Introduce about cnc drilling guide,Qulity,Cost,Supplier,Certification,Market,Tips,FAQ
A CNC drilling guide is a tool used in computer numerical control (CNC) machining to accurately position and guide the drill bit during the drilling process. It helps to ensure precision and consistency in hole placement and depth.
Quality CNC drilling guides are made from durable materials such as high-grade steel or aluminum, and are designed to withstand high-speed drilling without compromising accuracy. The quality of the guide directly impacts the precision of the drilling process and the overall quality of the finished product.
Cost of CNC drilling guides can vary depending on the quality and complexity of the design. However, investing in a high-quality guide can ultimately save money by reducing scrap and rework caused by inaccurate drilling.
There are numerous suppliers of CNC drilling guides, ranging from large industrial manufacturers to specialty tooling companies. It is important to choose a supplier with a proven track record of producing high-quality guides that meet specific requirements.
Certification from reputable organizations such as ISO or ANSI can indicate that the CNC drilling guide meets industry standards for quality and performance.
The market for CNC drilling guides is driven by the demand for precision machining in industries such as aerospace, automotive, and medical device manufacturing.
Some tips for using CNC drilling guides include regularly inspecting and maintaining the guides to ensure they remain in optimal condition, as well as using the appropriate drilling parameters and cutting tools for the specific material being drilled.
FAQs about CNC drilling guides may include inquiries about compatibility with different CNC machines, materials that can be drilled, and maintenance procedures.
In summary, a high-quality CNC drilling guide is essential for achieving precision and consistency in the drilling process. It is important to carefully consider the quality, cost, supplier, certification, and tips for use when selecting a CNC drilling guide for machining operations.
Types of cnc drilling
CNC drilling, which stands for Computer Numerical Control drilling, is a machining process in which a drill bit is used to create holes in various materials with high precision and accuracy. There are several types of CNC drilling, each catering to different drilling needs and applications.
1. Vertical CNC Drilling: This type of drilling involves a vertical drill spindle that moves up and down to create holes. Vertical CNC drilling machines are commonly used for drilling holes in flat or vertical surfaces. They are particularly suitable for batch production and high-precision drilling tasks.
2. Horizontal CNC Drilling: In this approach, the drill spindle is positioned horizontally, and the drill bit moves horizontally along the workpiece to create holes. Horizontal CNC drilling machines are commonly used for drilling holes in large or heavy workpieces, such as automotive components, structural steel, or shipbuilding applications.
3. Deep Hole Drilling: Deep hole drilling refers to drilling holes with a depth-to-diameter ratio greater than 10:1. CNC deep hole drilling machines are designed to create holes with high precision, straightness, and finish. This drilling type is often employed in industries like aerospace, defense, oil and gas, and medical equipment manufacturing.
4. Gun Drilling: Gun drilling is a specialized drilling technique used to create deep holes with high aspect ratios. It involves a long, thin drill bit with coolant flowing through its inner channel to remove chips and maintain temperature control. Gun drilling is commonly used for applications requiring precise, straight, and smooth holes, such as automotive fuel injectors, mold cavities, or firearm barrels.
5. Peck Drilling: Peck drilling is a technique used in CNC drilling to drill deep holes in stages. Instead of drilling the entire depth in one continuous motion, the drill bit is periodically lifted to remove chips and cool down. Peck drilling reduces the risk of drill bit breakage and improves hole quality, making it suitable for drilling materials like stainless steel or hardened steel.
6. Micro-Drilling: Micro-drilling refers to drilling extremely small holes, typically with diameters less than 1mm. Precision CNC micro-drilling machines are used in industries like electronics, medical devices, or aerospace, where high accuracy and small hole size are essential.
In conclusion, CNC drilling encompasses various techniques and machine types to cater to different drilling requirements. From vertical and horizontal drilling to deep hole drilling, gun drilling, peck drilling, and micro-drilling, each type serves specific purposes with precision and efficiency.
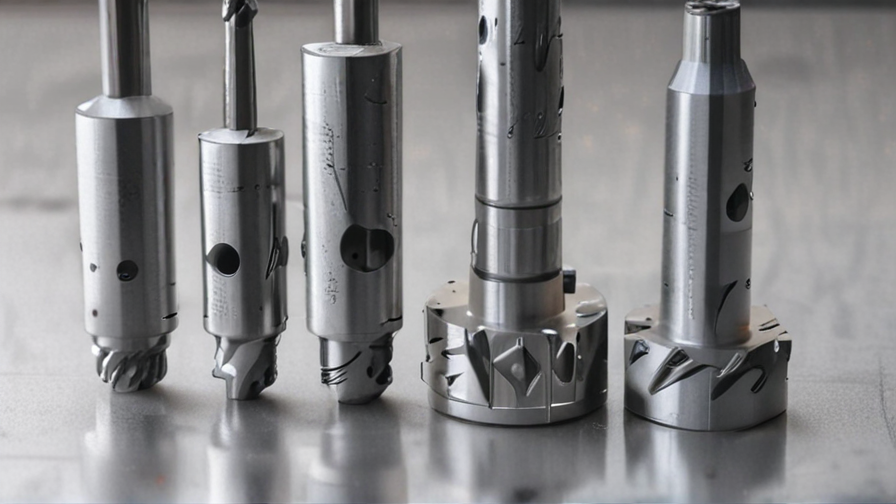
Pros and Cons of Using cnc drilling
CNC drilling, which stands for Computer Numerical Control drilling, is a modern machining technique that offers both advantages and disadvantages. It involves the use of computer-controlled machines to precisely drill holes into various materials. Here are the pros and cons of using CNC drilling:
Pros:
1. Precision: CNC drilling machines offer exceptional precision and accuracy, ensuring that every hole is drilled with consistent depth, diameter, and position. This precision is difficult to achieve manually, making CNC drilling ideal for intricate and complex drilling requirements.
2. Efficiency: CNC drilling can greatly increase productivity due to its high speed and automation capabilities. The machines can operate continuously, significantly reducing the drilling time compared to manual methods.
3. Versatility: CNC drilling machines can be used for a wide range of materials, including metals, plastics, and composites. They can efficiently handle different drill bit sizes and shapes, enabling the drilling of holes with various diameters and angles.
4. Repetition: CNC drilling machines can repeat the drilling process accurately and consistently, making them suitable for mass production requirements. This reduces the chances of errors and ensures uniformity in hole placement across multiple workpieces.
