Introduce about machining center guide,Qulity,Cost,Supplier,Certification,Market,Tips,FAQ
A machining center guide provides essential information about machining centers, which are advanced machines used in the manufacturing industry for various machining operations. This guide covers aspects such as quality, cost, suppliers, certification, market trends, tips, and frequently asked questions (FAQs).
Quality is a crucial consideration when selecting a machining center. Look for high-quality machines that are durable, accurate, and offer precise performance. It is essential to consider the quality of materials used and the level of technology incorporated into the machining center.
Cost is another vital factor to evaluate when purchasing a machining center. The cost varies depending on factors such as the machine’s size, capabilities, features, and the brand. It is advisable to compare prices from different suppliers and consider the long-term return on investment rather than solely focusing on the initial purchase cost.
Finding a reliable supplier is crucial to ensure product quality, support, and after-sales service. Look for reputable suppliers that have been in the industry for years and have positive customer reviews. It is also advisable to consider suppliers who offer comprehensive training and technical support to maximize machine utilization.
Certification is essential to validate the quality and compliance of machining centers. Look for machines that have industry-standard certifications, such as ISO 9001, which ensure high levels of quality management.
The machining center market is expected to witness significant growth due to increasing demand for precise and advanced machining operations. The market is driven by industries such as automotive, aerospace, electronics, and medical manufacturing.
Some tips for purchasing a machining center are to thoroughly assess your specific machining requirements, considering factors such as the size, type of materials, and desired output. Additionally, consider factors like power consumption, ease of operation, and maintenance requirements when selecting a machine.
Frequently asked questions (FAQs) in machining center purchases often include queries regarding machine capabilities, maintenance procedures, software compatibility, training, and warranty. It is advisable to consult suppliers or refer to the manufacturer’s guidelines to clarify any doubts.
In conclusion, a machining center guide provides valuable information on quality, cost, suppliers, certification, market trends, tips, and FAQs. It is crucial to conduct thorough research, assess specific requirements, and consider long-term benefits before investing in a machining center.
Types of machining center
Machining centers are versatile and high-precision machines used in manufacturing processes for a wide range of industries. They are designed to perform various machining operations such as milling, drilling, tapping, and boring with high accuracy and efficiency. There are several types of machining centers, each designed to meet specific machining requirements. Here are some common types of machining centers:
1. Vertical Machining Centers (VMC): VMCs have a vertical spindle and a worktable that moves in the X and Y axes. They are widely used in industries like automotive, aerospace, and mold making. VMCs are suitable for manufacturing complex 3D parts and offer high flexibility, allowing for multiple setups and easy tool changes.
2. Horizontal Machining Centers (HMC): HMCs have a horizontal spindle and a pallet system, where workpieces are loaded and unloaded. They are widely used in industries like automotive, aerospace, and heavy machinery. HMCs provide better chip evacuation, higher rigidity, and can perform continuous machining for higher production rates.
3. Five-Axis Machining Centers: Five-axis machining centers have the capability to move the workpiece and the cutting tool in five different axes simultaneously. This allows for complex and precise machining of parts from various angles. Five-axis machining centers are commonly used in industries like aerospace, medical, and automotive.
4. Multi-Tasking Machining Centers: Multi-tasking machining centers combine multiple machining operations into a single machine. They have the ability to perform turning, milling, drilling, and grinding operations in one setup. Multi-tasking machining centers are ideal for manufacturing complex and high-precision parts with reduced cycle times.
5. Swiss-Type Machining Centers: Swiss-type machining centers feature a sliding headstock and a guide bushing that provides support close to the cutting tool. They are commonly used in industries like watchmaking, medical, and electronics. Swiss-type machining centers are highly accurate and efficient for high-volume production of small and intricate parts.
6. CNC Routers: CNC routers are machining centers used specifically for cutting and shaping various materials like wood, plastics, and composites. They are widely used in furniture manufacturing, sign making, and woodworking industries. CNC routers use computer-controlled movements to create precise and intricate designs.
Overall, the choice of machining center depends on the specific requirements of the intended machining operations. Each type offers its own advantages and capabilities, ensuring high productivity and accuracy in manufacturing processes.
