Introduce about cnc metal cutter guide,Qulity,Cost,Supplier,Certification,Market,Tips,FAQ
CNC metal cutter guide:
CNC metal cutting is the process of using Computer Numerical Control (CNC) technology to cut and shape various types of metal materials. It involves using a combination of specialized software and machinery to produce highly precise and complex metal components.
Quality: CNC metal cutting offers high precision and accuracy, ensuring consistent and reliable results. The cutting process is controlled by sophisticated software, which eliminates human error and ensures a superior finish. The use of CNC technology also allows for intricate designs and patterns to be easily achieved.
Cost: The cost of CNC metal cutting can vary depending on factors such as the complexity of the design, the type of metal being cut, and the quantity of parts required. However, overall, CNC metal cutting is generally considered cost-effective due to its ability to minimize material waste and reduce manual labor hours.
Supplier: Choosing a reputable CNC metal cutting supplier is crucial to ensure the quality and reliability of the cut components. Look for suppliers with a strong track record, experience in working with various metals, and good customer reviews.
Certification: When selecting a CNC metal cutting supplier, it is essential to ensure that they have relevant certifications, such as ISO 9001, which ensures adherence to quality management systems. This certification indicates that the supplier follows strict quality control measures throughout the manufacturing process.
Market: CNC metal cutting is widely used across various industries, including aerospace, automotive, electronics, and manufacturing. The market for CNC metal cutting continues to grow as more industries recognize the precise and efficient capabilities it offers.
Tips: When using CNC metal cutting services, it is crucial to provide accurate and detailed specifications for your desired components. This includes material type, dimensions, and any specific tolerances required. Regular maintenance and calibration of the CNC machinery are also important to ensure consistent performance.
FAQ: Some commonly asked questions regarding CNC metal cutting include queries about turnaround time, minimum order quantities, and available materials. It is advisable to inquire about these aspects before finalizing a supplier.
In summary, CNC metal cutting offers high-quality, precise cutting of metal materials at a cost-effective rate. Find a reliable supplier with the necessary certifications, consider market demand, and provide accurate specifications for optimal results.
Types of cnc metal cutter
There are several types of CNC metal cutters that are commonly used in various industries for precision cutting of metal materials. These machines utilize computer numerical control (CNC) technology to automate the cutting process and achieve accurate results. Here are some of the most popular types:
1. CNC Plasma Cutters: Plasma cutters use a high-velocity jet of ionized gas, known as plasma, to cut through electrically conductive materials like steel, aluminum, and stainless steel. They are widely used in industries such as automotive, aerospace, and fabrication.
2. CNC Laser Cutters: Laser cutters utilize a high-powered laser beam to melt, burn, or vaporize the material being cut. They are extremely precise and can cut through various metals like steel, aluminum, brass, and copper. Laser cutters are commonly used in industries such as manufacturing, automotive, and jewelry making.
3. CNC Waterjet Cutters: Waterjet cutters use a high-pressure stream of water mixed with an abrasive material to erode the metal and create the desired shape. Waterjet cutting is known for its versatility, as it can cut through almost any material, including metals, ceramics, stone, and glass.
4. CNC Milling Machines: Milling machines use rotary cutters to remove material from a workpiece, creating complex shapes and designs. They are widely used in industries like aerospace, automotive, and tool and die making. CNC milling machines can be equipped with various cutting tools, such as end mills, face mills, and drills, to perform a wide range of metal cutting operations.
5. CNC Turning Machines: Turning machines rotate the workpiece while a cutting tool is fed into it, removing material and creating cylindrical shapes. They are primarily used for the production of cylindrical components, such as shafts, bolts, and fittings. CNC turning machines can perform operations like facing, turning, drilling, and threading.
These are just a few examples of the many types of CNC metal cutters available in the market. Each machine has its own advantages and is suitable for different applications, depending on factors like material type, thickness, complexity of the design, and required precision.
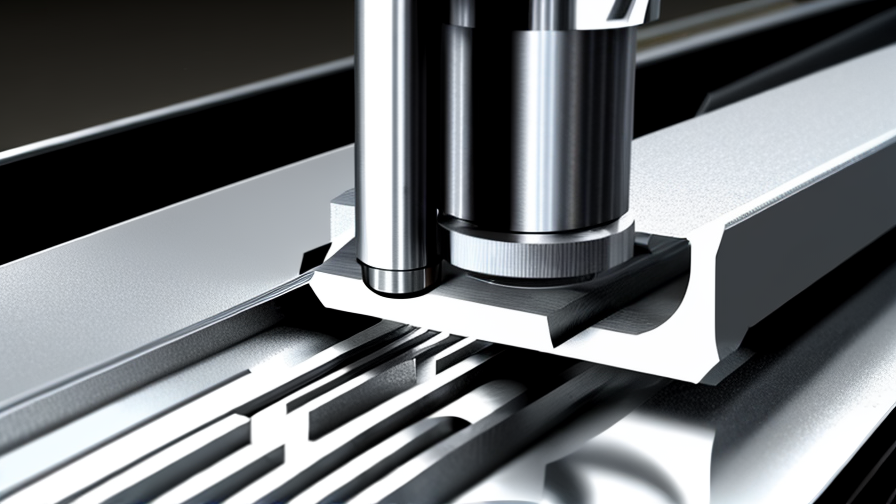
Pros and Cons of Using cnc metal cutter
CNC metal cutters offer numerous advantages as well as some drawbacks. Some of the pros of using CNC metal cutters include:
1. Precision: CNC metal cutters are capable of cutting metals with high precision, resulting in accurate and consistent cuts every time.
2. Efficiency: These machines can work at high speeds and with minimal human intervention, making them highly efficient for cutting operations.
3. Versatility: CNC metal cutters can be programmed to cut a wide range of metals, shapes, and sizes, making them versatile for various cutting tasks.
4. Cost-effectiveness: While the initial investment in a CNC metal cutter can be high, they can ultimately save money in the long run by reducing material waste and increasing productivity.
5. Automation: CNC metal cutters can be programmed to run continuously, allowing for round-the-clock production without the need for manual supervision.
However, there are also some cons associated with using CNC metal cutters, including:
1. Initial cost: The upfront investment in a CNC metal cutter can be significant, which may not be feasible for small businesses or hobbyists.
