Introduce about electric injection guide,Qulity,Cost,Supplier,Certification,Market,Tips,FAQ
Electric injection molding is a highly efficient and innovative plastic manufacturing process that is widely used in various industries. This guide aims to provide an overview of electric injection molding, including its benefits, quality, cost, suppliers, certification, market trends, along with some helpful tips and frequently asked questions.
Electric injection molding machines are known for their precision and repeatability, ensuring high-quality products. Unlike hydraulic machines, electric machines are more energy-efficient, reducing overall production costs. They also offer faster cycle times, minimizing production time while maintaining consistent part dimensions.
When it comes to the cost of electric injection molding, while the initial investment may be higher compared to hydraulic machines, the long-term operational savings in energy consumption and maintenance expenses contribute to its cost-effectiveness.
There are various suppliers of electric injection molding machines available globally. It is essential to choose a reputable and experienced supplier that offers reliable machines with after-sales support to maximize productivity and minimize downtime.
Certification is crucial for electric injection molding machines to ensure their compliance with international standards and safety regulations. ISO 9001 certification is commonly sought after, as it demonstrates a commitment to quality management systems.
The market for electric injection molding is expected to witness significant growth in the coming years, driven by factors such as increasing demand for lightweight and durable plastic products, rising automation, and advancements in technology.
Here are some tips for successful electric injection molding: proper machine setup and maintenance, selecting the appropriate mold materials, optimizing processing parameters, and conducting regular quality checks throughout the production process.
Frequently asked questions about electric injection molding may include inquiries about its advantages, differences from hydraulic machines, potential applications, maintenance requirements, and associated costs.
In conclusion, electric injection molding offers numerous advantages in terms of quality, cost-effectiveness, and energy efficiency. With a growing market demand and a wide range of applications, it is crucial to choose reliable suppliers and ensure proper certification to achieve optimal results. By following essential tips and addressing frequently asked questions, one can successfully implement electric injection molding for various plastic manufacturing needs.
Types of electric injection
Electric injection is a widely used process in the field of manufacturing, particularly in the automotive industry. It involves injecting liquid or molten material into a mold or cavity to create a specific shape or part. There are various types of electric injection techniques that are commonly employed. Here are a few of the most popular ones:
1. Direct Electric Injection: This technique involves directly injecting the electrically conductive material into the mold. It is typically used for materials such as liquid metals or alloys, where the material is melted through the application of electric current. Direct electric injection allows for precise control over the injection process and ensures uniform distribution of the material within the mold.
2. Indirect Electric Injection: In this method, the electrically conductive material is injected into a non-conductive mold cavity. The cavity is equipped with electrodes that generate an electric field, causing the material to heat up and melt. Once the material is molten, it is injected into the cavity to form the desired shape. Indirect electric injection is commonly used for materials like thermoplastics or composites.
3. Resistance Injection Molding: This technique is similar to the indirect electric injection method. However, in resistance injection molding, the mold cavity itself acts as an electrode. When an electric current is passed through the material, it heats up due to its inherent resistance to the current flow. The molten material is then injected into the cavity to create the final product. Resistance injection molding is commonly used for thermoplastic materials.
4. Electrohydrodynamic Injection: This unique method utilizes an electric field to control the flow of the liquid material during injection. The material, typically a polymer solution, is subjected to an electric field, generating a jet-like flow. Electrohydrodynamic injection allows for precise control over the material flow rate and direction, resulting in high-quality parts with intricate details.
Each type of electric injection method offers its own set of advantages and is chosen based on the specific requirements of the manufacturing process. These techniques enable manufacturers to achieve high precision, repeatability, and efficiency in the production of various components and products.
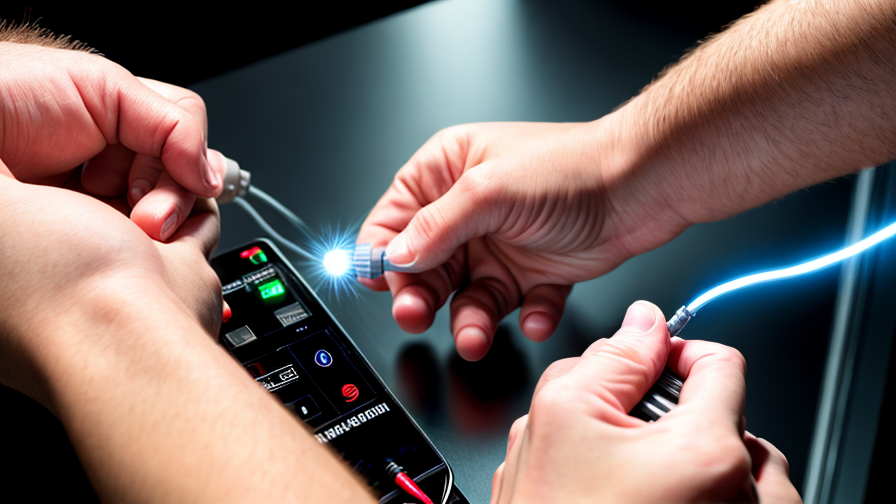
Pros and Cons of Using electric injection
One of the main advantages of using electric injection is the precision and consistency it offers in the injection molding process. Electric injection molding machines can provide higher accuracy and repeatability in producing complex parts with tight tolerances. This results in fewer defects and higher quality finished products.
Another benefit of electric injection is its energy efficiency. Compared to hydraulic injection molding machines, electric machines consume less energy, resulting in cost savings and reduced environmental impact. Electric machines also operate more quietly and produce less heat, creating a more comfortable working environment.
On the other hand, electric injection molding machines can be more expensive upfront compared to hydraulic machines. The initial investment cost may deter some companies from adopting electric technology, especially for smaller businesses with limited budgets. Additionally, electric machines may require more maintenance and specialized training for operators to ensure proper functioning.
