Types and Applications of ceramic pcb
Ceramic PCBs, also known as ceramic printed circuit boards, are a type of circuit board that uses a ceramic substrate instead of the traditional fiberglass or plastic substrate. The ceramic material used in these PCBs offer several advantages such as better thermal conductivity, higher mechanical strength, and higher resistance to harsh environments.
There are different types of ceramic PCBs such as alumina PCBs, aluminum nitride PCBs, and others. Alumina PCBs are the most common type and are made from aluminum oxide ceramic material. These PCBs are widely used in applications that require high thermal conductivity and high power dissipation such as LED lighting, power converters, and high-frequency power amplifiers.
Aluminum nitride PCBs, on the other hand, are made from aluminum nitride ceramic material. These PCBs offer even higher thermal conductivity than alumina PCBs and are used in high-heat applications such as power electronics, microwave communication, and semiconductor packaging. Aluminum nitride PCBs are also used in the production of high-frequency electronic components due to their excellent dielectric properties.
Ceramic PCBs are used in various applications due to their superior properties such as thermal conductivity, high mechanical strength, and excellent electrical properties. They are used in applications that require high power density, high-temperature resistance, and high-frequency signal transmission.
Some of the common applications of ceramic PCBs are:
1. LED lighting: Ceramic PCBs are used as substrates for high-power LED lighting due to their excellent thermal conductivity and heat dissipation properties.
2. Power electronics: Ceramic PCBs are used in power electronic applications such as power converters, inverters, and motor drives due to their high thermal conductivity, mechanical strength, and high-temperature resistance.
3. Microwave communication: Ceramic PCBs are used in microwave communication applications such as radar systems, satellite communication, and wireless networks due to their high frequency and dielectric properties.
4. Semi-conductor packaging: Ceramic PCBs are used in the packaging of semiconductors due to their high thermal conductivity and excellent dielectric properties.
In conclusion, ceramic PCBs offer numerous advantages over traditional PCBs and are widely used in various applications that demand high performance, reliability, and durability. The type of ceramic PCB used in a particular application depends on the specific requirements of that application.
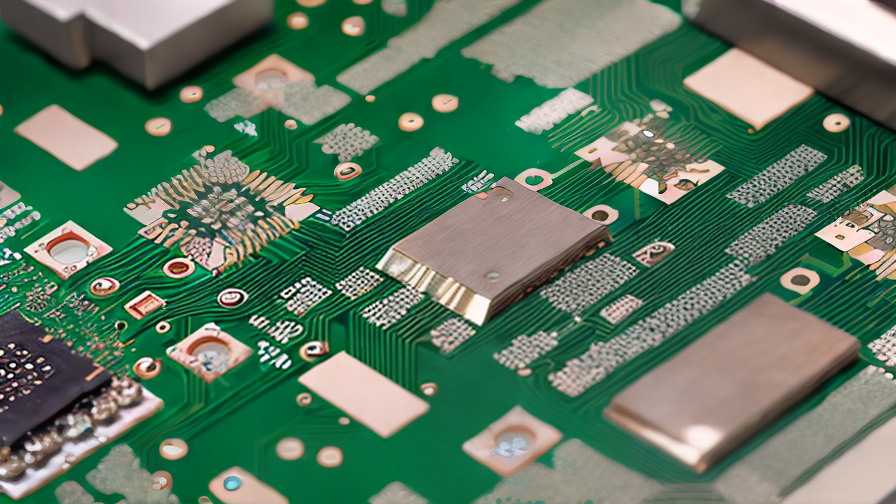
Benefits and Feature of Utilizing ceramic pcb
Ceramic printed circuit boards, or ceramic PCBs, are increasingly becoming popular in various industries due to their unique properties and benefits. These boards are typically made of ceramic materials such as alumina, zirconia, or aluminum nitride and have many advantages compared to traditional FR4 PCBs.
One of the most significant benefits of ceramic PCBs is their high thermal conductivity. The ceramic substrate material used in these PCBs can effectively dissipate heat from electronic components and devices, improving their performance and lifespan. Ceramic PCBs can also withstand high temperatures, making them suitable for use in extreme environments.
Another advantage of ceramic PCBs is their excellent electrical insulation properties. Ceramic material has a high resistance to electricity, allowing for the design of complex circuitry that can operate at high frequencies without interference. This feature is especially useful in applications that require high-frequency switching, such as power supplies, inverters, and motor controllers.
