manufacturers. Look for a professional and well-designed website, as this indicates a credible company.
3. Pay attention to the company’s profile, including their history, experience, and certifications. Reliable manufacturers often highlight their achievements and qualifications, demonstrating their commitment to quality production.
4. Look for customer testimonials or reviews on the company’s website. Genuine feedback from previous clients reflects the manufacturer’s reputation and reliability.
5. Utilize online business directories or B2B platforms, such as Alibaba, Made-in-China, or Global Sources. These platforms gather multiple manufacturers and suppliers in one place, making it easier to compare and select the most reliable ones.
6. Scrutinize the product listings on these platforms, paying attention to detailed product descriptions, specifications, and images. Look for manufacturers who provide comprehensive information and high-quality product images.
7. Evaluate the company’s verified credentials, such as business licenses, certifications, and product quality standards. Reputable manufacturers often display these important credentials to establish trust.
8. Contact a shortlist of manufacturers and suppliers either through their website contact forms or designated contact information. Communicate your specific requirements, inquire about their production capabilities, and request detailed quotations.
9. Evaluate the responsiveness and professionalism of the manufacturer’s communication. Prompt and clear responses are indicative of their commitment to customer service.
10. Request samples or visit their facilities if possible. This will allow you to assess the quality of their sheet metal machines firsthand and evaluate their production capacity.
By following these steps, you will be able to find and select reliable sheet metal machine manufacturers in China, ensuring a successful partnership for your business.
How to check sheet metal machines manufacturers website reliable,use google chrome SEOquake check if ranking in top 10M
To check the reliability of a sheet metal machines manufacturer’s website, you can use Google Chrome and install the SEOquake extension. By typing in the manufacturer’s website URL and checking if it ranks in the top 10 search results, you can get an idea of its credibility and popularity.
Additionally, you can look for customer reviews, testimonials, and case studies on the website to see what previous customers have to say about their experiences with the manufacturer. A reliable manufacturer will often have positive feedback from satisfied customers.
Furthermore, you can check if the website has clear contact information, such as a phone number, email address, or physical address, which can indicate that the manufacturer is legitimate and easily accessible.
It’s also important to look for certifications, awards, and industry affiliations on the website, as these can demonstrate the manufacturer’s commitment to quality and excellence.
Overall, by using SEOquake to check the manufacturer’s website ranking, reviewing customer feedback, verifying contact information, and checking for industry certifications, you can determine the reliability and credibility of the sheet metal machines manufacturer before making a purchase.
Top 10 sheet metal machines manufacturers in China with each 160 words introduce products,then use markdown create table compare
1. Maanshan Press and Shear Machinery Co., Ltd.
Maanshan Press and Shear Machinery Co., Ltd. specializes in the production of hydraulic press brakes, hydraulic shearing machines, and punching machines. Their products are known for their high precision, durability, and efficiency.
2. Anhui LIFU Machinery Technology Co., Ltd.
Anhui LIFU Machinery Technology Co., Ltd. manufactures a wide range of sheet metal machines including laser cutting machines, plasma cutting machines, and bending machines. Their products are widely used in industries such as automotive, aerospace, and construction.
3. Jiangsu YingNan Machinery Co., Ltd.
Jiangsu YingNan Machinery Co., Ltd. offers a variety of sheet metal machines such as hydraulic press brakes, shearing machines, and ironworkers. Their machines are known for their reliability, accuracy, and ease of use.
4. Ningbo Bohong Machinery Co., Ltd.
Ningbo Bohong Machinery Co., Ltd. produces CNC turret punching machines, hydraulic press brakes, and guillotine shearing machines. Their machines are suitable for processing various types of sheet metal with high efficiency and precision.