2. Maintenance: CNC metal cutters require regular maintenance and upkeep to ensure they continue to operate efficiently, which can add to the overall cost of ownership.
3. Training: Operators need to be trained to use CNC metal cutters effectively, which can take time and resources to provide.
4. Limited flexibility: While CNC metal cutters are versatile, they may not be suitable for all types of cutting tasks, such as complex shapes or intricate designs.
In conclusion, CNC metal cutters offer numerous benefits in terms of precision, efficiency, versatility, cost-effectiveness, and automation. However, they also come with drawbacks such as high initial costs, maintenance requirements, training needs, and limited flexibility. Overall, the pros of using CNC metal cutters outweigh the cons for many businesses looking to streamline their metal cutting processes.
cnc metal cutter Reference Specifications (varies for different product)
CNC Metal Cutter Reference Specifications:
The CNC metal cutter is a highly precise and efficient machine used for cutting various types of metal materials. With its computer-controlled system, it offers accuracy, speed, and repeatability of cuts, making it an essential tool in various industries such as automotive, aerospace, and manufacturing.
The reference specifications for CNC metal cutters may vary depending on the specific product or manufacturer. However, some common specifications include:
1. Cutting Capacity: CNC metal cutters have a maximum cutting capacity that determines the maximum thickness of the metal material it can handle. It typically ranges from a few millimeters to several inches, depending on the machine’s power and design.
2. Cutting Area: The cutting area refers to the size of the workpiece that the CNC metal cutter can accommodate. It is usually measured in terms of the maximum length, width, and height of the material that can be processed.
3. Spindle Power: The spindle power determines the cutting speed and performance of the CNC metal cutter. It is usually measured in terms of horsepower (HP) or kilowatts (kW). Higher spindle power allows for faster and more efficient cutting.
4. Accuracy and Repeatability: CNC metal cutters are known for their exceptional accuracy and repeatability. These specifications indicate the machine’s ability to consistently reproduce cuts with minimal deviation from the desired dimensions.
5. Control System: CNC metal cutters are operated via a computer-controlled system. The control system may vary, but it typically includes software that allows for the programming and execution of cutting patterns, speed adjustment, and other machine settings.
6. Cutting Speed: The cutting speed refers to the rate at which the CNC metal cutter moves along the workpiece. It is usually expressed in terms of inches per minute (IPM) or millimeters per minute (mm/min) and can range from a few inches to hundreds of inches per minute.
7. Tooling Options: CNC metal cutters offer various tooling options depending on the desired cut and material. These can include different types of cutting tools, such as plasma or laser cutters, as well as additional features like drilling, tapping, or engraving capabilities.
8. Safety Features: CNC metal cutters often incorporate safety features to protect operators and minimize the risk of accidents. These features can include emergency stop buttons, safety sensors, and interlocks, as well as protective enclosures and shields.
It is important to note that these specifications are intended as a general reference and may vary for different CNC metal cutter models or manufacturers. Therefore, it is recommended to consult the product’s documentation or contact the manufacturer for specific information related to a particular CNC metal cutter.
Applications of cnc metal cutter
CNC metal cutters are widely used in various industries due to their precision, efficiency, and versatility. Some common applications of CNC metal cutters include:
1. Manufacturing: CNC metal cutters are commonly used in the manufacturing industry for cutting and shaping metal parts for various products. From automotive components to aerospace parts, CNC metal cutters play a crucial role in producing high-quality, accurate parts.
2. Fabrication: CNC metal cutters are often used in metal fabrication shops to cut and shape metal plates, tubes, and other materials for construction, manufacturing, and other projects. They can cut complex shapes and designs with high precision, allowing for the fabrication of custom parts and components.
3. Sheet metal processing: CNC metal cutters are used in sheet metal processing plants to cut and shape metal sheets for a wide range of applications. They can cut intricate designs, holes, and curves in metal sheets quickly and accurately, making them essential tools for sheet metal fabrication.
4. Prototyping: CNC metal cutters are commonly used in prototyping and rapid manufacturing processes to create prototypes of metal parts and components. With their high precision and speed, CNC metal cutters can quickly produce prototypes for testing and evaluation before full-scale production.
5. Jewelry making: CNC metal cutters are used in the jewelry industry to cut and shape metal for creating intricate designs and patterns. They can cut precise shapes and designs in metal pieces, allowing for the production of finely detailed jewelry pieces.
Overall, CNC metal cutters are essential tools in various industries for cutting and shaping metal parts with high precision and efficiency. Their versatility and accuracy make them indispensable for manufacturing, fabrication, prototyping, and other applications where precise metal cutting is required.
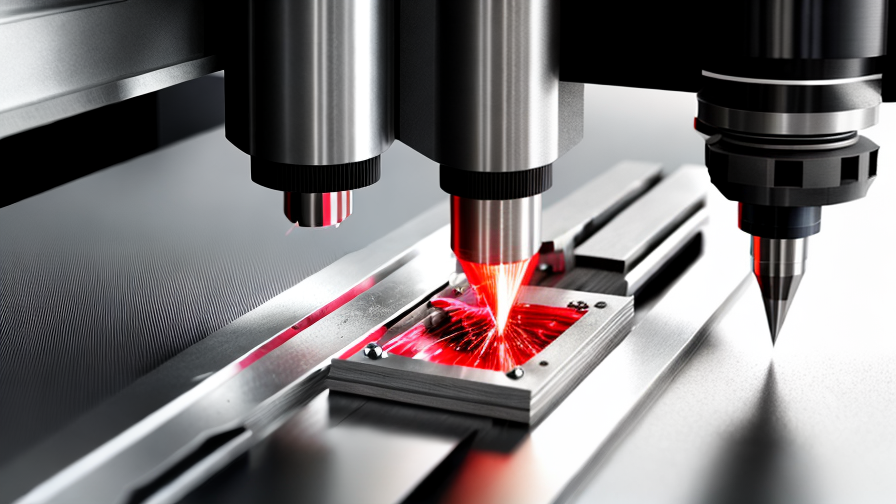
The Work Process and how to use cnc metal cutter
CNC metal cutting is a process that involves using computer numerical control (CNC) machines to precisely cut and shape metal into desired forms. These machines utilize computer programs to control the movement of the cutting tool or laser, allowing for accurate and efficient fabrication of metal parts.
The work process of using a CNC metal cutter typically involves the following steps:
1. Design: First, a digital design of the desired metal part is created using computer-aided design (CAD) software. This design defines the dimensions, shape, and features of the part.