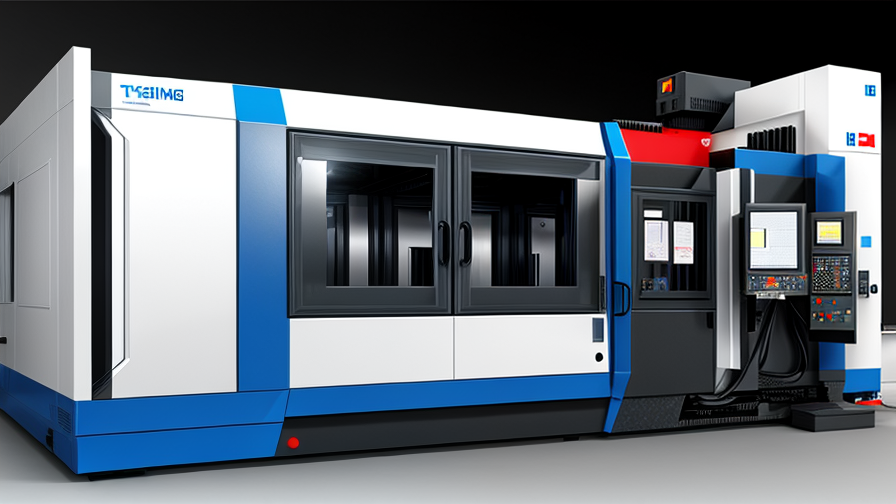
Pros and Cons of Using machining center
Machining centers are highly advanced machines used in the manufacturing industry to fabricate a wide range of products. They offer numerous advantages, but also have certain drawbacks to consider. Here, we will outline the pros and cons of using machining centers.
Pros:
1. Accuracy and Precision: Machining centers are known for their exceptional accuracy and precision in cutting, shaping, and drilling. These machines can achieve high dimensional accuracy, ensuring the production of high-quality and error-free parts.
2. Versatility: Machining centers are versatile machines capable of performing multiple operations in one setup. They can carry out milling, drilling, tapping, and other complex machining processes, reducing the need for additional machinery and increasing efficiency.
3. Increased Productivity: These machines can function continuously, with minimal downtime. They have automatic tool changers and multiple-axis capabilities, allowing for efficient and rapid machining. This results in increased productivity and shorter lead times.
4. Cost Efficiency: Although machining centers have higher upfront costs compared to conventional machines, their ability to perform multiple operations and high-speed machining leads to cost savings in the long run. They also minimize material waste, reducing overall production costs.
5. Improved Safety: Modern machining centers are equipped with safety features like automatic tool measurement, emergency stops, and machine guarding. These features protect operators and reduce the risk of accidents, making them a safer option for production environments.
Cons:
1. Initial Investment: Machining centers can be expensive to purchase, especially for small or medium-sized businesses. The cost of the machine, along with the necessary tooling, software, and maintenance, can be a significant financial burden.
2. Complex Programming: Operating a machining center requires skilled and trained personnel. The programming and setup processes can be intricate and time-consuming. Companies must invest in training and hiring experienced operators to maximize the machine’s potential.
3. Limited Flexibility: While machining centers offer high versatility, they may not be suitable for all types of jobs. Some applications require specialized machines tailored to specific tasks, limiting the flexibility of machining centers.
4. Maintenance and Repair: Regular maintenance is crucial to keep machining centers running smoothly and accurately. Maintenance costs and downtime for repairs should be factored into the overall cost of owning and operating these machines.
5. Space Requirement: Machining centers typically require a larger space compared to other traditional machines. Adequate facility space must be allocated for these machines, which can be a limitation for small-scale operations.
In conclusion, machining centers offer exceptional precision, versatility, and productivity gains. Despite the potential drawbacks of initial costs, complex programming, and limited flexibility, their benefits often outweigh the disadvantages, making them an invaluable asset in modern manufacturing environments.
machining center Reference Specifications (varies for different product)
A machining center is a highly versatile and automated machine tool used in the manufacturing industry for various operations such as milling, drilling, and tapping. These machines are capable of performing multiple tasks in a single setup, improving efficiency, accuracy, and productivity.
The reference specifications of a machining center can vary significantly depending on the specific product and its intended use. However, some general features and specifications remain consistent across different models.
One important specification of a machining center is its working capacity, which refers to the maximum size of the workpiece it can accommodate. The working capacity is determined by the dimensions of the machine’s table and the travel distances of its axes. This specification is crucial as it determines the size and complexity of the parts that can be machined.
Another key specification is the spindle speed, which determines the rotational speed at which the cutting tool operates. Higher spindle speeds are desirable for machining operations that require high-speed cutting or fine surface finishes.