5. Nanjing Prima CNC Machinery Co., Ltd.
Nanjing Prima CNC Machinery Co., Ltd. specializes in the production of CNC press brakes, CNC shearing machines, and CNC punching machines. Their products are known for their advanced technology, high performance, and durability.
| Manufacturer | Products | Specialization | Technology |
|——————————————-|———————————————-|—————-|————|
| Maanshan Press and Shear Machinery Co., Ltd. | Hydraulic press brakes, shearing machines, punching machines | Precision and durability | Hydraulic |
| Anhui LIFU Machinery Technology Co., Ltd. | Laser cutting machines, plasma cutting machines, bending machines | Versatility | Laser and plasma cutting |
| Jiangsu YingNan Machinery Co., Ltd. | Hydraulic press brakes, shearing machines, ironworkers | Reliability and accuracy | Hydraulic |
| Ningbo Bohong Machinery Co., Ltd. | CNC turret punching machines, hydraulic press brakes, guillotine shearing machines | High efficiency | CNC technology |
| Nanjing Prima CNC Machinery Co., Ltd. | CNC press brakes, CNC shearing machines, CNC punching machines | Advanced technology | CNC |
Background Research for sheet metal machines manufacturers Companies in China, use qcc.com archive.org importyeti.com
Sheet metal machines are essential tools in the manufacturing industry, used for cutting, bending, and shaping metal sheets to create a variety of products. In China, there are numerous manufacturers of sheet metal machines that cater to both domestic and international markets.
One of the leading manufacturers of sheet metal machines in China is Jinan Bodor CNC Machine Co., Ltd. They specialize in the production of laser cutting machines, fiber laser cutting machines, and metal sheet laser cutting machines. Their products are known for their high precision and efficiency, making them a popular choice among manufacturers worldwide.
Another prominent player in the industry is JiangSu TiangDing Machinery Manufacturing Co., Ltd. They offer a wide range of sheet metal machines, including shearing machines, bending machines, and punching machines. With a focus on quality and innovation, they have established themselves as a reliable supplier in the market.
Shanghai Huantu Technical Industry Co., Ltd. is also worth mentioning for their extensive range of sheet metal machines, such as hydraulic press brakes, hydraulic shearing machines, and rolling machines. They have a strong reputation for providing durable and cost-effective solutions for sheet metal processing.
Overall, the sheet metal machine manufacturing industry in China is highly competitive and constantly evolving to meet the growing demand for efficient and precise metal processing equipment. Companies like Jinan Bodor CNC Machine Co., Ltd., JiangSu TiangDing Machinery Manufacturing Co., Ltd., and Shanghai Huantu Technical Industry Co., Ltd. are leading the way with their innovative products and commitment to quality.
Leveraging Trade Shows and Expos for sheet metal machines Sourcing in China
Trade shows and expos are excellent platforms for sourcing sheet metal machines in China. These events provide a centralized location for manufacturers, suppliers, and buyers to connect, network, and explore potential business partnerships.
By attending trade shows and expos dedicated to sheet metal machines in China, buyers can take advantage of a wide range of benefits. Firstly, they can meet face-to-face with potential suppliers and manufacturers, allowing them to assess the quality of the machines, negotiate pricing, and establish long-term relationships. This direct interaction also gives buyers the opportunity to ask questions, seek clarification, and gain a better understanding of the products being offered.
Moreover, trade shows and expos often showcase the latest technologies, innovations, and trends in the sheet metal machine industry. Buyers can stay informed about market developments, compare different products, and make informed purchasing decisions based on their specific needs and requirements.
Additionally, trade shows and expos provide buyers with a platform to conduct market research, gain insights into industry best practices, and identify potential sourcing opportunities. By networking with other industry professionals, buyers can expand their knowledge, enhance their sourcing strategies, and stay ahead of the competition.
In conclusion, leveraging trade shows and expos for sheet metal machines sourcing in China is a smart and efficient way for buyers to connect with suppliers, explore new products, and stay informed about industry developments. By attending these events, buyers can maximize their sourcing efforts and secure high-quality sheet metal machines for their business needs.
The Role of Agents and Sourcing Companies in Facilitating sheet metal machines Purchases from China
Agents and sourcing companies play a crucial role in facilitating purchases of sheet metal machines from China. These individuals or companies act as intermediaries between buyers and suppliers, offering valuable expertise, contacts, and assistance to ensure a smooth and successful transaction.
