Introduce about plastic mould making guide,Qulity,Cost,Supplier,Certification,Market,Tips,FAQ
Plastic mold making is an essential process in the manufacturing industry. It involves creating high-quality molds that are used to shape plastic into various forms. This guide will provide valuable insights into different aspects of plastic mold making.
Quality is of utmost importance in plastic mold making. A well-designed and precisely crafted mold ensures that the final plastic products meet the required specifications. It is crucial to work with experienced and skilled mold makers who can create high-quality molds that deliver consistent results.
Cost is another significant consideration in plastic mold making. The cost of creating molds can vary depending on factors such as complexity, size, and material. It is essential to balance cost and quality to ensure cost-effectiveness in the long run.
Choosing the right supplier for plastic mold making is vital. Look for reputable suppliers who specialize in manufacturing molds with a track record of delivering superior quality products. Collaborating with a reliable supplier ensures that you receive molds that meet your specific requirements.
Certification plays a crucial role in plastic mold making. Look for suppliers who hold certifications such as ISO 9001, which demonstrates adherence to international quality management standards. Certification ensures that the molds are manufactured using robust processes and are reliable.
The market for plastic mold making is vast and expanding. With the growth of industries such as automotive, consumer goods, and electronics, the demand for high-quality molds is increasing. This presents excellent opportunities for mold makers and suppliers.
Here are some tips to consider in plastic mold making: focus on design precision, select suitable materials, use advanced technologies, and maintain open communication with the mold maker for effective project management.
Frequently Asked Questions (FAQ) related to plastic mold making include inquiries about turnaround time, mold maintenance, customization options, and cost estimation. It is advisable to reach out to suppliers or mold makers to address any specific queries.
In conclusion, plastic mold making is a crucial process that requires attention to detail, quality, and cost-effectiveness. By collaborating with reputable suppliers, focusing on certification, and considering the tips mentioned, you can ensure the successful manufacturing of high-quality molds for your plastic products.
Types of plastic mould making
There are several types of plastic mold making processes used in the manufacturing industry. Each process utilizes different techniques and materials to create high-quality plastic molds.
1. Injection Molding: Injection molding is the most common type of plastic mold making. It involves injecting melted plastic material into a mold cavity at high pressure and then cooling it to form the desired shape. This process is highly efficient and is used to produce complex and intricate plastic parts with consistent quality.
2. Blow Molding: Blow molding is another popular type of plastic mold making. It is used to create hollow products such as bottles, containers, and tanks. In this process, a molten plastic tube, also known as a parison, is formed and then inflated to take the shape of the mold cavity.
3. Compression Molding: Compression molding is used to produce larger and thicker plastic parts. It involves placing a pre-measured amount of plastic material in a heated mold cavity and applying pressure to compress it into the desired shape. This process is commonly used for manufacturing automotive parts, electrical enclosures, and appliance components.
4. Thermoforming: Thermoforming is a process where a plastic sheet is heated and stretched over a mold to form the desired shape. The sheet is then cooled and trimmed to produce the final product. Thermoforming is often used for creating packaging materials, trays, and disposable products.
5. Rotational Molding: Rotational molding is suitable for producing large, hollow, and seamless plastic products. In this process, powdered plastic material is placed inside a heated mold, which is then rotated slowly in multiple axes to distribute the material evenly. As the mold cools, the plastic solidifies, and the finished product can be removed.
6. Extrusion Molding: Extrusion molding involves forcing melted plastic material through a die to create continuous profiles or specific shapes. The formed plastic is then cooled and cut into desired lengths. This process is commonly used to produce items such as pipes, tubes, and sheets.
In conclusion, plastic mold making processes include injection molding, blow molding, compression molding, thermoforming, rotational molding, and extrusion molding. Each process has its own advantages and is suitable for different types of plastic products. These manufacturing techniques play a vital role in producing a wide range of plastic products we use in our daily lives.
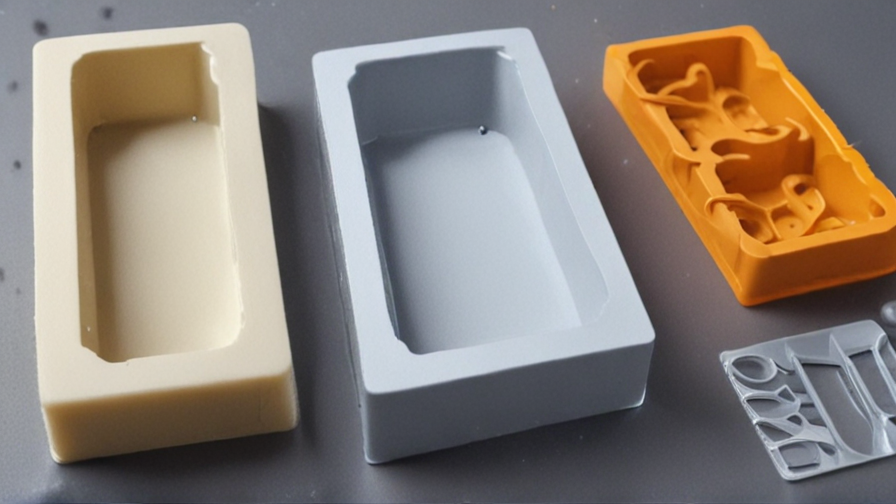
Pros and Cons of Using plastic mould making
Plastic mould making is a popular and efficient technique used to mass-produce plastic products. However, like any manufacturing process, it has its pros and cons. Here are some key points to consider:
Pros:
1. Cost-effective: Plastic mould making is generally cost-effective, especially when producing large quantities of plastic products. The initial investment in creating the mould is balanced out by the savings achieved through mass production.
2. High precision and accuracy: Moulds ensure consistent replication of the desired product. This precision allows for high-quality products with minimal variation in size, shape, and other specifications.
3. Fast production cycle: Once the mould is created, the production process can be rapid. The cycle time for making each product is relatively short, ensuring quick turnaround times and increased productivity.
4. Design flexibility: Plastic moulds enable designers to create products with complex and intricate designs that would be difficult to achieve through other manufacturing processes. The flexibility in design allows for innovation and customization of products.
5. Wide material selection: Plastic mould making is compatible with a variety of plastic materials, including thermoplastics and thermosetting plastics. This versatility offers options for different product requirements, such as strength, durability, and heat resistance.
Cons:
1. High initial cost: Creating the mould for plastic injection moulding can be relatively expensive. The costs associated with design, prototyping, and manufacturing the mould can be significant, especially for smaller businesses or startups.
2. Limited design modifications: Once the mould is created, making design modifications can be challenging and costly. Changing the design may require creating a new mould from scratch, which can disrupt production and add to expenses.
3. Environmental impact: Plastic mould making contributes to plastic waste generation. Improper disposal of plastic waste can harm the environment, leading to pollution of land and water bodies. Concerns about sustainability and waste management should be addressed when considering plastic mould making.
4. Long lead times: Developing a high-quality mould can take time, especially when the design and manufacturing processes are complex. The lead time to obtain the final mould needed for production can be longer compared to other manufacturing methods.