The power of the machine’s spindle motor is also an essential specification. A higher power rating allows for more aggressive cutting and reduces cycle times.
The tool capacity of the machining center is another critical specification. It refers to the number of tools the machine can hold in its tool changer. A larger tool capacity enables the machine to perform more complex operations without the need for manual tool changes, thus reducing setup times.
The control system is another important specification. Modern machining centers are equipped with advanced computer numerical control (CNC) systems that offer high precision, flexibility, and ease of use. The control system should have user-friendly software and the ability to handle complex programs for efficient operation.
Additionally, features such as automatic tool measurement, tool breakage detection, and coolant system are also common in machining centers, enhancing their overall performance and reliability.
In conclusion, the reference specifications of a machining center can vary depending on the specific product. However, working capacity, spindle speed, spindle motor power, tool capacity, control system, and additional features like tool measurement and coolant system are some of the common specifications that contribute to the versatility and efficiency of these machines.
Applications of machining center
Machining centers are versatile machines used in various industries for their precision, accuracy, and efficiency. Here are some common applications of machining centers:
1. Aerospace Industry: Machining centers play a critical role in manufacturing components for the aerospace industry. They are used to fabricate aircraft parts, such as turbine blades, engine components, and landing gear. The precision and high-quality finishes achieved by these machines are essential for ensuring the safety and performance of aircraft.
2. Automotive Industry: Machining centers are widely used in the automotive industry for producing a variety of components. They are used to machine engine blocks, cylinder heads, transmission parts, and brake components. These machines are known for their ability to achieve high levels of accuracy, ensuring the proper fit and function of automotive parts.
3. Medical Industry: Machining centers are used to manufacture intricate medical devices and implants with precision. They are utilized in the production of items such as surgical tools, prosthetics, orthopedic implants, and dental fixtures. The precise dimensions and surface finishes achieved by machining centers are crucial for ensuring the functionality and compatibility of these medical devices.
4. Electronics Industry: Machining centers are employed in the electronics industry for manufacturing intricate electronic components and parts. They are used to produce printed circuit boards (PCBs), connectors, and housings for electronic devices. The high precision and accuracy provided by machining centers allow for the intricate designs and small features required in the electronics industry.
5. Defense Industry: Machining centers are extensively utilized in the defense industry for manufacturing critical components needed in military equipment and vehicles. These machines are used to produce firearms, weapon mounts, armored vehicle parts, and missile components. The high levels of precision and durability achieved by machining centers are essential for ensuring the reliability and effectiveness of defense equipment.
6. Tool and Die Industry: Machining centers are used for manufacturing various types of tools, dies, molds, and fixtures. They are employed in the production of cutting tools, injection molds, casting dies, and jigs. The ability of machining centers to achieve intricate shapes and precise dimensions makes them indispensable in the tool and die industry.
Overall, machining centers are versatile machines with numerous applications across various industries. Their ability to provide high precision, accuracy, and efficiency makes them an essential tool in manufacturing a wide range of components and products.
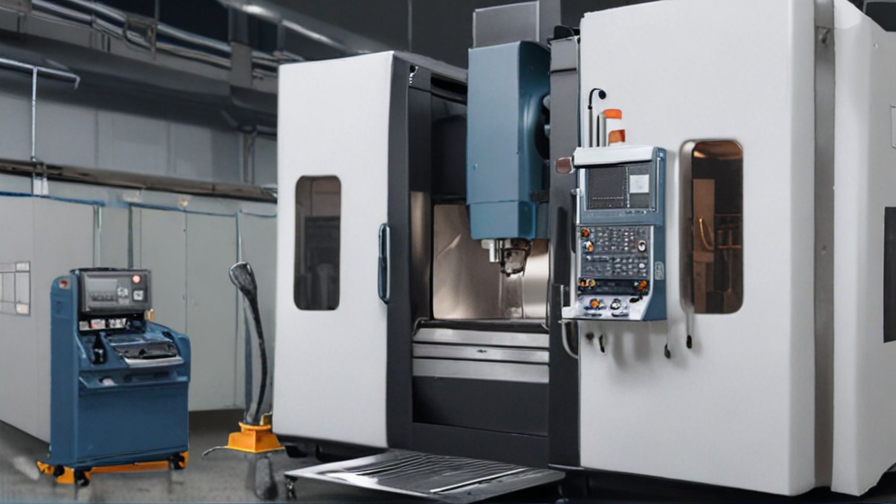
The Work Process and how to use machining center
A machining center is a highly versatile machine tool that is used for various operations such as milling, drilling, and turning. It is commonly used in manufacturing industries for precision machining of metal or other solid materials. The work process involves several steps to effectively utilize a machining center.