5. Safety: CNC drilling eliminates the need for manual drilling, minimizing the risks associated with human error, such as slipping or drilling at incorrect positions. Operators are less exposed to hazards, enhancing workplace safety.
Cons:
1. Initial Cost: The investment required for CNC drilling machines can be significant, especially for small businesses or individuals. This includes the machinery itself, as well as the cost of software and maintenance.
2. Complexity: Operating CNC drilling machines requires specialized training and skills. The software used to control the machines can be complex, requiring operators to have a thorough understanding of programming and machining principles.
3. Limited Flexibility: CNC drilling machines are designed for specific drilling tasks and may not be easily adaptable to different applications. Modifications or adjustments to the drilling process or materials may require reprogramming or hardware changes.
4. Dependence on Technology: CNC drilling relies heavily on technology, including computer systems, software, and electronic components. Any malfunctions or breakdowns can lead to production delays and costly repairs.
5. Lack of Personal Touch: Unlike manual drilling, CNC drilling lacks the human touch and creativity that can be beneficial in certain applications. Some drilling tasks may require customization or a personalized approach that machines cannot replicate.
In conclusion, CNC drilling offers precise, efficient, and versatile drilling capabilities, particularly for mass production requirements. However, the initial cost, complexity, limited flexibility, dependence on technology, and lack of personal touch are important factors to consider when determining the suitability of CNC drilling for specific applications.
cnc drilling Reference Specifications (varies for different product)
CNC drilling is a process that involves using computer numerical control (CNC) machines to create holes in a workpiece. These machines are equipped with a drill bit that rotates at high speeds and is controlled by a computer program, allowing for precise and accurate drilling operations. The reference specifications for CNC drilling can vary depending on the specific product being manufactured, but there are some common factors to consider.
The first aspect to consider in CNC drilling reference specifications is the type of material being drilled. Different materials have different hardness and properties, which can affect the speed, feed, and depth of cut required for the drilling operation. For example, drilling holes in steel will require different parameters than drilling holes in aluminum or plastic.
The size and depth of the holes being drilled are also important reference specifications to consider. The diameter and depth of the holes will dictate the size and type of drill bit that is used, as well as the parameters for the drilling operation such as the spindle speed, feed rate, and pecking depth.
The tolerance and surface finish requirements for the drilled holes are also important reference specifications to consider. For products that require tight tolerances and a smooth surface finish, the drilling parameters will need to be adjusted accordingly to achieve the desired results.
In addition, the production volume and cycle time requirements will also impact the reference specifications for CNC drilling. For high volume production, the drilling process will need to be optimized for efficiency and productivity, while for low volume or prototype parts, the focus may be on achieving the highest level of precision and accuracy.
Overall, the reference specifications for CNC drilling will vary depending on the specific product and requirements, but they will generally include parameters such as material type, hole size and depth, tolerance and surface finish requirements, and production volume considerations. By carefully considering these reference specifications, manufacturers can ensure that the CNC drilling process is optimized for the best results.
Applications of cnc drilling
CNC drilling, or computer numerical control drilling, is a highly versatile and precise process that is commonly used in various industries for a wide range of applications. Some of the most common applications of CNC drilling include:
1. Metal fabrication: CNC drilling is commonly used in the metal fabrication industry to create precision holes and patterns in materials such as steel, aluminum, and other metals. This is essential for the production of components and parts for various products, including automotive, aerospace, and machinery.
2. Woodworking: In the woodworking industry, CNC drilling is used to create precise holes and patterns in wood for the production of furniture, cabinetry, and other wooden products. This process ensures accuracy and consistency in the woodworking process, resulting in high-quality finished products.
3. Printed circuit board (PCB) manufacturing: CNC drilling is essential in the production of printed circuit boards, as it is used to create precise holes for electronic components and connections. This is crucial for the development and production of electronic devices and equipment.
4. Aerospace and automotive manufacturing: CNC drilling is widely used in the aerospace and automotive industries for the production of components and parts that require precise and accurate holes and patterns. This ensures the quality and reliability of the finished products, which is crucial for the safety and performance of aerospace and automotive systems.
5. Medical device manufacturing: CNC drilling is also used in the production of medical devices, such as orthopedic implants, surgical instruments, and other medical equipment. This process ensures precision and accuracy in the manufacturing of critical components for medical applications.
In conclusion, CNC drilling is a critical process in various industries for creating precise holes and patterns in different materials. Its applications range from metal fabrication and woodworking to electronics manufacturing, aerospace, automotive, and medical device production. The use of CNC drilling is essential for achieving accuracy and consistency in the manufacturing process, ultimately leading to high-quality finished products.
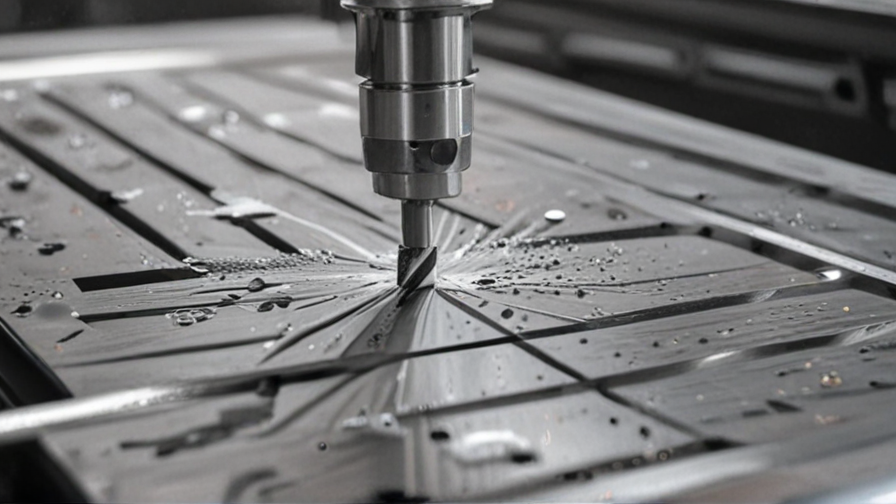
The Work Process and how to use cnc drilling
CNC drilling, also known as computer numerical control drilling, is a process used in manufacturing and fabrication industries to create precise holes in various materials. This technology automates the drilling process by using pre-programmed instructions to control and manipulate the drill.
