Introduce about electrochemical machining guide,Qulity,Cost,Supplier,Certification,Market,Tips,FAQ
Electrochemical machining (ECM) is a process that utilizes electrical energy for metal removal in various industries. This guide aims to provide a brief overview of ECM, including its quality, cost, suppliers, certifications, market, and helpful tips.
ECM is known for its ability to achieve complex and precise shapes, as it uses the principle of electrochemical dissolution to gradually remove metal from a workpiece. The quality of ECM-produced components is often superior, with high accuracy, minimal stress, and burr-free surface finishes. This makes it an ideal choice for manufacturing parts used in aerospace, medical, and automotive industries, among others.
Costs associated with ECM can vary depending on factors such as the size and complexity of the part, material used, and production volume. However, ECM generally offers cost advantages for high precision and intricate components, as it eliminates the need for expensive tooling or complex setups.
Finding reliable ECM suppliers is crucial for obtaining high-quality products. It is recommended to research and select suppliers with extensive experience in ECM, a proven track record, and good customer reviews. Additionally, suppliers with ISO 9001 certification ensure adherence to quality management practices, enhancing confidence in their products and services.
ECM is recognized as a proven and reliable technology, which has led to its widespread adoption in various industries globally. The market for ECM continues to expand as the demand for intricate and precise components increases. This presents a valuable opportunity for suppliers and manufacturers to cater to this growing market.
Some useful tips for ECM implementation include appropriate selection of electrolyte, operating parameters optimization, and regular maintenance of the ECM equipment. Such considerations can contribute to improved consistency, efficiency, and cost-effectiveness of the ECM process.
Frequently Asked Questions (FAQ) related to ECM may cover queries concerning its application range, compatibility with different materials, dimensional accuracy, tool life, and feasibility for mass production. Providing clear and concise answers to these FAQs helps potential users better understand the benefits and limitations of ECM.
By understanding the fundamentals, strengths, and considerations surrounding ECM, manufacturers can make informed decisions about adopting this technology for their specific needs.
Types of electrochemical machining
Electrochemical machining (ECM) is a process that uses electrical energy and chemical reactions to remove material from a workpiece. There are several types of ECM techniques, including:
1. Electrochemical Grinding (ECG): In ECG, a grinding wheel is used as an anode and the workpiece is used as a cathode. The electrolyte solution flows between the workpiece and the grinding wheel, removing material through an electrochemical reaction.
2. Electrochemical Drilling (ECD): ECD is a process used to create holes in a workpiece. A rotating electrode is used to apply an electrochemical reaction at the desired location, producing a hole with high precision and minimal distortion.
3. Electrochemical Deburring (ECD): ECD is used to remove burrs and sharp edges from a workpiece. An electrode is used to apply an electrochemical reaction at the burr location, smoothing out the surface and eliminating defects.
4. Electrochemical Etching (ECE): ECE is a process used to selectively remove material from a workpiece to create patterns or designs. An electrode is used to apply an electrochemical reaction at specific locations, etching away the material to produce the desired pattern.
5. Electrochemical Polishing (ECP): ECP is used to achieve a smooth and polished surface finish on a workpiece. An electrolyte solution and a polishing electrode are used to apply an electrochemical reaction, removing any roughness or imperfections on the surface.
Overall, ECM techniques offer precise control over material removal and can be used on a variety of materials, including metals, alloys, and composites. These techniques are often used in industries such as aerospace, automotive, and medical devices for producing complex and high-precision components.
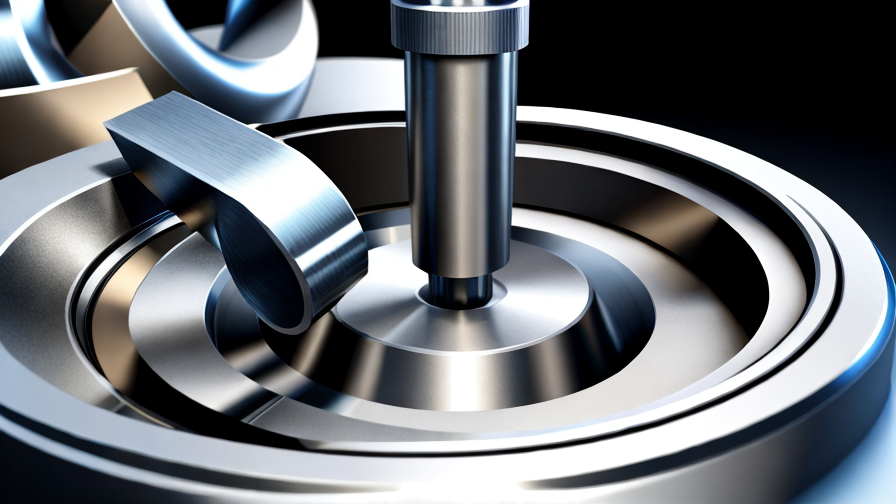
Pros and Cons of Using electrochemical machining
Electrochemical machining (ECM) is a non-traditional machining process that uses electrical energy and chemical reactions to remove material from the workpiece. It has several distinct advantages and disadvantages, which are discussed below.
Pros:
1. High Precision: ECM is known for its exceptional precision and accuracy. It can produce complex shapes with tight tolerances, making it ideal for industries such as aerospace and medical, where precision is crucial.
2. Burr-free and Stress-free: ECM produces a clean, burr-free surface finish. The process does not generate mechanical stresses on the workpiece, minimizing the risk of cracking or deformation. This feature is particularly beneficial for delicate or brittle materials.
3. Versatile: ECM can be applied to a wide range of materials, including conductive materials such as stainless steel, titanium, and even hard alloys. It can also work on complex, irregular, or curved geometries that are challenging for other machining processes.
4. No Tool Wear: Unlike conventional machining techniques, ECM does not involve physical contact between the tool and workpiece. Therefore, there is no tool wear, resulting in longer tool life and reduced maintenance costs.
5. High Material Removal Rate: ECM can achieve a high material removal rate, making it efficient for large-scale production. It is capable of removing material rapidly while maintaining the desired precision and surface finish.
Cons:
1. Limited Material Compatibility: One of the main drawbacks of ECM is its limited applicability to non-conductive materials. As it relies on electrochemical reactions, it does not work effectively on non-conductive materials like plastics or ceramics.