One of the main advantages of working with agents or sourcing companies is their in-depth knowledge of the Chinese market and industry. They have a deep understanding of the local manufacturing landscape, including the various sheet metal machine manufacturers, their capabilities, and product quality. This expertise allows them to identify reputable suppliers who meet the buyer’s specific requirements and quality standards.
Agents and sourcing companies also help overcome language and cultural barriers that may exist between buyers and Chinese suppliers. They typically have personnel with bilingual capabilities, ensuring effective communication and understanding between both parties. This helps clarify technical specifications, negotiate pricing, and address any concerns or issues that may arise during the purchase process.
Furthermore, agents and sourcing companies assist in verifying supplier credentials, conducting factory assessments, and performing quality inspections on behalf of the buyer. This quality control ensures that the purchased sheet metal machines meet the required standards and specifications.
Another significant advantage of working with agents or sourcing companies is their ability to navigate complex import/export regulations and logistics. They have experience in handling documentation, customs clearance, shipping, and transportation, ensuring the smooth movement of goods from the Chinese supplier to the buyer’s location. This expertise saves buyers time, effort, and potential headaches associated with international trade logistics.
In summary, agents and sourcing companies serve as invaluable partners when purchasing sheet metal machines from China. Their comprehensive knowledge of the market, ability to bridge cultural and language gaps, expertise in supplier verification and quality control, and proficiency in navigating import/export logistics greatly facilitate a successful transaction. Collaborating with these professionals minimizes risks, saves time and effort, and ultimately enhances the buyer’s chances of obtaining high-quality sheet metal machines at competitive prices.
Price Cost Research for sheet metal machines manufacturers Companies in China, use temu.com and 1688.com
When researching the prices and costs of sheet metal machines from manufacturers in China, two popular platforms to use are temu.com and 1688.com. These websites specialize in connecting international buyers with Chinese suppliers, making it easy to find a wide variety of sheet metal machines at competitive prices.
By browsing through the listings on temu.com and 1688.com, you can compare the prices of different models and brands of sheet metal machines from various manufacturers in China. It is important to pay attention to details such as the specifications, features, and quality of the machines when comparing prices.
Additionally, you can reach out directly to the manufacturers on these platforms to request quotes and negotiate prices for bulk orders. Many suppliers in China are open to negotiation and can offer discounts for larger purchases.
Overall, using temu.com and 1688.com can help you find affordable sheet metal machines from reliable manufacturers in China. By carefully researching prices and costs on these platforms, you can make informed decisions and find the best deals for your business needs.
Shipping Cost for sheet metal machines import from China
When importing sheet metal machines from China, the shipping cost will vary depending on various factors such as the size and weight of the machines, the shipping method chosen, and the destination country.
For smaller sheet metal machines, air freight may be a suitable shipping method. Air freight is generally faster but more expensive compared to sea freight. The cost of air freight for sheet metal machines can range from $3 to $8 per kilogram, with additional charges for handling and customs clearance.
For larger sheet metal machines, sea freight is the most cost-effective shipping method. The cost of sea freight for sheet metal machines can range from $500 to $2000 per cubic meter, depending on the volume and weight of the machines. There may also be additional charges such as customs duties, port fees, and insurance.
It is important to consider hiring a freight forwarder to handle the shipping logistics and ensure a smooth import process. A freight forwarder can help negotiate shipping rates, arrange transportation, and handle customs documentation.
In conclusion, when importing sheet metal machines from China, it is essential to consider the size and weight of the machines, choose the appropriate shipping method, and factor in additional costs such as customs duties and handling fees. By carefully planning and selecting the right shipping options, it is possible to keep shipping costs within a reasonable budget.
Compare China and Other sheet metal machines Markets: Products Quality and Price,Visible and Hidden Costs
China is one of the largest manufacturers and exporters of sheet metal machines globally. When comparing China’s sheet metal machines market to other markets worldwide, several factors come into play. These include product quality, price, visible and hidden costs.
Product Quality: China has often been associated with producing lower-quality products compared to some other markets. While this perception may have held some truth in the past, China has made significant strides in improving the quality of its sheet metal machines. Many Chinese manufacturers now employ advanced technology and adhere to strict quality control measures to produce high-quality machines. However, some other markets, particularly those known for their expertise in precision engineering, may still offer slightly superior quality products.