5. Limited product scalability: Once the mould is created, it is designed for a specific product. Scaling up production or producing a new product may require creating additional moulds, which can add to costs and lead times.
In conclusion, plastic mould making offers numerous benefits such as cost-effectiveness, precision, and design flexibility. However, it also has limitations like high initial costs, limited design modifications, and environmental concerns. It is essential to carefully evaluate these pros and cons to determine if plastic mould making is the right manufacturing process for a specific product or business.
plastic mould making Reference Specifications (varies for different product)
When it comes to plastic mould making, it is essential to consider various reference specifications that may vary depending on the product being manufactured. These specifications ensure that the mould meets specific requirements and quality standards. While the exact details may differ for different products, there are some general guidelines that can be followed.
Firstly, the design of the mould should be based on the product’s intended use and characteristics. The dimensions, shape, and surface finish of the mould should be in line with the product requirements. Factors such as wall thickness, draft angles, and parting lines need to be carefully considered to facilitate proper moulding.
The choice of materials for the mould is crucial for its durability and longevity. High-quality steel, such as tool steel or stainless steel, is commonly used due to its excellent wear resistance and ability to withstand high temperatures. The hardness and toughness of the mould material should be appropriate for the specific plastic resin being used.
The cooling system is another important aspect of mould design. An efficient cooling system ensures faster cycle times and prevents defects like warping or shrinkage. The cooling channels should be strategically placed to ensure uniform cooling throughout the mould.
The mould should also include provisions for ejecting the finished product. Ejector pins or plates are commonly incorporated to aid in the removal of the product from the mould. The design should account for smooth ejection without causing any damage to the product.
In addition, attention should be given to venting within the mould. Proper venting allows the escape of air or gas during the injection process, preventing defects like air traps or burn marks. The vents should be designed in a way that ensures minimal resistance to the flow of plastic material.
Finally, it is essential to conduct frequent maintenance and inspections of the mould to ensure its optimal performance. Regular cleaning, lubrication, and inspection for wear or damage should be carried out to prevent any defects or interruptions in the production process.
In conclusion, plastic mould making requires careful consideration of various reference specifications to ensure the production of high-quality products with minimal defects. By paying attention to aspects such as design, materials, cooling systems, ejection mechanisms, venting, and maintenance, manufacturers can achieve efficient and reliable plastic moulds for their specific products.
Applications of plastic mould making
Plastic mold making plays a crucial role in various industries, offering a wide range of applications. From manufacturing consumer goods to producing intricate parts for machinery, plastic mold making provides endless possibilities. Here are some key applications of plastic mold making:
1. Automotive industry: Plastic mold making is extensively used in the automotive sector for manufacturing various components, such as dashboards, interior trim, bumpers, and exterior body parts. These molds enable the production of parts with complex shapes, high precision, and excellent surface finish, providing durability and aesthetic appeal to automobiles.
2. Packaging industry: Plastic mold making is heavily relied upon in the packaging industry for producing containers, bottles, caps, and other packaging materials. These molds allow for the production of lightweight, stackable, and cost-effective packaging solutions. Additionally, plastic molds offer flexibility in design, allowing customization based on specific product requirements.
3. Electronics industry: Plastic mold making is crucial in the electronics industry for manufacturing components like casings, connectors, and housing for devices such as smartphones, laptops, and appliances. These molds facilitate the production of parts with precise dimensions, electrical insulation properties, and surface finishes required for electronic devices.
4. Medical industry: Plastic mold making is widely used in the healthcare sector for creating medical devices, laboratory equipment, and disposable products. Some examples include syringes, IV components, catheters, and surgical instruments. The molds ensure superior hygiene, high accuracy, and the ability to produce sterile products, contributing to the overall safety and effectiveness of medical practices.
5. Consumer goods industry: Plastic mold making is essential in the production of a wide array of consumer goods, including toys, kitchenware, household appliances, and sports equipment. Plastic molds offer the advantage of fast and efficient mass production, allowing manufacturers to meet the demands of large-scale consumer markets.
6. Aerospace industry: Plastic mold making finds applications in the aerospace industry for producing lightweight and strong components, such as air ducts, brackets, and interior panels. These molds enable the creation of high-precision parts that meet the stringent safety and performance standards of the aerospace sector.
In conclusion, plastic mold making has diverse applications in various industries, including automotive, packaging, electronics, medical, consumer goods, and aerospace. Its ability to produce complex shapes, high-precision parts, and customizable designs makes it an indispensable process for the modern manufacturing world.
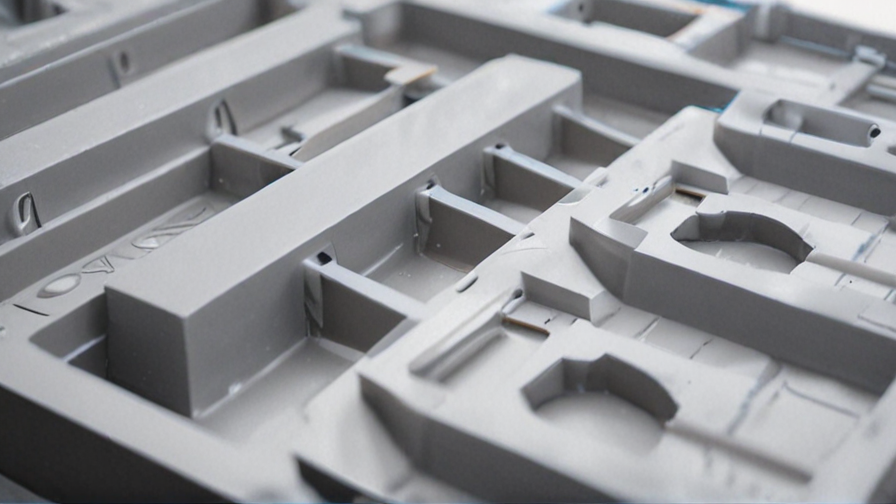
The Work Process and how to use plastic mould making
The process of plastic mold making involves several steps to create a mold or tool that can be used to produce plastic parts. Here is a simplified overview of the work process:
1. Product Design: The first step is to design the plastic part that needs to be manufactured. This involves creating a 3D CAD model using specialized software.
2. Mold Design: Once the product design is finalized, a mold design is created. This includes determining the number of cavities, the parting line, and the cooling system. The mold design will determine the shape, size, and features of the final plastic part.
3. Material Selection: The appropriate plastic material is then selected based on the desired properties of the part such as strength, flexibility, and appearance.
4. Mold Making: The mold making process starts by creating a master pattern or prototype of the part. This can be made using various techniques like CNC machining, 3D printing, or hand sculpting. This master pattern is used to create the mold.
5. Mold Fabrication: The mold is fabricated by pouring or injecting a liquid material, typically made of silicone or urethane, around the master pattern. Once the liquid material cures, it forms a mold that replicates the shape of the part.
6. Mold Testing: The mold is tested to ensure it meets the required specifications. This may involve conducting trial runs to check for any defects or issues in the final plastic part.
7. Production: Once the mold is approved, it is ready for production. Molten plastic is injected into the cavity of the mold, which then solidifies to form the final plastic part. The mold can be used repeatedly to produce multiple parts.