2. Complex Setup: ECM requires complex setup and specialized equipment, including power supplies, electrolytes, and control systems. This may lead to higher initial investment costs and increased complexity of operation.
3. Environmental Concerns: Some ECM processes involve the use of corrosive electrolytes, which can be hazardous to the environment if not handled properly. The disposal and management of wastewater contaminated with electrolyte residues must be adhered to strict regulations.
4. Limited Shape Complexity: Although ECM can handle complex geometries, it may encounter challenges with intricate internal features or deep cavities. Electrolyte flow and access to confined spaces can be limited, affecting the efficiency and accuracy of the process in such cases.
5. Electrical Power Consumption: ECM relies heavily on electrical power, which can result in higher energy costs compared to conventional machining methods. Energy-efficient strategies should be considered to optimize the process and minimize power consumption.
In conclusion, electrochemical machining offers numerous benefits, including high precision, burr-free surface finish, and versatility. However, it also has limitations such as limited material compatibility, complex setup requirements, environmental concerns, and restrictions on intricate shapes. Understanding these pros and cons is crucial in determining the suitability of ECM for specific manufacturing applications.
electrochemical machining Reference Specifications (varies for different product)
Electrochemical machining (ECM) is a non-traditional machining process that utilizes the principles of electrochemistry to remove material from a workpiece. The process involves the application of electrical energy to a conductive workpiece submerged in an electrolyte solution, resulting in the controlled dissolution of the material.
ECM offers several advantages over conventional machining methods, including high precision, complex shape capability, stress-free machining, and the ability to machine difficult-to-cut materials. However, the process also has certain limitations, such as the requirement for conductive workpieces and the need for customized tooling for each specific application.
The reference specifications for ECM vary depending on the specific product being manufactured. Some of the common parameters that influence the process include:
1. Current density: The amount of electrical current applied to the workpiece per unit area influences the material removal rate. The current density is typically controlled to achieve the desired machining rate without causing excessive tool wear.
2. Electrolyte composition: The composition of the electrolyte solution used in ECM affects the efficiency and effectiveness of the process. Factors such as pH, conductivity, and temperature can be adjusted to optimize the machining parameters.
3. Tool design: The design of the tool, typically referred to as the cathode or electrode, plays a critical role in achieving the desired machining result. The geometry and size of the tool are selected based on the desired shape, surface finish, and material removal rate.
4. Process control: ECM requires precise control over various parameters, such as voltage, current flow, electrolyte flow rate, and gap distance between the tool and the workpiece. Advanced sensors and control systems are used to monitor and regulate these parameters to maintain consistency and accuracy.
Overall, ECM offers significant flexibility in terms of its applications and can be used for a wide range of products, including aerospace components, medical devices, automotive parts, and microelectromechanical systems (MEMS). However, it is essential to consult product-specific guidelines and references to ensure adherence to the required specifications and achieve the desired machining outcome.
Applications of electrochemical machining
Electrochemical machining (ECM) is a non-traditional machining process that uses a controlled electrochemical reaction to remove material from a workpiece. This process is commonly used in industries such as aerospace, automotive, and medical to produce complex and precision components.
One of the primary applications of ECM is in the manufacturing of aerospace components such as turbine blades, fuel nozzles, and engine parts. ECM can produce intricate shapes and fine features with high precision, making it ideal for producing components with tight tolerances and complex geometries. The process can be used to machine various materials, including high-temperature alloys and superalloys, commonly used in aerospace applications.
In the automotive industry, ECM is utilized for the production of fuel injectors, gears, and engine components. The process can be used to machine hardened materials such as stainless steel and tool steels, which are commonly used in automotive applications. ECM can also be employed to produce prototypes and small batches of automotive components quickly and cost-effectively.
In the medical industry, ECM is used to manufacture surgical instruments, orthopedic implants, and dental components. The process can produce components with high surface finish and dimensional accuracy, essential for medical devices. ECM can also be used to machine biocompatible materials such as titanium and stainless steel, ensuring the safety and reliability of medical components.
Overall, electrochemical machining finds applications in various industries where precision, complexity, and efficiency are required. Its ability to produce high-quality components with minimal tool wear and heat-affected zones makes it a valuable machining process in modern manufacturing processes.
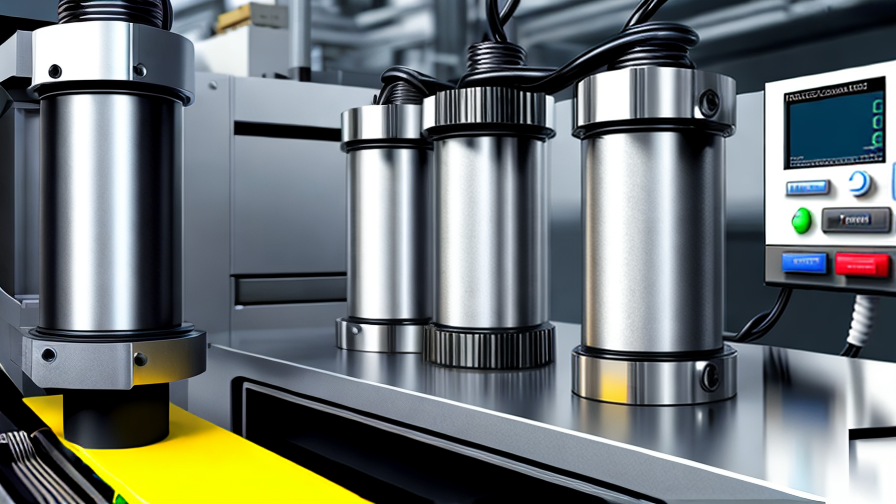
The Work Process and how to use electrochemical machining
Electrochemical machining (ECM) is a non-traditional machining process that uses the principles of electrolysis to remove material from a workpiece. It is commonly used in industries such as aerospace, automotive, and medical device manufacturing, where high precision and intricate shapes are required.
The work process of ECM involves immersing the workpiece in an electrolyte solution and applying a direct current between the workpiece and a specially designed tool called an electrode. The electrode is typically made of a highly conductive material such as copper or graphite, and is shaped to mirror the desired shape of the final workpiece. As the current passes through the electrolyte solution, material is removed from the workpiece through a process of electrochemical dissolution.