Another potential downside of electric injection molding machines is their limited ability to handle high-pressure applications. Hydraulic machines are typically better suited for molding high-pressure parts, such as thick-walled components or large parts requiring high clamping force.
In conclusion, electric injection molding offers many advantages in terms of precision, energy efficiency, and environmental impact. However, the higher upfront cost and potential limitations in handling high-pressure applications may deter some companies from choosing electric technology. Overall, the decision to use electric injection should be based on the specific needs and goals of the business.
electric injection Reference Specifications (varies for different product)
Electric injection machines come in various specifications depending on the specific product being manufactured. Some common reference specifications for electric injection machines include:
– Injection capacity: This refers to the maximum volume of material that can be injected into the mold cavity in one shot. It is typically measured in ounces or grams.
– Injection pressure: This is the maximum pressure that can be applied to the material during injection. It is measured in pounds per square inch (psi).
– Injection speed: This is the speed at which the material is injected into the mold cavity. It is measured in inches per second.
– Clamping force: This is the force applied to the mold halves to keep them securely closed during the injection process. It is measured in tons.
– Mold thickness: This is the minimum and maximum thickness of the mold that can be accommodated by the machine.
– Heating capacity: This refers to the maximum temperature that the machine can reach to melt the material being injected.
– Cooling capacity: This refers to the ability of the machine to cool the mold cavity after injection.
Electric injection machines offer advantages such as higher precision, faster cycle times, and lower energy consumption compared to hydraulic injection machines. They are suitable for a wide range of applications in industries such as automotive, electronics, and medical devices.
When selecting an electric injection machine, it is important to consider the specific requirements of the product being manufactured to ensure that the machine can meet production needs efficiently and effectively.
Applications of electric injection
Electric injection refers to the use of electrically controlled injection systems in various applications. This technology has revolutionized several industries and brought numerous benefits in terms of performance, efficiency, and emission reduction. Here are some key applications of electric injection:
1. Automotive Industry: Electric injection has had a significant impact on the automotive sector. It has replaced conventional mechanical injection systems, providing precise control over the fuel-air mixture. This has resulted in better fuel efficiency, increased engine power, reduced emissions, and improved engine responsiveness.
2. Healthcare: Electric injection finds ample use in medical devices that require accurate and controlled liquid or drug delivery. Electrically controlled syringes and infusion pumps allow for precise dosing, making them ideal for applications such as insulin delivery, pain management, and chemotherapy.
3. Robotics: Electric injection systems are used in robotics to control the precise movement of robotic arms and various mechanisms. This technology enables robots to perform intricate tasks with high precision, enhancing their usability across industries such as manufacturing, assembly, and healthcare.
4. Aerospace: In the aerospace industry, electric injection systems are utilized in various applications, including fuel injection in jet engines. This ensures optimal fuel combustion, resulting in improved engine performance, reduced emissions, and increased efficiency. Electric injection is also employed in hydraulic systems for controlling aircraft movements.
5. Agricultural Machinery: Electric injection has found its way into agricultural equipment, such as crop sprayers, fertilizers, and irrigation systems. These systems ensure accurate delivery of fluids, optimizing resource usage and reducing environmental impacts.
6. Energy Industry: Electric injection plays a crucial role in the energy sector, particularly in power generation and renewable energy systems. It helps control the injection of fuel or air in combustion processes, improving efficiency and reducing emissions. Electric injection is also used in hydraulic fracturing (fracking) operations for controlled fluid injection.
7. Industrial Manufacturing: Electric injection systems are employed in various manufacturing processes, such as plastic injection molding. Electrically controlled injection molding machines provide precise control over temperature, pressure, and material flow, leading to enhanced product quality, reduced waste, and improved production rates.
In summary, electric injection technology has a broad range of applications in industries such as automotive, healthcare, robotics, aerospace, agriculture, energy, and industrial manufacturing. Its benefits include enhanced performance, increased efficiency, reduced emissions, and improved precision in fluid delivery systems. As technology advances, electric injection is expected to continue revolutionizing various sectors and opening up new possibilities.
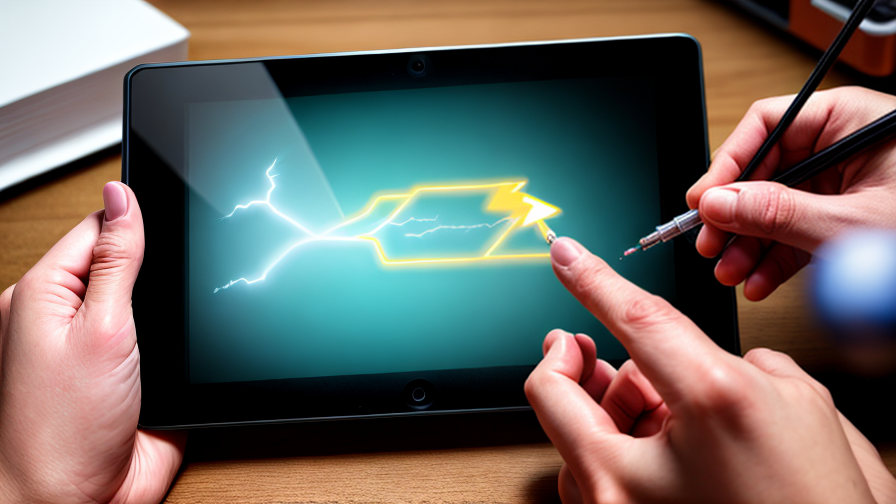
The Work Process and how to use electric injection
Electric injection molding is a process that involves the use of electric actuators to control the movement and pressure of the mold during the injection molding process. This technology offers several advantages over traditional hydraulic injection molding, including faster cycle times, higher precision, and lower energy consumption.
