Types and Applications of composite insulators
Composite insulators are a type of electrical insulating material that is made up of a combination of materials, such as fiberglass, resin, and silicon rubber. There are different types of composite insulators that are used in various electrical applications. In this article, we will discuss the four main types of composite insulators and their applications.
1. Suspension Insulators: Suspension insulators are used to support overhead electrical transmission lines. They are designed to withstand high mechanical loads and provide excellent insulation resistance. Suspension insulators are typically used in high-voltage systems, and they are an ideal choice for coastal and desert environments due to their resistance to salt spray and UV radiation.
2. Pin Insulators: Pin insulators are used to support electrical conductors on utility poles. They are designed to withstand the weight of the conductor and provide excellent insulation. Pin insulators are typically used in low-voltage systems, and they are an ideal choice for residential and commercial overhead electrical distribution.
3. Post Insulators: Post insulators are used to insulate electrical equipment, such as transformers and switchgear. They are designed to provide high insulation resistance and prevent electrical discharge. Post insulators are typically used in medium and high-voltage systems, and they are an ideal choice for industrial and commercial electrical applications.
4. Railway Insulators: Railway insulators are used to provide electrical insulation for railway signaling systems. They are designed to withstand high mechanical loads and provide excellent insulation resistance. Railway insulators are typically used in high-speed railway systems, and they are an ideal choice for harsh environments where high-levels of vibration, shock, and temperature variations are common.
In conclusion, composite insulators are a versatile and reliable solution for a wide range of electrical applications. The different types of composite insulators offer unique features and benefits that cater to specific electrical needs. The use of composite insulators can improve safety, reliability, and efficiency in electrical systems.
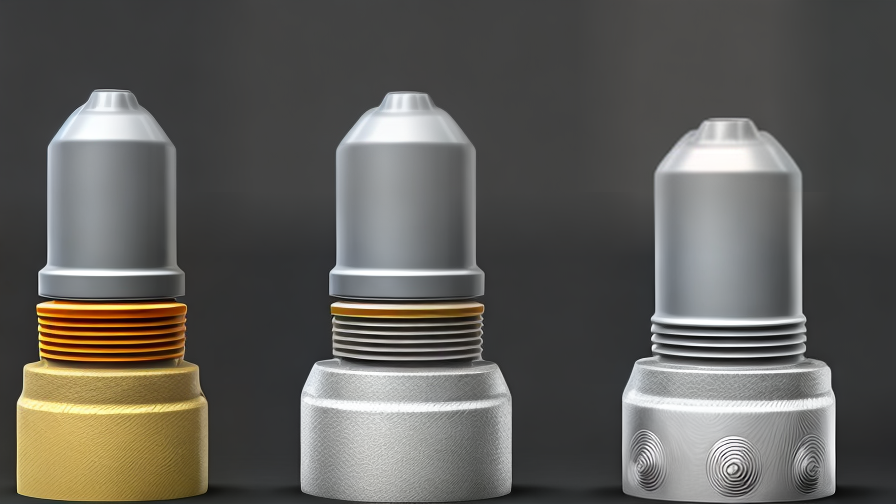
Benefits and Feature of Utilizing composite insulators
Composite insulators are made of a composite material that is composed of a core, a shed, and an outer coating. The benefits of utilizing composite insulators over traditional insulators made of glass or porcelain include lighter weight, higher strength, improved resistance to weather conditions, and longer lifespans. Other benefits of using composite insulators are as follows:
1. Reliable Insulation: Composite materials provide insulation properties that are more reliable and effective compared to traditional insulators. They are better able to withstand electrical stress and faults.
2. Easy to install: Composite insulators are easy to install due to their lightweight, which makes them easy to handle and transport.
3. Chemical Resistance: Composite insulators are highly resistant to chemical corrosion, making them suitable for use in harsh environments like chemical plants.
4. Low Maintenance Costs: Composite insulators require minimal maintenance, and this reduces the overall cost of operating and maintaining power lines.