To use ECM, the workpiece is first securely clamped in the machine and the electrode is positioned in close proximity to the workpiece. The electrolyte solution is then pumped through the gap between the electrode and the workpiece, creating a conductive path for the current to flow. The voltage and current are carefully controlled to ensure precise material removal without damaging the workpiece.
One key advantage of ECM is its ability to machine complex shapes and difficult-to-reach areas with high accuracy and minimal tool wear. It is also a fast and cost-effective process compared to traditional machining methods for certain applications.
In conclusion, electrochemical machining offers a unique and efficient solution for machining complex components with high precision and accuracy. By understanding the work process and proper techniques of ECM, manufacturers can achieve superior results in their production processes.
Quality Testing Methods for electrochemical machining and how to control the quality
Electrochemical machining (ECM) is a non-traditional machining process that uses electrochemical principles to remove material from a workpiece. As with any manufacturing process, quality testing and control are essential to ensure the desired results. There are several quality testing methods commonly used in ECM:
1. Dimensional Inspection: This method involves measuring the workpiece’s dimensions using precision instruments like calipers, micrometers, or coordinate measuring machines. It ensures that the ECM process has accurately achieved the required dimensions and tolerances.
2. Surface Roughness Measurement: Surface finish and roughness directly affect the functionality of a workpiece. Instruments like surface profilometers or roughness testers can measure the roughness parameters, such as Ra, Rz, or Rt, to verify if they meet the specified requirements.
3. Microstructural Analysis: ECM can influence the microstructure of the workpiece, particularly in heat-affected zones. Metallographic examination can be conducted to inspect the microstructure’s integrity, grain size, and any potential defects like voids or cracks.
4. Chemical Analysis: ECM involves the dissolution of materials based on their electrochemical properties. Thus, it is crucial to analyze the chemical composition of the workpiece after machining to ensure it matches the required specifications. Techniques like X-ray fluorescence spectroscopy or energy-dispersive X-ray analysis can be used for chemical analysis.
5. Film Thickness Measurement: In ECM processes using coatings or masking, it is vital to verify the film thickness to ensure uniformity, stability, and durability. Techniques such as eddy current or optical profilometers can be employed to measure the coating thickness accurately.
To control the quality of electrochemical machining, several measures can be taken:
1. Process Parameter Control: Proper control of ECM parameters, such as current density, voltage, electrolyte concentration, and flow rate, is essential to achieve the desired material removal rate and surface finish.
2. Electrolyte Control: Regular monitoring and maintenance of the electrolyte composition, pH, temperature, and conductivity are crucial in maintaining consistent ECM performance and preventing adverse effects on the workpiece.
3. Tooling and Electrode Maintenance: Frequent inspection and maintenance of the tooling and electrodes, such as ensuring sharpness, shape, and proper alignment, are vital for achieving accurate machining results.
4. Process Monitoring: Real-time monitoring techniques, like thermocouples for temperature measurement or sensors for current density monitoring, can help identify and rectify any deviations in the ECM process promptly.
5. Operator Training: Well-trained operators who understand the ECM process, its limitations, and the quality requirements are essential for consistent and high-quality output.
In summary, appropriate quality testing methods, combined with effective quality control measures, are crucial to ensuring reliable and accurate electrochemical machining processes.
electrochemical machining Sample Policy and Post-Purchase Considerations for electrochemical machining from China
Sample Policy for Electrochemical Machining from China:
1. Sample Availability: Before placing a bulk order for electrochemical machining equipment from China, it is recommended to request product samples from the supplier. This enables the buyer to evaluate the quality and performance of the equipment as per their specific requirements.
2. Sample Cost and shipping: The buyer is responsible for covering the cost of the sample, including its shipping charges. However, some suppliers may offer to refund the sample costs upon placing a bulk order.
3. Customization: If the buyer requires any specific customization or modifications to the electrochemical machining equipment, it is important to discuss this with the supplier during the sample procurement stage. Any additional costs or lead times for customization should be clarified beforehand.
4. Quality Assurance: Suppliers should provide relevant certificates and documentation to ensure the quality and compliance of their electrochemical machining equipment with international quality standards. Buyers can request sample test reports, manufacturing standards, and product specifications to verify the quality assurance of the supplied samples.
Post-Purchase Considerations for Electrochemical Machining from China:
1. Warranty and After-sales Service: Ensure that the supplier provides a warranty period for the electrochemical machining equipment. Request details on the warranty coverage, including repair, replacement, or refund options. Also, inquire about the availability of after-sales technical support and the procedure for raising service requests.
2. Spare Parts Availability: Inquire about the availability of spare parts for the electrochemical machining equipment in the long run. This ensures smooth maintenance and minimizes downtime in case of component failures, reducing production disruptions.
3. Shipping and Logistics: Discuss shipping terms, transportation modes, and packaging requirements with the supplier. Clearly establish responsibilities and costs associated with customs, taxes, and other import/export regulations. Ensure that the supplier is experienced in handling international shipping to avoid any delays or complications.
4. Payment Terms: Clarify the accepted payment methods and conditions for the electrochemical machining equipment. Discuss initial payment, progress payments, or letter of credit terms to secure both parties’ interests and financial safety.
5. Communication and Language: Establish a clear communication channel with the supplier, ensuring they can communicate effectively in English or any other preferred language. Prompt and transparent communication is vital for understanding product specifications, resolving disputes, and maintaining a healthy business relationship.
By considering these sample policies and post-purchase considerations for electrochemical machining from China, one can ensure a smooth buying process and reduce the chances of any potential issues or misunderstandings.
Sourcing electrochemical machining from China: Opportunities, Risks, and Key Players
Electrochemical machining (ECM) is a manufacturing process that utilizes electrochemical processes to remove metal from a workpiece. It offers numerous advantages such as high precision, complex shape capabilities, and the ability to machine difficult-to-machine materials. Sourcing ECM from China presents several opportunities, along with associated risks, and involves key players in the market.
Opportunities:
1. Cost-Effectiveness: China is known for its low-cost manufacturing capabilities, making it an attractive option for sourcing ECM. The lower labor and operating costs allow for competitive pricing compared to other countries.
