Introduce about cnc clamping guide,Qulity,Cost,Supplier,Certification,Market,Tips,FAQ
CNC clamping guide is an essential tool used in the machining industry to securely hold workpieces in place during the CNC machining process. It ensures precise and accurate machining by minimizing vibrations and movement of the workpiece.
Quality is a crucial factor when selecting a CNC clamping guide. It should be made of high-quality materials, such as hardened steel or alloy, to withstand the forces exerted during machining. Quality clamping guides also have a robust design, allowing them to endure repetitive use without losing their effectiveness.
Cost is another important consideration. CNC clamping guides vary in price depending on factors like material, size, and brand. It is advisable to choose a clamping guide that offers the best value for money, balancing both quality and cost-effectiveness.
There are numerous suppliers of CNC clamping guides available in the market. It is recommended to research and choose a reputable supplier known for delivering reliable and durable clamping guide products. Reading customer reviews and checking their track record can help in making an informed decision.
Certification, such as ISO 9001, is an indicator of a supplier’s commitment to quality and compliance with international standards. It is advisable to choose a supplier with relevant certifications to ensure that the clamping guides meet industry requirements.
The CNC clamping guide market is growing steadily due to the rapid expansion of the machining industry. With the increasing demand for precision machining, the need for reliable and efficient clamping guides is also rising.
Here are some tips for choosing the right CNC clamping guide:
1. Consider the type and size of workpieces you will be machining.
2. Ensure compatibility with your CNC machine and other accessories.
3. Look for adjustable and versatile clamping guides to accommodate different workpiece sizes and shapes.
4. Prioritize quality and durability over lower cost options.
FAQ:
Q: What is the purpose of a CNC clamping guide?
A: A CNC clamping guide securely holds workpieces in place during machining to ensure accuracy and precision.
Q: How do I select the right size of CNC clamping guide?
A: Consider the size and shape of your workpieces and select a clamping guide that can accommodate them comfortably.
In summary, CNC clamping guides are vital tools for the machining industry. Quality, cost, supplier reliability, certifications, and compatibility should be considered when selecting one. The market for CNC clamping guides is growing due to the industry’s expansion, so choosing the right guide is crucial for precise and efficient machining operations.
Types of cnc clamping
CNC clamping refers to the process of securing a workpiece or tool in place during machining on a CNC (Computer Numerical Control) machine. There are several types of CNC clamping techniques used depending on the application and the type of workpiece being machined. Here are some common types of CNC clamping:
1. Manual Clamping: This is the most basic type of clamping, where the operator manually tightens the clamps to secure the workpiece in place. It is suitable for simple and small-sized workpieces that do not require high precision.
2. Mechanical Clamping: Mechanical clamping involves the use of clamping devices such as vices, clamps, or fixtures. These devices provide a secure and rigid grip on the workpiece. Mechanical clamping is commonly used for milling operations, where the workpiece is held in place by the force applied by the clamping device.
3. Hydraulic Clamping: Hydraulic clamping systems use hydraulic pressure to secure the workpiece. This type of clamping is often used for heavy and large-sized workpieces that require high clamping force. Hydraulic clamping systems provide greater stability and precision during machining operations.
4. Pneumatic Clamping: Pneumatic clamping involves the use of compressed air to secure the workpiece. It is generally used for lightweight workpieces or where quick clamping and releasing are required. Pneumatic clamping systems are fast and easy to operate.
5. Vacuum Clamping: Vacuum clamping utilizes suction to hold the workpiece in place. It is commonly used for thin and flat workpieces with smooth surfaces, such as sheet metal or glass. Vacuum clamping provides uniform gripping force across the entire workpiece surface.
6. Magnetic Clamping: Magnetic clamping employs magnets to hold the workpiece securely. It is commonly used for ferrous materials and provides a strong and stable grip, even during heavy machining operations. Magnetic clamping is fast and easy to set up.
7. Specialized Clamping: Depending on the specific requirements of the machining operation, specialized clamping techniques may be used. This includes 3D printed customized fixtures, adhesive clamping, or even combination clamping methods.
Choosing the right clamping method is crucial for achieving accurate and reliable machining results. Factors such as workpiece material, size, shape, and the required holding force need to be considered when selecting a clamping technique. The chosen clamping method should provide sufficient stability and rigidity to prevent workpiece movement during machining, ensuring the desired precision and finish of the final product.
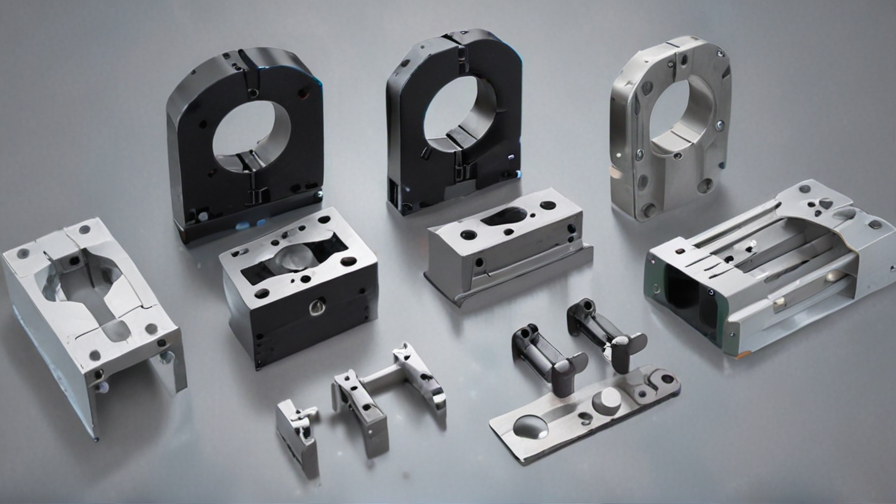
Pros and Cons of Using cnc clamping
CNC clamping is an essential process in the manufacturing industry that involves holding and securing a workpiece during CNC machining operations. This technique offers various advantages and disadvantages, which can significantly impact the overall production process. Here are the pros and cons of using CNC clamping:
Pros:
1. Enhanced precision: CNC clamping ensures the workpiece remains securely fixed in place during machining. This prevents any movement or vibration that could result in inaccuracies, delivering precise and consistent results.
2. Increased productivity: With CNC clamping, manufacturers can achieve higher machining speeds and feed rates without compromising the stability of the workpiece. This leads to improved efficiency and increased productivity.
3. Versatility: CNC clamps come in various sizes and designs, allowing for the secure clamping of different types and shapes of workpieces. This versatility makes CNC clamping suitable for a wide range of machining applications.
4. Cost-effective: CNC clamping eliminates the need for manual clamping methods, which can be time-consuming and labor-intensive. By reducing manual labor requirements, CNC clamping helps optimize production processes and reduce costs.
5. Improved safety: CNC clamps provide reliable and stable clamping, minimizing the risk of workpiece slippage or ejection during machining. This promotes a safer working environment for operators.
Cons:
1. Initial investment: The purchase and installation of CNC clamping systems can be costly, especially for small-scale manufacturers. This initial investment may deter some businesses from adopting CNC clamping.
2. Limited workpiece size: CNC clamps have certain size limitations, which may restrict the size of workpieces that can be effectively clamped. This can be a disadvantage for manufacturers working on larger objects.