Firstly, the workpiece needs to be properly secured on the machine table using clamps or fixtures. This ensures that the workpiece remains stable during the machining process. The operator must carefully align the workpiece to the desired position and make sure it is securely fixed.
After securing the workpiece, the operator needs to program the machining center using computer-aided design (CAD) or computer-aided manufacturing (CAM) software. This programming involves creating a sequence of instructions that specify the tool paths, cutting speeds, feed rates, and any other parameters required for the machining operation.
Once the program is ready, it is loaded into the machining center’s control system. The operator then selects the appropriate cutting tools and tool holders and installs them in the machine’s spindle. The cutting tools should be carefully chosen based on the material being machined and the desired machining operations.
With everything set up, the operator can start the machining process. The machining center automatically moves the cutting tools along the programmed paths to remove material from the workpiece. The precise movements and cutting actions are controlled by the machine’s computerized control system, ensuring high accuracy and repeatability.
During the machining process, the operator should carefully observe the operation to ensure everything is running smoothly. They may need to periodically check and adjust the coolant or lubricant levels to maintain proper temperature and tool life. If any issues arise, the operator should stop the machining process, troubleshoot the problem, and make necessary adjustments.
Once the machining operation is complete, the operator carefully removes the finished workpiece from the machine table. They may use specialized tools or techniques to minimize the risk of damage to the machined surfaces. The workpiece can then be further processed, inspected, or used as required.
In conclusion, a machining center offers a highly efficient and versatile solution for precision machining. By following the work process described above, operators can effectively utilize a machining center to produce accurate and high-quality parts in various manufacturing applications.
Quality Testing Methods for machining center and how to control the quality
Quality testing methods for machining centers include both visual inspection and the use of specialized measuring instruments. Some commonly used methods are:
1. Visual inspection: This involves visually examining the machining center for any visible defects or irregularities such as scratches, dents, or improper assembly. It can also include checking for proper lubrication and cleanliness of the machine.
2. Dimensional measurement: Various measuring instruments like calipers, micrometers, and depth gauges are used to measure the dimensions of machined parts for accuracy and consistency. This ensures that the machining center is meeting the required tolerance levels.
3. Surface finish measurement: Instruments like surface roughness testers are used to evaluate the quality of the surface finish of machined parts. This helps identify any irregularities, scratches, or roughness that may affect the final product.
4. Performance testing: Machining centers need to undergo performance testing to ensure they are functioning as expected. This can include testing the spindle speed, feed rate, cutting tool performance, and overall machine stability and precision.
To control the quality of machining centers, several steps can be taken:
1. Regular maintenance: Regularly inspecting and maintaining the machining center, including lubrication, cleaning, and replacing worn-out parts, can prevent machine failure and ensure consistent quality.
2. Employee training: Proper training of machine operators and inspectors is crucial for understanding quality standards, identifying defects, and using measuring instruments correctly.
3. Documentation: Maintaining comprehensive records of inspection results, machine maintenance, and any identified defects can help identify patterns, track improvements, and ensure accountability.
4. Continuous improvement: Implementing quality improvement techniques such as Lean Manufacturing, Six Sigma, or Total Quality Management can help identify areas for improvement, reduce defects, and continuously enhance the quality of machining center outputs.
By employing these quality testing methods and implementing effective quality control measures, manufacturers can ensure that their machining centers consistently produce high-quality products.
machining center Sample Policy and Post-Purchase Considerations for machining center from China
Sample Policy:
1. Quality Assurance: The supplier should provide a comprehensive quality assurance policy, ensuring that the machining center meets international standards and specifications. This includes providing documentation such as certificates of compliance, quality control records, and inspection reports.
2. Warranty: The supplier should offer a reasonable warranty period for the machining center, covering parts, labor, and any necessary repairs or replacements. The warranty should be clearly defined and easily accessible to the buyer.
3. Technical Support: The supplier should provide prompt and efficient technical support, including remote assistance, troubleshooting, and guidance for operating and maintaining the machining center. This can include access to technical manuals, online resources, and a dedicated support team.