2. Skilled Workforce: China has a large pool of skilled workers in the field of manufacturing and engineering. This skilled labor force can contribute to the production of high-quality ECM products.
3. Technological Advancements: China has made significant progress in technological advancements and infrastructure. This includes the development of advanced ECM machinery and equipment, enabling the production of intricate and precise parts.
Risks:
1. Quality Concerns: Ensuring the quality of ECM products can be challenging when sourcing from China. Suppliers may not adhere to the same quality standards as required by the buyer, leading to potential quality issues and setbacks.
2. Intellectual Property (IP) Protection: China has faced scrutiny in the past regarding IP protection. Sourcing ECM from China may expose companies to the risk of imitation or intellectual property theft.
3. Communication and Language Barriers: Engaging with Chinese suppliers may encounter communication challenges due to language differences. This can lead to misunderstandings and delays in fulfilling requirements.
Key Players:
1. Beijing YHDG Electrochemical Machining Technology Co., Ltd.: A leading ECM technology company in China offering a wide range of ECM products and services.
2. Suzhou Suxin Electrochemical Machining Technology Co., Ltd.: Specializes in the development and production of ECM products for various industries.
3. Qingdao Jingxinli Precision Machinery Co., Ltd.: Offers ECM solutions for precision machining and has experience in serving both domestic and international markets.
In conclusion, sourcing ECM from China can provide opportunities in terms of cost-effectiveness, access to a skilled workforce, and technological advancements. However, quality concerns, IP protection, and communication barriers are important risks to consider. Key players in the Chinese ECM market include Beijing YHDG Electrochemical Machining Technology Co., Ltd., Suzhou Suxin Electrochemical Machining Technology Co., Ltd., and Qingdao Jingxinli Precision Machinery Co., Ltd.
How to find and select reliable electrochemical machining manufacturers in China,use google search manufacturers and suppliers
When searching for reliable electrochemical machining manufacturers in China, it is important to utilize Google search to identify reputable manufacturers and suppliers. By using specific keywords such as “electrochemical machining manufacturers in China” or “best electrochemical machining suppliers in China”, you can narrow down your search results to find potential options.
Once you have a list of manufacturers and suppliers, it is important to do further research to ensure their reliability and quality of products. Look for reviews and testimonials from past customers to gauge the satisfaction levels of their products and services. Additionally, check if the manufacturer has any certifications or accreditations that demonstrate their commitment to quality and industry standards.
When selecting a manufacturer, consider factors such as their experience in the industry, the range of services they offer, their production capacity, and their pricing. It is also important to communicate with the manufacturer directly to discuss your specific requirements and ensure that they can meet your needs.
Overall, by conducting thorough research, reading reviews, and communicating with potential manufacturers, you can find and select a reliable electrochemical machining manufacturer in China that meets your needs and specifications.
How to check electrochemical machining manufacturers website reliable,use google chrome SEOquake check if ranking in top 10M
To check the reliability of an electrochemical machining (ECM) manufacturer’s website, you can follow these steps:
1. Open the manufacturer’s website using Google Chrome browser.
2. Install the SEOquake extension for Google Chrome (if you do not have it already).
3. Once installed, click on the SEOquake icon in the toolbar of your browser.
4. A pop-up window will appear with various statistics about the website.
5. Look for the website’s Alexa Rank, which indicates the website’s popularity and traffic volume. If the website is ranked within the top 10 million on Alexa, it generally suggests a reasonably reliable and well-established website. However, this should not be the sole determinant of an ECM manufacturer’s website reliability.
6. Additionally, check for the website’s PageRank, a Google metric that evaluates the importance and trustworthiness of a website. Higher PageRank often signifies greater reliability, quality, and relevance.
7. Pay attention to the website’s user interface, design, and overall professionalism. A reliable ECM manufacturer would likely invest in a user-friendly and visually appealing website.
8. Verify if the website provides detailed information about their ECM capabilities, experience, certifications, and customer testimonials. A reliable manufacturer would likely offer comprehensive and transparent information to establish credibility.
9. Look for contact information or a customer support system. A dependable manufacturer should provide accessible communication channels such as email, phone number, or live chat for customer inquiries and support.
10. Lastly, ensure that the website is secure by checking if it has an SSL certificate (indicated by a padlock icon in the URL). A secure website demonstrates the manufacturer’s commitment to data protection and customer safety.
By taking these steps and using SEOquake to gauge the website’s popularity and performance, you can get an initial idea of an electrochemical machining manufacturer’s reliability. However, it is advisable to conduct further research and consider other factors before making any final judgments.
Top 10 electrochemical machining manufacturers in China with each 160 words introduce products,then use markdown create table compare
1. Beijing Jingdiao Group Co., Ltd (160 words):
As one of the top electrochemical machining manufacturers in China, Beijing Jingdiao Group Co., Ltd offers a range of high-quality products. Their electrochemical machining solutions use advanced technologies to achieve precision and efficiency. The company’s products include CNC electrochemical machining centers, electrode grinders, and portable electrochemical machining machines. These machines are widely used in industries such as aerospace, automotive, and electronics for precision machining of complex and delicate parts.
2. Jiangsu Sanxing Machinery Manufacture Co., Ltd (160 words):
Jiangsu Sanxing Machinery Manufacture Co., Ltd is a renowned manufacturer of electrochemical machining equipment in China. Their products cover a wide range of applications, including precision electrochemical machining systems, deburring machines, and hybrid electrochemical machining equipment. With a strong focus on research and development, the company has developed cutting-edge technologies to provide efficient and reliable solutions for various industries. Notably, their hybrid electrochemical machining equipment combines the benefits of electrochemical machining and traditional machining methods, offering enhanced precision and productivity.