3. Design limitations: Some complex workpiece designs may pose challenges when it comes to clamping. Certain shapes or features might require specialized clamping techniques, which can be more time-consuming and less efficient.
4. Potential damage: Incorrect clamping setup or excessive clamping force can potentially damage the workpiece, resulting in scrapped parts and additional costs. It is crucial to carefully program and monitor the clamping process to avoid such issues.
In conclusion, CNC clamping offers significant advantages in terms of precision, productivity, versatility, and safety. However, it also has some drawbacks, including initial investment costs, size limitations, design challenges, and potential damage risks. Manufacturers should carefully evaluate their specific requirements and consider these pros and cons to determine the suitability of CNC clamping for their operations.
cnc clamping Reference Specifications (varies for different product)
CNC (Computer Numerical Control) clamping is an essential aspect of the manufacturing process, ensuring secure fixation of the workpiece during machining operations. Reference specifications for CNC clamping vary depending on the specific product being manufactured. However, certain key parameters are generally considered to ensure efficient and accurate clamping operations.
One crucial reference specification in CNC clamping is the clamping force. It refers to the force required to securely hold the workpiece in place against the cutting forces generated during machining. The clamping force should be carefully determined to avoid workpiece deformation or slippage and to guarantee dimensional accuracy and surface finish of the machined part. The required clamping force varies depending on factors such as workpiece material, size, shape, and the type of machining operations involved.
Another important consideration is the clamping mechanism or system. CNC clamping systems include various types such as hydraulic, pneumatic, mechanical, or magnetic systems. The choice of clamping mechanism depends on factors like the workpiece material, production volume, accessibility, and the required clamping force. It is crucial to select a clamping mechanism that ensures optimal grip and stability while allowing easy loading and unloading of the workpiece.
The clamping device or fixture design is also critical in CNC clamping. The fixture holds the workpiece securely in the desired position and orientation during machining. It should be designed to accommodate the specific geometry of the workpiece and provide adequate support. Proper alignment and locating features should be incorporated in the fixture design to enable repeatability and precise positioning of the workpiece. Additionally, the fixture should allow for efficient chip evacuation, coolant flow, and accessibility for tooling.
Furthermore, the clamping setup time is a vital consideration in CNC clamping specifications. Minimizing the setup time is crucial to enhance productivity and reduce manufacturing costs. Quick-change clamping systems or modular fixtures can significantly reduce setup time by allowing rapid and accurate workpiece changeovers.
In conclusion, CNC clamping reference specifications encompass several key parameters such as clamping force, clamping mechanism, fixture design, and setup time. Adhering to these specifications ensures effective and reliable clamping operations, ultimately leading to high-quality, accurate, and efficient manufacturing processes.
Applications of cnc clamping
CNC clamping refers to the process of securing workpieces in place during Computer Numerical Control (CNC) machining operations. This technique is crucial for maintaining accuracy and ensuring quality throughout the manufacturing process. CNC clamping systems are designed to firmly hold components in position while subjected to various cutting, milling, drilling, or grinding forces. By stabilizing workpieces, CNC clamping plays a vital role in enhancing productivity, efficiency, and safety in various industries.
One prominent application of CNC clamping is in the automotive industry, where it is used in the production of various vehicle components. These clamping systems securely hold engine blocks, cylinder heads, crankshafts, and other intricate parts, enabling precise machining and enhancing tolerances. CNC clamping ensures that critical features and dimensions of automotive components are accurately machined, leading to reliable and high-performing end products.
Another significant application of CNC clamping is in the aerospace industry. This sector demands extremely tight tolerances due to safety and performance requirements. CNC clamping systems are utilized to secure materials like aluminum, titanium, and composites during milling, drilling, or cutting operations. By preventing unwanted vibrations or movements, CNC clamping ensures precise machining and reduces the risk of errors in aerospace components, such as aircraft wings, fuselages, or engine parts.
CNC clamping also finds a wide range of applications in the electronics industry. It is essential for the manufacturing of PCBs (Printed Circuit Boards) and other electronic components. CNC clamping systems precisely hold the workpieces, allowing accurate drilling, soldering, and routing operations. With the right clamping approach, the risk of damage to delicate electronic components can be minimized, ensuring high-quality products that meet stringent industry standards.
Furthermore, CNC clamping is extensively used in the production of furniture and cabinetry. Whether machining wood, metal, or composite materials, CNC clamping systems provide stability and safety during cutting, carving, or shaping operations. This enables manufacturers to achieve intricate designs, precise measurements, and consistent product quality.
In summary, CNC clamping plays a critical role in various industries requiring precise and efficient machining. From automotive and aerospace to electronics and furniture manufacturing, CNC clamping systems ensure secure workpiece fixation, enabling accurate and reliable results. These applications highlight the significance of CNC clamping in enhancing productivity, improving product quality, and reducing manufacturing costs.
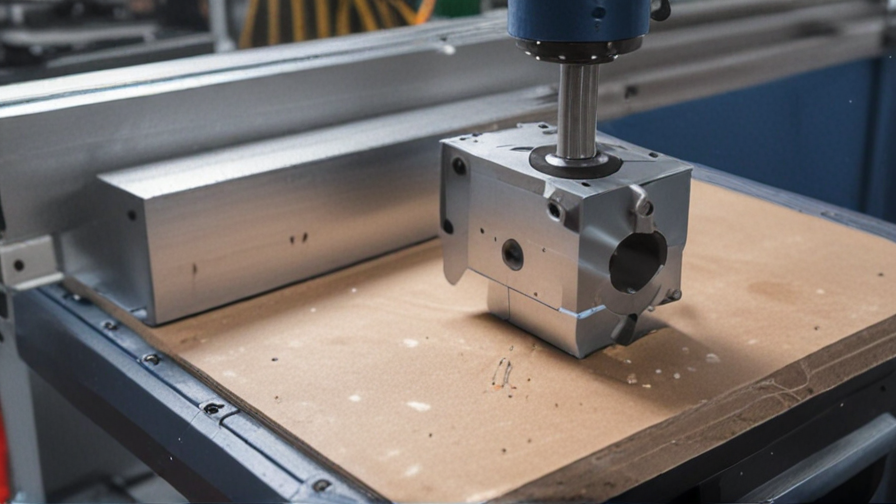
The Work Process and how to use cnc clamping
The work process of using CNC clamping involves several steps to ensure proper setup and operation.
Firstly, it is important to select the appropriate type of CNC clamp for the specific application. There are various clamping devices available, such as vise clamps, hydraulic clamps, pneumatic clamps, and magnetic clamps, each designed for different purposes and materials.
Once the appropriate clamp is chosen, the workpiece is positioned securely in the machine’s cutting area. This can be done by attaching the clamp to the worktable or machine bed and adjusting it to hold the workpiece firmly in place.
Next, the CNC machine is programmed with the desired specifications for the cutting or machining operation. This includes inputting the necessary tool paths, speeds, feeds, and other parameters. The machine’s computer control system ensures accurate and precise execution of these instructions.
Before starting the machining process, it is important to check that the clamp is securely tightened and that the workpiece is correctly aligned. This helps prevent any movement or vibration during operation, which could lead to inaccuracies or damage.
Once everything is set up, the CNC machine can be started, and the cutting or machining operation begins. The machine, guided by the programmed instructions, moves the cutting tool or tools in a controlled manner to shape or remove material from the workpiece.
