Types and Applications of ceramic plunger
Ceramic plungers have become a popular choice for demanding applications that require high levels of wear-resistance. They are typically used in pump and valve applications where precise fluid control is necessary. Ceramic plungers offer several advantages over traditional metallic materials such as high strength, durability, and chemical resistance. Here are some types and applications of ceramic plungers:
1. Alumina Ceramic Plunger: This is the most commonly used ceramic plunger due to its high mechanical strength, excellent resistance to wear and corrosion, and high thermal stability. Alumina ceramic plungers are used in high-pressure plunger pumps for water treatment, in chemical processing plants, and in industrial power generation.
2. Zirconia Ceramic Plunger: Zirconia ceramic plungers are known for their exceptional fracture toughness, high wear-resistance, and exceptional dynamic strength. Zirconia ceramic plungers are used in chemical transfer pumps, oil and gas operations, and medical devices.
3. Silicon Nitride Ceramic Plunger: Silicon nitride ceramic plungers offer excellent thermal shock resistance, high mechanical strength, and low thermal expansion. They are used in high-pressure diesel fuel injection systems, water-jet cutting machines, and fluid transfer pumps.
4. Applications: Ceramic plungers are used in various applications such as in chemical industry, water treatment, oil and gas, healthcare, and food processing. They are used in pumps and valves for high-pressure applications such as in oil drilling, chemical processing, and water treatment. These pumps are used to deliver highly pressurized liquids, gases, or solids which require high levels of wear-resistance. They are also used in hydraulic systems to control the flow of fluids in industrial equipment. In medical applications, ceramic plungers are used in surgical tools and dental equipment, where precision and hygiene are critical.
In conclusion, ceramic plungers offer several advantages over traditional metallic materials, making them an excellent choice for demanding applications that require high levels of wear-resistance. With different types of ceramic plungers available, they offer a wide range of options for diverse applications in various industries such as healthcare, oil and gas, chemical industry, and water treatment, among others.
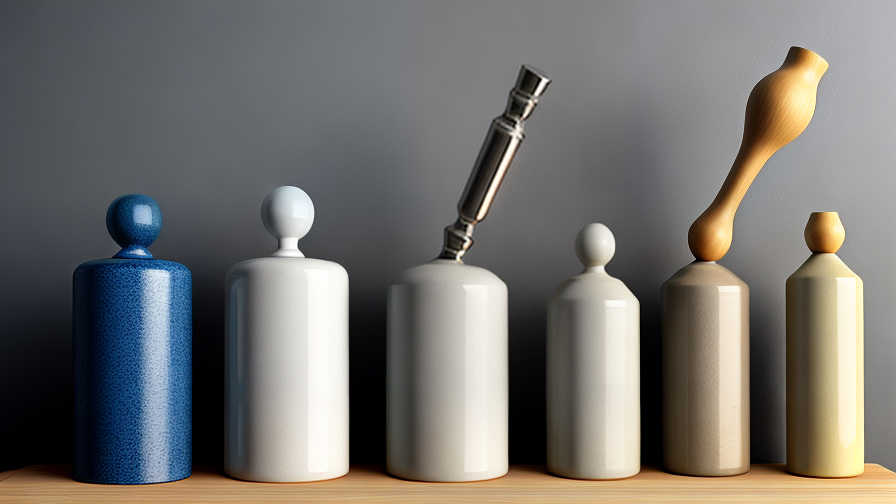
Benefits and Feature of Utilizing ceramic plunger
Ceramic plunger is a crucial component of industrial machines such as pumps and compressors. They are manufactured using advanced ceramic materials that exhibit high strength, hardness and resistance to wear and corrosion. Ceramic plungers are known for their impressive performance and durability properties, they are used widely in various industries, including chemical processing, oil and gas, food and beverage, pharmaceuticals, and many more.
Below are some of the benefits and features of utilizing ceramic plunger:
1. Wear Resistance: Ceramic plungers are highly wear-resistant, thanks to their hardness properties. They are capable of handling abrasive materials without getting damaged, which is critical in industrial applications.
2. Corrosion resistance: Ceramic plungers can withstand various chemicals, including acids, bases and solvents without getting corroded. As a result, they are used extensively in chemical processing plants and other industries that require such resistance.