3. Suzhou Hanxin Machinery Equipment Co., Ltd (160 words):
Suzhou Hanxin Machinery Equipment Co., Ltd is a leading manufacturer of electrochemical machining machines in China. The company produces a comprehensive range of products, including high-speed electrochemical machining systems, pulse electrochemical machining equipment, and CNC electrode grinders. These machines are known for their exceptional accuracy, surface finish, and process stability. Suzhou Hanxin Machinery Equipment Co., Ltd’s electrochemical machining machines find applications in industries such as medical, aerospace, and electronics, where precision and quality are critical.
| Manufacturer | Products | Specialties |
|————–|———-|————–|
| Beijing Jingdiao Group Co., Ltd | CNC electrochemical machining centers, electrode grinders, portable electrochemical machining machines | Precision machining, efficiency |
| Jiangsu Sanxing Machinery Manufacture Co., Ltd | Precision electrochemical machining systems, deburring machines, hybrid electrochemical machining equipment | Cutting-edge technologies, enhanced precision |
| Suzhou Hanxin Machinery Equipment Co., Ltd | High-speed electrochemical machining systems, pulse electrochemical machining equipment, CNC electrode grinders | Exceptional accuracy, surface finish, stability |
Background Research for electrochemical machining manufacturers Companies in China, use qcc.com archive.org importyeti.com
China is known for its vast manufacturing industry, and within that sector, there are several electrochemical machining (ECM) manufacturers. By utilizing websites such as qcc.com, archive.org, and importyeti.com, one can gain valuable insights into these companies.
Qcc.com is a popular Chinese business database that provides comprehensive information about companies operating in China. It lists contact details, company profiles, and legal registration information for ECM manufacturers. This platform allows users to search for specific companies, filter results based on location, and access key information essential for business partnerships or inquiries.
Archive.org is a website that captures and stores web pages over time, providing historical data. Although information on ECM manufacturers may not be available directly on this platform, archive.org can be helpful in retrieving previously indexed company websites, product catalogs, and other relevant data that might have been removed from the internet.
Importyeti.com is a platform that focuses on facilitating import-export activities. It provides detailed information about product imports and exports, enabling users to identify specific ECM manufacturers and gain insights into their trading activities. This platform can be helpful in discovering potential ECM manufacturers exporting their products to China or importing materials necessary for ECM manufacturing.
By utilizing these platforms, researchers can gather valuable information about ECM manufacturers in China. This includes company profiles, contact details, historical data from archived websites, and import-export activities. These sources provide researchers with a comprehensive understanding of ECM manufacturers operating in China, aiding in decision-making processes, business collaborations, or further inquiries.
Leveraging Trade Shows and Expos for electrochemical machining Sourcing in China
Trade shows and expos in China are excellent opportunities for sourcing electrochemical machining suppliers and technology. These events bring together a wide range of manufacturers, suppliers, and industry experts under one roof, making it easy for buyers to connect with potential suppliers.
By attending trade shows and expos focused on electrochemical machining, buyers can explore the latest technologies, products, and services offered by different suppliers. They can also meet with potential suppliers face-to-face, discuss their specific requirements, and see live demonstrations of the equipment in action. This allows buyers to make informed decisions about which suppliers best meet their needs.
In addition, trade shows and expos provide a platform for networking with other industry professionals, sharing knowledge and insights, and staying up-to-date on the latest industry trends and developments. This can help buyers make more strategic sourcing decisions and stay ahead of the competition.
To make the most of trade shows and expos for electrochemical machining sourcing in China, buyers should come prepared with a list of specific requirements, conduct thorough research on potential suppliers beforehand, and take advantage of networking opportunities to build relationships with key industry players. By leveraging trade shows and expos, buyers can streamline their sourcing process, access a wider range of suppliers, and ultimately find the best partners for their electrochemical machining needs.
The Role of Agents and Sourcing Companies in Facilitating electrochemical machining Purchases from China
Agents and sourcing companies play a crucial role in facilitating electrochemical machining (ECM) purchases from China. As buyers seek to procure high-quality and cost-effective ECM products from China, these intermediaries act as a bridge between the buyers and the Chinese suppliers, streamlining the purchasing process and mitigating potential risks.
One key role of agents and sourcing companies is to identify reliable and suitable suppliers in China for ECM products. They leverage their extensive network and knowledge of the industry to conduct thorough assessments and due diligence on potential suppliers. This involves verifying their capabilities, quality control processes, certifications, and past performance. By carefully selecting reliable suppliers, agents and sourcing companies help buyers find reputable manufacturers that meet their specific requirements.
Moreover, agents and sourcing companies facilitate communication between the buyers and suppliers. They bridge any language and cultural barriers, ensuring effective and efficient communication throughout the purchasing process. This includes assisting with product inquiries, negotiations, and clarifying technical specifications. By acting as a liaison, they help to minimize misunderstandings and ensure that both parties are on the same page.
Furthermore, these intermediaries facilitate the logistics and shipping process. They coordinate with the suppliers to arrange packaging, transportation, and customs procedures. This ensures that the ECM products are delivered to the buyers in a timely and cost-effective manner. Agents and sourcing companies may also handle the necessary documentation and provide updates on the shipment’s progress, giving buyers peace of mind and saving them valuable time and resources.
Additionally, agents and sourcing companies play a crucial role in quality control. They may conduct on-site inspections and audits of the suppliers’ facilities to ensure that they meet the required standards. By monitoring the production process and quality control measures, they can minimize potential risks of receiving substandard ECM products.
In conclusion, agents and sourcing companies serve as essential facilitators in purchasing ECM products from China. They assist buyers in finding reliable suppliers, bridge communication gaps, manage logistics, and ensure quality control. By leveraging their expertise and network, these intermediaries streamline the purchasing process, enabling buyers to access high-quality ECM products from China efficiently.
Price Cost Research for electrochemical machining manufacturers Companies in China, use temu.com and 1688.com
When looking for electrochemical machining manufacturers in China, companies can utilize platforms like temu.com and 1688.com to conduct price and cost research. These platforms offer a wide range of suppliers specializing in electrochemical machining services.
By using these platforms, companies can compare prices from different manufacturers, enabling them to find the most cost-effective option that meets their specific requirements. It is essential to consider factors such as production capacity, quality standards, and lead times when assessing costs.
Additionally, companies can negotiate prices directly with suppliers on these platforms to further optimize their sourcing strategy. Through effective communication and negotiation, businesses can potentially secure better pricing and terms, ensuring a successful partnership with the chosen electrochemical machining manufacturer.
In conclusion, temu.com and 1688.com provide valuable resources for companies in China seeking electrochemical machining manufacturers, allowing them to conduct price and cost research efficiently and effectively. By leveraging these platforms, businesses can make informed decisions that align with their budget and production needs.
