Analysis of Manufacturing Expenses for fiberglass cost
The manufacturing expenses for fiberglass can be significant due to the cost of raw materials and the specialized equipment required for production. The primary cost driver for fiberglass production is the raw material, which includes glass fibers and resin. The cost of raw materials can vary depending on the quality, type, and quantity used.
In addition to raw materials, the manufacturing process for fiberglass requires specialized equipment such as ovens, rollers, and molds. The cost of purchasing and maintaining these machines can also add to the overall expense of production. Additionally, labor costs are a significant component of manufacturing expenses as skilled workers are required to operate equipment and oversee the production process.
Other expenses add to the overall cost of fiberglass production, including transportation, storage, and waste management. The transportation of raw materials and finished products can be costly, especially for international shipments. Storage and waste management costs come into play as unwanted and unused materials must be properly stored and disposed of.
Overall, the manufacturing expenses for fiberglass can be high due to the cost of raw materials, specialized equipment, labor, and additional expenses. Companies seeking to reduce costs can explore alternative raw materials, optimize production processes, or find ways to reduce waste and transportation expenses.
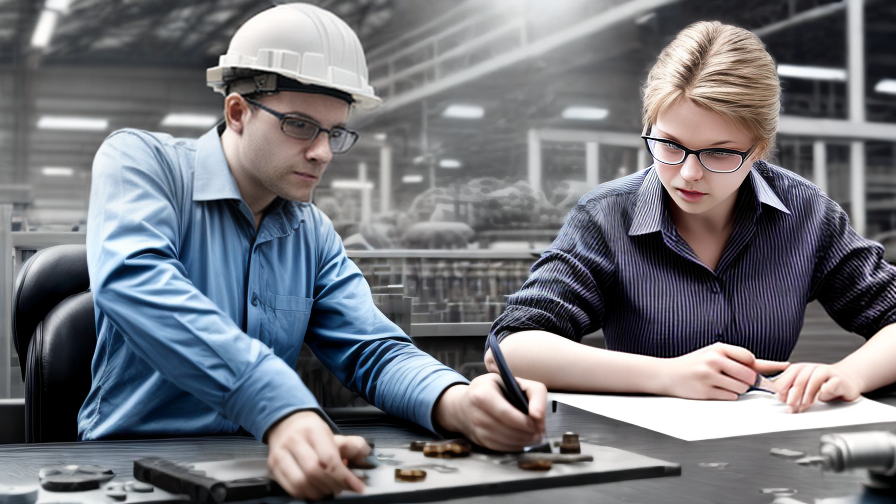
Understanding the Components that Contribute to the Price of fiberglass cost
Fiberglass is made of thin fibers of glass and resin, which are woven together and then impregnated with a thermosetting polymer that hardens when heated. The resulting material is light, strong, and corrosion-resistant, making it ideal for a wide range of applications in various industries.
There are several components that contribute to the price of fiberglass. These include:
1. Raw material costs: The cost of the raw materials used to make fiberglass, such as glass fibers, resin, and the thermosetting polymer, can have a significant impact on the overall price.
2. Manufacturing process: The manufacturing process used to make fiberglass can also affect its price. Different methods may require different equipment or facilities, which can increase costs.
3. Quality of materials: The quality of the materials used to make fiberglass can impact its price. Higher quality materials may cost more, but they may also result in a stronger, more durable product.
4. Quantity of production: The quantity of fiberglass produced can also impact its price. Larger quantities may be more cost-effective, as the manufacturer can take advantage of economies of scale.
5. Labor costs: Labor costs are another factor that can contribute to the price of fiberglass. Skilled labor is required during the manufacturing process, and the cost of these workers can vary by region.
6. Transportation costs: Depending on where the fiberglass is produced and where it is being shipped, transportation costs can also affect the price. These costs can be affected by distance, method of transportation, and the size of the shipment.
Overall, the price of fiberglass is influenced by a variety of factors. By understanding these components, buyers can make informed decisions when purchasing fiberglass for their specific needs.
Comparing the Wholesale and Retail Prices of fiberglass cost in China
In China, the wholesale and retail costs of fiberglass vary significantly. Wholesale prices are often lower than retail prices due to the larger quantities that are purchased in bulk.
Fiberglass is widely used in various industries, including construction, automotive, and aerospace. Its popularity is due to its excellent mechanical properties, durability, and resistance to corrosion. As a result, fiberglass is in high demand in China, which has led to a wide range of wholesalers and retailers supplying the market.
The wholesale cost of fiberglass in China depends on various factors, including the quality, quantity, and location. On average, the wholesale cost of fiberglass in China is around $1.50 to $5 per kilogram. However, the cost of high-quality fiberglass can be significantly higher.
On the other hand, retail prices for fiberglass tend to be higher due to additional costs such as delivery and packaging. The cost of fiberglass is also influenced by the customer’s location and the supplier’s markup.
In summary, there is a significant difference between the wholesale and retail prices of fiberglass in China. Wholesale prices are lower due to the economies of scale, while retail prices are higher due to additional costs. Both the wholesale and retail prices of fiberglass will vary based on various factors such as quality, quantity, location, and delivery.

Understanding Shipping and Logistics for fiberglass cost from China
Shipping and logistics are important aspects to consider when importing fiberglass from China. Fiberglass is a lightweight and durable material used in various industries, such as construction, automotive, and marine.
