Types and Applications of blending tank
Blending tanks are vessels that are designed for mixing different substances to produce a homogeneous mix. They can be made of either stainless steel or plastic materials depending on the substances being blended. There are several types of blending tanks, each with unique features and applications.
1. Vertical Blending Tanks: These tanks have a vertical orientation and are ideal for high shear mixing of viscous substances. The agitator inside the tank rotates at a high speed, creating turbulence that enhances the blending process.
2. Horizontal Blending Tanks: These tanks have a horizontal orientation and are designed for low shear mixing of powders and liquids. The substances are mixed using a dual-axis agitator that rotates at a slower speed, ensuring that the mix is gentle and thorough.
3. Cylindrical Blending Tanks: These tanks have a cylindrical shape and are used for blending liquids with similar viscosity. They are ideal for applications such as mixing ingredients in the food and beverage industry.
4. Conical Blending Tanks: These tanks have a cone-shaped bottom and are used for blending solids with liquids. The tapered design ensures that the powders are evenly distributed throughout the liquid, resulting in a homogeneous mix.
Blending tanks are used in a variety of industries, including food and beverage manufacturing, pharmaceutical production, and chemical processing. They are ideal for mixing ingredients, dissolving solids, and creating emulsions. Some common applications of blending tanks include:
1. Mixing powders and liquids to create a uniform mix.
2. Dissolving solids in liquids to create a solution.
3. Blending ingredients to create a homogeneous product, such as mayonnaise or salad dressing.
4. Creating emulsions by mixing liquids that don’t normally blend, such as oil and water.
In conclusion, blending tanks are a vital part of many manufacturing processes. They are available in different types and sizes to suit various applications, making them a versatile and essential piece of equipment in several industries.
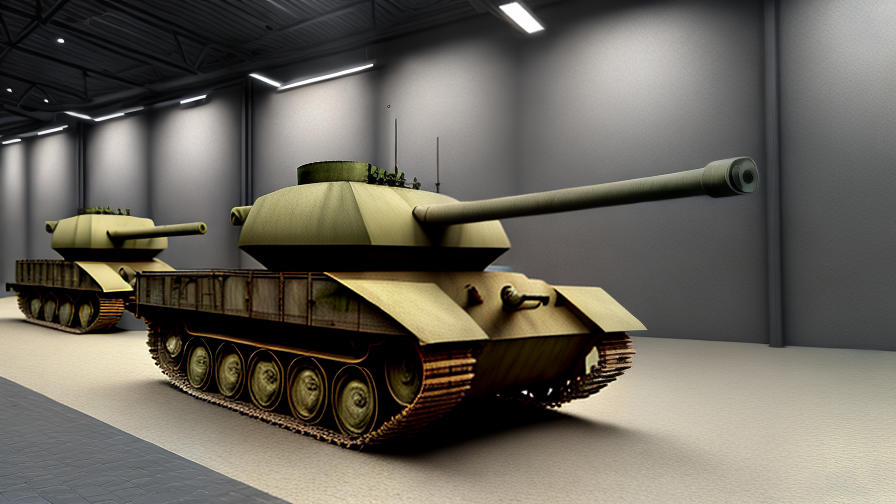
Benefits and Feature of Utilizing blending tank
Blending tanks are an important part of the industrial manufacturing process. They are used to mix materials together in a precise and controlled manner to create a finished product. Here are some of the benefits and features of utilizing blending tanks:
1. Consistency: Blending tanks ensure that the materials are mixed together evenly and consistently. This leads to a uniform product with no lumps or clumps.
2. Control: Blending tanks allow for precise control of the mixing process. The speed of the mixer, the amount of material added, and the mixing time can all be adjusted to achieve the desired result.
3. Reduced Waste: Blending tanks can reduce waste by ensuring that all materials are mixed together properly. This means that any leftover or unused materials can be easily reused in the next batch.
4. Increased Efficiency: Blending tanks can increase efficiency by allowing for continuous mixing. This means that the materials can be mixed together while other tasks are being performed, reducing downtime.
5. Safer Working Environment: Blending tanks are designed with safety in mind. They have features such as safety guards and emergency stop buttons to prevent accidents.
6. Cost Effective: Blending tanks are a cost-effective way to mix materials together. They require minimal maintenance and can be operated by a single person.
7. Versatility: Blending tanks can be used for a wide range of applications, including food and beverage production, pharmaceutical production, and chemical manufacturing.
Overall, blending tanks are an important tool for any manufacturing process that requires materials to be mixed together. They provide consistency, control, and efficiency while reducing waste and improving worker safety.
The Process of blending tank
The process of blending tank is a critical procedure in various industries such as food and beverage, chemical, pharmaceutical, and cosmetics. The blending tank is designed for mixing and blending various materials to create a uniform product. The tanks come in different sizes and shapes depending on the quantity of the materials to be blended.
The blending process starts with adding the raw materials into the tank. The materials could be powders, liquids, or semi-liquids. The tank is then closed to prevent any contamination from occurring during the blending process. The agitator or mixer blades located inside the blending tank are then activated to start the mixing process.
The speed and duration of the blending process are dependent on the type of material, viscosity, and desired consistency. The agitator ensures that there is even mixing of the materials to avoid the formation of lumps and ensure that the final product is uniform.
The blending tank may be heated or cooled depending on the requirement of the process. In some cases, the addition of heat or cooling agents may be required to achieve a specific reaction or to prevent the growth of microorganisms.
Once the blending process is complete, the tank is opened, and the product is removed. The product is then transferred into appropriate containers for further processing or packaging. The blending tank is then cleaned and sanitized to remove any remaining traces of the material and prevent any contamination.
In conclusion, the blending tank is a vital part of many industrial processes, and it ensures that the final product is of high quality and uniform. The process involves adding the raw materials, mixing, heating or cooling where necessary, and cleaning the tank after use.