Shipping Cost for electrochemical machining import from China
The shipping cost for importing electrochemical machining equipment from China will vary depending on several factors such as the size and weight of the equipment, the shipping method chosen, and the distance between the origin and destination.
Typically, the most cost-effective shipping method for importing heavy machinery like electrochemical machining equipment from China is through sea freight. Shipping by sea is slower than air freight but is significantly more affordable for heavy and bulky items.
The cost of sea freight from China to most major ports in the United States or Europe can range from $700 to $2000 per cubic meter, with additional charges for handling, customs clearance, and delivery from the port to the final destination.
It is recommended to work with a freight forwarder or shipping company with experience in handling heavy machinery imports to ensure a smooth and cost-effective shipping process. They can provide a detailed quote based on the specific requirements of the electrochemical machining equipment and help navigate any potential challenges or delays in the import process.
Overall, by carefully planning the shipment and choosing the right shipping method and partner, it is possible to import electrochemical machining equipment from China without exceeding a reasonable budget for shipping costs.
Compare China and Other electrochemical machining Markets: Products Quality and Price,Visible and Hidden Costs
China is known for producing lower-cost products compared to other electrochemical machining markets, such as the United States and Europe. This is primarily due to lower labor costs and economies of scale in China. However, the quality of products from China can vary significantly. While some Chinese manufacturers produce high-quality products that meet international standards, others may cut corners to reduce costs, resulting in lower quality products.
In terms of visible costs, products from China are generally more affordable compared to those from other markets. The lower labor and production costs in China allow manufacturers to offer competitive prices to customers. However, the hidden costs associated with sourcing products from China, such as longer lead times, language barriers, and potential quality control issues, can impact the overall cost of doing business with Chinese suppliers.
On the other hand, products from other electrochemical machining markets, such as the United States and Europe, are typically of higher quality and come with a higher price tag. Manufacturers in these markets often invest in research and development to produce innovative products that meet the highest industry standards. While the initial cost of products from these markets may be higher, customers can benefit from better quality, reliability, and customer service.
Overall, when considering products from China and other electrochemical machining markets, customers should carefully weigh the trade-offs between price and quality. While products from China may offer lower costs, there may be hidden expenses associated with sourcing from overseas. On the other hand, products from other markets may come with a higher price tag, but customers can expect higher quality and better overall value.
Understanding Pricing and Payment Terms for electrochemical machining: A Comparative Guide to Get the Best Deal
Electrochemical machining (ECM) is a specialized manufacturing process that uses an electrolyte solution and an electrically conductive workpiece to remove material through the process of electrochemical dissolution. This guide aims to provide a comprehensive understanding of the pricing and payment terms associated with ECM services, aiming to ensure that businesses can secure the best deal.
Pricing for ECM can vary depending on several factors. The complexity and size of the workpiece, the type and thickness of the material being machined, and the desired precision and surface finish all play a role in determining the cost. Additionally, the quantity of workpieces needed and the turnaround time required may also impact the pricing. It is important to communicate these specifications clearly to potential ECM service providers to obtain accurate quotes.
Payment terms for ECM services can vary depending on the supplier and the scope of the project. Typically, larger projects may require a down payment or initial deposit before the work begins. This ensures commitment from both parties and covers any initial expenses incurred by the ECM service provider. The remaining balance is usually due upon completion and satisfactory delivery of the machined workpieces.
In some cases, especially for long-term or repeat projects, ECM service providers may offer discounts or reduced prices. Establishing a good working relationship can be beneficial in negotiating favorable pricing terms. Additionally, it is important to clarify any additional costs that may be involved, such as tooling or setup charges, transportation fees, or any applicable taxes.
When seeking ECM services, it is recommended to obtain quotes from multiple providers to compare pricing and payment terms. However, it is important to consider not only the cost but also the reputation, experience, and capabilities of the ECM service provider. Choosing the lowest-priced option may not always guarantee the best quality or timely delivery.
In conclusion, understanding pricing and payment terms is crucial when seeking ECM services. Clear communication of project specifications, obtaining multiple quotes, and considering the reputation and capabilities of the service provider are essential for securing the best deal. By doing so, businesses can ensure the desired results while maintaining cost-effectiveness in their ECM projects.
Chinese Regulations and Industry Standards Certifications for electrochemical machining,Import Regulations and Customs for electrochemical machining from China
China has implemented several regulations and industry standards certifications for electrochemical machining (ECM) to ensure quality and safety in the industry. One prominent certification is the ISO 9001:2015, which sets the standard for quality management systems. ECM manufacturers in China need to comply with this certification to demonstrate their ability to consistently provide products that meet customer requirements.
Another significant certification is the ISO 14001:2015, which focuses on environmental management systems. This certification ensures that ECM manufacturers in China have implemented effective practices to minimize their environmental impact during the production process.
Additionally, the Chinese government has established several regulations to regulate the import and export of ECM products. For instance, the Customs Import and Export Commodity Inspection Law requires ECM products to undergo mandatory inspection and quality checks before entering or leaving the country. This is done to maintain quality standards and prevent the import or export of substandard or dangerous products.
China also follows the Harmonized System (HS), an internationally recognized classification system for traded products. ECM manufacturers need to ensure that their products are correctly classified according to the HS code to facilitate smooth customs clearance.
In terms of customs procedures, China requires ECM manufacturers to provide detailed documentation for import and export processes. This includes invoices, packing lists, shipping bills, and other necessary documents. Additionally, the Chinese government imposes customs duties and taxes on imported ECM products based on their declared value and classification.
Importers and exporters of ECM products should also be aware of the specific regulations of destination countries. Each country may have its own import regulations and customs procedures for ECM products, which need to be followed to avoid any legal complications or delays.
Overall, China has implemented regulations and certifications to ensure the quality, safety, and proper handling of ECM products. Adhering to these standards and being knowledgeable about import regulations and customs procedures is crucial for both ECM manufacturers and importers/exporters to maintain compliance and facilitate smooth trade operations.
Sustainability and Environmental Considerations in electrochemical machining Manufacturing
Sustainability and environmental considerations are becoming increasingly important in the manufacturing industry. As electrochemical machining (ECM) is a widely used manufacturing process, it is crucial to address its impact on the environment and explore ways to make it more sustainable.