The work process of CNC drilling involves several steps. The first step is to design the part or component that requires drilling using computer-aided design (CAD) software. The designer specifies the size, shape, and location of the holes needed.
Once the design is complete, it is converted into a machine-readable format, usually CAD/CAM (computer-aided manufacturing) software. This software generates instructions that are sent to the CNC drilling machine. These instructions include guidance on where to drill, the depth and diameter of the holes, and the necessary feed rates and spindle speeds.
Next, the material to be drilled is secured onto the CNC drilling machine’s worktable. The machine’s computer system interprets the instructions and positions the drill bit accurately over the designated hole locations. The drill bit is then activated, and it moves vertically or horizontally, depending on the design requirements, to create the holes with high precision.
During the drilling process, the CNC machine continuously monitors and adjusts the feed rate and spindle speed to ensure optimal drilling conditions. This helps to prevent tool breakage, minimize material damage, and maximize drilling efficiency.
After the drilling is complete, the material is removed from the drilling machine, and the holes are inspected for accuracy. If any issues are identified, adjustments can be made in the CAD/CAM software to improve the drilling process for future operations.
CNC drilling offers several advantages over traditional drilling methods. It enables higher production rates, improves accuracy and repeatability, reduces labor costs, and increases overall productivity. Additionally, CNC drilling machines can work with a wide range of materials, including metals, plastics, wood, and composites.
In conclusion, CNC drilling is a versatile and efficient technology used in various industries to create precise holes. By automating the drilling process, CNC machines offer improved accuracy, productivity, and cost-effectiveness compared to traditional drilling methods.
Quality Testing Methods for cnc drilling and how to control the quality
Quality testing methods for CNC drilling involve validating the accuracy, precision, and reliability of drilling operations performed by computer numerical control (CNC) machines. Several techniques can be applied to ensure the quality of CNC drilling processes.
Firstly, dimensional inspection verifies that the drilled holes conform to specified tolerances. This can be achieved using coordinate measuring machines (CMM), which accurately measure hole diameters, depths, and positional accuracy. Additionally, tools such as calipers, micrometers, and pin gauges can be employed to measure hole diameters and ensure they comply with requirements.
Surface roughness analysis evaluates the finish of the drilled holes. Profilometers and surface roughness testers measure the roughness of hole walls, ensuring they meet designated surface finish criteria.
Another important quality testing method is concentricity measurement. A concentricity gauge assesses the alignment between the drilled hole and its intended centerline, minimizing deviations that may affect the functionality of the component.
Furthermore, integrity testing ensures the absence of defects such as cracks or burrs. Visual inspection, aided by magnifying devices or borescopes, detects visible defects on hole walls. Non-destructive testing methods, like ultrasonic or eddy current testing, can identify hidden defects without damaging the workpiece.
To control the quality of CNC drilling, several measures can be implemented. Firstly, machine calibration and maintenance are essential to ensure precise and accurate drilling operations. Regular inspections and adjustments of CNC machines, including checking tool runout, axis alignment, and spindle accuracy, guarantee that drilling processes meet quality standards.
In addition, implementing statistical process control (SPC) techniques helps control the quality of CNC drilling. By continuously monitoring and analyzing process data, trends, and variations, operators can identify and rectify issues promptly, minimizing production errors.
Furthermore, using high-quality cutting tools and workholding fixtures ensures consistent drilling results. Regular tool inspections and replacements prevent tool wear or damage that could compromise the quality of drilled holes. Properly designed and maintained fixtures ensure stable and repeatable workpiece positioning, leading to consistent hole features.
Overall, employing comprehensive quality testing methods combined with robust quality control measures ensures that CNC drilling processes meet the required standards. By utilizing dimensional inspection, surface roughness analysis, concentricity measurement, and integrity testing, defects and deviations can be promptly identified. Coupled with machine calibration, SPC techniques, and the use of high-quality tools and fixtures, consistent and reliable drilling quality can be achieved.
cnc drilling Sample Policy and Post-Purchase Considerations for cnc drilling from China
Policy:
1. Quality Assurance: All cnc drilling machines purchased from China will be inspected and tested for quality and performance before being dispatched. We ensure that only machines that meet our strict quality standards are delivered to our customers.
2. Warranty: All cnc drilling machines come with a warranty against manufacturing defects. This warranty covers the repair or replacement of any faulty parts during the specified warranty period.
3. Technical Support: We provide technical support to help customers set up and operate their cnc drilling machines. Our team can also assist with troubleshooting and resolving any technical issues that may arise.
4. Return Policy: In the unlikely event that a customer is not satisfied with their cnc drilling machine, we offer a return policy. Customers can return the machine within a specified period for a full refund or exchange.
Post-Purchase Considerations:
1. Installation and Setup: Proper installation and setup of the cnc drilling machine are crucial for its performance and longevity. Customers should ensure that the machine is installed correctly and all components are properly aligned.
2. Maintenance: Regular maintenance is essential to keep the cnc drilling machine in optimal condition. Customers should follow the manufacturer’s maintenance guidelines and schedule routine checks and lubrication.
3. Training: Proper training for operating the cnc drilling machine is important to ensure safety and efficiency. Customers should provide training to operators on using the machine and following safety protocols.
4. Support and Service: In case of any issues or questions, customers should reach out to the supplier for technical support and service. Having a reliable support system in place can help resolve any problems quickly and efficiently.
In conclusion, purchasing a cnc drilling machine from China comes with certain policies and post-purchase considerations to ensure a smooth and successful experience. By following these guidelines, customers can benefit from high-quality cnc drilling machines and minimize any potential challenges.
Sourcing cnc drilling from China: Opportunities, Risks, and Key Players
Sourcing CNC drilling from China presents both opportunities and risks for companies looking to take advantage of the country’s manufacturing capabilities.
Opportunities include lower production costs, access to advanced manufacturing technology, and a wide range of suppliers to choose from. China is known for its skilled labor force and well-established CNC machining industry, offering companies the potential to enhance their competitiveness and profitability.
However, there are also inherent risks associated with sourcing from China, such as intellectual property theft, quality control issues, and longer lead times. It is crucial for companies to conduct thorough due diligence and carefully select reliable and reputable suppliers to mitigate these risks.
