Analysis of Manufacturing Expenses for building materials cost
Manufacturing expenses for building materials can be broken down into various categories, including raw material cost, labor cost, overheads, and transportation cost. Understanding the factors that affect these expenses can help manufacturers make informed decisions to optimize their production processes and reduce costs.
Raw Material Cost:
The raw material cost is an essential component of manufacturing expenses for building materials. The cost of raw materials such as cement, steel, wood, and glass can fluctuate based on various factors such as changes in demand, supply, and international commodity prices.
Labor Cost:
Labor cost for building materials includes wages, salaries, benefits, and incentives paid to employees working on the production line. The labor cost can be influenced by the availability of labor, labor laws, and regulations, and the level of specialization required for the job.
Overhead Costs:
Overhead costs, such as utilities, rent, taxes, and insurance, are necessary expenses that manufacturers must factor into their overall production costs. These costs can be reduced by improving operational efficiency and technology adoption.
Transportation Cost:
Transportation cost for building materials includes shipping, fuel, and vehicle maintenance expenses involved in moving products to customers. The cost can be affected by the distance of the customer’s location, fuel prices, and any regulatory requirements.
In conclusion, manufacturers need to closely monitor their manufacturing expenses to remain profitable. By utilizing cost-saving measures like improved operational efficiency, adopting new technologies, and optimizing logistics, companies can maintain a competitive advantage while keeping the cost of building materials reasonable.
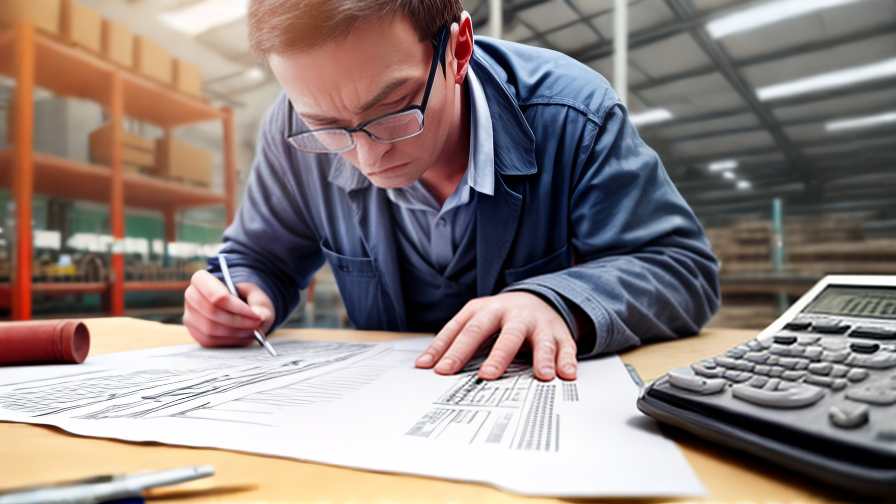
Understanding the Components that Contribute to the Price of building materials cost
The price of building materials is determined by various components that influence the supply and demand in the construction industry. There are several factors that contribute to the cost of building materials, and understanding these components is essential for builders, contractors, and project managers.
1. Raw Material Costs – The cost of building materials varies based on the cost of production of the raw materials used to make them. The rising cost of raw materials, such as lumber, metals, and concrete, has a significant impact on the overall cost of building materials.
2. Transportation Costs – Transportation expenses are incurred by manufacturers, wholesalers, and retailers to transport the building materials to different locations. Rising fuel prices and transportation charges lead to higher costs for building materials.
3. Labor Costs – The cost of labor charged by manufacturers, wholesalers, and retailers also affects the price of building materials. Labor costs can rise due to increasing wages and salaries and training costs.
4. Energy Costs – Energy costs are an essential component of the production process for building materials. The energy used for manufacturing, processing, and transportation of building materials impacts the final price of the product.
5. Market Demand – The demand for building materials fluctuates based on the needs of the construction industry for various projects. Changes in market demand affect the price of building materials significantly.
6. Taxes and Duties – Import and export taxes and duties imposed by governments can increase the price of building materials.
In summary, understanding these components that contribute to the price of building materials can help builders, contractors, and project managers make informed decisions and plan their projects better. These factors not only impact the cost of building materials but also the overall cost of construction projects, which can have significant implications on the final cost of projects.
Comparing the Wholesale and Retail Prices of building materials cost in China
China is a global leader in the production and export of building materials. The country is known for its robust manufacturing sector and cost-effective production processes. Wholesale and retail prices of building materials in China are significantly lower than those in other parts of the world, making it an attractive destination for construction firms and contractors.
Wholesale prices of building materials in China are significantly lower than in other parts of the world. This is because of the massive scale of production and the availability of raw materials. Building material manufacturers in China benefit from economies of scale, which enables them to produce goods at a lower cost and sell them at a lower price. For example, the wholesale price of cement in China is approximately $50 per tonne, significantly lower than the global average of $100 per tonne.
Retail prices of building materials in China are higher than wholesale prices, but still competitive compared to other countries. The retail price of building materials in China is affected by a range of factors, including production cost, transportation cost, and supply and demand. Factors like government policies, environmental regulations, and tax policies also impact the retail price of building materials in China. The retail price of cement in China, for example, ranges from $80 to $100 per tonne, depending on the location and market demand.