One of the primary environmental advantages of ECM is its ability to operate with a small carbon footprint. Since ECM is a non-traditional machining method, it eliminates the need for cutting tools, minimizing waste generation. Additionally, ECM does not produce any significant heat or noise, reducing energy consumption and pollution levels. This aspect contributes to the overall sustainability of the manufacturing process.
Moreover, ECM typically employs electrolytes as the medium for material removal. These electrolytes can be designed to have minimal environmental impact, focusing on biodegradability, and reduced toxicity. By utilizing environmentally friendly electrolytes, ECM can further reduce its ecological footprint.
Another aspect to consider is the recycling potential of ECM. Often, the electrolytes used in this process can be effectively recycled, minimizing waste generation. Implementing a closed-loop system for electrolyte management can minimize the environmental impact associated with ECM manufacturing.
Furthermore, some advancements in ECM technology have led to the development of hybrid systems that couple ECM with other manufacturing processes like 3D printing. These hybrid approaches provide the opportunity to reduce material waste by selectively removing material in a precise manner, reducing overall resource consumption.
To enhance the sustainability of ECM manufacturing, companies can also incorporate life cycle assessments (LCAs) to evaluate the environmental impact of the entire manufacturing process. By identifying specific areas of improvement, companies can implement targeted strategies to minimize their ecological footprint and enhance the overall sustainability of their operations.
In conclusion, sustainability and environmental considerations play a significant role in electrochemical machining manufacturing. By embracing environmentally friendly electrolytes, adopting closed-loop systems, and integrating hybrid approaches, ECM can minimize waste generation, reduce energy consumption, and contribute to a more sustainable manufacturing industry. Implementing life-cycle assessments can help identify areas for improvement and further enhance the sustainability of ECM manufacturing.
List The Evolution history of “electrochemical machining”
Electrochemical machining (ECM) is a non-traditional machining process that uses the principles of electrochemistry to remove material from a workpiece. The evolution of ECM can be traced as follows:
1. Origin: The concept of electrochemical machining was first proposed in the late 1940s by Professor Carl Gustav Söderberg in Sweden. He suggested using electrolysis to remove metal from a workpiece to achieve precise shaping.
2. Development: In the 1950s, the technology of ECM was further explored and developed by several researchers worldwide. The process involved immersing a workpiece in an electrolyte solution and using an electric current to erode the material selectively.
3. Industrial Applications: By the 1960s, ECM began to see industrial applications. It proved to be particularly useful for machining challenging materials such as heat-resistant alloys, which were difficult to machine using conventional methods. ECM started finding applications in aerospace, automotive, and medical industries.
4. Advancements: In the 1970s, advancements in ECM technology included better control systems, electrolyte circulation, and tool design. These developments resulted in improved accuracy, surface finish, and process stability.
5. ECM Variants: Over time, several variants of ECM were developed to cater to specific machining needs. These variants include pulsed ECM, which uses pulsed current to improve material removal rates, and electrochemical grinding, which combines ECM with grinding.
6. Advanced ECM: In recent years, advanced ECM techniques have emerged. For example, electrochemical deburring is used for precision deburring of intricate parts, while electrochemical micromachining is employed to manufacture miniature components with high precision.
7. Integration with Automation: With the advancement of automation, ECM has been integrated with computer numerical control (CNC) systems, allowing for greater precision and repeatability. This integration has enabled ECM to be used in high-volume production environments.
8. Future Prospects: The evolution of ECM is ongoing, with ongoing research aiming to improve processes, increase efficiency, and expand the range of applicable materials. Integration with other advanced technologies such as additive manufacturing and machine learning is being explored.
In summary, electrochemical machining has come a long way since its inception in the 1940s. From early development to industrial adoption, advancements in technology and process variants have made ECM a valuable tool for precision machining. With further research and integration with other advanced technologies, ECM is expected to continue evolving and finding new applications in the future.
The Evolution and Market Trends in electrochemical machining Industry
Electrochemical machining (ECM) is a non-traditional machining process that uses the principles of electrolysis to remove material from a workpiece. It has been widely used in various industries for precision machining of complex shapes and difficult-to-machine materials. Over the years, the ECM industry has witnessed significant evolution and market trends that have shaped its growth and prospects.
One of the key developments in ECM is the advancement in tooling and electrode design. Manufacturers have been investing in research and development to create more efficient and cost-effective electrodes for ECM. These advancements have led to improved tool life, higher machining speeds, and enhanced accuracy, making ECM more attractive to industries seeking high-quality machining solutions.
Market trends have also played a crucial role in shaping the ECM industry. One of the major trends is the increasing demand for miniaturization and high-precision components in sectors such as aerospace, medical devices, and electronics. ECM, with its ability to produce intricate and precise parts with minimal thermal and mechanical stresses, has gained prominence as a preferred machining method for these industries.
Moreover, the growing focus on sustainable manufacturing practices has led to increased interest in ECM due to its environmental advantages. ECM is a non-contact and non-thermal process, resulting in minimal material waste and reduced energy consumption compared to conventional machining techniques. This makes ECM a sustainable option for manufacturers aiming to reduce their environmental footprint.
Furthermore, the integration of advanced technologies, such as computer-aided design and computer numerical control, has revolutionized ECM processes. These technologies have enabled better control and monitoring of the machining parameters, resulting in improved accuracy and efficiency.
In terms of market growth, the global ECM market is expected to experience significant expansion in the coming years. The rising adoption of ECM in industries such as automotive, aerospace, and medical devices is driving the demand for ECM solutions. Additionally, the increasing need for intricate and high-precision components in emerging industries like 3D printing and renewable energy further fuels the growth of the ECM market.
In conclusion, the ECM industry has evolved through advancements in tooling and electrode design, increasing demand for high-precision components, and the integration of advanced technologies. With its ability to provide precision machining with minimal environmental impact, ECM is well-positioned for future growth in various sectors where precision and intricate components are essential.
Custom Private Labeling and Branding Opportunities with Chinese electrochemical machining Manufacturers
Private labeling and branding opportunities with Chinese electrochemical machining (ECM) manufacturers provide businesses with the chance to uniquely position their products and establish a strong brand presence in the market. ECM manufacturers in China offer custom private labeling services, allowing businesses to customize the appearance and packaging of their products to reflect their brand identity.