To make efficient use of plastic mold making, it is important to consider factors such as the complexity of the part, the desired quantity of parts, and the quality requirements. Additionally, using advanced techniques like computer-aided design and manufacturing (CAD/CAM) can help streamline the process and ensure the accuracy and precision of the mold. Regular maintenance and cleaning of the mold is also crucial to prolong its lifespan and ensure consistent part quality.
Quality Testing Methods for plastic mould making and how to control the quality
When it comes to quality testing methods for plastic mould making, there are several key steps and techniques that can be employed to ensure the desired level of quality is achieved. These methods help in controlling and monitoring the entire manufacturing process, from design to production to final inspection.
Firstly, the quality of the plastic mould can be verified through dimensional inspection. This involves measuring key dimensions and tolerances of the mould components using precise tools such as calipers, micrometers, and coordinate measuring machines (CMM). Deviations from the intended specifications can indicate potential issues that need to be addressed.
Secondly, visual inspection is carried out to identify any surface defects or imperfections. This can be done using techniques like magnification, color contrast, or special lighting to ensure a thorough examination of the mould surface. Any surface defects can be promptly addressed to maintain the quality of the mould.
Furthermore, functional testing is essential to ensure the mould performs as intended. This involves running trial productions using the mould to verify its functionality, consistency, and accuracy. Samples produced using the mould are inspected for any defects, such as warping, flashing, or inaccuracies in part dimensions.
To control the quality during the plastic mould making process, regular monitoring and documentation are crucial. Key process parameters such as temperature, pressure, and cooling time need to be recorded and monitored throughout production. This helps to identify any variations or deviations from the optimal settings, enabling timely corrective actions.
Additionally, quality control checks can also be implemented at various stages of plastic mould making. This includes checking the quality of raw materials, such as the plastic resin used, to ensure it meets the required standards. Intermediate inspections can be performed during the mould fabrication process to catch any potential issues early on.
To summarize, quality testing methods for plastic mould making involve dimensional inspection, visual inspection, and functional testing. Regular monitoring and documentation help to control the quality, while implementing quality control checks at different stages ensures a high-quality final product. By utilizing these methods, manufacturers can produce plastic moulds that meet the desired specifications and quality standards.
plastic mould making Sample Policy and Post-Purchase Considerations for plastic mould making from China
Sample Policy for Plastic Mould Making from China:
1. Initial communication: When considering purchasing plastic moulds from China, it is crucial to establish effective communication channels with the supplier. Clearly explain your requirements, including specifications, quantities, and desired quality. Provide any necessary drawings or samples to ensure accurate understanding.
2. Request for samples: It is advisable to request samples before placing a bulk order. This allows you to evaluate the supplier’s quality standards, precision, and finishing. Pay attention to the material used, durability, and any defects or imperfections. Evaluate the samples thoroughly to ensure they meet your desired standards.
3. Quality control: Discuss with the supplier their quality control procedures, certifications, and any relevant testing procedures in place. Make sure they comply with international standards such as ISO 9001. Regular inspections during production and before shipment are crucial to ensure the moulds meet your specifications.
4. Payment terms: Negotiate and agree upon payment terms before making any payments. Common options include a percentage deposit, with the balance paid upon completion before shipment. Be cautious of making full payments upfront, especially when dealing with a new supplier.
5. Production timeline: Clearly establish the production timeline, including lead time, sampling time, and estimated delivery dates. Ensure the supplier has sufficient capacity to meet your timeline requirements. Regularly communicate with the supplier to monitor progress and any potential delays.
Post-Purchase Considerations for Plastic Mould Making from China:
1. Inspection upon delivery: Upon receiving the moulds, perform a comprehensive inspection to verify that they meet the specified requirements. Inspect for any damage during transportation, ensure proper packaging, and confirm the correct quantity as per your order.
2. After-sales support: Discuss the supplier’s after-sales support and warranty policy. In case of any defects or issues with the moulds, ensure you have a clear understanding of the actions the supplier will take to rectify the situation.
3. Feedback and future collaboration: Provide constructive feedback to the supplier regarding the moulds’ performance and any room for improvement. This can enhance the future collaboration and help the supplier understand your requirements better.
4. Maintain a good relationship: Establishing a good relationship with the supplier is crucial for future collaborations. Timely payments, open communication, and prompt feedback can foster a long-term partnership and ensure smooth future transactions.
In conclusion, when considering plastic mould making from China, clear communication, sample evaluation, quality control, payment terms, and post-purchase considerations are vital to ensure a successful and satisfactory transaction. Regular communication and maintaining a good relationship with your supplier can contribute to fruitful collaborations in the future.
Sourcing plastic mould making from China: Opportunities, Risks, and Key Players
Sourcing plastic mould making from China presents both opportunities and risks. China is a leading global manufacturer of plastic moulds, offering a wide range of options at competitive prices. The country’s established infrastructure and experienced workforce make it an attractive destination for businesses looking to reduce production costs or expand their manufacturing capabilities.
One of the significant opportunities in sourcing plastic moulds from China is cost advantage. Chinese manufacturers often offer lower prices due to lower labor and production costs. This cost-effectiveness enables businesses to access high-quality moulds at a fraction of the cost compared to suppliers in other countries. Additionally, China’s vast production capacity allows for greater flexibility and faster turnaround times.
However, there are also risks associated with sourcing from China. Quality control can be a challenge, as some manufacturers may prioritize low-cost production and compromise on product quality. It is crucial for businesses to conduct thorough due diligence to ensure that suppliers have the necessary certifications, compliance with international standards, and a proven track record of delivering high-quality products.
Intellectual property protection is another concern when sourcing from China. Unscrupulous manufacturers may attempt to copy or steal designs and technologies, posing a risk to businesses’ intellectual property rights. Implementing strict intellectual property protection measures and signing non-disclosure agreements are critical for safeguarding proprietary information.
When sourcing plastic moulds from China, it is advisable to work with reputable and reliable manufacturers. Some key players in the Chinese plastic mould industry include Taizhou Huangyan JMT Mould Co., Ltd., Taizhou Tengfei Mould Factory, and Zhejiang Huangyan Yongqiang Plastic Mould Factory. These companies have a proven track record and are known for their quality craftsmanship and customer service.
In conclusion, sourcing plastic mould making from China offers significant opportunities in terms of cost-effectiveness and production capacity. However, businesses must carefully assess the associated risks, including quality control and intellectual property protection. By working with reputable manufacturers, businesses can access high-quality plastic moulds at competitive prices while mitigating potential risks.
How to find and select reliable plastic mould making manufacturers in China,use google search manufacturers and suppliers
Finding and selecting reliable plastic mold making manufacturers in China can be a daunting task, but with the right approach and resources, it can be simplified. Here are a few steps to follow:
1. Start with a Google search: Use relevant keywords such as “plastic mold making manufacturers in China” or “reliable plastic mold suppliers.” This will provide you with a list of potential manufacturers.
2. Verify their website and credentials: Visit the websites of the manufacturers that appear in the search results. Look for information about their experience, certifications, production capabilities, and samples of their previous work. Assess their credibility in the industry.