4. Spare Parts Availability: The supplier should guarantee the availability of spare parts for the machining center for at least the warranty period. This ensures that any future repairs or replacements can be quickly addressed, minimizing downtime.
Post-Purchase Considerations:
1. Installation and Training: It is essential to ensure that the supplier provides professional installation services and training for the operation, programming, and maintenance of the machining center. This can be done either on-site or through remote guidance, depending on the supplier’s capabilities.
2. Regular Maintenance: Following the supplier’s recommended maintenance schedule is crucial to ensure the optimal performance and longevity of the machining center. Regularly cleaning, lubricating, and inspecting the machine will help prevent issues and extend its lifespan.
3. Operator Training: It is advisable to provide adequate training to the operators using the machining center to maximize its efficiency and minimize the risk of accidents or improper handling. Ongoing training and refresher courses can help operators stay updated with new features or improvements.
4. Technical Support and Spare Parts: Ensuring that the supplier continues to provide reliable technical support and access to spare parts beyond the warranty period is crucial. Prompt response and easy availability of spare parts can minimize downtime and keep the machining center in optimal condition.
By carefully considering and implementing the above sample policy and post-purchase considerations, buyers can ensure a successful purchase and long-term satisfaction with their machining center from China.
Sourcing machining center from China: Opportunities, Risks, and Key Players
Sourcing machining centers from China can present both opportunities and risks for businesses. On one hand, China is known for its advanced manufacturing capabilities and competitive pricing, making it an attractive option for cost-effective procurement. China’s well-established supply chains and large-scale production capacity also offer significant opportunities for businesses looking to source machining centers.
One key opportunity for companies sourcing machining centers from China is the access to a wide range of models and specifications. Chinese manufacturers offer a diverse selection of machining centers, including vertical machining centers (VMC), horizontal machining centers (HMC), and five-axis machining centers, catering to various machining needs. This ensures that businesses can find a suitable model based on their specific requirements.
Moreover, China’s thriving machining center industry is supported by a large pool of skilled labor and engineering expertise. Local manufacturers have been investing heavily in research and development (R&D) to enhance their product quality and technological capabilities. Therefore, businesses sourcing from China can benefit from the continuous innovation and improvement in machining center technology.
However, there are also risks associated with sourcing machining centers from China. Quality control can be a concern, as some manufacturers may prioritize low cost over product reliability and durability. It is crucial to thoroughly vet suppliers, conduct factory audits, and request samples before finalizing any purchase agreements.
Intellectual property rights (IPR) protection is another concern. China has faced criticism for its lax IPR enforcement, leading to issues such as counterfeiting and unauthorized reproductions. Businesses must take appropriate measures to protect their designs and patents when sourcing from China, including proper legal contracts and strict quality control protocols.
Key players in the Chinese machining center market include Haas Automation, DMG Mori, Mazak, and Fanuc Corporation. These companies boast a strong presence and reputation both domestically and globally. Working with established and reputable manufacturers reduces the risks involved in sourcing and ensures product quality.
In conclusion, sourcing machining centers from China offers opportunities for businesses, thanks to its advanced manufacturing capabilities, competitive pricing, and extensive product range. Nonetheless, the risks associated with quality control and IPR protection must be carefully addressed. Partnering with key players in the market can mitigate some of these risks and ensure a successful sourcing experience.
How to find and select reliable machining center manufacturers in China,use google search manufacturers and suppliers
When searching for reliable machining center manufacturers in China, utilizing Google search can be an efficient approach. Here are some steps to follow:
1. Begin by typing key terms related to your requirements into the Google search bar. For example, search for “machining center manufacturers in China” or specific terms like “CNC machining center manufacturers China” for more targeted results.
2. The search results will display various manufacturers and suppliers. It is important to evaluate the credibility and reliability of the companies. Look for well-established companies with a good reputation in the industry.
3. Visit the manufacturer’s website to gather information about their products, services, and capabilities. Look for details such as the company’s history, production facilities, certifications, and client testimonials. This will help you assess their reliability and expertise.
4. Verify the manufacturer’s credentials. Check if they have relevant certifications, such as ISO 9001, which ensures adherence to quality standards. Look for any awards or recognitions they may have received.
5. Consider the company’s experience and expertise. Look for manufacturers with a long history in producing machining centers and a strong track record of delivering high-quality products. Experience often indicates a better understanding of customer needs and superior manufacturing processes.