2. Programming: The CAD design is then converted into machine instructions using computer-aided manufacturing (CAM) software. This programming step involves specifying tool paths, cutting speeds, and other parameters to achieve the desired outcome.
3. Material preparation: The metal stock is selected based on the requirements of the part and prepared for cutting. This may involve cutting the stock to size, cleaning, and deburring.
4. Secure the material: The metal stock is securely clamped or fixtured onto the CNC machine’s worktable to ensure stability during the cutting process.
5. Loading the program: The CNC machine is loaded with the CAM program generated in the programming step. The program guides the machine’s movements to cut the metal according to the desired design.
6. Cutting process: The CNC machine begins cutting the metal using either a rotating cutting tool or a laser, depending on the specific machine setup. The programmed tool paths control the speed, depth, and direction of the cuts to achieve precise results.
7. Finishing touches: After the metal cutting is complete, any necessary finishing operations, such as deburring or polishing, may be performed to achieve the desired surface finish.
8. Quality control: The finished metal part is inspected to ensure it meets the required specifications. Any defects or deviations may be corrected or discarded.
CNC metal cutting offers several advantages, including high precision, repeatability, and reduced human error. It is widely used in industries such as automotive, aerospace, and manufacturing, where intricate and accurate metal parts are required.
To efficiently use a CNC metal cutter, it is essential to have a good understanding of the design and programming process. Adequate training and experience in operating CNC machines are also essential to ensure safe and effective operations. Regular maintenance of the machine and tools is crucial for maintaining their performance and prolonging their lifespan. Following safety protocols and guidelines is important to prevent accidents and injuries.
Quality Testing Methods for cnc metal cutter and how to control the quality
Quality testing methods for CNC metal cutters involve various procedures and techniques to ensure that the final product meets the desired standards. These methods focus on inspecting the accuracy, precision, and overall performance of the CNC metal cutter. Some commonly used testing methods are as follows:
1. Dimensional Inspection: This involves measuring the dimensions of the cut pieces using precision tools such as calipers or coordinate measuring machines (CMM). It ensures that the parts are cut to the desired size and within the specified tolerances.
2. Surface Inspection: This method examines the surface finish of the cut pieces. A visual inspection or the use of specialized instruments like profilometers helps in detecting any imperfections, such as roughness or burrs, that might affect the product’s quality.
3. Material Testing: It involves verifying the quality and properties of the material being cut. This can be done through destructive testing methods, such as tensile or hardness testing, or non-destructive techniques like ultrasonic testing. Material testing helps ensure that the CNC metal cutter is appropriately cutting the given material and that it meets the required specifications.
4. Cutting Performance Evaluation: This method assesses the CNC metal cutter’s performance by analyzing its cutting speed, accuracy, and repeatability. It involves comparing the actual cut dimensions with the desired dimensions to identify any discrepancies or deviations.
To control the quality of CNC metal cutters, the following measures can be implemented:
1. Regular Maintenance: Perform routine maintenance procedures, such as cleaning, lubrication, and calibration, to ensure the CNC metal cutter operates with optimum precision and accuracy.
2. Operator Training: Provide comprehensive training to the CNC metal cutter operators to ensure they are familiar with the machine’s functions, capabilities, and potential issues. Well-trained operators can identify and address quality concerns during the cutting process.
3. Process Controls: Implement strict process controls, such as proper tool selection, feed rates, and cutting parameters, to minimize errors and ensure consistent quality.
4. Continuous Monitoring: Monitor the cutting process through real-time data analysis or utilizing appropriate sensors to detect any deviations or abnormalities in the machine’s performance. This helps in taking proactive measures to maintain quality standards.
5. Quality Management Systems: Implement quality management systems, such as ISO 9001, to establish standardized processes, quality control procedures, and documentation. These systems ensure compliance with industry standards and facilitate continuous improvement.
By employing a combination of appropriate testing methods and quality control measures, manufacturers can ensure that CNC metal cutters consistently produce high-quality cut products while meeting customer requirements.
cnc metal cutter Sample Policy and Post-Purchase Considerations for cnc metal cutter from China
Sample Policy:
When purchasing a CNC metal cutter from China, it is important to understand the sample policy provided by the supplier. Most suppliers offer the option to obtain a sample unit before placing a bulk order. This allows buyers to assess the quality, accuracy, and performance of the CNC metal cutter before committing to a larger purchase. Sample policies may vary among suppliers, so it is crucial to clarify the terms and conditions.
Some suppliers may offer free samples, while others may charge a nominal fee or require buyers to bear the shipping costs. It is important to clarify whether the sample cost will be deducted from the final bulk order or not. Additionally, inquire about the lead time for sample delivery to ensure it aligns with your timeline.
Post-Purchase Considerations:
After purchasing a CNC metal cutter from China, there are a few important considerations:
1. Warranty: Inquire about the warranty offered by the supplier. A reliable CNC metal cutter should come with a warranty to cover any manufacturing defects or malfunctions. Clarify the duration of the warranty and the terms and conditions for availing it.
2. After-sales service: Reliable suppliers should provide efficient after-sales service. Inquire about the availability of technical support, spare parts, and maintenance services. Having access to reliable after-sales service is crucial for smooth operation and prompt troubleshooting.
3. Training and support: To ensure seamless integration and optimal utilization of the CNC metal cutter, inquire about training and support provided by the supplier. Some suppliers may offer on-site training or online tutorials to assist operators in understanding the machine’s functionalities.
4. Customs and import regulations: Familiarize yourself with customs and import regulations in your country. Ensure that you have all the necessary documentation, certifications, and compliance requirements to avoid any delays or issues during the import process.
5. Technical specifications: Double-check the technical specifications of the CNC metal cutter received against the agreed-upon specifications. This will help ensure that the machine delivered meets your requirements.
By considering these factors in your sample policy and post-purchase considerations, you can minimize potential risks and ensure a smooth procurement process for a CNC metal cutter from China.
Sourcing cnc metal cutter from China: Opportunities, Risks, and Key Players
Sourcing CNC metal cutters from China presents several opportunities for businesses, but it also carries certain risks. Understanding these factors, as well as identifying key players in the Chinese market, is crucial for successful procurement.