During the machining process, it is important to periodically check the clamp and workpiece to ensure stability and accuracy. Any necessary adjustments or repositioning should be made to maintain the desired outcome.
Once the machining operation is completed, the clamp can be loosened, and the finished part can be removed from the machine. It is important to handle the finished part carefully to avoid damage.
In summary, the work process of using CNC clamping involves selecting the appropriate clamp, positioning and aligning the workpiece, programming the machine, securely tightening the clamp, executing the machining operation, and checking for stability and accuracy throughout the process. Attention to detail and proper set up are key to achieving high-quality results.
Quality Testing Methods for cnc clamping and how to control the quality
When it comes to quality testing methods for CNC clamping, several approaches can be employed to ensure that the clamping process meets the required standards. Here are some commonly used methods:
1. Visual Inspection: The clamping components, such as clamps, screws, and support structures, are visually examined for any physical defects or damages. This inspection helps identify any visible abnormalities that could impact the clamping quality.
2. Dimensional Accuracy: Key dimensions of the clamping components are measured using precision tools like calipers and micrometers. These measurements are compared to the specified tolerances to ensure that the clamping system is within acceptable limits.
3. Torque Testing: The clamping screws or bolts are tightened using an appropriate torque wrench. The torque applied is measured to ensure that it meets the specified requirements. This helps guarantee that the clamps securely hold the workpiece without any chances of slippage during machining operations.
4. Load Testing: The clamping system is subjected to the maximum or predetermined load it will encounter during the CNC machining process. This test helps evaluate the clamping system’s ability to withstand the applied load without any significant deformation or failure.
To control the quality of CNC clamping, the following practices can be implemented:
1. Standard Operating Procedures (SOPs): Develop comprehensive SOPs for clamping operations, which outline the correct procedures, parameters, and requirements for ensuring consistent clamping quality. Regularly train and update the personnel on these SOPs.
2. Regular Maintenance: Implement a preventive maintenance program to ensure that clamping components are regularly inspected, cleaned, and calibrated. This helps identify and rectify any potential issues that may degrade the clamping quality.
3. Statistical Process Control (SPC): Utilize SPC techniques to continuously monitor and control the clamping process. By collecting and analyzing data at various stages of clamping, any process variations or deviations can be quickly identified and rectified.
4. Continuous Improvement: Encourage feedback from operators and regularly review the clamping process to identify potential improvement areas. This can involve investing in better clamping equipment, exploring innovative clamping solutions, or optimizing existing clamping methods.
By utilizing appropriate quality testing methods and implementing robust quality control measures, the CNC clamping process can consistently deliver high-quality results while minimizing the chances of errors or subpar performance.
cnc clamping Sample Policy and Post-Purchase Considerations for cnc clamping from China
Sample Policy:
When purchasing CNC clamping from China, it is important to have a clear and detailed sample policy. This policy should outline the terms and conditions for requesting samples from the supplier. The policy may include the following elements:
1. Sample Request Process: Specify the procedure for requesting samples, including the necessary information to provide (such as product specifications, quantity, and shipping address).
2. Sample Cost: Clearly state if there are any charges associated with samples (including product cost, shipping fees, and any taxes or customs duties). Additionally, mention whether sample costs will be refunded upon placing a bulk order.
3. Sample Delivery Time: Set expectations regarding the time it takes for the supplier to prepare and ship the samples. This can help avoid misunderstandings and ensure a smooth process.
4. Sample Quality Assurance: Establish a guarantee that the samples provided will be representative of the actual product’s quality, functioning, and appearance.
5. Sample Modifications: Specify whether customization or modification of samples is possible, and if so, any additional charges or restrictions that may apply.
Post-Purchase Considerations:
After purchasing CNC clamping from a Chinese supplier, it is essential to consider a few key factors to ensure a successful transaction:
1. Quality Inspection: Implement a thorough quality inspection upon receiving the products. This includes verifying that the CNC clamping meets the agreed-upon specifications, functions properly, and is free from any defects or damages caused during transportation.
2. Communication: Maintain open and frequent communication with the supplier, addressing any concerns or questions that may arise post-purchase. This ensures a clear understanding between both parties and facilitates prompt resolution of any issues.
3. Warranty and Return Policies: Familiarize yourself with the supplier’s warranty and return policies. Be aware of the terms and conditions, including the warranty period, eligible reasons for return, and any associated costs. Promptly report any defects or damages that occur within the warranty period to benefit from possible compensation or replacement.
4. Long-Term Relationship: If satisfied with the CNC clamping and the supplier’s service, consider establishing a long-term relationship. This can create a reliable source for future purchases, providing consistent product quality, and potentially better terms and prices.
By implementing a clear sample policy and considering important post-purchase factors, you can minimize risks and ensure a positive experience when purchasing CNC clamping from China.
Sourcing cnc clamping from China: Opportunities, Risks, and Key Players
Sourcing CNC clamping from China offers various opportunities, as well as risks, in the market. China has emerged as a major hub for manufacturing, including CNC clamping, due to its cost-effective production capabilities and extensive supplier network. The opportunities associated with sourcing from China include competitive pricing, access to a wide range of suppliers, and potential for customization.
One key opportunity lies in the cost advantage offered by Chinese manufacturers. Generally, labor and production costs in China are lower compared to many other countries, allowing for more affordable prices on CNC clamping products. This can be advantageous for businesses looking to optimize their supply chain and reduce manufacturing expenses.
Moreover, China’s vast supplier network provides companies with a wide array of options to choose from. This allows buyers to select from numerous players in the CNC clamping market, fostering healthy competition and potential for better product quality, design, and innovation.
However, sourcing from China also involves certain risks and challenges. One major concern is the potential for quality issues. While China excels in mass production, there have been cases of substandard or counterfeit products being supplied. To mitigate this risk, thorough due diligence and careful supplier selection are crucial. Conducting factory audits and requesting product samples can help ensure quality standards are met.
Another risk is intellectual property (IP) infringement. China has faced allegations of IP theft and non-compliance with international patent laws. Companies sourcing from China should utilize legal measures, such as filing for patents and trademarks, to protect their proprietary designs and technologies.
Key players in the CNC clamping market in China include:
1. Gerardi SPA: A leading Italian company with production facilities in China, providing a wide range of CNC clamping solutions.
2. Jergens Inc.: An American manufacturer that has established a presence in China, offering innovative CNC clamping and workholding solutions.
3. EROWA AG: A Swiss company with manufacturing facilities in China, specializing in high-precision CNC clamping systems.
4. Mitee-Bite Products LLC: An American manufacturer with a presence in China, known for their innovative and flexible CNC clamping solutions.
Overall, sourcing CNC clamping from China presents opportunities for competitive pricing and access to a large supplier network. However, careful evaluation of suppliers and protection of intellectual property are essential to mitigate risks and ensure product quality.
How to find and select reliable cnc clamping manufacturers in China,use google search manufacturers and suppliers
When searching for reliable CNC clamping manufacturers in China, Google can be a helpful tool to begin the process. Here are a few steps to follow:
1. Start by searching for specific keywords such as “CNC clamping manufacturers in China” or “CNC clamping suppliers in China.” This will generate a list of potential manufacturers and suppliers.