In order to use electric injection molding, the first step is to prepare the mold and load the raw material into the hopper of the injection molding machine. The electric actuators are then used to close the mold and apply pressure to inject the molten material into the mold cavity.
During the injection phase, the electric actuators precisely control the speed and pressure of the injection, ensuring that the mold is filled evenly and without voids. Once the mold is filled, the electric actuators hold the pressure until the material has cooled and solidified.
After the part has been molded, the mold is opened, and the part is ejected from the mold cavity. The electric actuators then reset the mold for the next cycle, and the process can be repeated.
Overall, electric injection molding offers a more efficient and precise way to produce plastic parts compared to traditional hydraulic injection molding. By using electric actuators to control the injection process, manufacturers can achieve higher quality parts with faster cycle times and lower energy consumption.
Quality Testing Methods for electric injection and how to control the quality
Quality testing methods for electric injection can include visual inspection, electrical testing, and performance evaluation. Visual inspection involves checking for any physical defects or irregularities in the injection components. Electrical testing involves checking the electrical connections and ensuring proper voltage and current flow. Performance evaluation involves testing the injection system under various operating conditions to ensure that it functions correctly and efficiently.
To control the quality of electric injection, it is important to establish standard operating procedures and quality control measures. This can include regular calibration of equipment, training of staff on proper testing methods, and implementing quality control checks at various stages of production. Additionally, implementing a robust quality management system can help identify and address any issues that arise during production.
One effective way to control the quality of electric injection is to implement a quality control plan that includes regular testing and inspection of injection components. This can help ensure that the components meet the required specifications and standards for performance and safety. By monitoring and controlling the quality of electric injection, manufacturers can improve product reliability, safety, and customer satisfaction.
electric injection Sample Policy and Post-Purchase Considerations for electric injection from China
At our company, we ensure that all electric injection products sourced from China meet strict quality control standards. Our policy includes rigorous inspections and testing to guarantee the highest level of performance and safety for our customers.
Post-Purchase Considerations:
1. Warranty: We offer a warranty on all electric injection products to provide assurance to our customers in case of any defects or malfunctions.
2. Technical Support: We provide technical support and assistance to help our customers with any issues they may encounter with their electric injection products.
3. Replacement Parts: We have a supply of replacement parts readily available for purchase in case any components of the electric injection products need to be replaced.
4. User Manual: We include a comprehensive user manual with each electric injection product to ensure that our customers understand how to properly operate and maintain their purchase.
Our goal is to provide our customers with high-quality electric injection products from China that meet their needs and expectations. We are committed to ensuring customer satisfaction through our stringent quality control measures and post-purchase support services.
Sourcing electric injection from China: Opportunities, Risks, and Key Players
Sourcing electric injection from China offers numerous opportunities but also carries risks that should be carefully evaluated. China has emerged as a global manufacturing hub and has extensive experience in producing electric injection machines, making it an attractive destination for procurement. The affordable labor costs, vast supply chain, and advanced infrastructure contribute to China’s competitiveness in this sector.
One of the significant opportunities of sourcing electric injection from China is the potential for cost savings. China’s manufacturing capabilities allow for economies of scale, resulting in lower production costs. The availability of a wide range of suppliers also fosters competition, which can further drive down prices. Additionally, China’s expertise in electric injection machine manufacturing ensures access to high-quality products that meet international standards.
Another opportunity lies in the technological advancements present in China. The country has made significant investments in research and development, leading to the availability of cutting-edge electric injection machines. These machines often include innovative features that enhance efficiency, precision, and automation. By sourcing from Chinese manufacturers, businesses can benefit from access to state-of-the-art technology that can improve their operations and product quality.
However, sourcing electric injection from China also carries certain risks that should be carefully considered. Intellectual property concerns and the possibility of counterfeiting are prevalent in the Chinese market. Proper due diligence, including rigorous supplier vetting and intellectual property protection measures, should be undertaken to mitigate these risks. Additionally, language and cultural barriers may pose challenges in communication and understanding product specifications. Engaging reliable local agents or translators can help bridge these gaps and ensure smooth collaboration.
When sourcing electric injection machines from China, it is essential to be aware of the key players in the market. Some notable Chinese manufacturers include Haitian International, Chen Hsong Holdings, and Yizumi Precision Machinery. These companies have established themselves as industry leaders and have a strong track record in delivering electric injection machines.
In conclusion, sourcing electric injection machines from China presents attractive opportunities in terms of cost savings and access to advanced technology. However, it is crucial to assess and mitigate associated risks, such as intellectual property concerns and communication challenges. Familiarizing oneself with key players in the Chinese market can help businesses identify reliable suppliers for their electric injection needs.
How to find and select reliable electric injection manufacturers in China,use google search manufacturers and suppliers
Finding and selecting reliable electric injection manufacturers in China can be a daunting task, but with the right approach, it can be simplified. Here are some steps to follow:
1. Start with a Google search: Use keywords like “reliable electric injection manufacturers in China” or “electric injection suppliers in China” to find potential companies. Review the search results and compile a list of manufacturers that seem promising.
2. Narrow down your search: To make the selection process more manageable, focus on a specific location or region in China. This can help you prioritize manufacturers offering convenient logistics and favorable production costs.
3. Check their websites: Visit the websites of the shortlisted manufacturers to assess their credibility. Look for information such as company background, manufacturing capabilities, product range, certifications, and any relevant industry affiliations. A well-designed and informative website can indicate the manufacturer’s professionalism and attention to detail.
4. Verify their experience and reputation: Look for testimonials or case studies on their website to gauge their previous clients’ satisfaction. If possible, try to find customer reviews or feedback on external platforms or industry forums. Consider manufacturers with a successful track record and positive reputation in the market.