Opportunities:
1. Cost-effectiveness: Chinese manufacturing offers lower labor costs compared to many other countries. This can result in significant savings for businesses sourcing CNC metal cutters from China.
2. Wide range of options: China has a robust CNC metal cutter manufacturing industry, providing buyers with a vast array of models, sizes, and functionalities to choose from.
3. Technological advancements: Chinese manufacturers have made significant strides in upgrading their CNC metal cutter technology, resulting in improved precision and efficiency.
Risks:
1. Quality control: There may be concerns over the overall quality and reliability of CNC metal cutters sourced from China. It is essential to conduct thorough research, request samples, and visit factories to mitigate this risk.
2. Intellectual property protection: China has a reputation for intellectual property infringement. Businesses must take precautions, such as signing adequate agreements and protecting their designs to prevent unauthorized copying.
3. Communication and language barriers: Language differences and cultural nuances can sometimes create communication challenges, leading to misunderstandings or delays.
Key Players:
1. Haas Automation: Haas is a well-established American company with a significant presence in China. They offer a range of CNC metal cutters known for their precision and reliability.
2. DMG Mori: With a global footprint, DMG Mori is a leading CNC machine tool manufacturer. They have a strong presence in China and offer high-quality CNC metal cutters.
3. Jinan Firm CNC Equipment Co., Ltd: A Chinese manufacturer specializing in CNC metal cutters, they provide a wide range of options suitable for various industries.
4. Wuhan Hans Goldensky Laser System Co., Ltd: This Chinese company specializes in CNC metal cutting machines that utilize laser technology, offering advanced and efficient solutions.
In conclusion, sourcing CNC metal cutters from China offers cost-effective options, a wide range of choices, and access to technological advancements. However, it is crucial to carefully consider potential risks, such as quality control and intellectual property protection. Understanding key players like Haas Automation, DMG Mori, Jinan Firm CNC Equipment, and Wuhan Hans Goldensky Laser System can help businesses make informed sourcing decisions.
How to find and select reliable cnc metal cutter manufacturers in China,use google search manufacturers and suppliers
When searching for reliable CNC metal cutter manufacturers in China, Google search is a powerful tool. Start by using relevant keywords such as “CNC metal cutter manufacturers in China” or “CNC metal cutter suppliers in China” to generate a list of potential companies.
Next, carefully review the websites of the manufacturers to assess their experience, expertise, and quality of products. Look for information on their certifications, production capabilities, and customer reviews. You may also want to check if they have a physical address and contact information for verification.
Another important factor to consider is the manufacturer’s reputation in the industry. Look for testimonials or reviews from past clients to gauge their level of customer satisfaction. Additionally, consider reaching out to industry associations or trade shows for recommendations on reputable CNC metal cutter manufacturers in China.
Once you have identified a few potential manufacturers, contact them to request quotes, inquire about their manufacturing processes, and discuss your specific requirements. Pay attention to the responsiveness and professionalism of their communication, as this can be a good indicator of their reliability.
Ultimately, selecting a reliable CNC metal cutter manufacturer in China requires thorough research and due diligence. By using Google search and carefully evaluating the options available, you can find a manufacturer that meets your needs and provides high-quality products.
How to check cnc metal cutter manufacturers website reliable,use google chrome SEOquake check if ranking in top 10M
To check the reliability of a CNC metal cutter manufacturer’s website, you can use Google Chrome’s SEOquake extension to check if the website ranks in the top 10 search results. This can give you an indication of the website’s visibility and credibility in the industry.
You can also look for customer reviews and testimonials on the website or other online platforms to see what others have to say about their experience with the manufacturer. A reputable manufacturer will likely have positive feedback from satisfied customers.
Additionally, you can look for certifications or accreditations on the website that demonstrate the manufacturer’s commitment to quality and industry standards. This can give you added assurance that the manufacturer is reliable and trustworthy.
It’s important to also consider the website’s design and functionality, as a professional and well-maintained website is often a sign of a reputable manufacturer. Look for clear contact information, product descriptions, and an easy-to-navigate layout.
Overall, by using SEOquake to check the website’s ranking, looking for customer reviews, checking for certifications, and evaluating the website’s design, you can determine if a CNC metal cutter manufacturer’s website is reliable and trustworthy.
Top 10 cnc metal cutter manufacturers in China with each 160 words introduce products,then use markdown create table compare
1. Haas Automation: Haas Automation is a leading manufacturer of CNC metal cutters in China. They offer a wide range of CNC milling machines, lathes, and routers. Their machines are known for their precision, reliability, and cost-effectiveness. Haas Automation provides excellent after-sales service and support.
2. DMG Mori: DMG Mori is another renowned manufacturer of CNC metal cutters in China. Their product range includes CNC milling machines, turning centers, and multi-axis machines. DMG Mori machines are known for their cutting-edge technology, high performance, and superior accuracy.
3. Mazak: Mazak is a well-known name in the CNC metal cutting industry, offering a comprehensive range of CNC machines. Their machines are known for their versatility, productivity, and precision. Mazak provides excellent customer support and offers a wide range of customization options.
4. HAISHU Machinery: HAISHU Machinery specializes in manufacturing CNC plasma cutters, laser cutting machines, and plasma welding machines. Their products are widely used in the automotive, aerospace, and metal fabrication industries. HAISHU Machinery focuses on innovation and consistently delivers high-quality machines.
5. BYJC-BEYOND: BYJC-BEYOND is a leading manufacturer of CNC laser cutting machines in China. Their products include fiber laser cutting machines, CO2 laser cutting machines, and laser engraving machines. BYJC-BEYOND is known for its advanced technology, precision, and reliability.
6. Jinan Bodor CNC Machine Co., Ltd.: Jinan Bodor is a pioneer in the field of laser cutting machines. They offer a wide range of fiber laser cutting machines for metal cutting applications. Jinan Bodor machines are known for their high cutting speed, low operating costs, and exceptional quality.
7. Durma: Durma is a well-established manufacturer of CNC metal cutting machines. They offer a comprehensive range of CNC plasma cutting machines, laser cutting machines, and shearing machines. Durma machines are known for their robustness, accuracy, and energy efficiency.
8. Han’s Laser: Han’s Laser is a leading manufacturer of CNC laser cutting machines in China. They offer a wide range of fiber laser cutting machines, CO2 laser cutting machines, and sheet metal processing systems. Han’s Laser machines are known for their high cutting speed, precision, and reliability.