The cost of shipping and logistics depends on several factors, such as the volume and weight of the consignment, the shipping method, the distance between the origin and destination, and the customs and taxes.
One of the most common shipping methods for importing fiberglass from China is sea freight. This involves transporting goods in a container via ship. The cost of sea freight depends on the volume and weight of the shipment, as well as the shipping route and transit time. Shipping costs can also be impacted by certain external factors such as political relations or natural disasters.
Logistics also play a crucial role in the transportation of fiberglass from China, as it involves managing the flow of goods from the factory to the final destination. It includes arranging for transportation, handling, and storage of the products. In order to avoid any damage to the fiberglass while in transit, logistics companies offer specialized packaging and handling services.
In conclusion, when importing fiberglass from China, it is important to consider shipping and logistics costs as they can significantly impact the overall cost of the product. Sea freight is the most commonly used shipping method, and logistics companies offer specialized services for handling fragile fiberglass products.
Potential Tariffs or Import Taxes on fiberglass cost Purchased from China
In recent years, the United States has imposed tariffs on a range of products imported from China. These tariffs are intended to protect domestic industries and reduce the trade deficit with China. Fiberglass is one product that may potentially be subject to tariffs or import taxes if it is purchased from China.
Currently, there are no specific tariffs on fiberglass imported from China. However, it is possible that tariffs may be imposed in the future if the U.S. government determines that Chinese fiberglass is being sold at unfairly low prices, a practice known as “dumping.” If this occurs, the U.S. Department of Commerce may conduct an investigation and impose anti-dumping duties on Chinese fiberglass.
In addition, fiberglass may be subject to general tariffs on imported goods from China. The U.S. government has implemented a range of tariffs on Chinese imports in recent years, including tariffs of 10-25% on a variety of products. If fiberglass is included in these tariffs, the cost of importing fiberglass from China would increase, potentially making it less competitive with domestically produced fiberglass or fiberglass imported from other countries.
Finally, there is also the possibility of import taxes being imposed on fiberglass from China due to ongoing trade tensions between the two countries. In recent years, the U.S. and China have engaged in a trade war, increasing tariffs and other trade barriers in an attempt to gain leverage in negotiations. Depending on the outcome of these negotiations, fiberglass may be subject to additional tariffs or other trade barriers in the future.
In conclusion, while there are currently no specific tariffs or import taxes on fiberglass imported from China, the product may potentially be subject to these measures in the future. Businesses who rely on imported fiberglass from China should monitor developments in trade policy and be prepared to adjust their supply chains if necessary.

Impact of Market Demand and Competitive Environment on fiberglass cost
The market demand and competitive environment have a significant impact on the cost of fiberglass. When the demand for fiberglass increases, the cost of production also goes up, which eventually leads to higher prices for consumers. On the other hand, when the demand for fiberglass decreases, the cost of production decreases, resulting in a decrease in prices for consumers.
In a competitive environment, companies are always trying to outdo each other, leading to price wars that can have a direct impact on the cost of fiberglass. Companies may lower their prices to attract more customers, and as a result, the cost of production may decrease.
Environmental factors can also affect the price of fiberglass. For example, a shortage of raw materials such as silica sand or the energy used to manufacture fiberglass can lead to increased costs of production, which directly affect the cost of fiberglass.
Moreover, government policies and regulations can have a significant impact on the cost of fiberglass. This can include taxes or subsidies on raw materials, energy, or transportation that affect the cost of production.
In conclusion, the market demand and competitive environment, along with environmental factors and government policies, play a critical role in determining the cost of fiberglass. Companies need to monitor these factors continually to stay competitive and meet consumer demands while keeping production costs to a minimum.
FAQ about fiberglass cost with multiple answers
Q: What is the average cost of fiberglass installation?
A1: The cost of fiberglass installation can range from $3 to $8 per square foot.
A2: On average, it can cost around $1,500 to $2,500 to have fiberglass insulation installed in a typical home.
A3: The cost of fiberglass installation may vary depending on the size of the job and the location of the property.
Q: How much does it cost to replace old fiberglass insulation?
A1: The cost of removing old fiberglass insulation can range from $1.50 to $3 per square foot.
A2: The cost of installing new fiberglass insulation after removing the old one can range from $1.50 to $3 per square foot.
A3: On average, the total cost of replacing old fiberglass insulation can range from $2,500 to $4,000 depending on the size of the job.
Q: Is it worth the cost to install fiberglass insulation?
A1: Yes, it is worth the cost as fiberglass insulation can significantly reduce energy bills by preventing heat loss during winter and keeping the house cool during the summer.
A2: Additionally, fiberglass insulation can also help improve indoor air quality by minimizing the amount of outside pollutants that infiltrate the home.
A3: The initial investment in fiberglass insulation can save homeowners money in the long run on energy bills and maintenance costs.
Q: What factors can impact the cost of fiberglass installation?
A1: The size of the job, the type of insulation used, and the location of the property can all impact the cost of fiberglass installation.
A2: In addition, the condition of the property and the accessibility of the areas where insulation is needed can also affect the cost.
A3: The expertise of the contractor hired to install the insulation can also play a role in the cost, as more experienced professionals may charge higher rates.