3. Check supplier directories and platforms: Explore reputed B2B platforms like Alibaba, Made-in-China, or Global Sources. These platforms provide extensive directories of manufacturers in China with detailed profiles, certifications, customer reviews, and ratings. Narrow down your potential options based on their reputation and customer feedback.
4. Request quotations and evaluate responsiveness: Contact the shortlisted manufacturers and request quotations based on your specific mold requirements. Assess their responsiveness and ability to communicate effectively. Prompt and clear responses indicate a reliable manufacturer who values customer satisfaction.
5. Conduct background checks: Do some research on the shortlisted manufacturers to ensure their reliability. Check for any negative reviews or complaints from previous customers. Look for testimonials, certifications, and business registration details. This will help you gauge their reputation and reliability.
6. Consider a factory visit or third-party inspections: If feasible, plan a visit to the manufacturer’s facilities in China. This will help you assess their production processes, quality control measures, and overall infrastructure. In case a visit is not feasible, consider hiring a third-party inspection service to evaluate the manufacturer’s capabilities and quality standards.
7. Ask for samples and evaluate quality: Requesting sample molds is essential to understand the manufacturer’s capabilities and assess the quality of their work. This will allow you to check the surface finish, accuracy, and durability of the molds they produce.
8. Evaluate pricing and terms: Compare the quotations received from different manufacturers based on quality, production capability, lead time, and pricing. Remember that the cheapest option is not always the best choice. Select a manufacturer that offers a balance between quality and price, along with favorable payment terms.
Overall, thorough research, diligent evaluation, and proper due diligence are essential to find reliable plastic mold making manufacturers in China.
How to check plastic mould making manufacturers website reliable,use google chrome SEOquake check if ranking in top 10M
To check the reliability of a plastic mold making manufacturer’s website, one effective way is to use Google Chrome with the SEOquake extension. By following these steps, you can assess the website’s ranking and credibility:
1. Install SEOquake Extension: Open Google Chrome browser and search for the SEOquake extension. Install the extension on your browser.
2. Search for Relevant Keywords: In the Google search bar, enter keywords related to plastic mold making or the specific manufacturer’s name.
3. Analyze Search Results: Look for the plastic mold making manufacturer’s website in the search results. Ideally, reliable manufacturers often rank among the top 10 million websites.
4. Use SEOquake: Once you have reached the manufacturer’s website, activate the SEOquake extension by clicking on its icon in the browser toolbar.
5. Check Alexa Rank: A pop-up window will appear with various metrics. Look for the “Alexa Rank” section, which indicates the website’s overall popularity. A lower Alexa rank generally signifies a higher level of credibility.
6. Evaluate Other Metrics: Aside from Alexa Rank, SEOquake provides additional information such as domain age, organic search visibility, number of indexed pages, and social media metrics. Assessing these metrics can give you an overall idea of the website’s online performance.
7. Navigate the Website: While analyzing the website’s ranking is useful, don’t solely rely on it. Explore the manufacturer’s website thoroughly to check if the information provided is comprehensive, up to date, and well-structured. Look for product details, certifications, customer testimonials, and a clear contact page.
Remember, using SEOquake and analyzing a manufacturer’s website ranking is just one step in assessing reliability. It’s also important to consider other factors, such as the manufacturer’s reputation, customer reviews, and industry certifications.
Top 10 plastic mould making manufacturers in China with each 160 words introduce products,then use markdown create table compare
1. Sositar Mould: With extensive experience in plastic mould making, Sositar Mould specializes in designing and manufacturing high-quality injection molds for a wide range of industries. Their products include precision molds for automotive components, household appliances, medical devices, and consumer products.
2. Xiamen DTG Tech Co., Ltd.: DTG Tech offers a comprehensive range of plastic mould making services. Their products cover various industries, such as electronics, automotive, and household. Their expertise lies in the production of injection molds, blow molds, and extrusion molds.
3. Fowmould: Fowmould is a leading manufacturer of plastic injection molds in China. They provide excellent precision molds for industries like automotive, electronics, and medical. Their products are known for their high accuracy, durability, and cost-effectiveness.
4. HQ Mould: HQ Mould focuses on the production of plastic injection molds for household appliances, automotive parts, and industrial components. They have rich experience in mold design and production, ensuring top-notch quality and performance.
5. TSY Mould: TSY Mould specializes in manufacturing custom plastic injection molds for various industries, including automotive, electronics, and medical. They offer a wide range of mold types, including two-shot molds, gas-assisted molds, and hot runner molds.
6. Sinotech Mold Co., Ltd.: Sinotech Mold delivers quality plastic injection molds customized to meet clients’ specific needs. They have experience in manufacturing molds for automotive, electronic, and consumer product industries, providing reliable and efficient solutions.
7. Asia Billion Industrial Co., Ltd.: Asia Billion offers precision plastic mould making for industries such as automotive, medical, and consumer electronics. They excel in creating multi-cavity molds, high-precision molds, and overmolding solutions.
8. Chuangyuan Mould: Chuangyuan specializes in designing and manufacturing plastic injection molds for electronic components, automotive parts, and household appliances. Their molds combine durability, accuracy, and efficiency.
9. Mold-Town Industrial Co., Ltd.: Mold-Town is a reliable plastic mould making manufacturer with expertise in designing and producing molds for automotive, electronics, and medical industries. They focus on providing high-quality molds and exceptional customer service.
10. Topworks Plastic Mold: Topworks is known for its high-quality plastic injection molds used in automotive, electronic, and medical sectors. Their molds are manufactured with advanced technology and offer excellent precision and repeatability.
| Manufacturer | Products |
| :————————————————————————: | :————————————————–: |
| Sositar Mould | Precision molds for automotive, household appliances, medical devices, and consumer products |
| Xiamen DTG Tech Co., Ltd. | Injection molds, blow molds, and extrusion molds |
| Fowmould | Precision molds for automotive, electronics, and medical industries |
| HQ Mould | Plastic injection molds for household appliances, automotive parts, and industrial components |
| TSY Mould | Custom plastic injection molds, two-shot molds, gas-assisted molds, and hot runner molds |
| Sinotech Mold Co., Ltd. | Custom plastic injection molds for automotive, electronic, and consumer product industries |
| Asia Billion Industrial Co., Ltd. | Precision plastic molds for automotive, medical, and consumer electronics industries |
| Chuangyuan Mould | Plastic injection molds for electronic components, automotive parts, and household appliances |
| Mold-Town Industrial Co., Ltd. | Plastic molds for automotive, electronics, and medical industries |
| Topworks Plastic Mold | High-quality plastic injection molds for automotive, electronic, and medical sectors |
Background Research for plastic mould making manufacturers Companies in China, use qcc.com archive.org importyeti.com
China is known as the world’s largest manufacturing hub and is home to numerous plastic mold making manufacturers. Some popular platforms to find information about these companies include qcc.com, archive.org, and importyeti.com.
Qcc.com is a comprehensive business information platform in China that provides data on registered companies. It offers detailed company profiles, contact information, and business history. By searching for “plastic mould making manufacturers” on qcc.com, one can gather relevant information such as company names, addresses, registration numbers, and contact details.