Price: China’s sheet metal machines market is renowned for its competitive pricing. Chinese manufacturers benefit from lower labor and production costs, allowing them to offer products at more competitive rates compared to some other markets. This affordability has made Chinese machines attractive to businesses looking for cost-effective solutions. However, other markets may offer higher-priced machines that come with certain quality guarantees or additional features.
Visible and Hidden Costs: Visible costs, which are easily identifiable, include the actual purchase price of the sheet metal machine. China’s competitive pricing often makes it more attractive in terms of visible costs. However, there may be hidden costs associated with purchasing from China, such as shipping fees, import duties, and potential delays. On the other hand, purchasing from local or regional markets may come with higher visible costs but could potentially have lower hidden costs due to reduced shipping and import-related expenses.
In summary, China’s sheet metal machines market has evolved to provide improved product quality, particularly in the context of cost-effective solutions. Chinese manufacturers have made significant advancements in technology and quality control processes. However, it is important to consider other markets known for precision engineering and potentially higher-quality machines. The pricing competitiveness of China’s market is an advantage, although hidden costs such as shipping fees and import duties should be taken into account when comparing with other markets.
Understanding Pricing and Payment Terms for sheet metal machines: A Comparative Guide to Get the Best Deal
Pricing and payment terms for sheet metal machines can vary significantly depending on the specific type of machine, brand, model, and the supplier. Understanding these factors and having a comparative guide can help you navigate through the various options and ultimately secure the best deal for your needs. Here is a brief overview of key considerations:
1. Types of Sheet Metal Machines: It is essential to have a clear understanding of the different types of sheet metal machines available in the market, such as shearing machines, bending machines, punching machines, laser cutting machines, etc. Each type has its own pricing range based on the complexity and functionality involved.
2. Brand and Model: Premium brands may offer machines with higher durability, precision, and advanced features, but they often come with a higher price tag. It is important to research and compare different brands and models to find the right balance between quality and affordability for your specific requirements.
3. Supplier Comparison: Obtain quotes from multiple suppliers to get the most competitive pricing. Consider factors such as after-sales service, warranty, and reputation in addition to pricing. Tradeshows, online B2B marketplaces, and industry-specific publications are useful resources to find reputable suppliers.
4. New vs. Used Machines: Used machines can be a cost-effective alternative, but they may come with limited warranties and higher maintenance requirements. Carefully assess the condition and performance history of used machines to ensure they meet your production needs.
5. Payment Terms: Payment terms can vary between upfront payment, partial payment with installments, or leasing options. Evaluate the financial implications of each option and consider your cash flow requirements to determine the most feasible payment plan. Negotiating favorable payment terms may be possible, especially for large orders or long-term relationships.
6. Total Cost of Ownership: Look beyond the price tag and consider the total cost of ownership. This includes additional costs such as installation, training, spare parts, maintenance, and any necessary upgrades. These costs should be factored into your budget and taken into account when comparing deals.
In conclusion, understanding the various aspects of pricing and payment terms for sheet metal machines is crucial to get the best possible deal. By researching and comparing different options, considering the type, brand, supplier, and payment terms, you can make an informed decision that meets your business requirements while ensuring long-term value for money.
Chinese Regulations and Industry Standards Certifications for sheet metal machines,Import Regulations and Customs for sheet metal machines from China
When importing sheet metal machines from China, it is important to be aware of the various Chinese regulations and industry standards certifications that may apply. The Chinese government has strict regulations in place for the production and importation of these machines to ensure quality and safety standards are met. Some key certifications to look for include ISO 9001 for quality management, CE certification for European markets, and CCC certification for domestic Chinese markets.
In addition to certifications, there are also import regulations and customs procedures to be aware of when importing sheet metal machines from China. It is important to ensure that the machines meet the technical requirements and regulations of the importing country. This may include requirements for voltage, safety features, and labeling. Customs duties and taxes may also apply, so it is important to be prepared for these additional costs.