How to use blending tank
A blending tank is a type of vessel used in various industries such as chemical, pharmaceutical, food and beverage, and cosmetics. It is primarily used to mix or blend different substances to create a homogenous mixture. Here are the steps to use a blending tank:
1. Preparation: Before using the blending tank, it is important to ensure that it is clean and free of any residue or impurities. The tank should be sanitized by using a cleaning solution.
2. Loading: Once the blending tank is cleaned, the ingredients to be blended are loaded into it. The amount of each ingredient should be measured accurately to ensure the desired level of consistency.
3. Mixing: After loading the ingredients, the tank is switched on, and the mixing process begins. Depending on the type of blending tank, the mixing can be done using a mechanical agitator or by passing the mixture through a series of pumps.
4. Monitoring: During the mixing process, the operator should keep an eye on the parameters such as the temperature, pressure, and the quality of the mixture. Any deviation from the desired conditions should be corrected immediately.
5. Unloading: Once the blending process is completed, the mixture is unloaded from the blending tank. The tank is cleaned thoroughly to avoid any contamination of the next batch.
In summary, the blending tank is a crucial component in the mixing process. Proper preparation, loading, mixing, monitoring, and unloading are key to ensure a consistent and high-quality mixture.
blending tank Manufacturer,Supplier and Wholesale
As a leading manufacturer, supplier, and wholesaler of blending tanks, we specialize in offering high-quality products that meet the diverse needs of our customers. Our blending tanks are designed with advanced technology that meets the highest industry standards. They are made with premium quality raw materials like stainless steel, which makes them corrosion-resistant and long-lasting.
We offer a wide range of blending tanks, including vertical blending tanks, horizontal blending tanks, and conical blending tanks. Our blending tanks can be customized as per the specific requirements of our customers. We can modify the design, size, and capacity of the blending tanks to meet your unique needs. Our products are widely used in industries such as pharmaceuticals, cosmetics, food & beverage, and chemical.
We have a team of skilled professionals who are dedicated to providing excellent customer service. Our experts understand the technical aspects of blending tanks and can offer you valuable advice on selecting the right blending tank for your application. We also provide installation and maintenance services for our products, ensuring that our customers get the best value for their money.
At our manufacturing unit, we use cutting-edge technology and state-of-the-art machinery to ensure the highest quality standards are met. We have a stringent quality control system that is enforced to ensure that our products are free from any defects or errors. We also conduct regular quality audits to ensure that all our products meet the highest standards.
In conclusion, if you are in the market for high-quality blending tanks, look no further than our company. We can provide you with the best solutions tailored to your specific needs. Our products are priced competitively, and we offer prompt delivery and after-sales services. Contact us today to discuss your blending tank needs.

blending tank Price
Blending tanks are essential equipment in various industries such as food and beverage, pharmaceuticals, and chemicals. The price of blending tanks can vary greatly depending on several factors such as the size, material used, and features.
The most common materials for blending tanks are stainless steel and polyethylene. Stainless steel blending tanks are highly durable and resistant to corrosion, making them ideal for most industries. Polyethylene blending tanks, on the other hand, are more affordable and lightweight, making them suitable for smaller operations.
The size of blending tanks can also impact the price. Smaller tanks designed for laboratory or pilot-scale applications typically range from $1,000 to $5,000. Larger tanks used for production and processing can range from $5,000 to over $100,000.
The features of blending tanks such as agitation systems, mixing speed controls, and temperature sensors can also affect the price. Blending tanks with more advanced features will generally cost more.
Other factors that can affect blending tank prices include customization, installation, and shipping costs.
When selecting a blending tank, it is essential to consider your specific industry needs carefully. Work with a reputable supplier that can tailor a solution that fits your requirements while keeping costs reasonable.
Overall, blending tank prices vary widely, and it is best to work with an experienced supplier to ensure you get the most value for your investment. Choose a trusted provider that offers quality products and reliable after-sales support to ensure smooth operations and optimized performance.
FAQ sourcing blending tank manufacturer from China with multiple answers
What is a blending tank?
A blending tank is a type of industrial tank that is used to mix two or more materials or substances to form a homogeneous mixture.
How to source a blending tank manufacturer from China?
There are several ways to source a blending tank manufacturer from China. One way is to search for them on B2B websites such as Alibaba, Made-in-China, or Global Sources. You can also attend trade shows such as Canton Fair, which is held in Guangzhou, China twice a year, and connect with manufacturers in person. Another way is to hire a sourcing agent or a procurement company that specializes in finding and vetting suppliers from China.
What should I consider when choosing a blending tank manufacturer from China?
When choosing a blending tank manufacturer from China, you should consider factors such as their experience, expertise, quality control processes, pricing, lead times, after-sales support, and communication skills. It is important to conduct due diligence and verify their credentials, certifications, and references before committing to a partnership.
What materials are blending tanks made of?
Blending tanks can be made of a variety of materials such as stainless steel, carbon steel, aluminum, and plastic. The choice of material depends on the type of substance being mixed, the level of cleanliness required, and other factors such as temperature and pressure.
Can I customize my blending tank?
Yes, most blending tank manufacturers in China offer customization services. You can specify the size, shape, material, agitator type, motor size, and other parameters according to your specific requirements.
How much does a blending tank from China cost?
The cost of a blending tank from China depends on several factors such as the material, size, customization level, and quantity. Generally, the price range for a 1000-liter blending tank can be between $1000-$5000.
How long does it take to manufacture a blending tank?
The lead time for manufacturing a blending tank in China can vary depending on several factors such as the size, complexity, customization level, and the manufacturer’s capacity. Typically, it can take between 4-12 weeks to manufacture a blending tank.