Archive.org is a digital archive platform that stores snapshots of web pages from various periods. By searching for specific company websites involved in plastic mold making manufacturing, one can access archived versions of their websites. This can be useful for gaining insights into their past operations, product portfolio, and any changes they might have made over time.
Importyeti.com is an import-export data intelligence platform that compiles trade records from various sources. It provides information on the sourcing and shipment details of imported and exported products. By searching for plastic mold making manufacturers on Importyeti.com, one can find companies that have engaged in international trade activities. This data can be useful for assessing their export capabilities and identifying potential business partners.
Using these platforms, researchers can access the background information of plastic mold making manufacturers in China. Such information is crucial for evaluating their credibility, industry experience, production capacity, and other relevant factors when considering potential business collaborations. It is important to thoroughly analyze the gathered information and conduct further research to ensure the reliability and suitability of potential partners.
Leveraging Trade Shows and Expos for plastic mould making Sourcing in China
Trade shows and expos provide an excellent platform for sourcing plastic mold making services in China. These events offer a unique opportunity to connect with numerous suppliers, gain insights into the latest industry trends, and establish valuable business relationships. When leveraging trade shows and expos for sourcing plastic mould making in China, it is crucial to follow certain strategies to maximize the benefits.
Firstly, thorough research and planning are essential before attending a trade show or expo. Identifying the most relevant and reputable events in the plastic mold making industry, specifically those with a focus on China, is crucial. This ensures that the exhibiting companies will offer the required services and that the event attracts a significant number of quality suppliers.
Once the appropriate event is chosen, it is crucial to establish clear objectives and expectations for attending. This involves defining what specific plastic mould making requirements need to be sourced and setting realistic goals for initiating partnerships with potential suppliers.
During the event, it is vital to visit booths, engage with exhibitors, and gather relevant information about their capabilities, experience, and quality standards. Attending conferences, seminars, or presentations can provide valuable insights into the latest developments in plastic mold making and help identify potential suppliers.
Networking is a key aspect of trade shows and expos. Building relationships with suppliers, industry experts, and other attendees can lead to valuable connections and partnerships. Maintaining a professional approach, sharing business cards, and scheduling follow-up meetings or discussions with potential suppliers are effective ways to take advantage of networking opportunities.
Additionally, conducting due diligence and verifying suppliers’ qualifications is essential. Gathering information about their production capacity, quality control measures, certifications, and past clients can help ensure the reliability and suitability of chosen suppliers.
In conclusion, trade shows and expos present a valuable opportunity for sourcing plastic mould making services in China. Thorough research, clear objectives, effective networking, and diligent supplier evaluation are key strategies to leverage these events successfully. Following these practices within the limited word count of 300 will help ensure efficient sourcing and establish beneficial partnerships for plastic mold making in China.
The Role of Agents and Sourcing Companies in Facilitating plastic mould making Purchases from China
Agents and sourcing companies play a crucial role in facilitating plastic mold making purchases from China. They act as intermediaries between buyers and suppliers, utilizing their expertise, networks, and local knowledge to streamline the procurement process. These professionals help overseas buyers navigate the complexities of engaging with Chinese manufacturers, ensuring a successful and smooth transaction.
One of the primary responsibilities of agents and sourcing companies is to identify reliable and qualified mold manufacturers in China. They have a deep understanding of the local market and can assess suppliers based on their capabilities, quality standards, certifications, and track record. This saves buyers significant time and effort in searching for reputable manufacturers and mitigates the risk of fraud or dealing with unreliable suppliers.
Agents and sourcing companies also aid in negotiating the best terms and prices on behalf of the buyer. With their extensive industry knowledge and experience, they can ensure that buyers receive the most competitive quotes and avoid overpaying for the plastic molds. Their negotiation skills and established relationships with suppliers enable them to secure favorable terms, such as lower prices, faster lead times, or customization options, to meet the buyer’s specific requirements.
Quality control is another crucial aspect where agents and sourcing companies add value. They perform rigorous factory assessments, conduct inspections during production, and quality checks before shipment to ensure that the finished plastic molds meet the buyer’s expectations and comply with international standards. Their presence on the ground enables them to closely monitor the manufacturing process, identify potential issues, and address them promptly, minimizing the risk of defective or subpar products reaching the buyer.
Furthermore, agents and sourcing companies handle logistics, shipping, and customs clearance, making the import process seamless for the buyer. They have expertise and established relationships with shipping companies, freight forwarders, and customs officials, ensuring smooth and timely delivery of the plastic molds to the buyer’s location. They also assist with all documentation and paperwork required for import and provide guidance on tariff regulations and compliance.
In summary, agents and sourcing companies play a critical role in facilitating plastic mold making purchases from China. Their expertise, networks, and local knowledge enable them to identify reliable suppliers, negotiate favorable terms, ensure quality control, and manage logistics. By partnering with these professionals, buyers can navigate the complexities of dealing with Chinese manufacturers and have a successful sourcing experience.
Price Cost Research for plastic mould making manufacturers Companies in China, use temu.com and 1688.com
When it comes to sourcing plastic mould making manufacturers in China, two popular online platforms that can be utilized are temu.com and 1688.com. These platforms provide a comprehensive database of suppliers along with information about their products, capabilities, and pricing.
temu.com is a global supply chain platform that connects manufacturers and buyers worldwide. By using this platform, buyers can easily browse through a wide range of plastic mould making manufacturers in China. temu.com provides detailed product descriptions, manufacturing capabilities, certifications, and customer reviews, making it easier for buyers to assess the reliability and quality of the suppliers. In addition, temu.com allows users to request quotations directly from the suppliers to get accurate pricing information.
Another popular platform for sourcing from China is 1688.com, which is owned by Alibaba Group. Although it is primarily in Chinese language, it is a valuable resource for finding plastic mould making manufacturers. 1688.com offers a vast selection of suppliers, enabling buyers to find the best matches for their requirements. While navigating the platform might be slightly challenging for non-Chinese speakers, it provides detailed product information, negotiation options, and customer reviews. Buyers can also contact suppliers directly through the platform to inquire about pricing and negotiate deals.
When conducting price cost research on these platforms, it is essential to consider various factors that may affect the final pricing. These factors include the complexity of the mold design, material selection, manufacturing processes, and order quantity. Buyers should provide clear specifications when requesting quotations to receive accurate pricing details.
In conclusion, temu.com and 1688.com are valuable online platforms for researching and sourcing plastic mould making manufacturers in China. By utilizing these platforms, buyers can access detailed supplier information, request quotations, and compare prices to make informed decisions. However, it is crucial to consider the various factors that influence pricing to ensure a fair assessment of the costs involved.
Shipping Cost for plastic mould making import from China
The shipping cost for plastic mould making import from China can vary depending on various factors such as the size, weight, and quantity of the molds, destination country, shipping method chosen, and any additional services required.
There are generally two main shipping methods for importing goods from China – air freight and sea freight. Air freight is faster but more expensive, while sea freight is slower but more cost-effective for larger shipments.