2. Visit the websites of the companies that appear in the search results. Look for relevant information such as their experience in the industry, product range, certifications, and any customer testimonials or case studies.
3. Check if the manufacturer has a physical address listed on their website. A legitimate manufacturer should provide a verifiable address, and it can be useful to ensure they are not just a trading company.
4. Look for information about their manufacturing capabilities, including the type of CNC machines they use, the materials they work with, and any customizability options they offer. This will help determine if they can meet your specific requirements.
5. Verify the manufacturer’s quality control processes and certifications. Look for ISO certifications or other quality management system certifications to ensure that their products meet international standards.
6. Check for any online reviews or feedback from previous customers. Websites like Alibaba, Made-in-China, or Global Sources may have customer ratings, reviews, or comments that can provide insights into the reliability and quality of the manufacturer.
7. Consider contacting the manufacturer directly to request additional information or ask specific questions about their products, production processes, and capabilities. The responsiveness and professionalism of their communication can be a good indicator of their reliability and customer service.
8. If possible, consider visiting the manufacturer’s facilities in person to evaluate their production capabilities, quality control measures, and to establish a direct relationship.
Remember, it is important to thoroughly research and evaluate potential CNC clamping manufacturers in China before making a final selection. Taking the time to find a reliable and trustworthy partner will ensure smoother cooperation and satisfactory results.
How to check cnc clamping manufacturers website reliable,use google chrome SEOquake check if ranking in top 10M
To determine the reliability of a CNC clamping manufacturer’s website, you can follow these steps:
1. Use Google Chrome: Open the website in the Google Chrome browser for a smoother browsing experience and better compatibility with SEO tools.
2. Install SEOquake: Add the SEOquake extension to your Google Chrome browser. This tool provides an overview of the website’s SEO performance and ranking.
3. Check ranking in top 10M: Activate SEOquake and navigate to the manufacturer’s website. Look for the option to display Metrics and activate it. This will show you various statistics about the website, including its Alexa Rank. If the website is ranked within the top 10 million, it suggests a decent level of popularity and visibility.
4. Analyze website metrics: SEOquake provides additional metrics such as organic search visibility, the number of indexed pages, and the website’s traffic estimation. Browsing through these metrics can help evaluate the website’s overall SEO performance and credibility.
5. Assess website design and content: Evaluate the website’s design, layout, and overall user experience. A professional and user-friendly design indicates a higher level of reliability. Check for comprehensive information about the CNC clamping products, including specifications, certifications, and customer reviews or testimonials. Ensure that the content is well-written and provides accurate details.
6. Look for contact information: A reliable manufacturer should have clear contact information readily available on their website, such as a physical address, phone number, and email. This allows for easy communication and indicates their willingness to assist customers.
7. Verify certifications and licenses: If the website claims to have certain certifications or licenses, cross-check this information with the relevant authorities or certification bodies. Authentic certifications provide assurance of quality and reliability.
Remember to use these steps as a guide but also rely on your judgment and intuition when assessing the reliability of a CNC clamping manufacturer’s website.
Top 10 cnc clamping manufacturers in China with each 160 words introduce products,then use markdown create table compare
1. Jiangsu Shuangyang Precision Tools Co., Ltd.
Established in 2008, Jiangsu Shuangyang Precision Tools offers a wide range of CNC clamping solutions. Their products include precision vises, modular vise systems, CNC machine tool vise jaws, and quick-change pallet systems. Shuangyang is known for its high-quality products and innovative designs, catering to the diverse needs of customers from various industries.
2. Zhejiang Rizhong CNC Machine Tool Co., Ltd.
Founded in 2000, Zhejiang Rizhong CNC Machine Tool specializes in the production of hydraulic clamping systems. Their product range encompasses hydraulic vises, rotary tables, indexing heads, and power chucks. With a strong focus on technology and quality, Rizhong is renowned for its reliable clamping solutions in the CNC machining industry.
3. Shandong Fangzheng Machine Tool Co., Ltd.
Shandong Fangzheng Machine Tool is a leading manufacturer of CNC clamping fixtures and workholding systems. Their product portfolio includes precision machine vises, quick-change pallet systems, and hydraulic clamps. With a commitment to continuous innovation, Fangzheng’s products are designed to enhance precision and efficiency in machining operations.
4. Dongguan Weichang Precision Machinery Co., Ltd.
Dongguan Weichang Precision Machinery has been dedicated to the development and production of CNC machine tool accessories since 2000. Their range of products includes quick-change CNC vises, modular fixture systems, and power chucks. Weichang’s clamping solutions are widely used in industries such as automotive, aerospace, and electronics.
5. Beijing Marchic Automation Equipment Co., Ltd.
As a leading manufacturer of intelligent CNC clamping systems, Beijing Marchic Automation Equipment offers integrated solutions for workholding. Their product lineup comprises hydraulic vises, self-centering chucks, and flexible clamping modules. Marchic’s products are widely recognized for their advanced technology and excellent performance.
6. Suzhou Sunzu Precision Machinery Co., Ltd.
Suzhou Sunzu Precision Machinery specializes in the production of CNC clamping tools and accessories. Their offerings include CNC vises, leveling jacks, and indexing heads. Sunzu’s products are widely used in precision machining applications, meeting the stringent demands of customers within the metalworking industry.
7. Guangdong Jingjie Intelligent Equipment Co., Ltd.
Guangdong Jingjie Intelligent Equipment focuses on the design and manufacture of high-precision CNC clamping fixtures. Their range includes CNC vises, rotary tables, and magnetic chucks. Jingjie’s products are known for their stability, durability, and accuracy, ensuring optimal workpiece fixation during machining processes.
8. Zhejiang Chenggao Machinery Co., Ltd.
With over 20 years of experience, Zhejiang Chenggao Machinery specializes in the production of CNC clamping devices. Their product range encompasses hydraulic vises, toggle clamps, and quick-change pallet systems. Chenggao’s clamping solutions are widely used in machining centers, providing efficient and reliable workholding solutions.
9. Ningbo GMT Precision Machinery Co., Ltd.
Ningbo GMT Precision Machinery is renowned for its precision CNC clamping solutions. They offer a comprehensive range of products, including precision vises, modular clamping systems, and magnetic chucks. GMT’s products are widely used in various industries, guaranteeing high accuracy and stability during machining operations.
10. Jiangmen Weirui Industrial Development Co., Ltd.
Jiangmen Weirui Industrial Development specializes in the design and manufacture of CNC clamping devices. Their product portfolio includes precision vises, pneumatic clamps, and workholding fixtures. Weirui’s clamping solutions are widely adopted in the automotive, mold, and mechanical industries due to their reliability and precision.
| Manufacturer | Products Offered |
| ——————————— | ————————————————————- |
| Jiangsu Shuangyang Precision Tools | Precision vises, modular vise systems, vise jaws |
| Zhejiang Rizhong CNC Machine Tool | Hydraulic vises, rotary tables, indexing heads, power chucks |
| Shandong Fangzheng Machine Tool | Machine vises, quick-change pallet systems, hydraulic clamps |
| Dongguan Weichang Precision Mach. | Quick-change vises, fixture systems, power chucks |
| Beijing Marchic Automation Equip. | Hydraulic vises, self-centering chucks, flexible clamping mods |
| Suzhou Sunzu Precision Machinery | CNC vises, leveling jacks, indexing heads |
| Guangdong Jingjie Intelligent Eq. | CNC vises, rotary tables, magnetic chucks |
| Zhejiang Chenggao Machinery | Hydraulic vises, toggle clamps, quick-change pallet systems |
| Ningbo GMT Precision Machinery | Precision vises, modular clamping systems, magnetic chucks |
| Jiangmen Weirui Industrial Dev. | Precision vises, pneumatic clamps, workholding fixtures |
Background Research for cnc clamping manufacturers Companies in China, use qcc.com archive.org importyeti.com
When researching CNC clamping manufacturers in China, several websites can provide valuable information. One such website is qcc.com, which is a Chinese business database that offers comprehensive company profiles. By searching for CNC clamping manufacturers on this platform, one can find a list of companies along with basic details such as contact information, business scope, and registration details. This can be a useful starting point to gather a list of potential manufacturers.