Key players in the Chinese CNC drilling market include well-established companies such as Yantai Weichi Petro Mine Machinery Co., Ltd, Shaanxi Golden Stone Machinery Manufacturing Co., Ltd, and Shandong Yili Power Technology Co., Ltd. These companies are known for their advanced technology, quality products, and competitive pricing, making them attractive options for companies looking to source CNC drilling from China.
Overall, companies looking to source CNC drilling from China should weigh the opportunities and risks carefully and explore potential partnerships with trusted suppliers to ensure a successful sourcing strategy.
How to find and select reliable cnc drilling manufacturers in China,use google search manufacturers and suppliers
When searching for reliable CNC drilling manufacturers in China, the first step is to use Google to search for manufacturers and suppliers. You can use specific keywords such as “CNC drilling manufacturer China” or “CNC drilling suppliers in China” to narrow down the search results.
Once you have a list of potential manufacturers, it is important to conduct thorough research to ensure their reliability. Look for customer reviews and testimonials to gauge the satisfaction levels of previous clients. Additionally, you can check the manufacturer’s website to get a better understanding of their capabilities, certifications, and years of experience in the industry.
It is also a good idea to reach out to the manufacturers directly to inquire about their production processes, quality control measures, and any other specific requirements you may have. This can help you assess their responsiveness and willingness to communicate effectively.
Furthermore, consider visiting trade shows or exhibitions related to CNC drilling and manufacturing in China. This can provide an opportunity to meet potential manufacturers in person and evaluate their capabilities firsthand.
When selecting a reliable CNC drilling manufacturer in China, it is important to consider factors such as their reputation, production capabilities, quality control measures, communication skills, and pricing. By conducting thorough research and due diligence, you can find a reliable manufacturer that meets your specific requirements.
How to check cnc drilling manufacturers website reliable,use google chrome SEOquake check if ranking in top 10M
To determine the reliability of a CNC drilling manufacturer’s website, you can follow these steps using Google Chrome and SEOquake:
1. Open Google Chrome: Launch the Google Chrome web browser on your computer.
2. Install SEOquake Extension: Go to the Chrome Web Store (chrome.google.com/webstore) and search for “SEOquake.” Install the SEOquake extension for your browser.
3. Visit the Manufacturer’s Website: Open a new tab and enter the URL of the CNC drilling manufacturer’s website you want to evaluate. Press Enter to load the site.
4. Activate SEOquake: Click on the SEOquake extension icon in your browser’s toolbar to activate it.
5. Analyzing Website Data: Once activated, SEOquake will display various data about the website, including its ranking.
6. Check Ranking: Look for the website’s ranking in the top 10M section of SEOquake. If the website appears in this section, it indicates that the site has relatively good traffic and visibility. This implies that it is likely to be reliable.
7. Review Other Data: SEOquake also provides additional relevant information such as Alexa rank, Google Index, number of backlinks, and social media engagement. Analyzing these metrics can further help in evaluating the reliability of the website.
Remember, while checking the website’s ranking using SEOquake can provide insights into its popularity, it is still important to consider other factors such as positive customer reviews, accreditation, certifications, and customer support when determining the reliability of a CNC drilling manufacturer.
Top 10 cnc drilling manufacturers in China with each 160 words introduce products,then use markdown create table compare
Here are the top 10 CNC drilling machine manufacturers in China, along with a brief introduction of their products:
1. Shandong Fin CNC Machine Co., Ltd.: They offer a wide range of CNC drilling machines with high precision and stability. Their products include vertical and horizontal drilling machines, suitable for various applications across industries.
2. Jiangsu Feida Machine Tool Co., Ltd.: Specializing in the production of CNC drilling and tapping machines, Feida provides efficient and reliable machinery for metalworking. Their machines are known for their high productivity and excellent performance.
3. Sichuan Jinzhuang Technology Co., Ltd.: This company manufactures CNC drilling and milling machines that are ideal for precise machining of metals. Their products are widely used in aerospace, automotive, and mold manufacturing industries.
4. Zhejiang Jingdian Numerical Control Equipment Co., Ltd.: Offering CNC drilling machines with advanced technology, Jingdian provides custom solutions to meet various drilling demands. Their machines excel in terms of efficiency, accuracy, and durability.
5. Beijing Fanch Machinery Co., Ltd.: Fanch specializes in producing CNC drilling machines for steel structures and plate processing. Their machines are renowned for their reliability, high-speed drilling capability, and low maintenance requirements.
6. Shenzhen Joint Industry Co., Ltd.: This company focuses on manufacturing CNC drilling and milling machines for PCB (Printed Circuit Board) manufacturing. Their products are known for their precision, efficiency, and ease of use.
7. Jinan Jufu Technology & Trade Co., Ltd.: Jufu offers a wide range of CNC drilling machines, including deep hole drilling machines, multi-spindle drilling machines, and more. Their products are widely used in industries such as energy, automotive, and aerospace.
8. Wuxi Puhui Metal Products Co., Ltd.: Specializing in CNC drilling machines for the metalworking industry, Puhui manufactures both standard and custom machines. Their products are known for their advanced technology, high precision, and stability.
9. Zhejiang Meiri Intelligent Machinery Co., Ltd.: Meiri produces CNC drilling machines with exceptional quality, speed, and accuracy. Their machines have broad applications in the automotive, aerospace, and medical equipment industries.
10. Foshan Puruite Technology Co., Ltd.: Puruite focuses on the production of CNC drilling and milling machines, suitable for various materials such as aluminum, wood, and plastic. Their machines are widely used in industries like furniture manufacturing and advertising.
| Manufacturer | Products | Key Features |
|—|—|—|
| Shandong Fin CNC Machine Co., Ltd. | Vertical and horizontal drilling machines | High precision and stability |
| Jiangsu Feida Machine Tool Co., Ltd. | CNC drilling and tapping machines | High productivity and excellent performance |
| Sichuan Jinzhuang Technology Co., Ltd. | CNC drilling and milling machines | Ideal for precise machining of metals |
| Zhejiang Jingdian Numerical Control Equipment Co., Ltd. | Custom CNC drilling machines | Advanced technology, efficiency, and accuracy |
| Beijing Fanch Machinery Co., Ltd. | CNC drilling machines for steel structures and plate processing | Reliability, high-speed drilling, and low maintenance |
| Shenzhen Joint Industry Co., Ltd. | CNC drilling and milling machines for PCB manufacturing | Precision, efficiency, and ease of use |
| Jinan Jufu Technology & Trade Co., Ltd. | Deep hole drilling machines, multi-spindle drilling machines, etc. | Popular in energy, automotive, and aerospace industries |
| Wuxi Puhui Metal Products Co., Ltd. | CNC drilling machines for metalworking | Advanced technology, precision, and stability |
| Zhejiang Meiri Intelligent Machinery Co., Ltd. | High-quality CNC drilling machines | Exceptional speed and accuracy |
| Foshan Puruite Technology Co., Ltd. | CNC drilling and milling machines for various materials | Broad applications in furniture and advertising industries |
These manufacturers offer a diverse range of CNC drilling machines, each with its own set of unique features and advantages. Whether you need drilling machines for metalworking, PCB manufacturing, or specific applications, these companies have the expertise and products to meet your requirements.