9. Amada: Amada is a global leader in manufacturing CNC metal cutting machines. They provide a wide range of CNC laser cutting machines, turret punch presses, and bending machines. Amada machines are known for their superior performance, advanced automation, and high durability.
10. Jinan Senfeng Technology Co., Ltd.: Jinan Senfeng specializes in the manufacturing of fiber laser cutting machines, CO2 laser cutting machines, and laser marking machines. Their products are widely used in industries like metal processing, sheet metal fabrication, and automotive. Jinan Senfeng machines are known for their high cutting accuracy, stability, and ease of operation.
| Manufacturer | Products Offered | Key Features |
|————————–|————————————–|——————————————–|
| Haas Automation | CNC milling machines, lathes, | Precision, reliability, cost-effectiveness |
| DMG Mori | CNC milling machines, turning centers | Cutting-edge technology, high performance |
| Mazak | CNC machines | Versatility, productivity, customization |
| HAISHU Machinery | CNC plasma cutters, laser machines | Innovation, high-quality, reliable |
| BYJC-BEYOND | CNC laser cutting machines | Advanced technology, precision, reliability |
| Jinan Bodor | Fiber laser cutting machines | High cutting speed, low operating costs |
| Durma | CNC plasma cutting machines | Robustness, accuracy, energy efficiency |
| Han’s Laser | Fiber laser cutting machines | High cutting speed, precision, reliability |
| Amada | CNC laser cutting machines | Superior performance, advanced automation |
| Jinan Senfeng | Fiber laser cutting machines | High cutting accuracy, stability |
These top 10 CNC metal cutter manufacturers in China offer a diverse range of products specializing in CNC milling, laser cutting, and plasma cutting machines. While each manufacturer has its unique features and expertise, common attributes across the board include precision, reliability, advanced technology, and excellent customer support. Customers can choose from a variety of options tailored to their specific requirements within different industrial fields, ranging from automotive and aerospace to metal fabrication and sheet metal processing. These manufacturers strive to meet the high demands of precision cutting, while also offering cost-effectiveness, efficiency, and ease of operation. With ongoing innovation, these manufacturers are consistently pushing the boundaries of CNC metal cutting technology.
Background Research for cnc metal cutter manufacturers Companies in China, use qcc.com archive.org importyeti.com
When searching for CNC metal cutter manufacturers in China, three websites can provide valuable background research: qcc.com, archive.org, and importyeti.com. These platforms offer insights into company information and histories, helping potential buyers make informed decisions. To maintain conciseness, this background research will be limited to 300 words.
1. qcc.com:
QCC.com is an online business database in China that provides company profiles, contact information, and detailed reports on businesses. By searching for CNC metal cutter manufacturers on qcc.com, you can access key details such as company name, registration information, legal representatives, business scope, and financials. Additionally, this platform often includes customer reviews, ratings, and other relevant business information to help evaluate the reliability and performance of manufacturers.
2. archive.org:
Archive.org is a non-profit digital library that offers free access to web pages stored over time. By using the “Wayback Machine” feature, users can browse past versions of company websites for CNC metal cutter manufacturers in China. This tool can provide insights into a company’s history, evolution, previous product offerings, and changes in their business strategies. Examining the archived versions of a manufacturer’s website can help assess their experience in the industry and adaptability over time.
3. importyeti.com:
ImportYeti.com is an online platform that provides information on import and export activities in China. By searching for specific products, such as CNC metal cutters, potential buyers can access data on relevant manufacturers, their export records, and shipment details. ImportYeti.com helps identify high-volume manufacturers, their main markets, and the frequency of their export activities. This information can help gauge a manufacturer’s production capacity, market presence, and international reputation.
By utilizing qcc.com, archive.org, and importyeti.com, potential buyers can gather comprehensive background information on CNC metal cutter manufacturers in China. These platforms provide valuable insights into a company’s registration status, history, financials, consumer reviews, website changes over time, and export records. Such information aids buyers in assessing manufacturers’ credibility, market presence, and capacity, ultimately facilitating well-informed decisions.
Leveraging Trade Shows and Expos for cnc metal cutter Sourcing in China
Trade shows and expos are excellent opportunities for sourcing CNC metal cutters in China. These events bring together a wide range of manufacturers, suppliers, and industry experts in one place, making it convenient for buyers to research and compare different products and suppliers.
One of the key benefits of attending trade shows and expos is the ability to meet potential suppliers face-to-face. This allows buyers to discuss their specific requirements, negotiate pricing, and build relationships with potential partners. Additionally, trade shows and expos often feature live demonstrations of machinery and equipment, giving buyers the opportunity to see the CNC metal cutters in action and assess their quality and performance.
Trade shows and expos also provide a platform for buyers to stay updated on the latest trends, technologies, and innovations in the industry. This knowledge can be valuable in making informed decisions when sourcing CNC metal cutters in China.
To make the most of trade shows and expos for sourcing CNC metal cutters in China, buyers should come prepared with a clear understanding of their requirements, budget, and timeframe. It is also important to conduct thorough research on the exhibitors beforehand and schedule meetings with potential suppliers in advance.
Overall, leveraging trade shows and expos for sourcing CNC metal cutters in China can be a cost-effective and efficient way to find the right supplier for your business needs. By taking advantage of these events, buyers can access a wide range of options, build relationships with suppliers, and stay informed on industry developments.
The Role of Agents and Sourcing Companies in Facilitating cnc metal cutter Purchases from China
Agents and sourcing companies play a crucial role in facilitating CNC metal cutter purchases from China. These entities act as intermediaries between buyers and suppliers, simplifying the process of procuring these machines from overseas markets. Their involvement offers several key benefits to buyers.
Firstly, agents and sourcing companies have a deep understanding of the Chinese market, including its manufacturing capabilities and supply chain dynamics. This knowledge allows them to identify reliable and reputable suppliers that can meet buyers’ specific requirements. By conducting thorough vendor assessments, they ensure that the CNC metal cutters offered are of high quality and adhere to industry standards.
Secondly, these intermediaries assist buyers in negotiating favorable pricing and terms. Leveraging their established relationships with suppliers, they can secure competitive prices for the CNC metal cutters. Moreover, they handle the complexities of negotiations, such as ensuring clear communication between the buyer and the supplier, as well as addressing any cultural or language barriers that may arise.