6. Look for manufacturers who offer customization options. This is crucial if you require specific specifications or customization for your machining center. A reliable manufacturer will have the capability to accommodate individual requirements.
7. Check if the manufacturer has a team of skilled professionals. Skilled workers are crucial for ensuring the precision and quality of machining centers. A company with a dedicated and experienced workforce is more likely to produce reliable products.
8. Consider reaching out to the manufacturer directly to discuss your requirements and ask any questions you may have. This interaction will provide insight into their responsiveness, communication skills, and willingness to assist.
In conclusion, using Google search to find and select reliable machining center manufacturers in China involves evaluating the manufacturer’s credibility, assessing their capabilities and experience, verifying their credentials, and engaging in direct communication. By following these steps, you can narrow down the options and find a reliable manufacturer that meets your specific requirements.
How to check machining center manufacturers website reliable,use google chrome SEOquake check if ranking in top 10M
To determine the reliability of a machining center manufacturer’s website, you can follow these steps:
1. Use Google Chrome: Open the website in Google Chrome as it offers various extensions and tools that can help verify the reliability and popularity of a website.
2. Install SEOquake: Install the SEOquake extension on your Google Chrome browser. This tool provides detailed website statistics, such as Google PageRank, Alexa rank, indexed pages, and more.
3. Check Google PageRank: With SEOquake enabled, look for the Google PageRank icon. If the machining center manufacturer’s website has a higher PageRank (out of 10), it indicates its overall credibility and authority.
4. Check Alexa Rank: Alexa rank shows the popularity and traffic volume of a website. If the machining center manufacturer’s website has a lower Alexa rank (closer to 1), it indicates higher website traffic, which usually correlates with reliability.
5. Verify Indexed Pages: SEOquake also provides information on the number of indexed pages on the website. If the machining center manufacturer’s website has a higher number of indexed pages, it suggests that the content is extensive and regularly updated, which can be an indicator of reliability.
6. Check Ranking: With SEOquake, you can inspect the website’s ranking among the top 10 million websites globally. If the machining center manufacturer’s website is ranked within the top 10M, it implies a higher degree of popularity and trustworthiness.
7. Assess Overall User Experience: Apart from SEOquake’s insights, thoroughly navigate the website to evaluate its overall appearance, user-friendliness, customer testimonials, product information, and any certifications or awards received.
Remember, while SEOquake and other tools provide valuable insights, they are not definitive measures of a website’s reliability. Combine these objective indicators with subjective evaluations to make an informed judgment.
Top 10 machining center manufacturers in China with each 160 words introduce products,then use markdown create table compare
1. DMG MORI
DMG MORI is a leading global manufacturer of high-tech machining centers. In China, they offer a wide range of products, including vertical and horizontal machining centers. Their machines are known for their precision, reliability, and advanced technology. With cutting-edge features like high-speed spindles and automatic tool changers, DMG MORI machining centers ensure efficient and accurate operations.
2. Haas Automation
Haas Automation is renowned for its CNC machining centers. Based in the USA, they have expanded their operations in China and offer a variety of vertical and horizontal machining centers. Haas machining centers are known for their robust construction, user-friendly interface, and high-speed machining capabilities. Their machines are suitable for a wide range of applications, from aerospace to automotive industries.
3. Fanuc
Fanuc is a prominent manufacturer of CNC machining centers. With their extensive experience in the field, Fanuc offers a comprehensive range of vertical and horizontal machining centers in China. Their machines are engineered for high precision, productivity, and versatility. With advanced features like high-speed spindles and intelligent automation, Fanuc machining centers deliver exceptional performance and reliability.
| Brand | Product Range | Key Features |
| ————— | ————————————– | ————————————– |
| DMG MORI | Vertical and Horizontal Machining Centers | precision, reliability, advanced technology|
| Haas Automation | Vertical and Horizontal Machining Centers | robust construction, user-friendly interface, high-speed machining capabilities |
| Fanuc | Vertical and Horizontal Machining Centers | high precision, productivity, versatility |
4. Makino
Makino is a well-established manufacturer known for its high-performance machining centers. They provide various models of vertical and horizontal machining centers in China. Makino machines are engineered to deliver exceptional accuracy, speed, and rigidity. With features like rigid construction, advanced control systems, and superior spindle technology, Makino machining centers are ideal for intricate and complex machining operations.