3. High Strength: Ceramic plungers have high strength properties that make them ideal for handling high pressure and heavy loads. These properties prevent the plungers from cracking or breaking under pressure, which promotes their longevity and reliability.
4. Low Friction: Ceramic materials used for the manufacturing of plungers offer low friction characteristics, which result in less wear, less noise and fewer vibrations.
5. Long Life: Ceramic plungers are known to have a long lifespan due to their resistance to wear and corrosion, as well as their ability to handle extreme conditions.
6. Versatility: Ceramic plungers can be designed to meet different industrial needs. They can be produced in unique shapes and sizes to fit specific applications, and can be modified with coatings or other finishes to improve their properties.
7. Energy Efficiency: The low weight and high strength properties of ceramic plungers can lead to energy efficiency in systems, leading to lower power consumption and cost savings.
In conclusion, the utilization of ceramic plungers offers significant benefits and features that make them an indispensable component in various industries. They are reliable, durable, and resistant to wear, corrosion, and extreme conditions, which promotes their longevity and cost-effectiveness over time.
The Process of ceramic plunger
Ceramic plungers are essential components in various commercial systems such as hydraulic pumps, pressure washers, and high pressure water pumps. The main characteristic of ceramic plungers is their high strength, wear resistance, and thermal stability. The ceramic plunger is a vital part of the system and is used for moving fluids.
The production of ceramic plungers involves several processes. Firstly, the ceramic material is selected and prepared for use. The ceramic selected is generally of high-grade, such as aluminum oxide or zirconia. The ceramic material is then milled and mixed with a binder to form a slurry. The slurry is then molded into the desired shape by using a hydraulic press. The plunger is then fired at high temperatures to remove the binder and harden the ceramic. This process also helps the plunger acquire the required strength.
The firing process of the plunger involves heating the ceramic to a high temperature suitable for densification. The temperature is usually between 1400°C to 1800°C, depending on the ceramic material and the application. After the firing process, the ceramic plunger undergoes a machined process for the final finishing of the plunger’s surface.
The next step of the ceramic plunger is to inspect the finished surface and any defects created. Any defect discovered is corrected during this phase of polishing and surface finishing. Once the surface quality has been achieved, the ceramic plunger is now ready to be assembled and installed into the system.
In summary, the process of manufacturing a ceramic plunger entails material selection, milling, molding, firing, machining, polishing and surface finishing, and inspection of the final product. The manufacture of ceramic plungers is an intricate process, which requires precision and expertise to create a highly durable, wear-resistant, and reliable product. It is the attention to detail in each step of the manufacturing process that ultimately attributes to the superior quality of ceramic plungers.

How to use ceramic plunger
A ceramic plunger is a versatile tool used for a variety of applications, including liquid pumping and pressure control. The plunger is made from high-quality ceramic material and is designed to withstand high levels of wear and tear, making it particularly useful for heavy-duty applications. Here are some tips on how to use a ceramic plunger:
1. Clean the Plunger: Before use, always ensure that the ceramic plunger is free from any dirt, debris, or residue. The plunger can be cleaned using a mild detergent and clean water.
2. Lubricate the Plunger: To ensure smooth operation, apply lubricant to the surface of the ceramic plunger. This ensures that the plunger moves freely and does not get stuck during the pumping or pressure control function.
3. Install the Plunger: The ceramic plunger should be installed according to the manufacturer’s instructions, depending on the specific application. Ensure that the plunger is tightly fitted and secure.
4. Maintain the Plunger: To keep the ceramic plunger in top condition, regular maintenance is necessary. This includes regular cleaning and periodic lubrication.
5. Adjust the Pressure: The ceramic plunger can be used for pressure control by adjusting the pressure valve. This feature is particularly useful in maintaining consistent pressure in a system.
6. Replace the Plunger: Over time, the ceramic plunger may experience wear and tear, leading to decreased performance or even failure. To ensure optimal functioning, the plunger should be replaced periodically or as recommended by the manufacturer.
In summary, using a ceramic plunger involves cleaning, lubricating, installing, maintaining, adjusting, and periodically replacing the plunger for optimal performance. Proper use and care of the ceramic plunger ensure longevity and efficient functioning of the device.
ceramic plunger Manufacturer,Supplier and Wholesale
As a leading ceramic plunger manufacturer, supplier, and wholesaler, we offer the highest quality products and services to our clients. Our ceramic plungers are made using the latest technology and the best quality materials, ensuring exceptional performance and durability.