With a large number of ECM manufacturers in China, businesses have a wide range of options to choose from. These manufacturers have expertise in producing high-quality ECM products, using advanced technology and precision machining techniques. By partnering with these manufacturers, businesses can benefit from their expertise while incorporating their own branding elements.
The private labeling and branding process typically involves collaborating closely with the Chinese ECM manufacturer to design and develop customized product packaging, including labels, logos, and other branding elements. This allows businesses to create a distinct and memorable brand identity that resonates with their target customers.
Furthermore, private labeling and branding opportunities may extend to product customization, allowing businesses to tailor the ECM products to meet specific market demands. Manufacturers can adjust product dimensions, materials, finishes, and other features to align with the brand’s requirements. Customization options provide businesses with a competitive advantage by offering unique and personalized products to their customers.
Partnering with a Chinese ECM manufacturer for private labeling and branding can also result in cost savings and improved efficiency. Manufacturers in China typically offer competitive pricing due to lower labor and production costs. Additionally, their expertise and streamlined production processes ensure timely delivery and high-quality products.
In conclusion, Chinese ECM manufacturers present excellent opportunities for businesses seeking custom private labeling and branding options. By collaborating with these manufacturers, businesses can create a differentiated brand identity and enhance their product offerings, ultimately gaining a competitive edge in the market.
Tips for Procurement and Considerations when Purchasing electrochemical machining
When purchasing electrochemical machining (ECM) equipment, there are several factors to consider to ensure you are getting the best value for your investment. Here are some tips and considerations:
1. Research and Compare Options: Before making a purchase, research different ECM equipment suppliers and compare their products based on factors such as price, quality, reviews, and after-sales support.
2. Evaluate Your Needs: Determine your specific production requirements, such as the types of materials you will be working with, the size and complexity of the parts to be machined, and the desired production output. This will help you select the right ECM machine for your needs.
3. Quality and Performance: Consider the quality and performance of the ECM equipment, including factors such as accuracy, speed, surface finish, and the capability to handle different materials and part geometries.
4. Maintenance and Support: Choose a supplier that offers adequate support, maintenance, and training services to ensure the smooth operation of your ECM equipment.
5. Cost Considerations: While price is an important factor, it should not be the only consideration when purchasing ECM equipment. Consider the total cost of ownership, including maintenance, energy consumption, and the potential for increased productivity and efficiency.
6. Technology and Innovation: Look for ECM equipment that incorporates the latest technology and innovation to improve performance, accuracy, and efficiency.
7. Compatibility and Integration: Ensure that the ECM equipment you choose is compatible with your existing manufacturing processes and can be easily integrated into your production line.
8. Reliability and Durability: Choose a reputable supplier with a track record of producing reliable and durable ECM equipment that can withstand the demands of your manufacturing operations.
By carefully considering these factors and following these tips, you can make an informed decision when purchasing electrochemical machining equipment that meets your specific needs and provides the best value for your investment.
FAQs on Sourcing and Manufacturing electrochemical machining in China
1. What is electrochemical machining (ECM)?
Electrochemical machining (ECM) is a metal removal process that uses an electrolyte solution and an electric current to dissolve and remove metal from a workpiece. It is commonly used for intricate or complex shapes, particularly in hard materials.
2. Why source and manufacture ECM in China?
China has become a leading manufacturing hub due to its large industrial base, competitive costs, and vast supplier network. The country offers a wide range of specialized equipment and expertise in various industries, including ECM. By sourcing and manufacturing ECM in China, businesses can benefit from cost savings, high-quality products, and efficient production processes.
3. What are the advantages of sourcing ECM in China?
Sourcing ECM in China brings several advantages, such as lower production costs due to the availability of skilled workers at competitive wages. China also has a well-established supply chain and an extensive network of manufacturers, allowing for quick turnaround times and flexibility in production capacity. Additionally, many Chinese ECM manufacturers have gained experience and expertise from working with international clients, ensuring high-quality standards and innovative solutions.
4. Are there any challenges in sourcing and manufacturing ECM in China?
While China offers numerous benefits, there are some challenges to consider. These include potential language and communication barriers, intellectual property concerns, and cultural differences. However, these challenges can be addressed by partnering with reputable manufacturers or using sourcing agents who have experience in dealing with Chinese suppliers.
5. How can I find reliable ECM manufacturers in China?
To find reliable ECM manufacturers in China, it is crucial to conduct thorough research. This can involve attending trade shows, utilizing online sourcing platforms, and engaging with industry associations. Verifying manufacturers’ certifications, reputation, and past customer reviews are essential steps in ensuring the reliability and quality of the chosen supplier.
In conclusion, sourcing and manufacturing electrochemical machining in China can be advantageous due to cost savings, high-quality products, and efficient production processes. However, businesses need to consider potential challenges, including language barriers and intellectual property concerns. Conducting thorough research and partnering with reputable manufacturers can help address these challenges and ensure a successful ECM sourcing and manufacturing process in China.
Why contact sourcifychina.com get free quota from reliable electrochemical machining suppliers?
Sourcifychina.com is a trusted platform for sourcing manufacturing partners in China, including reliable electrochemical machining suppliers. By contacting Sourcifychina.com, you can easily receive a free quota from these suppliers and access their services at competitive prices.
Electrochemical machining suppliers sourced through Sourcifychina.com are carefully vetted to ensure they meet high-quality standards and have a track record of delivering excellent results. Contacting Sourcifychina.com for a free quota allows you to compare quotes from different suppliers, enabling you to choose the one that best fits your budget and requirements.
The platform also provides a streamlined communication process, ensuring that all your queries and specifications are clearly conveyed to the suppliers. This minimizes the risk of miscommunication and errors in the manufacturing process.
Additionally, Sourcifychina.com offers support and guidance throughout the sourcing and production process, helping you navigate the complexities of working with overseas suppliers. Their expertise and experience in the Chinese manufacturing industry can help you secure the best possible deal with electrochemical machining suppliers.
In summary, by contacting Sourcifychina.com for a free quota from reliable electrochemical machining suppliers, you can access cost-effective manufacturing solutions while benefiting from expert guidance and support.