For smaller shipments or urgent orders, air freight is usually the preferred option. The cost of air freight for plastic mould making can range from $4 to $8 per kilogram, with additional charges for fuel surcharge, security fees, customs clearance, and handling fees. The total cost can be estimated by multiplying the weight of the molds by the air freight rate and adding the additional charges.
For larger shipments, sea freight is the more economical option. The cost of sea freight is usually calculated based on the volume or weight of the shipment, whichever is higher. The approximate cost of sea freight for plastic mould making can range from $400 to $800 per cubic meter, depending on the destination and shipping company. Additional charges such as customs clearance, local handling fees, and documentation fees may also apply.
It is important to note that these estimates are just approximate figures and can vary based on the specific requirements and circumstances of each shipment. It is recommended to obtain quotes from multiple shipping companies to compare prices and choose the most suitable option.
Furthermore, it is essential to consider any additional expenses such as customs duties, import taxes, insurance, and port fees that may be incurred during the import process. These costs should be factored into the overall budget for importing plastic mould making from China. Consulting with a shipping agent or freight forwarder can provide a more accurate cost assessment and streamline the import process.
Compare China and Other plastic mould making Markets: Products Quality and Price,Visible and Hidden Costs
China is the largest plastic mould making market globally, with a strong reputation for manufacturing and exporting a wide range of plastic mould products. When comparing China to other plastic mould making markets, several factors stand out: product quality, price, visible and hidden costs.
In terms of product quality, China offers both advantages and disadvantages. On one hand, China has a vast number of experienced mould makers who have perfected their craft over the years. This expertise and dedication to quality ensure that many plastic mould products produced in China are of high quality, meeting international standards. On the other hand, there have been concerns about the consistency of product quality in China due to the large number of manufacturers and the varying levels of expertise. It is therefore essential for buyers to carefully select reputable manufacturers to ensure consistent product quality.
Price is often a crucial consideration when comparing plastic mould making markets. China has a notable advantage in terms of cost-effectiveness. The country’s large manufacturing infrastructure and economies of scale allow for competitive pricing. China’s low labor costs also contribute to lower product prices. However, it is important to note that while China’s prices may be lower on the surface, hidden costs such as import tariffs, shipping fees, and quality control inspections can add to the overall cost. Buyers must carefully evaluate both the visible and hidden costs when making price comparisons.
Visible costs, such as the actual price of the plastic mould, are relatively easy to compare across markets. However, hidden costs can be more challenging to discern. For example, importing plastic moulds from China may involve additional costs such as customs duties, taxes, and shipping fees, which can significantly impact the overall cost. Additionally, quality control and inspection costs may also be necessary to ensure that the products meet the required standards. It is crucial to consider these hidden costs when comparing different markets to make an informed decision.
In summary, China’s plastic mould making market offers a combination of advantages and challenges when compared to other markets. It is known for its wide range of high-quality plastic mould products, but consistency may often be a concern. China’s competitive pricing due to low labor costs and manufacturing capabilities makes it an attractive option, but buyers should carefully evaluate the visible and hidden costs associated with importing from China. By considering these factors, buyers can make informed decisions when choosing a plastic mould making market that best suits their needs.
Understanding Pricing and Payment Terms for plastic mould making: A Comparative Guide to Get the Best Deal
When it comes to plastic mould making, understanding pricing and payment terms is crucial to ensure you get the best deal possible. This comparative guide aims to shed light on these aspects, helping you navigate the process effectively.
The pricing for plastic mould making varies based on several factors. These may include the complexity of the mould design, size and dimensions, material requirements, and the quantity of moulds needed. It’s important to compare quotes from different suppliers to gauge a fair price range. Keep in mind that excessively low prices may indicate compromise in quality and durability.
Payment terms also play a significant role in securing the best deal. Common payment arrangements include upfront payments, milestone-based payments, and instalment plans. It’s essential to negotiate payment terms that align with your budget and project timeline. Consider factors like cash flow, supplier credibility, and your relationship with the supplier when determining suitable payment terms.
Additionally, understanding the breakdown of costs within the pricing is crucial. Obtain a detailed quote that includes expenses for design, material procurement, machining, finishing, and any additional services provided. This will enable you to compare costs accurately and identify any hidden charges.
To get the best deal, consider the reputation and experience of the mould maker. Look for suppliers who have a proven track record of delivering high-quality moulds within the agreed timeline. Reviews and references can provide valuable insights into their reliability and customer satisfaction.
Furthermore, consider the supplier’s production capabilities and capacity. A reputable mould maker should have state-of-the-art machinery and equipment, allowing for efficient and precise manufacturing. This can impact the price, timeline, and overall quality of the mould.
Lastly, be proactive in engaging with the supplier during the quotation and negotiation process. Clearly communicate your requirements and expectations, ensuring that all parties are on the same page. This will help minimize misunderstandings and reduce the chances of unexpected costs or delays.
In summary, understanding pricing and payment terms when it comes to plastic mould making is crucial for securing the best deal. Consider various factors like pricing breakdown, payment arrangements, supplier reputation, production capabilities, and effective communication. By utilizing this comparative guide, you can approach the process with confidence, ultimately ensuring high-quality moulds within your budget and timeline.
Chinese Regulations and Industry Standards Certifications for plastic mould making,Import Regulations and Customs for plastic mould making from China
China is a major player in the plastic mould making industry, and as such, it has established various regulations and industry standards certifications to ensure the quality and safety of its products. These regulations are crucial for both domestic manufacturers and exporters looking to supply plastic moulds to international markets.
One of the essential certifications for plastic mould making in China is the ISO 9001:2015. This certification ensures that the manufacturer has a quality management system in place, emphasizing the consistency and reliability of their products. Manufacturers are required to meet specific criteria and undergo regular audits to maintain this certification.
Additionally, the China Compulsory Certification (CCC) is necessary for products that are considered to have potential safety risks. While this certification is not mandatory for plastic moulds, it may be required for some electrical or electronic components incorporated into the moulds.
When importing plastic moulds from China, it is vital to comply with import regulations and customs procedures. It is crucial to work with an experienced freight forwarder who can help navigate the complex import procedures and ensure compliance with the destination country’s regulations.
Customs duties and taxes may also apply when importing plastic moulds. Importers should familiarize themselves with the specific tariff codes applicable to plastic moulds and determine the applicable duties and taxes for their particular situation.
To facilitate the importation process, it is advisable to obtain all relevant documentation from the Chinese manufacturer, such as commercial invoices, packing lists, and certificates of origin. These documents will be required by customs authorities to verify the origin and value of the goods.
In conclusion, ensuring compliance with Chinese regulations and industry standard certifications is essential when dealing with plastic mould making. Importers should also be aware of the import regulations and customs procedures in their respective countries to ensure a smooth process.
Sustainability and Environmental Considerations in plastic mould making Manufacturing
Sustainability and environmental considerations play a crucial role in the plastic mould making manufacturing process. With the increasing need for sustainable practices, it is essential for manufacturers to prioritize eco-friendly approaches to minimize their environmental impact. Here are some key considerations in plastic mould making manufacturing:
1. Material Selection: Opting for environmentally friendly materials is vital. Manufacturers should choose recyclable or biodegradable plastics, such as PLA or PHA, over conventional plastics like PVC or ABS. This reduces the long-term ecological effects and promotes a circular economy.