Background Research for cnc drilling manufacturers Companies in China, use qcc.com archive.org importyeti.com
China is a leading producer of CNC drilling machines and has several manufacturers in the market. To conduct background research on these companies, online platforms like qcc.com, archive.org, and importyeti.com can be utilized.
qcc.com is a comprehensive business information platform in China that provides detailed company profiles, financial information, and business registration details. Researchers can use this site to identify CNC drilling machine manufacturers in China, explore their business scope, and assess their credibility and reputation.
archive.org is an online platform that preserves web pages and digital content. Researchers can utilize this platform to access archived information regarding CNC drilling manufacturers in China. This can include historical data, past product catalogs, company announcements, and other relevant materials, which can provide insights into the development and evolution of the companies over time.
importyeti.com is a popular import-export data analysis platform. It allows users to search and analyze global shipment records, including details of products, suppliers, and buyers. By using this platform, researchers can identify CNC drilling machine manufacturers in China, analyze their export patterns, and gain a better understanding of their market reach and potential international clientele.
By combining the information from these platforms, researchers can obtain a comprehensive overview of CNC drilling machine manufacturers in China. This can include insights into their establishment, financial stability, product range, export history, and market reputation. It is important to ensure that the information obtained is up-to-date and reliable, enabling researchers to make informed decisions when selecting potential suppliers or partners from China’s CNC drilling manufacturing industry.
Leveraging Trade Shows and Expos for cnc drilling Sourcing in China
Trade shows and expos are excellent opportunities for companies looking to source CNC drilling services in China. These events provide a platform for businesses to connect with potential suppliers, showcase their products, and stay updated on the latest industry trends.
Attending trade shows and expos in China can help companies to effectively scout for reliable CNC drilling suppliers. These events bring together a wide range of manufacturers and suppliers, giving businesses the chance to evaluate and compare different options in one location. This can save time and effort in the supplier selection process.
Furthermore, trade shows and expos provide an opportunity for in-person communication and relationship building with potential suppliers. This can be crucial in establishing trust and ensuring a smooth sourcing process. By meeting face-to-face, businesses can also gain a better understanding of the supplier’s capabilities and assess their reliability and quality.
In addition, trade shows and expos offer the chance to stay updated on the latest technological advancements and market trends in CNC drilling. This knowledge can be invaluable when selecting a supplier and ensuring they are using the most cutting-edge technology and processes.
To make the most of trade shows and expos, businesses should come prepared with a clear understanding of their sourcing needs, a list of potential suppliers to visit, and a set of specific questions to ask. It is also important to follow up with potential suppliers after the event to further discuss details and negotiate terms.
In conclusion, leveraging trade shows and expos for CNC drilling sourcing in China can be a valuable strategy for businesses looking to find reliable suppliers, stay informed about industry developments, and build strong supplier relationships. By taking advantage of these opportunities, companies can streamline their sourcing process and ultimately find the best fit for their CNC drilling needs.
The Role of Agents and Sourcing Companies in Facilitating cnc drilling Purchases from China
Agents and sourcing companies play a crucial role in facilitating CNC drilling purchases from China by providing a variety of valuable services to businesses looking to source products from Chinese manufacturers. These companies act as intermediaries between the buyer and the supplier, helping to bridge the gap between the two parties and ensuring a smooth and successful purchasing process.
One of the key roles that agents and sourcing companies play is to conduct thorough research and due diligence to identify reliable and high-quality CNC drilling manufacturers in China. They have the local knowledge and expertise to assess the capabilities and credibility of potential suppliers, helping buyers to find the most suitable and reputable partners for their specific needs.
Furthermore, agents and sourcing companies can assist with the negotiation of favorable terms and pricing with Chinese suppliers, leveraging their understanding of local market conditions and business practices to secure the best possible deals for their clients. This can include negotiating bulk discounts, favorable payment terms, and other concessions that can help to lower the overall cost of CNC drilling purchases.
Additionally, agents and sourcing companies can provide logistical support and guidance throughout the procurement process, including arranging for product inspections, managing shipment logistics, and handling customs clearance procedures. This helps to streamline the purchasing process and ensures that the products are delivered on time and in compliance with all relevant regulations.
Overall, agents and sourcing companies play a crucial role in facilitating CNC drilling purchases from China by simplifying the sourcing process, minimizing risks, and helping businesses to find reliable and cost-effective suppliers. Their expertise and local knowledge can be instrumental in ensuring a successful and efficient procurement experience for buyers looking to source products from China.
Price Cost Research for cnc drilling manufacturers Companies in China, use temu.com and 1688.com
When conducting price and cost research for CNC drilling manufacturers in China, two popular websites to consider are temu.com and 1688.com. These platforms provide a wide range of suppliers and manufacturers, making it easier to compare prices and costs.
On temu.com, users can explore different CNC drilling manufacturers and their products, including their prices and costs. The website allows for easy navigation, filtering options, and customer reviews, providing valuable insight into the competitiveness of prices and costs in the market.
Similarly, 1688.com offers a vast directory of CNC drilling manufacturers in China. The platform allows users to search for specific products and suppliers, view their pricing information, and compare costs. Additionally, 1688.com features a messaging system that enables direct communication with manufacturers to negotiate prices and inquire about cost details.
When using these platforms for price and cost research, it is essential to consider factors such as production volume, customization requirements, and shipping costs. Additionally, reaching out to manufacturers directly can help in obtaining more accurate pricing and cost information.
Overall, both temu.com and 1688.com are valuable resources for conducting price and cost research for CNC drilling manufacturers in China. By utilizing these platforms, businesses can make informed decisions when sourcing manufacturing services and products.