In conclusion, China’s construction industry benefits greatly from low wholesale prices of building materials. The country’s robust manufacturing sector, efficient production processes, and availability of raw materials make it more cost-effective to produce building materials in China than other parts of the world. While retail prices of building materials in China are slightly higher, they remain competitive compared to other countries, making China an attractive destination for construction firms and contractors.

Understanding Shipping and Logistics for building materials cost from China
When importing building materials from China, it is essential to consider the costs of shipping and logistics. These costs can vary depending on several factors such as the type of materials, the quantity, and the delivery destination.
Generally, there are two primary methods of transportation: sea and air. Sea freight is the most common mode of transportation due to its affordability, while air freight is faster but more expensive. The cost of shipping can be influenced by the volume of the cargo and shipping service provider’s rates.
Logistics costs depend on the activities involved in getting the goods from the manufacturer to the final destination. This may involve transportation from the factory to the port or warehouse, customs clearance, storage, and onward transportation. These costs can be influenced by the level of complexity involved in the process and the availability of infrastructure.
To help manage costs, it is advisable to work with experienced suppliers who can provide reliable shipping and logistics services. Additionally, working with freight forwarders can help to simplify the process and ensure that you are getting a fair deal for shipping and logistics costs. It is also crucial to factor in any potential taxes, duties, and tariffs that may be imposed when sourcing building materials from overseas.
Overall, understanding the shipping and logistics costs involved in importing building materials from China is essential for budgeting and ensuring a smooth and efficient process.
Potential Tariffs or Import Taxes on building materials cost Purchased from China
The United States could impose tariffs or import taxes on building materials purchased from China, which could increase the cost of construction for builders and ultimately the cost of homes for consumers. Building materials that could be affected by such tariffs or taxes include steel, aluminum, lumber, and cement.
Trade tensions between the U.S. and China have escalated in recent years, with both countries imposing tariffs on each other’s goods. The Trump administration in particular has targeted Chinese imports with tariffs in an effort to address perceived trade imbalances.
If tariffs or taxes were imposed on building materials, Chinese manufacturers could respond by raising their prices to offset the added cost of doing business. U.S. companies could also seek alternative suppliers or shift their production to other countries, which could affect the supply chain and lead to price increases.
On the other hand, tariffs or taxes could incentivize U.S. manufacturers to increase production of building materials domestically, which could create jobs and stimulate the economy. However, this would depend on the availability of domestic resources and the competitiveness of domestic manufacturers.
In conclusion, the imposition of tariffs or import taxes on building materials purchased from China could have various impacts on the construction industry, from price increases to shifts in the supply chain and domestic manufacturing.

Impact of Market Demand and Competitive Environment on building materials cost
The market demand and competitive environment can have a significant impact on the cost of building materials. When the demand for building materials is high, the cost is likely to increase due to limited supply. This is because manufacturers may struggle to keep up with the demand leading to a price hike. On the other hand, when demand is low, the cost could decrease due to surplus stock and overproduction. For instance, in the wake of the COVID-19 pandemic, the demand for building materials has significantly increased due to the growth in the construction sector as people invest in homes, leading to an increase in the price of the materials.
The competitive environment can also impact the cost of building materials. When there is intense competition in the market, manufacturers may reduce the price of their building materials to remain competitive, even with lower profit margins. This means that buyers can purchase quality materials at lower prices. Additionally, competition may also lead to innovation and better-quality building materials with improved features and increased durability, contributing to the overall cost.
However, competition could lead to a situation where some manufacturers try to reduce the cost of production, resulting in poor-quality materials. Some suppliers may compromise on quality in a bid to cut costs, which can raise safety concerns and increase repair and maintenance costs for builders.
In conclusion, demand and the competitive business environment have a significant influence on the cost of building materials. Therefore, it is necessary to track market trends and forecasts to ensure that when making investment decisions on building materials, you are well-informed and can respond to market changes effectively.
FAQ about building materials cost with multiple answers
Q: Why have building materials costs increased in recent years?
A: There are several reasons for the increase in building materials costs, including higher demand due to a booming construction industry, increased transportation costs, tariffs on imported materials, and disruptions in supply chains due to the COVID-19 pandemic.
Q: Which building materials have seen the largest cost increases?
A: Lumber is perhaps the material that has seen the largest cost increases, with prices reaching record highs in 2021. Other materials that have seen cost increases include steel, copper, and PVC piping.
Q: How do construction companies manage these increased costs?
A: Construction companies may manage increased costs by increasing the prices of their projects to reflect the higher cost of materials, seeking out alternative materials, or negotiating with suppliers for better pricing.
Q: Will building materials costs continue to rise?
A: It is difficult to predict the trajectory of building materials costs, but some analysts predict that the cost increases will continue as demand remains high and supply chain disruptions persist.
Q: How can homeowners save money on building materials?
A: Homeowners may be able to save money on building materials by shopping around for the best prices, considering alternative materials, and carefully planning their projects to minimize waste.
Q: Are eco-friendly building materials more expensive?
A: Eco-friendly building materials may be more expensive initially, but they can provide long-term cost savings by reducing energy and water costs, improving indoor air quality, and reducing the need for maintenance and repairs.
Q: How can builders and homeowners reduce the environmental impact of building materials?
A: Builders and homeowners can reduce the environmental impact of building materials by selecting materials that have been responsibly sourced and manufactured, minimizing waste during construction, and properly disposing of materials after the project is complete.