When importing sheet metal machines from China, it is recommended to work with a reliable supplier who can provide the necessary certifications and documentation to ensure a smooth import process. It is also advisable to work with a customs broker who can help navigate the customs procedures and ensure compliance with all regulations. By being aware of the regulations and certifications required for sheet metal machines from China, importers can ensure a successful import process and avoid any potential issues or delays.
Sustainability and Environmental Considerations in sheet metal machines Manufacturing
Sustainability and environmental considerations play a crucial role in the manufacturing of sheet metal machines. The sheet metal industry heavily relies on various processes, materials, and energy sources, which can have significant environmental impacts if not managed properly. By integrating sustainable practices into the manufacturing process, the industry can minimize its ecological footprint.
One major environmental consideration is the choice of materials used in the production of sheet metal machines. Opting for environmentally friendly and recyclable materials, such as aluminum, can greatly reduce the environmental impact. Recycling and reusing materials also minimize waste and promote a circular economy.
Energy consumption is another critical aspect to address. Manufacturers can adopt energy-efficient technologies, such as using advanced machinery, optimizing production processes, and implementing energy management systems. Renewable energy sources, such as solar or wind power, can also be employed, reducing reliance on fossil fuels and greenhouse gas emissions.
Water usage is often overlooked, but it is crucial to minimize water consumption and implement water recycling systems. By capturing and treating wastewater, manufacturers can reduce their water usage and conserve this precious resource.
Waste management is essential to prevent pollution and minimize landfill contributions. Implementing proper waste segregation and recycling programs ensure that various components and materials, such as metals or hazardous substances, are disposed of appropriately.
Finally, manufacturers should focus on product life cycle assessment (LCA) to understand the environmental impacts of the sheet metal machines from the procurement of raw materials to the end of life. Improving designs for disassembly and recyclability can make it easier to recycle or repurpose the products, reducing waste generation.
Overall, sustainability and environmental considerations in the manufacturing of sheet metal machines are vital to minimize the industry’s ecological footprint. By choosing eco-friendly materials, optimizing energy consumption, reducing water usage, implementing waste management systems, and considering product life cycles, manufacturers can contribute to a more sustainable and environmentally friendly future.
List The Evolution history of “sheet metal machines”
Sheet metal machines have played a crucial role in various industries, revolutionizing the way metal sheets are processed and fabricated. The evolution of these machines can be traced back to ancient times when basic hand tools like hammers and chisels were used for sheet metal shaping. However, significant advancements have taken place over the years, leading to highly sophisticated sheet metal machines we see today.
In the 18th century, the emergence of fly presses accelerated sheet metal forming. These machines, operated manually, provided increased force and accuracy for bending and shaping metal sheets. The Industrial Revolution in the late 18th and early 19th centuries brought about significant changes in the manufacturing industry, leading to the development of early sheet metal machines such as hand-operated power shears.
During the late 19th century, mechanical advancements led to the introduction of foot-powered shears, which were easier to operate and improved productivity. The introduction of treadle-powered bending brakes further revolutionized sheet metal fabrication, enabling precise bending and folding.
The early 20th century witnessed the advent of electric-powered sheet metal machines, providing increased power and efficiency. Machines like power shears, press brakes, and slip rolls became widely used in industries such as automotive, construction, and aerospace.
As technology continued to advance, hydraulic and pneumatic systems were incorporated into sheet metal machines. Hydraulic press brakes and pneumatic shears allowed for higher tonnage capacities and faster operations. This evolution significantly improved efficiency and productivity in the sheet metal industry.
Most recently, computer numerical control (CNC) technology has transformed sheet metal fabrication. CNC machines are capable of automated operation, precision, and versatility. These machines can be programmed to perform complex tasks such as punching, laser cutting, and forming with minimal human intervention, reducing errors and increasing production speed.
In conclusion, sheet metal machines have evolved from basic hand tools to highly sophisticated automated systems. The combination of technological advancements and engineering innovations has greatly contributed to the efficiency, accuracy, and productivity of sheet metal fabrication processes throughout history.
The Evolution and Market Trends in sheet metal machines Industry
The sheet metal machines industry has evolved significantly in the past few decades, with rapid advancements in technology and automation. Traditional manual machines have been replaced by computer-controlled machines that offer increased precision, efficiency, and flexibility in sheet metal processing.