2. Energy Efficiency: Implementing energy-efficient practices helps to reduce greenhouse gas emissions. Using advanced machines with lower energy consumption, optimizing production processes, and investing in energy-efficient technologies are effective ways to ensure sustainability.
3. Waste Management: Proper waste management is crucial in plastic mould making manufacturing. Manufacturers should implement recycling programs to reuse leftover plastics from the moulding process. Additionally, integrating waste reduction techniques like lean manufacturing can minimize scrap and material wastage.
4. Water Conservation: Water consumption during the manufacturing process should be minimized. Installing water recycling systems and using closed-loop cooling systems can reduce water usage. Moreover, employing water-efficient cleaning techniques and optimizing machine operations further contribute to sustainability.
5. Emissions Control: The release of harmful emissions should be minimized. Manufacturers need to invest in pollution control technologies like air filtration systems and implement best practices to reduce air pollution. This helps in maintaining a clean and healthy working environment.
6. Supply Chain Optimization: Collaborating with suppliers that follow sustainable practices is essential. Manufacturers can ensure reduced carbon footprints by sourcing materials locally, optimizing transportation routes, and using eco-friendly packaging options.
7. Life Cycle Assessment: Conducting a life cycle assessment helps evaluate the overall environmental impact of the plastic mould making process. This assessment considers raw material extraction, manufacturing, usage, and disposal. It helps identify areas for improvement and implement eco-friendly practices throughout the entire life cycle.
By integrating sustainability and environmental considerations into plastic mould making manufacturing, manufacturers can contribute to a greener future. Prioritizing the use of eco-friendly materials, reducing energy and water consumption, implementing waste management strategies, controlling emissions, optimizing the supply chain, and conducting life cycle assessments are key measures that promote a more sustainable approach in plastic mould making manufacturing.
List The Evolution history of “plastic mould making”
Plastic mould making has evolved significantly over the years to meet the increasing demand for plastic products in various industries. Here is a brief overview of the evolution history of plastic mould making:
1. Early Techniques and Materials:
Plastic mould making traces its roots back to the late 19th century when early techniques like compression moulding were employed. These techniques involved applying pressure to shape plastic materials, such as celluloid and bakelite, into desired forms. These materials were initially used to create simple objects like buttons and combs.
2. Injection Moulding:
The breakthrough in plastic mould making came with the invention of injection moulding in the 1930s. It revolutionized the industry by enabling mass production of plastic products. In injection moulding, molten plastic material is injected into a mould cavity under high pressure, resulting in the desired shape when cooled. This technique enabled the production of complex and detailed plastic items, from household goods to automotive components, at a faster rate.
3. Advancements in Materials:
With ongoing research and development, various plastic materials were introduced, offering enhanced properties and versatility in plastic mould making. For instance, in the 1950s, polyethylene and polypropylene were introduced, followed by polyvinyl chloride (PVC) in the 1960s. These new materials expanded the range of plastic products that could be manufactured.
4. Computer-Aided Design (CAD) and Computer-Aided Manufacturing (CAM):
In the 1980s, the integration of CAD and CAM technologies revolutionized plastic mould making. CAD enabled precise and detailed design creation using computer software, while CAM facilitated the translation of those designs into instructions for automated manufacturing machines. This integration significantly improved the accuracy, efficiency, and speed of plastic mould making.
5. Advanced Mould Making Techniques:
Recent years have seen the adoption of advanced techniques like 3D printing and CNC machining in plastic mould making. 3D printing enables the creation of complex prototypes and moulds with high accuracy and shorter lead times. CNC machining allows for precise shaping of moulds using computer-controlled cutting tools. These techniques have further broadened the possibilities and accelerated the development of plastic mould making.
In conclusion, plastic mould making has come a long way from its early techniques to the advanced methods used today. The industry has witnessed significant advancements in materials, manufacturing techniques, and technology integration, allowing for the production of a vast range of plastic products efficiently and with greater precision.
The Evolution and Market Trends in plastic mould making Industry
The plastic mold making industry has experienced significant evolution and market trends over the years. With advancements in technology and manufacturing processes, the industry has adapted to meet the growing demands of various sectors.
One of the notable evolutions in plastic mold making is the integration of computer-aided design (CAD) and computer-aided manufacturing (CAM) systems. These technologies have revolutionized the industry by enabling more precise and efficient mold designs and manufacturing processes. CAD/CAM systems allow for the creation of complex molds with intricate details, which was not possible with traditional mold making methods. This evolution has contributed to the production of high-quality and customized plastic products.
Another significant trend in the plastic mold making industry is the shift towards the use of eco-friendly materials and processes. With an increasing emphasis on sustainability and environmental consciousness, manufacturers are opting for biodegradable and recyclable plastics. Additionally, processes such as injection molding are being optimized to reduce waste and energy consumption. This trend supports the global movement towards sustainable manufacturing practices.
Market trends in the plastic mold making industry include the growth in demand for lightweight and durable plastic products. Industries such as automotive, aerospace, and consumer goods are increasingly using plastic components to reduce weight and improve fuel efficiency. This has led to a rise in the demand for molds that can produce intricate and high-performance plastic parts.
Furthermore, the rise of additive manufacturing or 3D printing has impacted the plastic mold making industry. 3D printing allows manufacturers to quickly prototype and produce plastic molds, reducing lead times and costs. This technology has democratized mold making, enabling small-scale manufacturers to enter the market more easily.
In conclusion, the plastic mold making industry has evolved with the integration of CAD/CAM systems, the adoption of eco-friendly materials and processes, and the emergence of 3D printing. These trends have contributed to the production of high-quality plastic products, increased sustainability, and improved accessibility in the industry. As the demand for lightweight and durable plastic products continues to grow, the plastic mold making industry will continue to adapt and thrive.
Custom Private Labeling and Branding Opportunities with Chinese plastic mould making Manufacturers
Chinese plastic mold making manufacturers offer a wide range of opportunities for custom private labeling and branding. With their expertise in creating high-quality molds, businesses can benefit from these manufacturers to create unique and customized products.
Private labeling allows businesses to place their brand name and logo on the products. This offers a sense of exclusivity, enabling businesses to establish a strong presence in the market. Chinese manufacturers understand the importance of branding and work closely with businesses to ensure their products align with their desired brand image.
With the advancements in technology and skilled craftsmanship, Chinese plastic mold making manufacturers can produce molds of various shapes, sizes, and complexities. This enables businesses to create products that cater to their specific requirements while maintaining consistent quality.
In addition to private labeling, Chinese manufacturers also offer branding opportunities. This includes customizing the packaging, color schemes, and designs to reflect the brand identity. By creating a unique and visually appealing product, businesses can attract and engage potential customers, leading to increased brand recognition and loyalty.
China’s competitive manufacturing costs and efficient production processes give businesses a cost advantage when it comes to custom private labeling and branding opportunities. By partnering with Chinese plastic mold making manufacturers, businesses can access affordable and high-quality molds, reducing production costs and maximizing profit margins.