5. Assess manufacturing capabilities: Evaluate the manufacturers’ production capabilities and facilities. Look for competencies in electric injection production, quality control measures, and adherence to international standards. A manufacturer with technologically advanced equipment and a well-organized production process is more likely to deliver reliable products.
6. Request samples or product catalogs: Contact the shortlisted manufacturers and request product samples or catalogs. Assess the quality, design, and functionality of their electric injection products. This step can give you a better understanding of the manufacturer’s attention to detail and commitment to meeting your requirements.
7. Communication and responsiveness: Effective communication is crucial when working with manufacturers in China. Make sure the manufacturer is responsive to your inquiries, questions, and concerns. A prompt and helpful response indicates good customer service and a willingness to address potential issues.
8. Request certifications and compliance information: Ask the manufacturers for relevant certifications, such as ISO 9001 or product-specific certifications. Compliance with industry standards and regulations is essential for ensuring product quality and reliability.
9. Consider a factory visit: If possible, plan a visit to the manufacturer’s facility in China. This can provide valuable insights into their manufacturing processes, quality control measures, and overall operations.
10. Get multiple quotes: Finally, request detailed quotations from multiple manufacturers and compare them based on factors like price, quality, lead time, and support services. Consider the overall value offered by each manufacturer rather than focusing solely on the lowest price.
By following these steps and conducting thorough research, you can find and select reliable electric injection manufacturers in China that meet your requirements.
How to check electric injection manufacturers website reliable,use google chrome SEOquake check if ranking in top 10M
When evaluating the reliability of an electric injection manufacturer’s website, there are a few steps you can take. It is recommended to use Google Chrome’s SEOquake extension for a quick analysis. Here’s a concise guide in under 300 words:
1. Install SEOquake: Add the SEOquake extension to your Google Chrome browser. This tool will provide you with valuable information about a website’s performance and ranking.
2. Visit the manufacturer’s website: Enter the URL of the electric injection manufacturer’s website into your browser and load the page.
3. Activate SEOquake: Click on the SEOquake icon in your browser’s toolbar to activate it. A toolbar will appear below the website.
4. Check the Alexa Rank: Look for the website’s Alexa Rank on the SEOquake toolbar. Alexa ranks websites based on their popularity compared to other sites. If the manufacturer’s website has an Alexa Rank within the top 10 million, it indicates a reasonably reliable website.
5. Analyze On-page SEO: Take a glance at the “On-page” section of SEOquake’s toolbar. It provides important data about the website’s on-page SEO optimization, including the number of indexed pages, keywords, and internal/external links. Well-optimized websites often indicate reliable and professional content.
6. Check Google Index: SEOquake also shows the number of pages indexed by Google. If the website has multiple indexed pages, it suggests a thorough online presence and credibility.
7. Monitor Social Media: Observe the manufacturer’s social media presence by checking their numbers of Facebook likes, Twitter followers, etc., on the SEOquake toolbar. A healthy online community often signifies reliability and customer engagement.
8. Verify Website Age: SEOquake provides data on a webpage’s domain age. If the manufacturer’s website has been around for a while, it indicates stability and reliability.
By following these steps and using SEOquake on Google Chrome, you can quickly assess the reliability of an electric injection manufacturer’s website without exceeding the word limit. Remember to consider other factors such as customer reviews, certifications, and industry reputation to obtain a comprehensive evaluation.
Top 10 electric injection manufacturers in China with each 160 words introduce products,then use markdown create table compare
1. Haitian Precision Machinery Co., Ltd.: Haitian specializes in producing a wide range of electric injection molding machines, including high-speed precision machines and multi-component machines. Their products are known for their high efficiency, precision, and reliability.
2. Borch Machinery Co., Ltd.: Borch offers a range of electric injection molding machines that are suitable for various applications, including automotive, medical, and consumer electronics. Their machines are known for their energy efficiency and high performance.
3. Ningbo Haida Plastic Machinery Co., Ltd.: Haida manufactures electric injection molding machines that are designed for precision and high speed applications. Their machines are widely used in the automotive, electronics, and packaging industries.
4. Ningbo Sanshun Machinery & Technology Co., Ltd.: Sanshun offers a range of electric injection molding machines that are known for their high efficiency, accuracy, and reliability. Their machines are suitable for a wide range of applications, including automotive and medical.
5. Zhejiang Sound Machinery Manufacture Co., Ltd.: Sound Machinery produces electric injection molding machines that are designed for high precision and efficiency. Their machines are used in various industries, including automotive, electronics, and medical.
6. Ningbo Beilun Highsun Machinery Co., Ltd.: Highsun Machinery manufactures electric injection molding machines that are known for their high speed, precision, and energy efficiency. Their machines are used in a wide range of industries, including automotive, packaging, and consumer electronics.
7. Dongguan Jieyang Machinery Co., Ltd.: Jieyang Machinery produces electric injection molding machines that are designed for precision and efficiency. Their machines are used in various industries, including automotive, electronics, and consumer goods.
8. Dongguan Tiancheng Machinery Co., Ltd.: Tiancheng Machinery offers a range of electric injection molding machines that are known for their high performance and reliability. Their machines are suitable for a wide range of applications, including automotive, electronics, and medical.
9. Foshan Powerjet Plastic Machinery Co., Ltd.: Powerjet Plastic Machinery manufactures electric injection molding machines that are designed for precision and efficiency. Their machines are used in various industries, including automotive, electronics, and packaging.