Market trends in the sheet metal machines industry include the increasing demand for customized and complex products, the growing adoption of Industry 4.0 technologies such as IoT and artificial intelligence, and the focus on sustainability and energy efficiency. Manufacturers are investing in advanced machines that can handle a wide range of materials, thicknesses, and shapes to cater to diverse customer requirements.
The market for sheet metal machines is also witnessing a shift towards digitalization, with the integration of software solutions for design, simulation, and monitoring. This enables manufacturers to optimize production processes, minimize errors, and maximize productivity.
Furthermore, global trends such as urbanization, infrastructure development, and the rising demand for consumer electronics are driving the growth of the sheet metal machines industry. Emerging economies in Asia, particularly China and India, are key markets for sheet metal machines due to their expanding manufacturing sectors.
In conclusion, the sheet metal machines industry is experiencing a transformation driven by technological advancements, changing customer preferences, and global market trends. Manufacturers need to stay abreast of these developments to stay competitive and meet the evolving demands of the industry.
Custom Private Labeling and Branding Opportunities with Chinese sheet metal machines Manufacturers
Chinese sheet metal machines manufacturers offer custom private labeling and branding opportunities for businesses looking to establish their own brand identity in the market. By partnering with a reputable manufacturer in China, companies can benefit from cost-effective and high-quality sheet metal machines that can be customized to meet their specific needs and preferences.
With the ability to add their logo, colors, and other branding elements to the machines, businesses can create a unique product that stands out from competitors and resonates with their target audience. This can help build brand recognition and loyalty, as well as differentiate their products in a crowded marketplace.
In addition to custom branding options, Chinese manufacturers also offer flexible manufacturing processes that can accommodate small to large-scale production runs. This means that businesses can easily scale their operations and meet changing market demands without compromising on quality or consistency.
Overall, partnering with a Chinese sheet metal machines manufacturer for custom private labeling and branding opportunities can help businesses establish a strong presence in the market, drive sales, and increase brand awareness. By working closely with a trusted manufacturer, companies can develop innovative products that meet the needs of their customers and set them apart from the competition.
Tips for Procurement and Considerations when Purchasing sheet metal machines
1. Know your specific needs: Before purchasing a sheet metal machine, identify the specific requirements of your business. Consider factors such as the type and thickness of metal you work with, production volume, and desired features.
2. Quality and reliability: When choosing a sheet metal machine, prioritize quality and reliability. Look for reputable manufacturers with a track record of producing durable machines that deliver consistent results.
3. Cost and budget: Consider your budget constraints when selecting a sheet metal machine. While it may be tempting to opt for the cheapest option, keep in mind that investing in a higher quality machine may result in better long-term performance and cost savings.
4. Size and capacity: Ensure that the machine you choose has the size and capacity to handle the size of metal sheets you work with. Consider factors such as the cutting or bending capacity, as well as the physical footprint of the machine in your workspace.
5. Maintenance and support: Consider the availability of maintenance services and technical support when purchasing a sheet metal machine. Opt for machines that come with comprehensive warranties and access to a responsive customer support team.
6. Safety features: Prioritize the safety of your workers by choosing a sheet metal machine with adequate safety features. Look for machines that comply with industry safety standards and have features such as emergency stop buttons and guards.
7. Training and expertise: Ensure that your team receives proper training on how to operate the sheet metal machine safely and effectively. Consider investing in training programs or hiring experienced operators to maximize the efficiency of the machine.
8. Future growth potential: Anticipate the future needs of your business when selecting a sheet metal machine. Choose a machine that can accommodate potential growth in production volume or new types of metalworking processes.
In conclusion, when purchasing a sheet metal machine, consider factors such as your specific needs, quality, cost, size, maintenance, safety, training, and future growth potential. By carefully evaluating these considerations, you can select the best machine for your business that will deliver reliable performance and long-term value.