Another useful website is archive.org, which offers access to historical data of websites. This can be helpful to evaluate the credibility and reliability of a CNC clamping manufacturer’s website. By checking the website’s past versions and analyzing any changes or trends over time, one can gain insights into the manufacturer’s stability and consistency.
Importyeti.com is another platform that can be valuable when searching for CNC clamping manufacturers in China. It provides data on import and export activities of various companies, including the products they import or export, as well as their trading partners. This information can be essential for assessing the experience and international reach of potential manufacturers.
In conclusion, qcc.com, archive.org, and importyeti.com are beneficial resources for conducting background research on CNC clamping manufacturers in China. Qcc.com provides company profiles, archive.org offers historical website data, and importyeti.com delivers import and export information. By utilizing these platforms, one can gather essential details to evaluate manufacturers and make informed decisions.
Leveraging Trade Shows and Expos for cnc clamping Sourcing in China
Trade shows and expos provide excellent opportunities for sourcing CNC clamping solutions in China. These events gather numerous suppliers and manufacturers under one roof, allowing buyers to assess and connect with potential suppliers efficiently. Leveraging these platforms enables businesses to explore the wide range of options available in the Chinese market, while also building relationships with trustworthy and reliable suppliers.
Attending trade shows and expos related to CNC clamping presents a unique opportunity to see the products firsthand, assess their quality, and compare different suppliers. It allows buyers to evaluate the latest technologies, materials, and designs in the industry, ensuring that the chosen supplier can meet their specific needs and requirements. Additionally, engaging in face-to-face communication with suppliers at these events helps in establishing a level of trust and confidence in their capabilities.
It is crucial, however, to make the most of these trade shows and expos by conducting thorough research beforehand. Understanding the specific needs of the business, researching potential suppliers, and having a clear idea of the desired CNC clamping solutions will ensure that the right exhibitors are targeted. This preparation will help optimize the limited time available at the event and maximize the chances of finding suitable suppliers.
During the trade show or expo, buyers should take the opportunity to gather information about suppliers, their manufacturing processes, quality control measures, and any certifications they possess. Engaging in detailed discussions about pricing, customization options, and lead times is also essential to make informed decisions.
After the event, it is crucial to follow up with potential suppliers to continue the conversation and obtain any additional information required. This may include requesting samples, discussing specific product modifications, or negotiating pricing and terms. Conducting due diligence by checking references, verifying qualifications, and carefully reviewing agreements is also vital before finalizing any orders.
In conclusion, trade shows and expos offer invaluable opportunities for sourcing CNC clamping solutions in China. By leveraging these platforms effectively, businesses can connect with potential suppliers, assess their products, and establish reliable partnerships that meet their specific needs. With careful preparation and thorough evaluation, trade shows and expos can be a strategic tool for successful overseas sourcing.
The Role of Agents and Sourcing Companies in Facilitating cnc clamping Purchases from China
Agents and sourcing companies play a crucial role in facilitating CNC clamping purchases from China. These intermediaries act as a bridge between buyers and Chinese manufacturers, streamlining the purchasing process and ensuring smooth operations.
Firstly, agents and sourcing companies have extensive networks and relationships with various manufacturers in China. They help buyers identify reliable and trustworthy suppliers that meet their specific requirements. This saves buyers a considerable amount of time and effort, as they don’t have to conduct extensive research themselves. Agents and sourcing companies also have in-depth knowledge of the local market and can provide valuable insights into the latest trends, pricing information, and product availability.
Additionally, agents and sourcing companies act as quality control inspectors, conducting factory audits and product inspections. They ensure that the CNC clamping products meet the required standards and specifications set by the buyers. By carrying out quality control measures, these intermediaries mitigate the risks of receiving substandard or defective products. This helps buyers avoid potential losses and maintain their reputation as reliable suppliers to their customers.
Furthermore, agents and sourcing companies assist with negotiations and contract agreements between buyers and manufacturers. They can effectively communicate the buyer’s requirements and negotiate competitive prices on their behalf. With their knowledge of the local language and culture, these intermediaries bridge the communication gap between buyers and manufacturers, ensuring a smooth transaction process.
Moreover, agents and sourcing companies handle logistics and shipping arrangements. They coordinate the transportation of the CNC clamping products from the manufacturer’s facility to the buyer’s location. This includes managing customs clearance, documentation, and arranging for the most cost-effective and efficient shipping methods. By taking care of these logistical aspects, agents and sourcing companies ensure that the products are delivered in a timely manner and at the lowest possible costs.
In conclusion, agents and sourcing companies play a vital role in facilitating CNC clamping purchases from China. They simplify the sourcing process by leveraging their networks, conducting quality control inspections, assisting with negotiations, and managing logistics. Their expertise and support not only save time and effort for buyers but also ensure a hassle-free and successful purchasing experience.
Price Cost Research for cnc clamping manufacturers Companies in China, use temu.com and 1688.com
When conducting price cost research for CNC clamping manufacturers in China, two reliable platforms to consider are temu.com and 1688.com. These platforms provide a wide range of suppliers and products, making them ideal for sourcing CNC clamping manufacturers in China.
Temu.com is an online global trade service platform that connects buyers with suppliers. It offers a variety of features such as product search, real-time quotations, and professional services. By searching for “CNC clamping manufacturers” on temu.com, a list of suppliers specializing in CNC clamping products can be obtained. It is recommended to filter the suppliers based on factors like their product range, customer reviews, and response rate to ensure a reliable and suitable supplier is chosen.
1688.com is a Chinese online wholesale platform that offers a vast range of products directly from manufacturers. It is commonly used by buyers around the world to source products from China. By searching for “CNC clamping manufacturers” on 1688.com, a comprehensive list of suppliers and manufacturers can be found. It provides detailed product information, pricing, and contact details, allowing buyers to easily connect with potential suppliers.
When researching prices, it is essential to consider various factors such as the quality of the products, manufacturing capabilities, and additional services provided by the suppliers. Requesting quotations from multiple manufacturers can help in comparing prices and negotiating favorable terms.
The research should also take into account the minimum order quantities, payment terms, and shipping options offered by the manufacturers. Understanding these details can help in estimating the overall cost, including manufacturing, shipping, and any additional charges.
In conclusion, temu.com and 1688.com are valuable platforms for conducting price cost research for CNC clamping manufacturers in China. By utilizing these platforms and considering various factors, buyers can identify reliable suppliers, compare prices, and make informed decisions for their sourcing needs.