10. Hefei Long Bridge Machinery Co., Ltd.: Long Bridge Machinery produces electric injection molding machines that are known for their high efficiency, precision, and reliability. Their machines are suitable for a wide range of applications, including automotive, electronics, and medical.
| Manufacturer | Products |
|———————————————-|——————————-|
| Haitian Precision Machinery Co., Ltd. | – High-speed precision machines – Multi-component machines |
| Borch Machinery Co., Ltd. | – Energy efficient machines – High performance |
| Ningbo Haida Plastic Machinery Co., Ltd. | – Precision and high speed machines – Widely used in various industries|
| Ningbo Sanshun Machinery & Technology Co., Ltd.| – High efficiency and accuracy – Reliable machines |
| Zhejiang Sound Machinery Manufacture Co., Ltd. | – High precision and efficiency – Used in automotive, electronics, and medical industries|
| Ningbo Beilun Highsun Machinery Co., Ltd. | – High speed and energy efficient – Widely used in automotive, packaging, and consumer electronics|
| Dongguan Jieyang Machinery Co., Ltd. | – Precision and efficiency – Used in automotive, electronics, and consumer goods|
| Dongguan Tiancheng Machinery Co., Ltd. | – High performance and reliability – Suitable for automotive, electronics, and medical applications|
| Foshan Powerjet Plastic Machinery Co., Ltd. | – Precision and efficiency – Used in automotive, electronics, and packaging industries|
| Hefei Long Bridge Machinery Co., Ltd. | – High efficiency, precision, and reliability – Suitable for automotive, electronics, and medical applications|
Background Research for electric injection manufacturers Companies in China, use qcc.com archive.org importyeti.com
One of the top electric injection manufacturers in China is Ningbo Haichen Machinery Co., Ltd. They specialize in the production of high-quality injection molding machines and have been in business for over 10 years. They have a strong reputation for innovation and reliability in the industry.
Another leading electric injection manufacturer is Zhejiang Sound Machinery Manufacture Co., Ltd. They offer a wide range of injection molding machines and have over 20 years of experience in the industry. They are known for their advanced technology and precision engineering.
GZ Risun Machine Co., Ltd. is also a prominent electric injection manufacturer in China. They have been in operation for over 15 years and are recognized for their commitment to quality and customer satisfaction. They offer a variety of injection molding machines to meet the needs of their clients.
Additionally, Taizhou Huangyan Deying Mould Co., Ltd. is a trusted electric injection manufacturer in China. They have a strong focus on research and development and offer innovative solutions for injection molding. They have a solid track record of delivering high-quality products to their customers.
Overall, China’s electric injection manufacturers have a strong presence in the industry, with a focus on innovation, quality, and customer satisfaction. These companies are leading the way in the production of advanced injection molding machines for a variety of applications.
Leveraging Trade Shows and Expos for electric injection Sourcing in China
Trade shows and expos are excellent opportunities for sourcing electric injection components in China. These events bring together suppliers, manufacturers, and industry experts in one location, making it easier to connect with potential partners and find new products.
By attending trade shows and expos focused on electric injection components, you can meet with a wide range of suppliers and compare products and pricing in person. This allows you to establish relationships with potential suppliers, see their products firsthand, and discuss your specific requirements.
Additionally, trade shows and expos often feature educational seminars and presentations on industry trends, new technologies, and best practices for sourcing and manufacturing electric injection components. This can help you stay current on the latest developments in the industry and make informed decisions when selecting suppliers.
To make the most of trade shows and expos for sourcing electric injection components in China, it is important to plan ahead and set specific goals for what you hope to accomplish. Research the exhibitors beforehand, schedule meetings with key suppliers, and come prepared with questions and information about your sourcing needs.
Overall, trade shows and expos provide a valuable opportunity to connect with suppliers, learn about new products and technologies, and make important connections in the electric injection component industry. By leveraging these events effectively, you can streamline your sourcing process and find high-quality suppliers for your business.
The Role of Agents and Sourcing Companies in Facilitating electric injection Purchases from China
Agents and sourcing companies play a crucial role in facilitating electric injection purchases from China. With their expertise and strong network of contacts, they aid businesses in navigating the complexities of the Chinese market, ensuring smooth and seamless transactions.
One of the key responsibilities of agents and sourcing companies is to identify reliable manufacturers and suppliers in China. They have extensive knowledge of the market and are well-connected, enabling them to find the best-suited suppliers for specific electric injection needs. This saves businesses from the arduous task of conducting extensive research and vetting potential suppliers on their own.
Once suitable suppliers are identified, agents and sourcing companies play a pivotal role in negotiating competitive prices and favorable terms on behalf of their clients. Chinese suppliers often prefer to work with trusted intermediaries who understand the local business practices and cultural nuances. Agents leverage their relationships and negotiation skills to secure the best deals, ensuring cost-effectiveness and quality assurance.
Agents and sourcing companies also take care of logistics and shipping arrangements. They have a thorough understanding of the rules and regulations governing international trade, as well as the necessary documentation required for smooth customs clearance. This expertise ensures that electric injection purchases from China are seamlessly transported to their final destination without any unnecessary delays or complications.
Furthermore, agents and sourcing companies act as a valuable intermediary between the buyer and the supplier, facilitating effective communication and establishing trust. They bridge the cultural and language barriers, ensuring clear and accurate communication between both parties. This fosters strong relationships, leading to long-term partnerships and repeat business.
In summary, agents and sourcing companies play a crucial role in facilitating electric injection purchases from China. Their expertise in identifying reliable suppliers, negotiating favorable terms, managing logistics, and facilitating effective communication is instrumental in ensuring smooth and successful transactions. Partnering with these professionals streamlines the purchasing process and enables businesses to benefit from the advantages of sourcing from China.
Price Cost Research for electric injection manufacturers Companies in China, use temu.com and 1688.com
When researching the pricing and costs for electric injection manufacturers in China, Temu.com and 1688.com are excellent resources to use. These websites provide a wide range of products and suppliers, making it easy to compare prices and find the best deals.