In conclusion, Chinese plastic mold making manufacturers provide businesses with excellent opportunities for custom private labeling and branding. Their expertise, flexibility, and cost-effective production processes allow businesses to create unique and customized products that align with their brand image and attract customers. With the assistance of Chinese manufacturers, businesses can establish a strong and recognizable brand presence in the market.
Tips for Procurement and Considerations when Purchasing plastic mould making
1. Define your requirements: Before purchasing a plastic mould making, it is important to clearly define your requirements. Consider factors such as the size and complexity of the mould, the material it will be used for, and the desired production quantity.
2. Quality and durability: Look for moulds that are made of high-quality materials, such as hardened steel or aluminum, as these materials offer better durability and longer lifespan. Consider the design features that ensure the mould can withstand repeated use without deformation or wear.
3. Precision and accuracy: Check if the mould provides precise and accurate molding capabilities. Look for features such as tight tolerances and smooth surface finishes, as these can greatly impact the quality of the final plastic products.
4. Compatibility with plastic materials: Ensure that the mould is suitable for the plastic materials you plan to use. Different plastic resins have different properties, and the mould should be able to handle the specific requirements of the chosen material, such as temperature and pressure.
5. Customizability and flexibility: Consider if the mould can be easily customized or modified to meet specific requirements or accommodate design changes. This is particularly important if you anticipate future design iterations or the need to produce different plastic parts.
6. Supplier reputation and support: Research the reputation and reliability of the suppliers you are considering. Look for suppliers with a proven track record in manufacturing high-quality moulds and providing excellent customer support.
7. Cost considerations: Compare prices from different suppliers, but be cautious of extremely low-cost options, as they may compromise on quality and durability. Consider the overall cost-effectiveness of the mould, considering factors such as lifespan, maintenance requirements, and potential production delays or defects.
8. Delivery time and logistics: Consider the supplier’s ability to deliver the mould within your desired timeframe. Ensure that they have efficient logistics processes in place to minimize any delays or transportation issues.
9. After-sales support: Inquire about the supplier’s after-sales support, including warranty, technical assistance, and spare parts availability. It’s important to have reliable support in case of any issues or maintenance needs.
10. Environmental considerations: If sustainability is a priority for your organization, consider suppliers that offer eco-friendly or recyclable moulding solutions. Evaluate their commitment to reducing environmental impact and their adherence to relevant sustainability standards.
By carefully considering these tips and factors, you can make a well-informed decision when purchasing plastic mould making.
FAQs on Sourcing and Manufacturing plastic mould making in China
1. Why should I consider sourcing and manufacturing plastic moulds in China?
China has emerged as a global manufacturing hub and offers cost-effective solutions for plastic mould making. The country has a well-established infrastructure, skilled labor force, and advanced manufacturing technologies. Chinese manufacturers often offer competitive pricing and quick turnaround times, making it an attractive choice for businesses worldwide.
2. How can I find reliable plastic mould manufacturers in China?
To find reliable manufacturers, conduct thorough research and due diligence. Utilize online platforms, such as Alibaba, which provide a comprehensive database of verified suppliers. Furthermore, attend trade shows or exhibitions where you can meet potential suppliers in person and assess their capabilities.
3. What factors should I consider when choosing a plastic mould manufacturer in China?
Consider factors such as the manufacturer’s experience, expertise, quality control measures, certifications, production capacity, and customer reviews or references. It is crucial to evaluate their ability to meet your specific requirements and ensure they comply with international manufacturing standards.
4. How can I ensure the quality of plastic moulds manufactured in China?
Working with a manufacturer that has stringent quality control processes in place is key. Ask for their quality control certifications and their procedures for inspecting, testing, and documenting the production process. Additionally, request samples or prototypes for evaluation before placing a large order.
5. What is the typical lead time for plastic mould manufacturing in China?
The lead time varies depending on the complexity of the mould and the manufacturer’s workload. On average, it can range from a few weeks to several months. It is essential to establish clear communication and production timelines with the manufacturer to ensure timely delivery.
6. How can I manage intellectual property (IP) protection when manufacturing plastic moulds in China?
IP protection is a valid concern, but it can be managed effectively by taking certain precautions. Sign a non-disclosure agreement (NDA) with the manufacturer to protect your designs and ideas. Additionally, consider filing for patents or trademarks, both in your home country and in China, to safeguard your intellectual property rights.
7. What are the payment terms for plastic mould manufacturing in China?
Payment terms can vary between manufacturers, but it is common to pay a percentage upfront and the remaining balance upon completion or before shipment. Ensure you have a clear understanding of the payment terms and negotiate a contract that protects your interests.
8. Can I visit the manufacturer’s facility in China before finalizing the order?
Visiting the manufacturer’s facility is highly recommended, as it allows you to assess their capabilities, production processes, and quality control measures firsthand. It also provides an opportunity to establish a personal relationship with the manufacturer, fostering better communication and understanding.
9. Are there any potential challenges in sourcing and manufacturing plastic moulds in China?
Some potential challenges include language barriers, cultural differences, potential communication gaps, and differences in business practices. However, with proper research, clear communication, and due diligence in choosing the right manufacturer, these challenges can be overcome effectively.
In conclusion, sourcing and manufacturing plastic moulds in China can offer cost advantages, access to advanced manufacturing technologies, and a large pool of skilled labor. However, thorough research, careful evaluation, and effective communication with manufacturers are essential to ensure a successful partnership.
Why contact sourcifychina.com get free quota from reliable plastic mould making suppliers?
Sourcifychina.com provides a platform that connects businesses with reliable plastic mould making suppliers in China. These suppliers offer free quotas to Sourcifychina.com for several reasons.
Firstly, plastic mould making suppliers understand the value of building trust and establishing long-term relationships with potential clients. By offering a free quota, suppliers demonstrate their commitment to providing a transparent and reliable service. This enables businesses to evaluate the supplier’s capabilities and quality before making a financial commitment.
Secondly, suppliers recognize that Sourcifychina.com plays a crucial role in connecting them with businesses worldwide. By providing free quotas, suppliers increase their exposure to a broader customer base, increasing the likelihood of securing future contracts and expanding their business.
Furthermore, offering a free quota also allows suppliers to showcase their expertise and the quality of their plastic moulds. This can be particularly beneficial for new suppliers or those wanting to penetrate new markets. By demonstrating their capabilities through a free quota, suppliers can gain the trust and confidence of potential clients, eventually leading to more business opportunities.
Moreover, offering a free quota aligns with Sourcifychina.com’s mission to provide businesses with a hassle-free sourcing experience. By eliminating the initial cost of obtaining a quota, Sourcifychina.com ensures that businesses can explore their options without financial constraints. This encourages businesses to engage with multiple suppliers and facilitates a competitive sourcing environment.
In summary, reliable plastic mould making suppliers offer free quotas to Sourcifychina.com to build trust, expand their customer base, showcase their expertise, and provide a hassle-free sourcing experience. This mutually beneficial arrangement allows businesses to make informed decisions and secure reliable suppliers for their plastic moulding needs.