5. High Flexibility: Composite materials are flexible, making them suitable for use in environments that experience significant temperature fluctuations.
6. Resilience to Impact: Composite insulators have improved mechanical strength, and they are strong enough to resist damage from storms or other natural disasters.
7. Improved Safety: Composite insulators are safer to use because they are non-conductive and do not require grounding.
8. Environmentally Friendly: Composite materials are eco-friendly and can be recycled, reducing the overall environmental impact of power generation and transmission.
In conclusion, composite insulators have several benefits over traditional insulators that make them a popular choice for use in power transmission and distribution. They offer enhanced performance, are reliable, and require less maintenance, making them an excellent choice for use in harsh environments.
The Process of composite insulators
Composite insulators are made of two main components, the first being a high-strength fiberglass rod or core, and the second being a layer of silicone rubber or other high dielectric strength material placed around the core. The manufacturing process begins with the selection of high-quality raw materials, which are carefully inspected to ensure their suitability for use in the production of composite insulators.
The first step in the production of composite insulators is the preparation of the fiberglass core. This involves the cutting of fiberglass strands to a specific length and diameter, which are then formed into a cylindrical shape using a mandrel. The core is then coated with a thin layer of silicone rubber or other insulating material, which acts as a barrier to prevent moisture ingress.
The next step in the production of composite insulators is the molding of the external insulating layer around the core. This is typically done using a silicone rubber injection molding process, where the silicone rubber material is heated and then injected into a precisely formed mold cavity. The mold is then cooled and the final insulator is removed from the mold.
Once the composite insulators have been molded, they are subjected to a series of quality control tests to ensure their suitability for use in high voltage applications. These tests include high voltage, current, and temperature testing, as well as visual inspection and dimensional measurement.
Overall, the production of composite insulators is a highly specialized process that requires the use of high-quality materials and skilled manufacturing techniques to produce a high-quality, reliable product that can withstand the harshest operating conditions.

How to use composite insulators
Composite insulators are high-voltage insulators that are used in power transmission and distribution networks, as well as in railway electrification systems. They are made up of a central core, which is usually made of glass or ceramic material, and an external layer of polymer material, which provides additional insulation and protection against environmental factors such as UV light, moisture, and pollution.
To use composite insulators, they must be installed in a correct and safe manner. Here are the steps to follow:
1. First, the composite insulators must be inspected to make sure that they are free from defects or damages. Any damaged or worn out insulators should be replaced immediately.
2. The insulators must be properly cleaned before installation. This involves removing any dust, dirt, or other debris that may be present on the insulator surface.
3. Determine the correct insulator type and size depending on the application. It is important to select the right insulator to avoid overloading or under-loading of the insulator.
4. The insulators should be mounted correctly on the support structure. The mounting method should be determined based on the type of insulator and the support structure used.
5. After mounting, the insulators should be properly tensioned. This ensures that the insulator is not under or over-stretched, which can cause damage.
6. Finally, the insulator’s integrity should be regularly checked to ensure that it remains in good condition. This includes conducting visual inspections and periodic testing of the insulator’s electrical strength.
In summary, when using composite insulators, it is important to follow proper installation procedures, correctly select the insulator type and size, properly mount and tension the insulator, and regularly check its integrity. By following these steps, composite insulators can be safely and effectively used in power transmission and distribution systems.
composite insulators Manufacturer,Supplier and Wholesale
A composite insulator is an insulating device that consists of an insulating core, housing, and end fittings. They are used to insulate high voltage electrical equipment from the ground, reducing the risk of electrical shock and damage. Composite insulators are more robust and durable than traditional porcelain insulators, making them ideal for use in harsh environments.
As a leading composite insulator manufacturer, supplier, and wholesale, we provide comprehensive solutions for electrical applications. Our insulators have been designed and tested to withstand extreme weather conditions, temperature fluctuations, and mechanical stresses. We use only the highest quality raw materials to ensure that our products meet international levels of quality and safety.