Ceramic PCBs are also known for their exceptional mechanical strength, durability, and resistance to corrosion, making them suitable for harsh environments where traditional PCBs may fail. Due to their high hardness and wear resistance, ceramic PCBs are also ideal for applications that are prone to wear, such as chemical processing, aerospace, and automotive industries.
Furthermore, ceramic PCBs are also environmentally friendly, as they do not contain hazardous substances like lead or other heavy metals.
In summary, ceramic PCBs offer many benefits that traditional FR4 PCBs cannot provide, including high thermal conductivity, excellent electrical insulation, mechanical strength, durability, and resistance to corrosion. Their unique properties make them ideal for use in various industries, including telecommunications, aerospace, automotive, and high-power applications.
The Process of ceramic pcb
Ceramic PCBs (Printed Circuit Boards) are becoming more common in electronic circuits due to their high thermal conductivity, excellent mechanical properties, and chemical stability. The process of manufacturing Ceramic PCBs involves several steps, as described below:
1. Material Selection: The first step in making ceramic PCBs is selecting the right ceramic material, such as aluminum oxide, aluminum nitride, or silicon carbide, depending on the specific requirements of the application.
2. Cutting: The ceramic material is then cut into the required size and shape using a laser cutter or CNC machine.
3. Drilling: Small holes are drilled in the ceramic substrate using a special diamond-coated drill bit. These holes will later be used to place components and wires.
4. Metallization: A thin layer of metal, usually copper, is deposited onto the ceramic surface using screen printing, sputtering, or electroplating. This layer is used to create conductive traces on the surface of the substrate.
5. Etching: The excess copper layer is removed using an etchant, leaving behind only the desired traces that will connect the components.
6. Layer Stacking: Multiple layers of ceramic substrate can be stacked together to create a multilayer ceramic PCB. The layers are bonded together using high-temperature adhesives.
7. Component Placement: Components, such as resistors, capacitors, and processors, are placed onto the ceramic substrate using surface-mount technology (SMT) or through-hole technology (THT).
8. Reflow Soldering: The components are then soldered onto the PCB using a reflow oven, where the solder is heated to a precise temperature to melt and bond the components to the board.
9. Quality Control: The PCB is then inspected for any defects and tested for functionality before being packaged and shipped.
Overall, the process of making a ceramic PCB involves careful selection of materials, precise cutting and drilling, metallization and etching of traces, layer stacking, component placement, reflow soldering and quality control to ensure a reliable, high-quality, and durable PCB.

How to use ceramic pcb
Ceramic PCB, also known as ceramic printed circuit board, is a type of printed circuit board made up of a ceramic layer that acts as the substrate material. They are designed to provide higher thermal conductivity and better electrical insulation compared to other types of PCBs such as FR4 or fiberglass PCBs. This makes ceramic PCBs ideal for applications that require high power, high-frequency, and high-temperature operations.
Ceramic PCBs can be used in a wide range of applications such as in power electronics, high-frequency circuits, LED lighting systems, and automotive electronics. To use a ceramic PCB, an individual needs to follow some basic steps such as:
1. Identify the application: Ceramic PCBs are ideal for applications that require high power and high-temperature operations. Identify such applications, and ensure that the ceramic PCB is the best fit for the job.
2. Design: Ceramic PCBs are designed using computer-aided design (CAD) software. The design process involves creating a layout, determining the number of layers required, and specifying the dimensions of the board.
3. Manufacturing: After designing, the ceramic PCB is manufactured using advanced manufacturing techniques such as laser drilling, plating, and lamination.
4. Assembly: After manufacturing, the ceramic PCB is assembled with components such as resistors, capacitors, and integrated circuits using surface mount technology (SMT).
5. Testing: After the assembly process, the ceramic PCB is tested to ensure that it meets all the required specifications such as power rating, signal integrity, and thermal management.
In conclusion, ceramic PCBs have a wide range of applications and offer many benefits such as high thermal conductivity and greater electrical insulation. Hence, they are preferred over other types of PCBs but need to be used systematically and as per the instructions.
ceramic pcb Manufacturer,Supplier and Wholesale
As a ceramic PCB manufacturer, supplier, and wholesale provider, we specialize in providing innovative and high-quality ceramic PCB solutions to meet the growing demand in the electronics industry. Our ceramic PCBs utilize high-grade ceramic materials that offer several benefits over traditional PCB materials such as improved thermal stability, robust mechanical properties, and superior electrical insulation.