Shipping Cost for cnc clamping import from China
The shipping cost of importing CNC clamping from China can vary based on various factors. The two primary factors that significantly impact the shipping cost are the weight of the shipment and the shipping method chosen.
The weight of the shipment is a key consideration as shipping costs are often calculated based on weight. CNC clamping equipment can vary in weight, depending on the size and specifications. It is essential to determine the weight of the shipment accurately to get an estimation of the shipping cost.
The shipping method chosen also affects the shipping cost. Generally, there are three main shipping methods: air freight, sea freight, and courier services like DHL, FedEx, or UPS. Air freight tends to be expensive but delivers the goods quickly. Sea freight is a more affordable option for bulky shipments, but it is a slower mode of transportation. Courier services are generally faster, but their rates can be relatively high.
Additionally, other factors that may influence the shipping cost include the origin and destination ports, customs duties and taxes, insurance, packaging, and any additional services required, such as door-to-door delivery or customs clearance.
To ensure that the shipping cost remains within a specified budget, it is advisable to compare quotes from different shipping companies, negotiate rates, and evaluate various shipping options based on the urgency of delivery, cost, and reliability. Moreover, consolidating shipments or opting for groupage services can help in reducing the overall shipping cost.
In conclusion, the shipping cost for importing CNC clamping from China depends on factors like weight, shipping method, origin and destination ports, customs duties, and additional services required. By meticulously assessing these factors and exploring cost-effective options, it is possible to find a shipping solution that fits within a budget.
Compare China and Other cnc clamping Markets: Products Quality and Price,Visible and Hidden Costs
China is known as one of the largest manufacturers and exporters of various products globally, including CNC clamping equipment. When comparing China to other CNC clamping markets, several aspects should be considered, such as product quality, price, visible and hidden costs.
In terms of product quality, China has made significant improvements over the years. Many Chinese manufacturers have invested in advanced technology and machinery, allowing them to produce high-quality CNC clamping equipment that meets international standards. However, it is important to note that there is still a wide range of quality among Chinese manufacturers. Some companies prioritize cost-cutting measures, resulting in lower quality products. On the other hand, other countries known for their CNC clamping equipment, such as Germany or Japan, have established a reputation for producing superior quality products with rigorous quality control systems.
When it comes to price, China often offers competitive prices for CNC clamping equipment. The labor costs in China are generally lower compared to other developed countries, allowing manufacturers to offer their products at a more affordable price point. However, it is crucial to consider hidden costs associated with importing from China, such as shipping fees, import duties, and taxes. These costs can significantly affect the overall price and should be taken into account when comparing prices with other markets.
Visible and hidden costs should also be considered when evaluating CNC clamping equipment from different markets. China often offers lower visible costs due to its competitive pricing; however, hidden costs such as quality control, intellectual property protection, and communication issues can arise. For instance, some manufacturers in China may offer lower prices but compromise on quality control measures, resulting in potential product defects or long-term reliability issues. Intellectual property protection can also be a concern, as unauthorized copying or counterfeiting may occur more frequently in China compared to other markets.
In conclusion, China holds a prominent position in the CNC clamping market due to its vast manufacturing capabilities and competitive pricing. However, product quality can vary among Chinese manufacturers, and hidden costs such as quality control and intellectual property protection should be carefully considered. When comparing with other markets, countries like Germany or Japan may offer higher quality CNC clamping equipment, but at a higher price. Ultimately, it is crucial for buyers to thoroughly evaluate their specific requirements and consider the trade-offs between quality, price, and hidden costs when making a purchasing decision.
Understanding Pricing and Payment Terms for cnc clamping: A Comparative Guide to Get the Best Deal
When purchasing CNC clamping equipment, understanding pricing and payment terms is crucial to ensure the best deal. Here is a comparative guide to help you make an informed decision:
1. Price Comparison: Start by comparing prices from different suppliers. Look for reputable manufacturers or distributors who offer CNC clamping products. Consider factors such as the quality, features, and reliability of the clamping systems alongside the price. It is essential to strike a balance between affordability and functionality.
2. Volume Discounts: Inquire about volume discounts if you plan to buy a significant quantity of CNC clamping equipment. Some suppliers offer discounts based on the volume of the order. It is advisable to negotiate and explore these possibilities to optimize your expenses.
3. Payment Terms: Understand the payment terms offered by suppliers. Some may require full payment upfront, while others may offer flexible payment options like installments or net payment terms, allowing you to pay after delivery. Assess your budget and choose the payment plan that suits your financial situation.
4. Shipping and Handling Costs: Don’t forget to consider shipping and handling costs when comparing prices. Some suppliers may include these expenses in their pricing, while others may charge separately. Scrutinize the total cost, including these additional fees, to get an accurate comparison.
5. Warranty and Support: Ascertain the warranty period offered by each supplier. A longer warranty indicates the manufacturer’s confidence in their product’s quality. Additionally, inquire about post-purchase support, such as technical assistance and spare parts availability. Reliable support can save both time and money in the long run.
6. Reputation and Reviews: Research the reputation and customer reviews of the suppliers. Look for feedback regarding the pricing, payment terms, product quality, and customer service. This information can give you valuable insights into the supplier’s reliability and help you make an informed decision.
In conclusion, when purchasing CNC clamping equipment, it is crucial to compare prices, negotiate volume discounts, understand payment terms, consider shipping costs, assess warranty and support, and research supplier reputation. By carefully considering these factors, you can secure the best deal and ensure high-quality CNC clamping equipment that meets your needs.
Chinese Regulations and Industry Standards Certifications for cnc clamping,Import Regulations and Customs for cnc clamping from China
In China, there are several regulations and industry standards certifications related to CNC clamping products. These certifications ensure the quality, safety, and performance of these products. The main certifications are:
1. China Compulsory Certification (CCC): This certification is mandatory for many CNC clamping products before they can be sold in the Chinese market. It covers safety aspects and ensures that the products meet the necessary quality standards.
2. ISO 9001: This international standard specifies requirements for a quality management system. Many CNC clamping manufacturers in China obtain ISO 9001 certification to demonstrate their commitment to quality control and customer satisfaction.
3. CE Marking: Although not a Chinese certification specifically, CE marking is required for CNC clamping products exported to the European market. It indicates compliance with relevant European Union directives, ensuring the products’ safety and meeting health, environmental, and consumer protection requirements.
When importing CNC clamping products from China, it is essential to understand the import regulations and customs procedures. These are some key points to consider:
1. Import Tariffs: Importing CNC clamping products may require paying import duties and taxes, which vary depending on the country and product category. Importers should check the specific tariff rates applicable in their country.
2. Customs Documentation: Importers need to prepare the necessary customs documentation, including commercial invoices, packing lists, bills of lading, and any required certificates or licenses. Accurate and complete documentation is crucial to ensure a smooth customs clearance process.
3. Customs Clearance Process: Importers must comply with the customs clearance procedures of their respective country. This process involves presenting the required documentation, paying any applicable customs duties and taxes, and providing additional information or inspections if needed.
4. Customs Broker: Engaging a customs broker or freight forwarder can be beneficial to navigate the customs clearance process. These professionals have the expertise to handle documentation, communicate with customs authorities, and ensure compliance with all regulations.