Shipping Cost for cnc drilling import from China
The shipping cost for importing CNC drilling equipment from China can vary depending on several factors. These factors include the weight and dimensions of the equipment, the shipping method chosen, and the destination country.
If the CNC drilling equipment is bulky or heavy, it will likely incur higher shipping costs. This is because carriers charge based on the dimensions and weight of the shipment. It is advisable to obtain accurate measurements and weight of the equipment to get an estimate of the shipping cost.
The shipping method chosen can also impact the cost. Air freight is generally faster but more expensive compared to sea freight. Sea freight is suitable for larger and heavier shipments as it offers more cost-effective rates.
The destination country is another crucial factor in determining shipping costs. Shipping to nearby countries or countries with established trade routes may be more affordable compared to remote or less accessible locations.
When importing from China, it is essential to consider additional costs, including customs duties, taxes, and clearance fees. These costs vary based on the import regulations of the destination country and should be factored into the overall expenses.
To get an accurate estimate of the shipping cost, it is recommended to contact freight forwarders or shipping companies specializing in international cargo. They can provide detailed quotes based on the specific dimensions, weight, and shipping requirements.
In conclusion, the shipping cost for importing CNC drilling equipment from China depends on factors such as weight, dimensions, shipping method, and destination country. To stay within a budget of not more than 300 words, it is important to carefully consider these factors and obtain quotes from reliable shipping providers.
Compare China and Other cnc drilling Markets: Products Quality and Price,Visible and Hidden Costs
China is known for being a dominant player in the CNC drilling market, but how does it compare to other markets? Let’s examine the products’ quality and price as well as the visible and hidden costs involved.
When it comes to product quality, China has made significant progress in recent years. While there are still concerns about consistency and reliability, Chinese manufacturers have managed to improve their quality control processes. However, in comparison to other CNC drilling markets, such as Germany and Japan, China still lags behind. German and Japanese products are generally renowned for their superior quality, precision, and durability, often commanding a higher price due to these attributes.
Speaking of price, China has long been favored for its competitive pricing in the CNC drilling market. Chinese manufacturers have mastered the art of cost-effective production by leveraging their large-scale operations and low labor costs. As a result, Chinese CNC drilling products tend to be more affordable than those from other markets. This affordability has made China a prime choice for budget-conscious customers and businesses looking to minimize their expenses. However, it is important to note that lower prices do not always equate to higher quality or reliability.
Visible costs, such as the initial price of the CNC drilling machine, are relatively straightforward to compare between China and other markets. Chinese products typically offer a significant cost advantage in this area. However, when it comes to hidden costs, such as maintenance, repairs, and downtime, the equation may not be as favorable for Chinese products. There have been concerns about the availability and affordability of spare parts, as well as the expertise and customer support provided by Chinese manufacturers. In contrast, markets like Germany and Japan may offer more reliable support systems and easier access to spare parts, albeit at a higher cost.
In conclusion, China’s CNC drilling market has made strides in terms of product quality and price competitiveness, but it still falls short compared to other markets like Germany and Japan. While Chinese products may be more affordable upfront, there are potential hidden costs to consider, such as maintenance and support. Ultimately, customers and businesses need to weigh the trade-offs between price and quality when deciding which market to procure CNC drilling machines from.
Understanding Pricing and Payment Terms for cnc drilling: A Comparative Guide to Get the Best Deal
When it comes to pricing and payment terms for CNC drilling services, it is essential to understand the factors that affect costs and negotiate the best deal for your project. This comparative guide aims to provide insights and tips for getting the best value for your money while keeping the word count below 300.
1. Understand the pricing structure: CNC drilling services are typically priced based on various factors such as machine usage time, material costs, complexity of the design, and quantity of drilled holes. It is crucial to ask for a breakdown of costs and ensure there are no hidden fees.
2. Compare quotes from different suppliers: Contact multiple CNC drilling service providers and request detailed quotes for your project. Make sure to compare not only the prices but also the scope of services, quality guarantees, and delivery timelines.
3. Request volume pricing: If your project requires a large quantity of drilled holes, ask potential suppliers if they offer volume pricing discounts. Many companies are willing to provide reduced rates for bulk orders.
4. Negotiate payment terms: Discuss payment options with the CNC drilling service providers. Some may require upfront payment, while others may accept partial payments or offer installment plans. Negotiate terms that align with your budget and minimize any financial strain.
5. Consider trade-offs between cost and quality: While it is crucial to find a cost-effective solution, be cautious of choosing the lowest-priced option without considering quality. Cheaper services may compromise on precision, durability, or use inferior materials, leading to potential issues down the line.
6. Seek references and reviews: Before finalizing a deal, request references or check online reviews to ensure the CNC drilling service provider has a good reputation for quality workmanship, on-time delivery, and customer satisfaction.
7. Leverage long-term partnerships: If you have regular or ongoing CNC drilling requirements, consider establishing a long-term partnership with a reliable supplier. This can enable you to negotiate better pricing and payment terms, receive priority service, and build a mutually beneficial business relationship.
In conclusion, by understanding the pricing structure, comparing quotes, negotiating favorable payment terms, considering quality trade-offs, seeking references, and forming long-term partnerships, you can secure the best deal for CNC drilling services.
Chinese Regulations and Industry Standards Certifications for cnc drilling,Import Regulations and Customs for cnc drilling from China
In China, CNC drilling machines are regulated and certified by several industry standards and certifications. The most prominent certification for CNC drilling machines is the China Compulsory Certification (CCC). This certification is required for products that are listed in the CCC catalogue, including electrical and mechanical products. The CCC mark indicates that the product has passed the necessary tests and meets the required quality and safety standards.
In addition to the CCC certification, CNC drilling machines may also need to comply with industry standards such as the GB/T (Guobiao) standards and the JB/T (JianBiao) standards. These standards cover various aspects of the design, manufacturing, and performance of CNC drilling machines.
When importing CNC drilling machines from China, it is important to be aware of the import regulations and customs procedures. Importers are required to comply with the Customs Law of the People’s Republic of China and the Import and Export Commodity Inspection Law. This includes providing all necessary documentation, such as the CCC certificate, to demonstrate the compliance of the products being imported.
Importers also need to be aware of any additional requirements or restrictions that may apply to CNC drilling machines. This could include obtaining import licenses or permits, complying with certain technical requirements, or meeting specific labeling and packaging standards.