We offer a wide range of composite insulators, including suspension insulators, pin insulators, line post insulators, and railway insulators. Each of our products is designed to meet specific electrical requirements, providing reliable and cost-effective solutions for our customers.
Our team of experienced engineers and technicians work closely with our customers to understand their specific requirements and help them select the right composite insulator for their application. We offer custom designs and configurations to meet unique needs, ensuring optimal performance and safety.
We believe in providing our customers with the best value for their investment. Our competitive prices and high-quality products have made us one of the most trusted composite insulator manufacturers, suppliers, and wholesalers in the industry.
Contact us today to learn more about our products and services.

composite insulators Price
Composite insulators are commonly used in power transmission and distribution networks due to their advantages over traditional ceramic and porcelain insulators. Composite insulators are made up of a core made of a fiberglass reinforced plastic (FRP) rod, which is surrounded by a layer of silicone rubber insulation. These materials combine to provide a strong, reliable insulation solution that is resistant to environmental factors such as UV light, pollution, and insulator fatigue.
The price of composite insulators depends on several factors such as size, material quality, and manufacturer. Composite insulators are typically priced per unit and can range from $20 to $2000 or more, depending on the voltage rating of the insulator.
Low voltage composite insulators used in residential or commercial applications usually have a lower price point and range from $20 to $50 per unit. Medium voltage composite insulators are typically used in power distribution networks and can range from $100 to $500 per unit. High voltage composite insulators, on the other hand, are used in the transmission of power over long distances and can range from $500 to $2000 or more per unit.
In general, the price of composite insulators is higher compared to traditional ceramic and porcelain insulators. However, the benefits of composite insulators in terms of durability, reliability, and resistance to environmental factors make them a cost-effective choice in the long term.
In conclusion, the price of composite insulators can vary depending on the voltage rating, size, and material quality. The cost of composite insulators is higher compared to traditional ceramic and porcelain insulators, but the benefits of composite insulators make them a cost-effective choice in the long term.
FAQ sourcing composite insulators manufacturer from China with multiple answers
Q: What are composite insulators?
A: Composite insulators are used to support and insulate high voltage electrical power lines. They are made up of a core made of fiberglass reinforced plastic (FRP) or other composite material, and a weather-resistant outer coating.
Q: What are the benefits of using composite insulators?
A: Composite insulators are lightweight, which makes them easier to handle and install. They are also resistant to UV radiation, chemicals, and pollution, which makes them more durable than traditional insulators.
Q: Can I source composite insulators from China?
A: Yes, there are many composite insulator manufacturers in China. Some of the most well-known companies include Pingxiang Hualian, Zhejiang Gaoneng Electric Installation, and Guangzhou Diron Steelpole.
Q: How can I find a reliable composite insulator manufacturer in China?
A: You can search online for a list of manufacturers, and then research each company’s reputation and customer reviews. You can also ask for recommendations from other companies in your industry, or from trade associations.
Q: What should I look for when selecting a composite insulator manufacturer in China?
A: Look for a manufacturer that has experience producing high-quality composite insulators and has a good reputation for customer service. Make sure they can provide you with the certifications and testing reports necessary to ensure the insulators meet industry standards. Also, consider the manufacturer’s production capacity and lead times to ensure they can meet your production needs.
Q: Can I request a sample from a Chinese composite insulator manufacturer?
A: Yes, most manufacturers are happy to provide samples upon request. You will likely need to pay for the cost of the sample and shipping.
Q: What is the typical lead time for composite insulator production in China?
A: Lead times can vary depending on the manufacturer and the specific order, but the typical lead time for composite insulator production in China is 4-6 weeks.
Q: What is the payment process for ordering composite insulators from a Chinese manufacturer?
A: The payment process can vary, but most manufacturers will require a deposit or full payment upfront. Make sure you understand the payment terms and have a clear agreement in place before placing your order.
Overall, sourcing composite insulators from China can be a cost-effective option for businesses that require high-quality insulators in large quantities. It is important to research and vet potential manufacturers to ensure you receive a reliable product that meets your specific needs.