In summary, complying with Chinese regulations and industry standards certifications, as well as understanding import regulations and customs procedures, are essential when dealing with CNC clamping products from China. Adhering to these requirements helps ensure the quality and legality of the products and facilitates a smooth import process.
Sustainability and Environmental Considerations in cnc clamping Manufacturing
Sustainability and environmental considerations are of utmost importance in the manufacturing industry, including CNC clamping manufacturing. CNC (Computer Numerical Control) clamping refers to the process of using automated machinery to secure workpieces during the manufacturing process. In order to minimize the environmental impact, several measures can be taken.
One key aspect of sustainability in CNC clamping manufacturing is the efficient use of resources. By optimizing the production process, manufacturers can minimize waste generation, reduce energy consumption, and conserve raw materials. This can be achieved by implementing lean manufacturing principles, such as reducing setup times, improving machine utilization rates, and ensuring proper maintenance of equipment. Implementing these measures not only reduces the environmental footprint but also increases productivity and reduces costs.
Additionally, the choice of materials and their disposal at the end of their useful life are important considerations. Manufacturers should select materials that have a low environmental impact, such as recyclable or biodegradable materials. Furthermore, the responsible disposal of waste materials is crucial. Companies should have proper waste management systems in place to ensure that recyclable materials are properly separated and sent for recycling, while hazardous waste is dealt with in accordance with regulations.
Energy consumption is another significant aspect of sustainability. Efficient use of energy can be achieved through the use of energy-efficient machinery, such as CNC clamping machines that consume less power and have optimized programming. Moreover, companies can adopt renewable energy sources, such as solar or wind power, to further reduce their carbon footprint.
Finally, the implementation of environmentally friendly practices within the manufacturing facility itself can have a positive impact. For instance, companies can invest in energy-efficient lighting, implement water-saving measures, and promote a culture of sustainability among employees.
In conclusion, sustainability and environmental considerations play a vital role in CNC clamping manufacturing. By optimizing processes, selecting materials responsibly, minimizing waste, and reducing energy consumption, manufacturers can minimize their environmental impact while simultaneously improving productivity and reducing costs. It is essential for companies to prioritize sustainability and adopt practices that ensure long-term viability for both the environment and their business.
List The Evolution history of “cnc clamping”
CNC clamping has undergone significant evolution since its inception, revolutionizing manufacturing processes and increasing efficiency. This technology entails the use of computer numerical control (CNC) to automate clamping systems, ensuring precise and repeatable clamping actions in various machining operations.
The early history of CNC clamping can be traced back to the 1960s when CNC machining technology began to emerge. Traditional manual clamping methods were labor-intensive, time-consuming, and prone to human error. This led to the development of rudimentary automated clamping systems that were controlled by early computer systems. These initial CNC clamping systems, although relatively basic, provided a starting point for further advancements.
As computer technology progressed, so did CNC clamping capabilities. In the 1970s, the introduction of microprocessors facilitated the development of more sophisticated CNC clamping systems. These systems offered enhanced control and accuracy, enabling manufacturers to improve productivity and reduce errors. However, these early CNC clamping systems were limited in terms of adaptability and versatility.
In the 1980s, advancements in sensor technology and the integration of pneumatic and hydraulic systems into CNC clamping brought about significant improvements. These developments allowed for dynamic clamping, where the clamping force could be adjusted based on real-time machining conditions. This innovation revolutionized the manufacturing industry, as it contributed to the increased efficiency and precision of machining operations.
The 1990s witnessed further innovation in CNC clamping with the introduction of electro-mechanical clamping systems. These systems utilized electrically controlled actuators instead of traditional pneumatic or hydraulic systems. Electro-mechanical clamping provided greater control, eliminated the need for external fluid sources, and reduced energy consumption.
In recent years, CNC clamping systems have become increasingly intelligent and integrated into overall manufacturing processes. The incorporation of advanced sensors, actuators, and software has allowed for real-time monitoring and adjustment of clamping forces, based on parameters such as material properties and machining conditions. Furthermore, the utilization of wireless communication and Internet of Things (IoT) technologies has enabled remote monitoring and control of CNC clamping systems, even from mobile devices.
Overall, the evolution of CNC clamping has progressed from rudimentary automated systems to sophisticated and intelligent setups. Each stage of development has contributed to improved efficiency, accuracy, adaptability, and ease of use. As technology continues to advance, the future of CNC clamping holds the promise of further enhancements, potentially incorporating artificial intelligence and machine learning to optimize clamping actions based on complex data analysis.
The Evolution and Market Trends in cnc clamping Industry
The CNC clamping industry has undergone significant evolution and witnessed several market trends in recent years. CNC clamping refers to the process of securely holding a workpiece or tool in place during CNC machining operations. It is a crucial aspect of CNC machining, ensuring accuracy, stability, and efficiency in manufacturing processes.
One of the notable evolution in the CNC clamping industry is the advancements in clamping technology. Manufacturers have introduced innovative clamping solutions that offer improved performance and flexibility. These advancements include the development of quick-change clamping systems, hydraulic and pneumatic clamping devices, and modular fixture systems. Such technological advancements have revolutionized CNC clamping, enabling faster setup times, increased productivity, and reduced downtime.
Another evolution in the CNC clamping industry is the integration of automation and smart features. With the rise of Industry 4.0, CNC clamping systems have become more intelligent and interconnected. Automated clamping systems can now communicate with CNC machines, adapting to different workpieces and adjusting clamping forces accordingly. This integration has streamlined production processes, minimized human errors, and enhanced overall efficiency.
In terms of market trends, there is a growing demand for customizable and versatile clamping solutions. Manufacturers require clamping systems that can accommodate a wide range of workpiece sizes, shapes, and materials. Consequently, the market has witnessed an increase in the development of modular clamping systems, adjustable fixtures, and universal clamps. These solutions provide manufacturers with the flexibility to adapt to changing production demands quickly.
Additionally, sustainability and eco-friendly practices have become important considerations in the CNC clamping industry. Manufacturers are increasingly adopting clamping systems that minimize material waste, reduce energy consumption, and promote sustainable machining practices. This trend aligns with the global focus on environmental sustainability and the circular economy.
In summary, the CNC clamping industry has evolved significantly in recent years, driven by technological advancements and the changing needs of manufacturers. The integration of automation, customization, and sustainability has shaped the market trends, leading to the development of more efficient and eco-friendly clamping solutions. As the manufacturing sector continues to evolve, it is expected that the CNC clamping industry will further innovate to meet the demands of the industry.
Custom Private Labeling and Branding Opportunities with Chinese cnc clamping Manufacturers
There are significant custom private labeling and branding opportunities available with Chinese CNC clamping manufacturers. With their expertise in manufacturing high-quality CNC clamping products, businesses can capitalize on private labeling to establish their brand identity and increase brand recognition.
Private labeling allows businesses to display their own brand name, logo, and design on the CNC clamping products manufactured by Chinese suppliers. This creates a cohesive and professional look for the products, enhancing their market appeal and distinguishing them from generic alternatives.
Additionally, private labeling provides businesses with the opportunity to build brand loyalty among their customers. By consistently offering reliable, high-quality CNC clamping products under their own brand name, businesses can foster trust and customer satisfaction, resulting in repeat business and positive brand associations.
Chinese manufacturers specializing in CNC clamping products often offer customization options, enabling businesses to tailor the products to their specific requirements. This customization can include aspects such as color, size, materials, and additional features, further enhancing the branding opportunities available.