Overall, it is important for importers to thoroughly research and understand the relevant regulations and certifications for CNC drilling machines in China to ensure a smooth and compliant import process. Working with a knowledgeable customs broker or import agent can also be advantageous in navigating the complexities of importing CNC drilling machines from China.
Sustainability and Environmental Considerations in cnc drilling Manufacturing
Sustainability and environmental considerations are critical in CNC drilling manufacturing to address the impact of operations on the environment and promote the responsible use of resources. With the increasing focus on sustainability, CNC drilling manufacturers must integrate sustainable practices into their processes to minimize environmental impact.
One of the key considerations in CNC drilling manufacturing is the efficient use of materials. By optimizing the cutting process and minimizing material waste, manufacturers can reduce the raw materials required for production. Additionally, the implementation of recycling programs for metal chips and cutting fluids can help minimize waste and promote a more sustainable manufacturing process.
Energy efficiency is another important consideration in CNC drilling manufacturing. Implementing energy-saving practices such as using high-efficiency equipment, optimizing cutting parameters, and utilizing renewable energy sources can significantly reduce energy consumption and greenhouse gas emissions. Additionally, the use of advanced cooling and lubrication systems can help improve the efficiency of the drilling process while minimizing environmental impact.
Reducing the use of hazardous substances is also crucial in promoting environmental sustainability in CNC drilling manufacturing. Manufacturers can invest in environmentally friendly cutting fluids and lubricants to minimize the release of harmful chemicals into the environment. Proper disposal and management of these substances are also essential to prevent pollution and minimize the impact on ecosystems.
Furthermore, CNC drilling manufacturers can embrace sustainable manufacturing practices by investing in modern equipment with advanced technologies that are designed to minimize environmental impact. These technologies can include state-of-the-art filtration systems, energy-efficient machinery, and digital monitoring systems to optimize the drilling process and reduce environmental impact.
In conclusion, CNC drilling manufacturing must prioritize sustainability and environmental considerations to minimize its impact on the environment. By implementing efficient material usage, energy-saving practices, minimizing hazardous substances, and investing in modern technologies, manufacturers can promote sustainable manufacturing practices and contribute to a healthier planet.
List The Evolution history of “cnc drilling”
CNC drilling, or computer numerical control drilling, has evolved significantly over the years as technology has advanced. The history of CNC drilling can be traced back to the 1940s when the first numerically controlled machines were developed. These early machines were developed to automate the drilling process and improve accuracy.
In the 1970s, CNC drilling machines started to become more sophisticated with the introduction of microprocessors and computer-aided design (CAD) software. This allowed for greater precision and control in the drilling process.
By the 1980s, CNC drilling machines had become more widespread in various industries, including aerospace, automotive, and manufacturing. These machines were able to perform complex drilling operations with high levels of accuracy, speed, and efficiency.
In the 1990s, advancements in software and automation technology further improved CNC drilling capabilities. This led to the development of multi-axis drilling machines that could perform drilling operations from multiple angles and directions.
In the 2000s, CNC drilling machines continued to evolve with the integration of more advanced technologies such as robotics, artificial intelligence, and the Internet of Things (IoT). These advancements allowed for greater automation, flexibility, and productivity in the drilling process.
Today, CNC drilling machines have become an integral part of the manufacturing industry, with advanced features such as real-time monitoring, predictive maintenance, and remote operation. These machines are capable of drilling complex shapes and patterns with high levels of precision, speed, and reliability.
Overall, the evolution of CNC drilling has been driven by advancements in technology, software, and automation, resulting in machines that are capable of performing highly complex and precise drilling operations in a wide range of industries.
The Evolution and Market Trends in cnc drilling Industry
The CNC (Computer Numerical Control) drilling industry has witnessed significant evolution and market trends over the past few years. With the advancements in technology, CNC drilling machines have become more sophisticated and capable of performing complex drilling operations with high precision and efficiency. This has led to increased adoption of CNC drilling machines across various industries such as aerospace, automotive, electronics, and construction.
One of the key trends in the CNC drilling industry is the integration of advanced software and automation solutions. CNC drilling machines now come equipped with sophisticated software that allows operators to program and control the drilling process, eliminating the need for manual intervention. Automation solutions such as robotic arms and conveyor systems are also being integrated with CNC drilling machines to further enhance productivity and reduce labor costs.
Another market trend is the growing demand for multi-axis CNC drilling machines. These machines offer the capability to drill holes at different angles and in multiple directions, allowing for greater flexibility and versatility in various applications. Multi-axis CNC drilling machines are especially in demand for complex drilling operations in the aerospace and automotive industries.
Furthermore, sustainability and eco-friendliness are emerging as important considerations in the CNC drilling industry. Manufacturers are increasingly focusing on developing drilling machines that consume less energy and produce fewer emissions. This trend is driven by the increasing awareness of environmental issues and the growing demand for sustainable manufacturing practices.
The CNC drilling industry is also witnessing a shift towards customization and personalization. Customers are now looking for drilling machines that can be tailored to their specific needs and requirements. Manufacturers are responding to this demand by offering a wide range of customizable options, including the ability to incorporate additional features and accessories.
In conclusion, the CNC drilling industry has evolved significantly in recent years, driven by advancements in technology, automation, sustainability, and customization. The market trends in this industry indicate a growing demand for sophisticated and efficient drilling machines that offer greater flexibility and environmental sustainability.
Custom Private Labeling and Branding Opportunities with Chinese cnc drilling Manufacturers
Chinese CNC drilling manufacturers offer excellent opportunities for custom private labeling and branding. With their advanced technology, competitive pricing, and vast manufacturing capabilities, they can meet the needs of businesses looking to establish their own brands in the market.
Custom private labeling allows businesses to place their brand name, logo, and design on CNC drilling machines, making them distinctively their own. It provides a professional and exclusive look to the products, enhancing brand recognition and recall among customers.
Chinese manufacturers understand the importance of branding and provide various customization options to meet specific requirements. They can modify the appearance, color, and design of CNC drilling machines to reflect the brand’s identity and values. This level of customization helps businesses create a unique and consistent brand image across their product range.
Furthermore, Chinese manufacturers offer branding opportunities by providing OEM (Original Equipment Manufacturer) services. This enables businesses to place their brand name on CNC drilling machines manufactured by Chinese companies. OEM allows companies to leverage the expertise and reputation of Chinese manufacturers while establishing their brand presence in the market.