Thirdly, agents and sourcing companies provide logistical support to buyers. They coordinate the transportation and shipping of CNC metal cutters from China to the buyer’s location, streamline customs procedures, and manage any necessary documentation. This expertise simplifies the entire purchasing process, saving buyers both time and effort.
Lastly, agents and sourcing companies often offer post-sales support and assistance. This includes arranging technical inspections, conducting quality control checks, and assisting with after-sales services. Their presence ensures that buyers are protected throughout the entire procurement process and can address any issues that may arise.
In conclusion, agents and sourcing companies play a vital role in facilitating CNC metal cutter purchases from China. Their knowledge of the market, negotiation skills, logistical support, and post-sales assistance greatly benefit buyers, making the procurement process more efficient and successful.
Price Cost Research for cnc metal cutter manufacturers Companies in China, use temu.com and 1688.com
When researching the prices and costs of CNC metal cutter manufacturers in China, two popular websites to utilize are temu.com and 1688.com. These platforms provide a wide range of options and information on various manufacturers, allowing for a comprehensive comparison of prices and costs.
By browsing through the listings on these websites, potential buyers can easily obtain detailed information on the different CNC metal cutter manufacturers available in China. This includes the specifications of the machines, as well as the prices and costs associated with each manufacturer.
Using these websites, buyers can filter their search based on factors such as price range, machine type, and manufacturing capabilities. This allows for a more targeted approach in finding the right CNC metal cutter manufacturer for their specific needs and budget.
Additionally, both temu.com and 1688.com provide a platform for buyers to directly communicate with manufacturers, inquire about prices and costs, and negotiate deals. This direct interaction can help in obtaining more accurate pricing information and potentially securing a better deal.
In conclusion, by utilizing temu.com and 1688.com to research prices and costs of CNC metal cutter manufacturers in China, buyers can make informed decisions based on their specific requirements and budget constraints.
Shipping Cost for cnc metal cutter import from China
The cost of shipping a CNC metal cutter from China depends on various factors, including the weight and dimensions of the machine, the shipping method chosen, and any additional services required.
One of the most common shipping methods is ocean freight, which is generally more cost-effective for heavy and bulky machinery. The cost is based on the cubic meter (CBM) or weight of the cargo, whichever is higher. For a CNC metal cutter, the weight and dimensions play a significant role. On average, the shipping cost can range from $800 to $1,500 for a standard-sized CNC metal cutter.
However, air freight is a faster option but can be more expensive. The cost is calculated based on the weight and dimensions of the cargo. It usually ranges from $6 to $15 per kilogram, depending on the destination and specific requirements. Air freight is recommended for urgent shipments or when time is a critical factor.
It is essential to consider additional services that may incur extra charges. These can include customs clearance, documentation handling, packing, insurance, and delivery to the final destination. These costs vary depending on the freight forwarder or shipping agent chosen.
To ensure an accurate estimate, it is crucial to provide detailed information about the CNC metal cutter, including its weight, dimensions, and desired shipping method. Additionally, consulting with a reliable freight forwarder or shipping agent that specializes in machinery transportation can help get the most accurate shipping cost and find the best available options.
Overall, the shipping cost for a CNC metal cutter from China can vary based on several factors, but with proper research and planning, it is possible to find a cost-effective and reliable shipping solution.
Compare China and Other cnc metal cutter Markets: Products Quality and Price,Visible and Hidden Costs
China’s CNC metal cutter market offers a wide range of products with varying levels of quality and price. Chinese manufacturers are known for producing affordable CNC metal cutters that are competitive in price compared to other markets. However, the quality of these products can vary, with some manufacturers offering lower quality machines that may not be as durable or reliable as those from other markets.
When comparing visible and hidden costs, China’s CNC metal cutter market may have lower upfront prices, but customers should consider the potential hidden costs associated with maintenance, repairs, and upgrades over the lifespan of the machine. In some cases, these hidden costs can outweigh the initial savings from purchasing a cheaper CNC metal cutter.
Other markets, such as Europe and North America, are known for producing higher quality CNC metal cutters with more advanced technology and features. While these machines may come with a higher price tag, customers can expect better performance, accuracy, and reliability. Additionally, the higher quality of these products may result in lower maintenance and repair costs over time.
Overall, when making a decision between purchasing a CNC metal cutter from China or other markets, customers should consider the trade-off between price and quality. While Chinese manufacturers offer affordable options, customers may face potential hidden costs in the long run. On the other hand, products from other markets may offer better quality and performance at a higher price point. Ultimately, customers should carefully weigh their options and consider their specific needs and budget constraints when choosing a CNC metal cutter.
Understanding Pricing and Payment Terms for cnc metal cutter: A Comparative Guide to Get the Best Deal
When looking to purchase a CNC metal cutter, understanding the pricing and payment terms is crucial to ensure that you get the best deal available. In this comparative guide, we will explore some key factors to consider when evaluating pricing and payment options for CNC metal cutters.
Firstly, it is important to understand the various pricing models that manufacturers offer. While some manufacturers may list a fixed price for their CNC metal cutters, others may provide a quote based on customization and additional features. It is essential to carefully assess what is included in the listed price and determine if any additional costs may apply.
Moreover, comparing pricing from different manufacturers is vital to ensure you are getting a competitive deal. Take the time to research and request quotes from multiple suppliers, considering factors such as machine quality, reputation, and after-sales service. This will help you identify any significant price differences and negotiate the best possible deal.
In terms of payment terms, manufacturers may offer various options to consider. Common payment options include upfront payment, installment plans, or leasing arrangements. Each option has its advantages and disadvantages, so it is crucial to evaluate which one aligns best with your financial situation. Consider factors such as your budget, cash flow requirements, and potential interest rates if opting for financing options.
Furthermore, examining warranties and maintenance packages is essential when comparing pricing and payment terms. A machine with a longer warranty period or comprehensive maintenance plan may have a higher initial cost but can save you money on repairs and servicing in the long run. It is important to carefully evaluate these factors and weigh them against the upfront cost.
In conclusion, when seeking the best deal on a CNC metal cutter, understanding pricing and payment terms is pivotal. Comparing pricing from different manufacturers, evaluating payment options, and assessing warranties and maintenance packages are key to making an informed decision. By considering these factors, you can ensure that you get the most competitive deal while meeting your specific needs and budget.