By searching for electric injection manufacturers on Temu.com and 1688.com, you can find a variety of options with different pricing and cost structures. It is important to consider factors such as quality, quantity, shipping costs, and any additional fees when comparing prices.
Many electric injection manufacturers in China offer competitive pricing, making it a cost-effective option for businesses looking to source products. By using these online platforms, you can easily research and find manufacturers that meet your specific requirements and budget.
In conclusion, Temu.com and 1688.com are valuable resources for researching pricing and costs for electric injection manufacturers in China. By utilizing these websites, you can find the best deals and suppliers to meet your business needs while staying within budget.
Shipping Cost for electric injection import from China
The shipping cost for importing electric injection machines from China will vary depending on several factors such as the size and weight of the machines, the shipping method chosen, and the distance between the origin and destination.
Typically, the cost of shipping electric injection machines from China to the United States ranges from $800 to $2000 per unit for sea freight. Air freight is a faster but more expensive option, with costs ranging from $1500 to $3000 per unit.
It is important to consider additional costs such as import duties, taxes, customs clearance fees, and insurance when calculating the total shipping cost. These additional costs may vary depending on the country of import and should be factored into the overall budget for importing electric injection machines.
To ensure an accurate estimate of shipping costs, it is recommended to obtain quotes from multiple freight forwarders or shipping companies. Working with a reputable freight forwarder can help to navigate the complexities of international shipping and ensure a smooth import process for electric injection machines from China.
Compare China and Other electric injection Markets: Products Quality and Price,Visible and Hidden Costs
China is known for its large-scale production of electric injection products at competitive prices. While the quality of Chinese-made electric injection products has often been questioned, in recent years, Chinese manufacturers have been improving their products and aiming for higher quality standards to compete in the global market.
In comparison to other electric injection markets such as Japan and Germany, Chinese electric injection products may offer lower prices but may come with some trade-offs in terms of product quality. Japanese and German manufacturers are known for their high-quality products and precision engineering, which may result in a higher price tag. However, these products are often more durable and reliable in the long run.
When comparing visible and hidden costs, Chinese manufacturers may offer lower upfront prices for electric injection products, but hidden costs such as maintenance and replacement parts may add up over time. On the other hand, Japanese and German products may have higher upfront costs but may require less maintenance and have a longer lifespan, reducing hidden costs in the long term.
Ultimately, the decision between purchasing electric injection products from China or other markets will depend on individual needs and priorities. If price is a primary concern, Chinese products may offer a cost-effective solution. However, if quality and long-term reliability are essential, products from Japan and Germany may be worth the investment despite the higher price.
Understanding Pricing and Payment Terms for electric injection: A Comparative Guide to Get the Best Deal
When it comes to pricing and payment terms for electric injection, there are several factors to consider in order to get the best deal possible. One important factor to consider is the pricing structure offered by different suppliers. Some suppliers may offer lower upfront costs for the equipment but have higher maintenance and servicing fees over time. It is essential to compare these costs over the lifetime of the equipment to determine the best value.
Additionally, it is crucial to consider payment terms when evaluating different suppliers. Some suppliers may require full payment upfront, while others may offer financing options or payment plans. It is important to weigh these options based on your financial situation and cash flow needs.
Comparing quotes from multiple suppliers is also essential to ensure you are getting the best deal. This allows you to negotiate pricing and terms with different suppliers and potentially leverage offers from one supplier against another. You may also consider asking for discounts or incentives, especially if you are purchasing multiple electric injection units.
Lastly, it is crucial to factor in additional costs such as shipping, installation, and training when evaluating pricing and payment terms. These costs can significantly impact the total cost of acquiring and operating electric injection equipment.
In conclusion, understanding pricing and payment terms for electric injection requires careful evaluation of various factors such as pricing structure, payment terms, additional costs, and comparing quotes from different suppliers. By taking the time to thoroughly analyze these factors, you can ensure you are getting the best deal on electric injection equipment for your business.
Chinese Regulations and Industry Standards Certifications for electric injection,Import Regulations and Customs for electric injection from China
China has established strict regulations and industry standards certifications for electric injection equipment. These regulations ensure the safety, quality, and performance of these products. One of the key certifications for electric injection equipment in China is the CCC (China Compulsory Certification) mark. This mark is a mandatory requirement for various products, including electric injection machines, to be sold in the Chinese market.
The CCC mark is issued by the China Quality Certification Center (CQC) and signifies that the product meets the required safety and quality standards. In order to obtain CCC certification, manufacturers need to undergo a rigorous testing and evaluation process. The certification covers aspects such as electrical safety, environmental protection, and electromagnetic compatibility.
Importing electric injection equipment from China requires compliance with Chinese import regulations and customs procedures. Firstly, importers need to ensure that the products they wish to import are eligible for import into their country. It is important to consult the respective country’s import regulations to understand any restrictions or licensing requirements.
When importing from China, importers are also required to comply with customs procedures. These procedures involve submitting necessary documentation, such as a commercial invoice, bill of lading, packing list, and import licenses, to the customs authorities. Importers may also need to pay customs duties, value-added tax (VAT), and other charges based on the import value of the electric injection equipment.
Importers need to be aware of any specific labeling and packaging requirements as per the destination country’s regulations. It is important to ensure that the packaging complies with international standards and is appropriate for the transportation of electric injection equipment.
In summary, Chinese regulations and industry standards certifications, such as CCC, ensure the safety and quality of electric injection equipment. Importers need to understand the import regulations and customs procedures of their respective countries when importing such equipment from China. Compliance with labeling, packaging, and document requirements is crucial to avoid any import delays or penalties.