Our state-of-the-art manufacturing facility is equipped with advanced machinery and skilled personnel that enable us to produce high-quality ceramic PCBs in large quantities while maintaining high standards of quality control. We use the latest manufacturing techniques to ensure that our ceramic PCBs meet or exceed all necessary industry standards.
As a reliable supplier and wholesale provider, we offer a comprehensive range of ceramic PCB solutions that cater to the diverse needs of our clients. We have a team of experienced professionals who work closely with our clients to understand their specific requirements and provide customized solutions that meet their needs.
Our ceramic PCBs find extensive use in a wide range of applications such as LED lighting, power electronics, automotive electronics, telecommunications, and many more. We believe in providing cost-effective solutions that offer excellent value for money and help our clients improve their bottom line.
In conclusion, we are a leading ceramic PCB manufacturer, supplier, and wholesale provider committed to providing innovative, high-quality, and cost-effective solutions to meet the growing demands of the electronics industry. We strive to exceed our clients’ expectations and build long-lasting relationships by providing excellent customer service, timely delivery, and customized solutions that meet their specific requirements.

ceramic pcb Price
Ceramic PCBs or printed circuit boards are highly durable and reliable due to their inherent material properties. They are used in a variety of applications such as telecommunications, aerospace, automotive, military, and medical equipment, where performance and reliability are paramount.
The price of ceramic PCBs varies depending on various factors such as board size, substrate material, copper thickness, surface finish, and quantity of order. In general, the cost of ceramic PCBs is significantly higher than traditional FR4 PCBs due to their unique manufacturing process and material cost. However, their performance and reliability justify their higher price.
The average price of a small-sized (1×1 inch) ceramic PCB can range from $10 to $50 per piece, whereas larger-sized (up to 12×18 inches) ceramic PCBs can cost anywhere from $50 to $500 per piece. The type of ceramic material used for the substrate, such as aluminum oxide, aluminum nitride, silicon carbide, or beryllium oxide, also affects the cost. Generally, aluminum oxide is the most commonly used and least expensive ceramic material, whereas beryllium oxide is the most expensive but has the best thermal conductivity.
The copper thickness and surface finish of the ceramic PCB also impact the overall cost. Higher copper thickness and complex surface finish such as gold plating or immersion silver can significantly increase the price. The quantity of order also plays a key role in determining the unit cost. Higher quantities typically lead to lower unit costs due to economies of scale in production.
In conclusion, ceramic PCBs come at a higher cost due to their unique material properties, advanced manufacturing process, and customization. However, their performance, reliability, and durability justify their higher price and make them an ideal choice for critical and high-performance applications.
FAQ sourcing ceramic pcb manufacturer from China with multiple answers
1. What industries typically use ceramic PCBs, and what are the benefits of using them?
Ceramic PCBs are commonly used in industries such as aerospace, defense, medical, and automotive. They offer many benefits, including high thermal conductivity, excellent electrical performance, high dimensional stability, and good mechanical strength.
2. Why should I consider sourcing ceramic PCBs from a China-based manufacturer?
China has become a leading manufacturer of printed circuit boards, including ceramic PCBs. Many Chinese companies offer competitive pricing, high-quality products, and efficient delivery options.
3. What should I look for in a quality ceramic PCB manufacturer in China?
Look for a company with a strong reputation for quality, with certifications such as ISO 9001, ISO 14001, and UL. Check their production capabilities, including technology and equipment, and ensure they have experience in producing ceramic PCBs for your industry.
4. How can I ensure that my ceramic PCBs meet my specifications?
Communicate clearly with your manufacturer and provide your specifications in detail. Request samples and prototypes to test and approve before committing to large-scale production.
5. What is the typical lead time for ceramic PCBs from a manufacturer in China?
Lead times vary depending on the complexity of the design and the size of the order. Some Chinese manufacturers offer fast-turnaround options, while others may require longer lead times. It’s important to discuss lead time expectations with your manufacturer and plan accordingly.
6. What are some potential challenges of sourcing ceramic PCBs from China?
Language and cultural barriers can present communication challenges. Quality control can also be a concern, but working with a reputable manufacturer and conducting thorough inspections can mitigate these issues. Shipping and logistics can also add to the cost and lead time.