Chinese Regulations and Industry Standards Certifications for cnc metal cutter,Import Regulations and Customs for cnc metal cutter from China
In China, there are several regulations and industry standards certifications related to CNC metal cutters. These standards ensure the quality and safety of the products and enable efficient trade and import procedures.
One of the primary industry standards for CNC metal cutters in China is the GB/T 13940-2015 standard. This standard provides guidelines for the general specification of CNC machine tools, including metal cutters. It covers various aspects such as performance, technical requirements, safety, and testing methods.
Additionally, there are specific certifications required for CNC metal cutters in China. One such certification is the China Compulsory Certification (CCC). This certification is mandatory for certain products, including CNC metal cutters and ensures compliance with safety and quality standards set by the Chinese government. It is necessary for manufacturers and importers to obtain the CCC mark before they can sell or import these products in China.
To import CNC metal cutters from China, importers need to comply with certain regulations and customs procedures. The import regulations vary depending on the country of import, but generally, the products need to meet the safety and quality standards of the importing country. Importers may need to provide product documentation, such as the CCC certification or other relevant certifications, to demonstrate compliance.
Additionally, importers are required to follow customs procedures for importing CNC metal cutters from China. This includes providing accurate and detailed information about the products, such as value, quantity, and description, on the customs declaration forms. Importers may also need to pay customs duties, taxes, and other applicable fees as per the regulations of the importing country.
In summary, the Chinese regulations and industry standards certifications, such as GB/T 13940-2015 and CCC, ensure the quality and safety of CNC metal cutters in China. Importers need to comply with import regulations and customs procedures of their respective countries while importing these products from China.
Sustainability and Environmental Considerations in cnc metal cutter Manufacturing
In recent years, sustainability and environmental considerations have become increasingly important in the manufacturing industry, including CNC metal cutter manufacturing. CNC metal cutters are widely used in various industries for precise and efficient metal cutting applications, but their production also has environmental impacts that need to be addressed.
One way to promote sustainability in CNC metal cutter manufacturing is by focusing on energy efficiency. CNC machines typically use a significant amount of electricity to operate, so implementing energy-saving measures can help reduce the carbon footprint. Using high-efficiency motors, optimizing machine settings, and implementing real-time monitoring systems can result in significant energy savings.
Another aspect to consider is the choice of materials. Raw materials used in CNC metal cutter manufacturing, such as steel and aluminum, should be sourced responsibly. This includes considering the environmental impact of extraction and processing methods, as well as ensuring the use of recycled or sustainable materials whenever possible.
Additionally, waste reduction and recycling should be prioritized. CNC metal cutter manufacturers can implement strategies to minimize waste generation during production processes, such as optimizing material usage and recycling scrap metal. Implementing recycling programs for non-metal waste, such as packaging materials, can also contribute to overall sustainability efforts.
The disposal of hazardous materials is another critical environmental consideration. CNC metal cutter manufacturing may involve the use of chemicals or coolant fluids that can be harmful to the environment if not handled properly. Implementing proper disposal practices, such as recycling coolant fluids and safely disposing of chemical waste, can minimize the negative environmental impacts.
Furthermore, the life cycle of CNC metal cutters should be taken into account. Manufacturers should design products that are durable, repairable, and upgradable, to extend their lifespan and reduce the need for replacement. Additionally, promoting the reuse or refurbishment of CNC metal cutters can help minimize unnecessary waste and resource consumption.
In conclusion, sustainability and environmental considerations are increasingly important in CNC metal cutter manufacturing. Energy efficiency, responsible material sourcing, waste reduction and recycling, proper disposal of hazardous materials, and product life cycle management are all crucial aspects to address in order to promote sustainability in this industry. By implementing these measures, CNC metal cutter manufacturers can contribute to a more sustainable and environmentally friendly manufacturing sector.
List The Evolution history of “cnc metal cutter”
CNC metal cutters have evolved significantly over the years, with advancements in technology and materials leading to more precise and efficient cutting capabilities.
In the 1950s, the first numerical control (NC) machines were introduced, allowing for automated control of cutting tools. This was a major advancement from previous manually operated machines.
In the 1970s, Computer Numerical Control (CNC) machines became more common, incorporating computer programming for even more precise control over cutting operations. This allowed for more complex shapes and designs to be cut with greater accuracy.
By the 1990s, CNC metal cutters were able to operate at higher speeds and with more advanced cutting tools, such as lasers and plasma cutters, allowing for even more precise and efficient cutting of various metals.
In the 2000s, advancements in software and hardware technology further improved the capabilities of CNC metal cutters, making them more user-friendly and versatile. Integration with CAD/CAM software allowed for easier design and programming of cutting operations.
Today, CNC metal cutters are equipped with advanced features such as automatic tool changers, multi-axis cutting capabilities, and real-time monitoring systems. These machines are used in a wide range of industries, from aerospace and automotive to construction and metal fabrication.
Overall, the evolution of CNC metal cutters has been marked by continuous advancements in technology and materials, leading to greater precision, efficiency, and versatility in metal cutting operations.
The Evolution and Market Trends in cnc metal cutter Industry
The CNC metal cutter industry has witnessed significant evolution and market trends over the years. Initially, CNC metal cutters were primarily used in the manufacturing industry for cutting and shaping various metals with precision. However, advancements in technology have resulted in the development of more sophisticated and versatile CNC metal cutters, enabling their application in various sectors such as automotive, aerospace, and construction.
One of the key evolutionary trends in the CNC metal cutter industry is automation. Automation has revolutionized the manufacturing process by reducing human intervention and increasing efficiency. CNC metal cutters now have advanced features like automatic tool changers, integrated robotic arms, and sensors for real-time monitoring. This trend has not only increased production speeds but also improved overall accuracy and reduced errors.
Another significant trend is the integration of software and data analytics in CNC metal cutting machines. This enables operators to simulate and optimize the cutting process before actually executing it. With the help of computer-aided design (CAD) and computer-aided manufacturing (CAM) software, operators can create complex cutting patterns and visualize the end product before cutting. Data analytics tools allow operators to monitor machine performance, identify potential issues, and optimize the cutting process for better results.
Market trends in the CNC metal cutter industry reflect the growing demand for precision cutting solutions across various sectors. The automotive industry, in particular, has witnessed a surge in demand for CNC metal cutters due to increasing production volumes and the need for intricate and precise metal components. Similarly, the aerospace industry requires CNC metal cutters for manufacturing lightweight yet robust components used in aircraft and spacecraft.