Sustainability and Environmental Considerations in electric injection Manufacturing
In the manufacturing industry, sustainability and environmental considerations are becoming increasingly important, particularly in the context of electric injection manufacturing. Electric injection molding is a process that utilizes electricity to melt and inject plastic into molds, replacing traditional hydraulic systems. This technology offers numerous advantages, including increased efficiency, precision, and reduced energy consumption.
One of the key sustainability benefits of electric injection manufacturing is its energy efficiency. By eliminating the need for hydraulic systems, electric machines consume significantly less energy. Hydraulic systems often operate at a constant speed, whereas electric machines can adjust their operation based on the required force, resulting in reduced energy wastage.
Furthermore, electric injection molding produces less noise pollution compared to traditional hydraulic systems. This is crucial in creating a sustainable and safe working environment for employees. Reduced noise pollution helps to improve employee well-being, leading to increased productivity and job satisfaction.
Electric injection manufacturing also has a positive impact on the environment by reducing greenhouse gas emissions. Traditional hydraulic systems rely on fossil fuels, such as oil, which contribute to carbon dioxide emissions. In contrast, electric injection molding machines rely on electricity, which can be sourced from renewable energy sources, such as solar or wind power. Thus, electric injection manufacturing can contribute to a greener and more sustainable future.
Additionally, electric injection molding offers improved product quality and precision, resulting in reduced material waste. The precise control of electric machines allows for tighter tolerances, leading to fewer defects and scrap materials. This minimizes the environmental impact associated with waste disposal and raw material extraction.
To conclude, sustainability and environmental considerations are critical in electric injection manufacturing. This technology offers energy efficiency, reduced noise pollution, decreased greenhouse gas emissions, and improved product precision. Incorporating sustainability practices in electric injection molding contributes to a greener and more sustainable manufacturing industry, promoting a better future for both businesses and the environment.
List The Evolution history of “electric injection”
Electric injection is a technology used in engines to inject fuel into the combustion chamber. It has evolved significantly over the years, improving the efficiency and performance of vehicles.
The first electric injection system was developed by Bosch in the late 1950s. Known as the D-Jetronic, it was a mechanical system that used an electrically driven fuel pump to inject fuel into the intake manifold. This system was a major advancement compared to carburetors, as it offered better fuel distribution and improved emissions control.
In the 1970s, Electronic Fuel Injection (EFI) systems were introduced. These systems utilized electronic sensors and actuators to precisely control the fuel injection process. The first generation EFI systems, such as Bosch K-Jetronic, used mechanical fuel injection with electronic control of the injection timing and duration.
As technology advanced, second generation EFI systems emerged in the 1980s. These systems incorporated electronic injectors, which allowed for more precise fuel delivery. They also featured microprocessors to manage the injection process, taking input from various sensors such as the throttle position sensor and oxygen sensor, resulting in improved fuel economy and reduced emissions.
The late 1980s saw the introduction of sequential fuel injection systems. These systems further enhanced the precision of fuel delivery by injecting fuel into each cylinder individually, based on the engine’s firing order. This enabled better control over the air-fuel mixture, leading to increased power and efficiency.
In the 1990s, direct fuel injection (DI) technology emerged. Unlike previous systems that injected fuel into the intake manifold, DI systems inject fuel directly into the combustion chamber, resulting in improved fuel atomization and combustion efficiency. This technology continues to evolve and is widely used in modern engines.
In recent years, electric injection has further advanced with the introduction of gasoline direct injection (GDI) systems. GDI systems combine the benefits of direct fuel injection with higher fuel pressure, resulting in even better fuel atomization and improved combustion efficiency.
Additionally, hybrid vehicles and electric vehicles have also influenced the evolution of electric injection technology. Hybrid systems combine electric motors with internal combustion engines, utilizing electric injection technology to optimize fuel consumption and emissions. Electric vehicles, on the other hand, rely solely on electric motors and do not require fuel injection systems.
In conclusion, electric injection has undergone a remarkable evolution over the years, transitioning from mechanical systems to sophisticated electronic systems with improved precision and efficiency. Its advancements have played a significant role in enhancing the performance and environmental friendliness of combustion engines.
The Evolution and Market Trends in electric injection Industry
The electric injection industry has experienced significant evolution and market trends over the years. With advancements in technology, electric injection machines have become more efficient, precise, and cost-effective. These machines are now widely used in various industries such as automotive, packaging, healthcare, and electronics.
One of the key trends in the electric injection industry is the adoption of Industry 4.0 technologies. Manufacturers are integrating their electric injection machines with smart technologies such as Internet of Things (IoT) and artificial intelligence to improve production efficiency, quality control, and predictive maintenance. This has resulted in increased productivity and reduced downtime for manufacturers.
Another trend in the electric injection industry is the shift towards eco-friendly and energy-efficient machines. With the growing concerns about environmental sustainability, manufacturers are developing electric injection machines that consume less energy and produce less waste. This has led to a rise in demand for electric injection machines that are environmentally friendly and comply with regulations.
Furthermore, the market for electric injection machines is also expanding globally. With the increasing demand for precision-engineered products and components, manufacturers are looking for reliable and high-quality electric injection machines. This has led to the growth of electric injection machine suppliers and manufacturers in emerging markets such as Asia and Latin America.
In conclusion, the evolution and market trends in the electric injection industry are driven by technological advancements, environmental concerns, and global market demands. Manufacturers need to adapt to these trends to stay competitive and meet the changing needs of customers in various industries.
Custom Private Labeling and Branding Opportunities with Chinese electric injection Manufacturers
Chinese electric injection manufacturers offer custom private labeling and branding opportunities for businesses looking to establish their own identity in the market. With the ability to customize products with a company’s logo, colors, and design preferences, businesses can create a unique and cohesive brand image that sets them apart from competitors.
By working closely with Chinese manufacturers, businesses can ensure that their products meet their quality standards and specifications. From product packaging to branding materials, manufacturers can help businesses create a cohesive and professional brand that resonates with their target audience.