Partnering with Chinese manufacturers for custom private labeling and branding also brings cost-effectiveness to businesses. Manufacturers in China generally have access to advanced technology and economies of scale, allowing for competitive pricing without compromising on product quality.
It is essential for businesses to conduct thorough research when identifying potential Chinese manufacturers for custom private labeling and branding. Assessing their manufacturing capabilities, quality control processes, reputation, and previous client collaborations are critical steps to ensure a successful partnership.
Maximizing custom private labeling and branding opportunities with Chinese CNC clamping manufacturers can help businesses establish a strong market presence, increase customer loyalty, and ultimately drive growth and profitability.
Tips for Procurement and Considerations when Purchasing cnc clamping
1. Identify the specific requirements: Before purchasing CNC clamping, it is important to clearly define the specific requirements of your project. Consider the type of material you will be working with, the size and shape of the parts, and the required precision levels. This will help you choose the right type of clamping system that can meet your needs effectively.
2. Research different clamping options: There are various types of CNC clamping systems available in the market, such as manual, hydraulic, pneumatic, and magnetic clamps. Each type has its own advantages and limitations. Research and compare different options to understand their features, benefits, and compatibility with your CNC machine.
3. Consider adaptability and compatibility: Ensure that the selected clamping system is compatible with your CNC machine and can be easily integrated into your existing setup. Additionally, consider its adaptability to handle different parts and workpieces. A versatile clamping system that allows for easy adjustment and reconfiguration can enhance the efficiency and productivity of your CNC operations.
4. Look for quality and durability: CNC clamping systems undergo extensive usage and load-bearing, making it crucial to invest in high-quality and durable clamping solutions. Check for the material and construction quality of the clamping system to ensure its longevity and reliability. Look for reputable manufacturers or suppliers with a proven track record of providing reliable and durable clamping systems.
5. Consider ease of use and maintenance: Look for a clamping system that offers ease of use and requires minimal maintenance. Consider features such as quick and easy setup, adjustable clamping pressures, and user-friendly controls. Additionally, check if the clamping system requires frequent lubrication or replacement parts and weigh those requirements against your operational needs and resources.
6. Evaluate cost-effectiveness: Price is an important consideration when purchasing CNC clamping systems, but it should not be the sole determining factor. While it is essential to ensure that the clamping system falls within your budget, also consider the long-term benefits and return on investment. A slightly higher upfront cost for a superior clamping system can often result in reduced downtime, increased productivity, and lower maintenance costs over time.
7. Seek expert advice and recommendations: If you are unsure about the best clamping system for your specific requirements, consider seeking expert advice from manufacturers, suppliers, or experienced CNC operators. They can provide valuable insights and recommendations based on their industry knowledge and experience.
In summary, when purchasing CNC clamping, it is important to identify specific requirements, research different options, consider adaptability and compatibility, prioritize quality and durability, evaluate ease of use and maintenance, assess cost-effectiveness, and seek expert advice. Following these considerations will help you select the most suitable clamping system for your CNC operations and maximize efficiency and productivity.
FAQs on Sourcing and Manufacturing cnc clamping in China
1. What is CNC clamping?
CNC clamping refers to the process of tightly securing a workpiece on a CNC (Computer Numerical Control) machine to ensure stability and precision during machining operations. It involves the use of specialized clamps or fixtures to hold the workpiece firmly in place.
2. Why source CNC clamping from China?
China has emerged as a global manufacturing powerhouse, offering competitive prices, a wide range of options, and reliable quality in various industries. Sourcing CNC clamping from China can be cost-effective for businesses looking to optimize their manufacturing processes and reduce production costs.
3. How to select a reliable supplier in China?
When sourcing CNC clamping from China, it is crucial to choose a reliable supplier. Consider the supplier’s experience, reputation, and certifications in the industry. Verify their manufacturing capabilities, machinery, and quality control processes. Request samples or visit their facilities if possible to assess their capabilities firsthand.
4. What are the common materials used for CNC clamping?
CNC clamping components are typically made from high-quality materials such as steel, aluminum, or stainless steel. The choice of material depends on the specific requirements of the application, including factors such as strength, durability, and resistance to wear or corrosion.
5. Can I customize CNC clamping designs in China?
Yes, most Chinese CNC clamping manufacturers offer customization options. They can work with customers to design and produce CNC clamping solutions tailored to their specific needs and requirements. Customization may include variations in size, shape, grip, or other functional specifications.
6. How to ensure quality control in CNC clamping manufacturing?
To ensure quality control, it is recommended to partner with manufacturers that have implemented robust quality management systems, such as ISO 9001 certification. Regular audits, inspections, and testing should be part of the manufacturing process. Requesting quality documentation and samples before finalizing a purchase can also help in assessing the quality of CNC clamping products.
7. What is the typical lead time for CNC clamping production in China?
Lead times can vary depending on several factors, including the complexity of the design, order quantity, and the manufacturer’s production capacity. In general, lead times for CNC clamping production in China can range from a few weeks to a few months. It is crucial to discuss lead times with potential suppliers and factor them into production planning.
8. What are the shipping and logistics considerations?
When sourcing CNC clamping from China, consider transportation logistics such as shipping methods, packaging requirements, and import/export regulations. Coordinate with suppliers to ensure timely delivery and discuss shipping options, including air freight, sea freight, or other modes of transportation based on your requirements and budget.
In summary, sourcing CNC clamping from China offers various advantages, such as cost-effectiveness and a wide range of manufacturing options. Selecting a reliable supplier, focusing on quality control, and addressing logistics considerations are essential for a successful sourcing process.
Why contact sourcifychina.com get free quota from reliable cnc clamping suppliers?
Sourcifychina.com is likely to offer free quota from reliable CNC clamping suppliers for various reasons.
Firstly, Sourcifychina.com acts as a sourcing platform that connects businesses with manufacturers and suppliers in China. They aim to provide a hassle-free and efficient sourcing experience for their users. By offering a free quota from reliable CNC clamping suppliers, Sourcifychina.com attracts more potential buyers to utilize their platform and services.
Secondly, CNC clamping is a critical component in the manufacturing and machining industry. It ensures the stability and accuracy of CNC machines during the production process. Hence, reliable and high-quality CNC clamping suppliers are in high demand. By providing a free quota, Sourcifychina.com enables buyers to assess and understand the costs and capabilities of different suppliers before making a purchase decision. This helps businesses to make informed choices and select the most suitable supplier based on their requirements.
Additionally, offering a free quota allows Sourcifychina.com to showcase their network of reliable suppliers. It demonstrates their commitment to sourcing products from trusted manufacturers, which builds trust and credibility among potential buyers. This can lead to long-term partnerships and repeated business transactions.
Moreover, by providing a free quota, Sourcifychina.com encourages businesses to utilize their platform to source CNC clamping suppliers. This not only promotes their own services but also benefits the suppliers listed on their platform. Increased visibility and opportunities for business collaborations can help suppliers expand their market reach and gain new customers.
In summary, offering a free quota from reliable CNC clamping suppliers is a strategy employed by Sourcifychina.com to attract more buyers to their sourcing platform. It allows businesses to evaluate different suppliers, showcases the reliability of the suppliers, and promotes long-term partnerships between buyers and suppliers.