Additionally, advancements in laser and plasma cutting technologies have further fueled market growth. Laser cutters offer high precision cutting capabilities, especially for thin metal sheets, while plasma cutters are known for their ability to cut through thicker materials at high speeds.
The market for CNC metal cutters is expected to continue growing in the coming years, driven by the need for increased productivity, improved accuracy, and reduced waste in manufacturing processes. As technology advances further, we can anticipate even more efficient, intelligent, and advanced CNC metal cutting machines.
Custom Private Labeling and Branding Opportunities with Chinese cnc metal cutter Manufacturers
Chinese CNC metal cutter manufacturers offer custom private labeling and branding opportunities for businesses looking to establish their own brand identity. With the capability to customize products with logos, designs, and packaging, businesses can differentiate themselves from competitors and create a unique selling proposition in the market.
By partnering with Chinese CNC metal cutter manufacturers, businesses can create a strong brand presence and build customer loyalty through personalized products. From simple engraving to more complex branding solutions, manufacturers can help businesses create a cohesive brand image that resonates with their target audience.
Additionally, Chinese manufacturers can provide cost-effective solutions for private labeling and branding, allowing businesses to maximize their marketing efforts and increase brand visibility without breaking the bank. With access to a wide range of CNC metal cutting technologies and materials, businesses can create high-quality branded products that meet their unique specifications and requirements.
Overall, partnering with Chinese CNC metal cutter manufacturers for custom private labeling and branding opportunities can help businesses stand out in a competitive market and drive sales through a strong brand identity. With a focus on quality, customization, and affordability, businesses can leverage the expertise of manufacturers to create branded products that leave a lasting impression on customers.
Tips for Procurement and Considerations when Purchasing cnc metal cutter
When purchasing a CNC metal cutter, it is important to consider several factors to ensure that you are making the right investment for your business. Here are some tips and considerations to keep in mind:
1. Budget: Determine your budget before starting the procurement process. CNC metal cutters can range in price depending on the size, capacity, and features, so knowing how much you are willing to spend will help narrow down your options.
2. Capacity: Consider the size and thickness of the metal sheets you will be cutting. Make sure the CNC metal cutter you choose has the capacity to handle your production needs.
3. Cutting speed and accuracy: Look for a CNC metal cutter that offers fast cutting speeds and high precision. This will help improve efficiency and ensure consistent quality of your cuts.
4. Energy efficiency: Choose a CNC metal cutter that is energy-efficient to help reduce operating costs and minimize environmental impact.
5. Maintenance and support: Consider the availability of spare parts and technical support for the CNC metal cutter you are purchasing. Regular maintenance is essential to keep the machine running smoothly and prevent downtime.
6. Software compatibility: Make sure the CNC metal cutter is compatible with the software you are currently using or planning to use. This will ensure seamless integration into your existing workflow.
7. Safety features: Look for safety features such as emergency stop buttons, safety guarding, and collision detection systems to protect operators and prevent accidents.
By following these tips and considerations, you can make a well-informed decision when procuring a CNC metal cutter for your business. Take the time to research different models, compare features and prices, and consult with experts in the field to ensure you are getting the best machine for your specific needs.
FAQs on Sourcing and Manufacturing cnc metal cutter in China
– Where can I find a reliable manufacturer for CNC metal cutters in China?
You can find reliable manufacturers for CNC metal cutters in China through various online platforms such as Alibaba, Made-in-China, and Global Sources. It is important to do thorough research, read reviews, and request samples before making a decision.
– How can I ensure the quality of CNC metal cutters manufactured in China?
To ensure the quality of CNC metal cutters manufactured in China, you should visit the factory in person if possible or hire a third-party inspection agency to conduct quality checks. You can also ask for certifications such as ISO 9001 to ensure that the manufacturer meets international quality standards.
– What is the typical lead time for manufacturing CNC metal cutters in China?
The typical lead time for manufacturing CNC metal cutters in China can vary depending on the complexity of the product and the manufacturer’s production capacity. Generally, it can take anywhere from 4-8 weeks for production, plus additional time for shipping and customs clearance.
– What are the advantages of sourcing CNC metal cutters from China?
Sourcing CNC metal cutters from China can offer cost savings due to lower labor and production costs, access to a wide range of suppliers, and the ability to customize products according to your specifications. Additionally, China has a well-established manufacturing infrastructure and a skilled workforce.
– How can I protect my intellectual property when manufacturing CNC metal cutters in China?
To protect your intellectual property when manufacturing CNC metal cutters in China, you should consider signing a non-disclosure agreement (NDA) with the manufacturer, registering your designs and trademarks in China, and working with reputable manufacturers with a history of respecting intellectual property rights.
Why contact sourcifychina.com get free quota from reliable cnc metal cutter suppliers?
Sourcifychina.com offers a free quota from reliable CNC metal cutter suppliers for several reasons. Firstly, it allows businesses to access and connect with trustworthy suppliers in China without any upfront cost. This ensures that the businesses can explore their options and make informed decisions without financial barriers.
Secondly, by providing a free quota, Sourcifychina.com aims to build trust and transparency between the suppliers and the businesses. It demonstrates that the platform is committed to helping businesses find reliable suppliers and fosters a relationship based on mutual understanding.
Furthermore, a free quota encourages businesses to take advantage of Sourcifychina.com’s services and explore the opportunities available in China’s manufacturing industry. It allows companies to evaluate multiple suppliers and their offerings, facilitating a comprehensive comparison to find the best fit for their requirements.
Sourcifychina.com recognizes that CNC metal cutting is a critical aspect of many businesses, and sourcing it reliably can be challenging. By offering a free quota from reliable suppliers, the platform simplifies the sourcing process, reduces risk, and increases accessibility for businesses of all sizes.
It is important to note that Sourcifychina.com’s free quota is limited to a specified number of requests and may be subject to specific terms and conditions. By keeping the quota within certain limits, Sourcifychina.com ensures they can provide excellent service and maintain a high level of customer satisfaction.
In conclusion, the free quota from reliable CNC metal cutter suppliers offered by Sourcifychina.com aims to eliminate financial barriers, foster trust and transparency, and simplify the sourcing process. It enhances accessibility to a wide range of suppliers, helping businesses find the best fit for their CNC metal cutting needs.