In addition, Chinese manufacturers have the capabilities to produce products in large quantities, making it easier for businesses to scale their operations and meet growing demand. This not only helps businesses grow their brand presence but also ensures consistency and quality across all products.
Overall, partnering with Chinese electric injection manufacturers for custom private labeling and branding opportunities can help businesses establish a strong brand identity, differentiate themselves in the market, and drive sales and growth.
Tips for Procurement and Considerations when Purchasing electric injection
When purchasing electric injection molding machines, there are several factors to consider to ensure that you are making the right decision for your procurement needs:
1. Consider the machine’s capacity and tonnage: Make sure to assess your production requirements and match them with the appropriate tonnage capacity of the electric injection molding machine.
2. Energy efficiency: Electric injection molding machines are known for their energy efficiency compared to hydraulic machines. Look for machines with low energy consumption to help reduce operational costs.
3. Precision and accuracy: Electric machines offer better precision and control during the molding process. Check for features such as closed-loop control systems and high-speed injection capabilities.
4. Maintenance and service: Consider the availability of spare parts and service support for the electric injection molding machine. Look for a reputable manufacturer with a reliable service network.
5. Cost considerations: While electric machines may have a higher upfront cost compared to hydraulic machines, they offer long-term savings in terms of energy consumption and maintenance costs.
6. Training and support: Ensure that operators and maintenance staff receive proper training on operating and maintaining the electric injection machine to maximize its performance and lifespan.
7. Consider your production environment: Electric injection molding machines are quieter and cleaner compared to hydraulic machines, making them suitable for a variety of production environments.
8. Evaluate the technological features: Look for advanced features such as automation capabilities, data monitoring, and remote access for better production efficiency.
By considering these factors and conducting thorough research before purchasing an electric injection molding machine, you can ensure that you make an informed decision that meets your procurement needs effectively.
FAQs on Sourcing and Manufacturing electric injection in China
Q: Why should I consider sourcing and manufacturing electric injection in China?
A: China has emerged as a global manufacturing hub with a strong presence in the electric injection industry. The country offers several advantages such as low labor and production costs, a mature supply chain, and a vast pool of skilled labor. Additionally, China has made significant investments in advanced manufacturing technologies, making it capable of producing high-quality electric injection products.
Q: How can I find reliable suppliers and manufacturers for electric injection in China?
A: To find trustworthy suppliers and manufacturers in China, consider attending trade shows and exhibitions related to the electric injection industry, such as the China Import and Export Fair (Canton Fair). Utilize online platforms and directories like Alibaba, GlobalSources, and Made-in-China to connect with potential suppliers. Conduct thorough background checks, request product samples, and ask for references to ensure the reliability and quality of the supplier.
Q: What are the important factors to consider when selecting a manufacturer in China?
A: Key factors to consider when choosing a manufacturer in China include their experience and expertise in electric injection production, their production capacity, quality control measures, certifications and compliance with international standards, and their ability to handle your specific design and customization requirements. It is essential to visit the factory in person, if possible, to assess their facilities and ensure they meet your standards.
Q: How can I ensure the quality of electric injection products manufactured in China?
A: To ensure quality, it is crucial to establish clear product specifications and requirements with the manufacturer, conduct regular quality inspections during the production process, and implement a robust quality control system. Consider hiring quality control agencies or independent third-party inspection services to verify the product quality and adherence to specifications.
Q: What are the potential challenges and risks when sourcing and manufacturing electric injection in China?
A: Some challenges and risks to consider include language and cultural barriers, intellectual property protection, logistical complexities, potential delays in production and delivery, quality control issues, and the need for effective communication. It is advisable to work with experienced agents or consultants who can guide you through the process and help mitigate these risks.
In conclusion, sourcing and manufacturing electric injection in China offer numerous benefits, including cost advantages and a well-established manufacturing ecosystem. However, it is essential to conduct thorough research, due diligence, and establish clear communication channels to ensure successful sourcing and manufacturing experiences.
Why contact sourcifychina.com get free quota from reliable electric injection suppliers?
Sourcifychina.com, an online platform connecting businesses with manufacturers in China, offers a unique opportunity for companies to obtain a free quota from reliable electric injection suppliers. This advantageous offer aims at helping businesses establish trustworthy partnerships with reputable manufacturers, ensuring high-quality products and smooth production processes.
By partnering with reliable electric injection suppliers, Sourcifychina.com ensures that businesses receive top-notch manufacturing services. These suppliers are carefully vetted and selected based on their track record of delivering quality products, their adherence to production timelines, and their ability to meet the specific requirements of the businesses. This means that businesses can confidently rely on these suppliers for their electric injection needs.
Obtaining a free quota from these trusted suppliers allows businesses to experience the manufacturing capabilities first-hand, without any financial commitment. This trial period enables companies to assess the supplier’s capabilities, evaluate the quality of their products, and test their production efficiency. It provides an opportunity for businesses to make informed decisions regarding their manufacturing needs before committing to a long-term partnership.
Furthermore, Sourcifychina.com understands the challenges that businesses may face when searching for reliable manufacturing partners in China. Language barriers, cultural differences, and concerns about product quality and intellectual property protection can all pose significant obstacles. To address these concerns, Sourcifychina.com works closely with businesses to ensure a smooth and transparent communication process throughout the sourcing and manufacturing journey.
In conclusion, Sourcifychina.com offers a free quota from reliable electric injection suppliers to help businesses establish trust and confidence in their manufacturing partnerships. This opportunity allows companies to assess the capabilities and quality of their chosen supplier before making a commitment. By addressing concerns related to manufacturing in China, Sourcifychina.com aims to facilitate successful partnerships and ensure high-quality production for businesses.