We specialize in providing ceramic components for a wide range of industrial applications, including fluid power pumps, hydraulic pumps, and high-pressure cleaners. Our ceramic plungers are designed to withstand extreme temperatures, pressure, and industrial chemicals, making them a reliable and cost-effective solution for our customers.
Our manufacturing process involves using advanced ceramic materials, such as zirconia and alumina, which are known for their high strength, hardness, and corrosion resistance. The ceramic material is shaped into a plunger using precision CNC machines and is then subjected to rigorous testing and inspection to ensure consistent quality.
As a wholesale ceramic plunger supplier, we offer competitive prices and fast and reliable delivery to meet the growing demands of our customers. We also provide customized solutions to cater to specific customer requirements, such as plunger design, material, and sizes.
In addition to manufacturing ceramic plungers, we also offer repair and refurbishment services for worn-out plungers. Our team of experts can repair or replace the damaged components, ensuring the plunger is restored to its original functionality and performance.
Overall, our commitment to quality, innovation, and customer satisfaction has made us a trusted name in the industry. We strive to exceed our customers’ expectations and continue to deliver exceptional ceramic plunger products and services.

ceramic plunger Price
Ceramic plungers are important components in many industrial applications, particularly in high-pressure fluid pumping and spraying systems. They are known for their high wear resistance, durability, and ability to provide a smooth and consistent flow of fluids. In order to determine the price of a ceramic plunger, several factors should be considered, including the type and size of the plunger, the material used, and the intended application.
Firstly, the type and size of the ceramic plunger will have a significant impact on its price. There are many different types of ceramic plungers available on the market, each with different designs and specifications. Some common types include axial flow plungers, radial flow plungers, and triplex plungers. Additionally, the size of the plunger will determine the amount of material required to manufacture it, which will affect the overall cost.
Another important factor to consider is the material used to manufacture the ceramic plunger. While ceramic is the primary material used for the plunger, different types of ceramic can be used, such as zirconia, alumina, and silicon nitride. Each of these materials has different properties that can affect the performance and durability of the plunger, and therefore the cost.
Finally, the intended application of the ceramic plunger will also impact its price. For example, ceramic plungers used in high-pressure water jetting systems will typically cost more than those used in lower pressure applications. Similarly, ceramic plungers used in aggressive, corrosive environments may require special coatings or materials that will increase the cost.
In general, ceramic plungers can range in price from a few dollars to several hundred dollars, depending on the factors mentioned above. It’s important to understand the specific requirements of your application and choose a ceramic plunger that is designed to meet those needs while also fitting within your budget.
FAQ sourcing ceramic plunger manufacturer from China with multiple answers
1) What is a ceramic plunger?
A ceramic plunger is a device that is used in high-pressure environments to pump fluids or gases. It is made up of a ceramic piston rod and a matching ceramic cylinder, both of which are highly durable and can withstand even the most corrosive chemical reactions.
2) Why source ceramic plungers from China?
China is a well-established manufacturer of industrial ceramics. It has a long history of producing high-quality products at a competitive price point. Furthermore, many ceramic plunger manufacturers in China offer a variety of customizable options when it comes to material type, size, and shape.
3) What should I look for when choosing a ceramic plunger manufacturer in China?
When sourcing a ceramic plunger manufacturer in China, be sure to look for a company with a proven track record and extensive experience producing high-quality ceramics. It is also important to verify that the manufacturer is compliant with all relevant safety and environmental regulations.
4) How can I ensure the quality of ceramic plungers from China?
Before committing to a manufacturer, request product samples and research the company’s reputation within the industry. Additionally, look for a manufacturer with comprehensive quality control standards in place to ensure that each ceramic plunger meets your specific needs and requirements.
5) What is the typical lead time for ceramic plungers from a China-based manufacturer?
Lead times vary depending on the specific manufacturer and the quantity of ceramic plungers ordered. Generally, lead times range from 6-12 weeks depending on the complexity of the product and the manufacturer’s production capacity. Be sure to verify the lead time with the manufacturer before placing your order.
Overall, sourcing a ceramic plunger manufacturer from China can be a great option for companies looking for a high-quality product at an affordable price. By doing your research, verifying the manufacturer’s quality control standards, and making a clear order agreement, you can ensure a successful partnership with a China-based manufacturer.