Additionally, Chinese manufacturers often offer flexible packaging options, enabling businesses to package CNC drilling machines with their own branded packaging. This further enhances the brand’s visibility and impact, creating a cohesive brand experience for customers.
Overall, partnering with Chinese CNC drilling manufacturers for custom private labeling and branding offers businesses a cost-effective way to establish their brand identity. It helps differentiate their products in the market, build customer loyalty, and increase brand recognition. With their extensive manufacturing capabilities and customization options, Chinese manufacturers are well-positioned to meet the unique branding needs of businesses worldwide.
Tips for Procurement and Considerations when Purchasing cnc drilling
When purchasing CNC drilling equipment, there are several key considerations and tips to keep in mind to ensure a successful procurement process. Here are some important factors to consider:
1. Define your requirements: Clearly define your drilling needs and specifications. Consider the materials you will be drilling, desired accuracy, production volume, and other specific requirements. This will help you narrow down your options and find the right CNC drilling machine for your needs.
2. Research the market: Conduct thorough research on the available CNC drilling machines and the manufacturers. Compare various brands, features, and customer reviews to identify reputable suppliers that offer reliable and high-quality equipment.
3. Evaluate the machine’s capabilities: Look for key features such as drilling speed, spindle motor power, spindle rotation speed, drilling capacity, and automatic tool changers. Ensure that the machine can handle your drilling requirements effectively.
4. Consider the space and installation requirements: Assess the available floor space in your facility and check the dimensions of the CNC drilling machine. Ensure that it can be accommodated properly and that your facility can provide the necessary power supply and ventilation required for safe operation.
5. Quality and reliability: Check the quality standards and certifications of the equipment, such as ISO or CE markings. Additionally, inquire about the machine’s maintenance requirements and the availability of spare parts to ensure uninterrupted production.
6. Consider after-sales support: Inquire about the manufacturer’s warranty, training, and technical support offered. A supplier that provides comprehensive after-sales support can help troubleshoot issues and prevent downtime during production.
7. Budget and cost-effectiveness: Set a clear budget for your CNC drilling machine while considering the long-term return on investment. Evaluate the total cost of ownership by considering energy consumption, maintenance requirements, and potential upgrades.
8. Seek professional advice: If you are new to CNC drilling, consider consulting with an industry expert or hiring a consultant to guide you through the procurement process. They can provide valuable insights and recommend suitable options based on your specific needs.
By considering these factors and following these tips, you can make an informed decision when purchasing CNC drilling equipment, ensuring that it meets your requirements, quality standards, and budget limitations.
FAQs on Sourcing and Manufacturing cnc drilling in China
1. Why should I consider sourcing and manufacturing CNC drilling in China?
China has emerged as the global manufacturing hub due to its cost-efficiency, skilled labor force, and advanced manufacturing infrastructure. Sourcing and manufacturing CNC drilling in China can significantly reduce production costs, providing you with a competitive advantage in your industry.
2. How can I find reliable CNC drilling manufacturers in China?
There are various ways to find reliable manufacturers in China. You can attend trade shows and exhibitions related to CNC drilling to connect with potential suppliers. Online platforms like Alibaba and Global Sources also allow you to search for manufacturers and read reviews from previous customers. Additionally, hiring a sourcing agent who has local expertise and contacts can help you find reliable manufacturers.
3. What should I consider when selecting a CNC drilling manufacturer in China?
When selecting a manufacturer, consider factors such as their experience in CNC drilling, quality control processes, production capacity, certifications, and the ability to meet your specific requirements. Request samples or visit their factory to inspect their equipment and production capabilities.
4. How can I ensure the quality of the CNC drilling products produced in China?
Ensure that the manufacturer you choose has a robust quality control system in place. Ask for their quality certifications, such as ISO 9001, and inquire about their inspection processes during production. Conduct regular inspections or hire a third-party quality inspection company to ensure consistent quality.
5. What is the typical lead time for manufacturing CNC drilling products in China?
Lead times can vary depending on the complexity and quantity of your order, as well as the manufacturer’s production capacity and workload. Typically, lead times range from a few weeks to a few months. It is essential to discuss the expected lead time with the manufacturer and agree on a timeline before placing an order.
6. Can I customize my CNC drilling products manufactured in China?
Yes, most manufacturers in China offer customization services. Provide detailed specifications, drawings, or samples to the manufacturer to ensure precise customization. However, keep in mind that customization may affect the lead time and production cost.
7. What are the payment terms when sourcing and manufacturing CNC drilling products in China?
Payment terms are usually negotiated with the manufacturer but commonly follow a combination of initial deposit, progress payments, and final payment before shipment. Consider using secure payment methods or escrow services to minimize risks.
In conclusion, sourcing and manufacturing CNC drilling in China can be a cost-effective and efficient solution. To ensure a successful partnership, conduct thorough research, select reliable manufacturers, and prioritize communication and quality control throughout the process.
Why contact sourcifychina.com get free quota from reliable cnc drilling suppliers?
Sourcifychina.com offers free quota from reliable CNC drilling suppliers to provide potential clients with an easy and efficient way to fulfill their manufacturing needs. By obtaining a free quota, customers can quickly and conveniently assess the cost and feasibility of their projects before committing to a partnership with a supplier. This allows for informed decision-making and ensures that clients are able to find the best fit for their specific requirements.
Additionally, obtaining a free quota from reliable CNC drilling suppliers through sourcifychina.com enables clients to benefit from the expertise and capabilities of top-tier manufacturing companies. These suppliers have been thoroughly vetted to ensure that they meet high standards of quality, efficiency, and reliability. As such, customers can have confidence in the accuracy and competitiveness of the quotes they receive, knowing that they are from trusted and reputable sources.
Moreover, the process of obtaining a free quota from reliable CNC drilling suppliers is streamlined through sourcifychina.com’s platform, saving clients time and effort in their search for suitable manufacturing partners. The user-friendly interface and efficient communication channels facilitate seamless interaction between clients and suppliers, allowing for prompt and effective exchange of project details and quotation requests.
In conclusion, by offering free quota from reliable CNC drilling suppliers, sourcifychina.com empowers clients to make informed decisions and access high-quality manufacturing services that align with their needs. The platform’s commitment to transparency, reliability, and efficiency makes it an invaluable resource for businesses seeking trusted and cost-effective manufacturing solutions.