FAQs on Sourcing and Manufacturing sheet metal machines in China
1. Why should I consider sourcing and manufacturing sheet metal machines in China?
Sourcing and manufacturing sheet metal machines in China can offer several advantages, including cost savings and access to a large pool of suppliers. China has a well-established manufacturing sector with a strong focus on sheet metal fabrication. The competitive labor costs and extensive supply chain network allow for more affordable production compared to many other countries. Moreover, China possesses advanced machinery and technology, ensuring high-quality and efficient manufacturing processes.
2. How can I find reliable suppliers in China?
To find reliable suppliers in China, several steps can be taken. Firstly, thorough research should be conducted to identify potential suppliers. This can involve exploring online directories, attending trade shows, and seeking recommendations from industry contacts. Interviewing and visiting potential suppliers can provide clarity on their capabilities, quality control measures, and production capacity. Requesting samples and checking references can also help evaluate their expertise and reliability. Additionally, it is crucial to conduct proper due diligence on potential partners by verifying their certifications, licenses, and compliance with local laws and regulations.
3. Are there any challenges in sourcing and manufacturing sheet metal machines in China?
While there are significant benefits, there are also challenges to consider. Language barriers and cultural differences may hinder effective communication and understanding. It is essential to establish clear and detailed specifications to avoid misinterpretations. Intellectual property protection can also be a concern, so working with trusted partners and implementing legal safeguards is crucial. It is advisable to engage local legal expertise to draft solid contracts and agreements that protect your interests. Finally, properly managing logistics and shipping can be complex, so working with experienced freight forwarders can help overcome these challenges.
4. How can I ensure quality control during manufacturing in China?
Quality control can be maintained through various measures. Establishing stringent quality standards and performing regular inspections throughout the manufacturing process is crucial. Conducting random sample inspections and implementing strict quality control protocols can help identify and address any non-compliant products. Collaborating closely with suppliers to provide clear specifications and regularly monitoring their progress can also contribute to quality control efforts. Third-party inspection agencies can be engaged to provide independent assessments and ensure adherence to international quality standards.
5. What is the typical lead time for sheet metal machine production in China?
The lead time for sheet metal machine production in China can vary depending on various factors such as machine complexity, supplier capacity, and order volume. Generally, the lead time ranges from 4 to 12 weeks, with more complex machines taking longer to manufacture. It is advisable to discuss and agree upon lead times with suppliers in advance and establish clear expectations to avoid any delays. Effective communication and project management can help ensure timely delivery of the machines.
In summary, sourcing and manufacturing sheet metal machines in China can provide cost advantages, a wide supplier network, and access to advanced technology. Thorough research, due diligence, and proper quality control measures are essential when engaging Chinese suppliers. Despite challenges such as language barriers and intellectual property concerns, careful planning and collaboration can result in successful production and delivery of high-quality sheet metal machines.
Why contact sourcifychina.com get free quota from reliable sheet metal machines suppliers?
Sourcifychina.com offers free quota from reliable sheet metal machines suppliers for several reasons. Firstly, it allows potential buyers to assess the capabilities and pricing of the suppliers before making any commitments. By obtaining a free quota, buyers can understand the supplier’s ability to meet their specific requirements and determine if they are the right fit for their business.
Additionally, providing a free quota encourages buyers to engage with sourcifychina.com and builds trust in their sourcing services. By offering access to verified and reliable suppliers, sourcifychina.com demonstrates their commitment to sourcing quality products and simplifying the sourcing process for buyers.
Furthermore, the free quota helps buyers compare different suppliers and make informed decisions. By obtaining multiple quotes from different suppliers, buyers can evaluate various factors such as pricing, lead times, and quality assurance. This allows them to select the supplier that best aligns with their needs and budget.
Moreover, the free quota from reliable suppliers reduces the risk of potential scams or fraudulent activities. Sourcifychina.com verifies the authenticity and reliability of all suppliers listed on their platform, ensuring that buyers can trust the quotes provided. This increases buyer confidence and minimizes potential risks associated with sourcing from unknown or unreliable sources.
Overall, offering a free quota from reliable sheet metal machines suppliers benefits both the buyers and sourcifychina.com. Buyers gain access to quality suppliers and accurate pricing information, facilitating their sourcing process, while sourcifychina.com establishes trust and credibility as a reputable sourcing platform.