5. Haas Automation
Haas Automation is another leading name in the machining center industry. With their extensive product range, they offer innovative and cost-effective machining centers in China. Haas machines are known for their durability, ease of operation, and high-performance capabilities. Suitable for a variety of industries, their machining centers ensure precise and efficient machining processes.
6. Okuma
Okuma is a renowned manufacturer of CNC machining centers in China. With a focus on technological innovation, Okuma offers a comprehensive range of vertical and horizontal machining centers. Their machines boast features like high-speed spindles, advanced control systems, and intelligent automation. Okuma machining centers provide exceptional precision, productivity, and reliability, making them an excellent choice for various applications.
| Brand | Product Range | Key Features |
| ————— | ————————————– | ————————————– |
| DMG MORI | Vertical and Horizontal Machining Centers | precision, reliability, advanced technology|
| Haas Automation | Vertical and Horizontal Machining Centers | robust construction, user-friendly interface, high-speed machining capabilities |
| Fanuc | Vertical and Horizontal Machining Centers | high precision, productivity, versatility |
| Makino | Vertical and Horizontal Machining Centers | exceptional accuracy, speed, rigidity |
| Haas Automation | Vertical and Horizontal Machining Centers | durability, ease of operation, high-performance capabilities |
| Okuma | Vertical and Horizontal Machining Centers | high-speed spindles, advanced control systems, intelligent automation |
7. Jinan Bodor
Jinan Bodor is a prominent manufacturer of laser cutting and engraving machines in China. Their product range includes various CNC laser machines, such as fiber laser cutting machines, CO2 laser engraving machines, and metal laser marking machines. Bodor machines are known for their precision, high cutting speeds, and reliable performance. With advanced laser technology, they deliver excellent results in various materials, including metals, plastics, and wood.
8. Shenyang Machine Tool
Shenyang Machine Tool is a leading manufacturer of CNC machine tools in China. They offer a wide range of products, including vertical and horizontal machining centers, CNC lathes, and grinding machines. With a strong focus on technological innovation, Shenyang Machine Tool machines are known for their precision, stability, and high-speed machining capabilities. They are widely used in industries like automotive, aerospace, and mold manufacturing.
9. Beijing Jingdiao
Beijing Jingdiao specializes in the production of high-precision machining centers and CNC engraving machines. Their product lineup encompasses vertical and horizontal machining centers, as well as 3D printers. Jingdiao machines are designed with advanced features like high-speed spindles, linear motors, and intelligent control systems. They offer exceptional accuracy, efficiency, and reliability, making them suitable for industries like electronics, medical, and mold-making.
10. Daheng Laser
Daheng Laser is a reputable manufacturer of laser cutting and engraving machines in China. They provide a comprehensive range of CNC laser machines, including fiber laser cutting machines, CO2 laser engraving machines, and laser marking machines. Daheng Laser machines are known for their high cutting precision, stability, and user-friendly operation. With advanced laser technology, they are capable of processing various materials with high efficiency and accuracy.
Background Research for machining center manufacturers Companies in China, use qcc.com archive.org importyeti.com
When it comes to researching machining center manufacturers in China, there are several platforms that can provide valuable information. Websites such as qcc.com, archive.org, and importyeti.com are useful tools for gathering background information on companies in this industry. Here is a brief overview of these platforms:
1. qcc.com: This website serves as a comprehensive database for Chinese company information. It provides access to business registration records, financial data, and other relevant details. By searching for machining center manufacturers on qcc.com, researchers can obtain information about a company’s legal status, registered capital, key personnel, and other vital statistics.
2. archive.org: Archive.org is a platform that crawls and archives websites over time. By using this tool, researchers can view historical snapshots of machining center manufacturers’ websites. This provides insight into a company’s evolution, product range, and other relevant changes that may have occurred over time.
3. importyeti.com: ImportYeti.com is a database that offers import and export data for various products and companies. By searching for importing or exporting records related to machining centers, researchers can gain valuable insights into a company’s trade activities, key global markets, and potential partnerships.
When using these platforms for research purposes, it is important to focus on key information such as the company’s history, production capabilities, certifications, customer base, and any relevant awards or achievements. Additionally, looking for customer reviews or feedback can provide insights into the company’s reputation and reliability.
Overall, by utilizing these platforms efficiently, researchers can gather essential background information on machining center manufacturers in China in a concise and precise manner.
Leveraging Trade Shows and Expos for machining center Sourcing in China
Trade shows and expos are valuable platforms for sourcing machining centers in China. They provide a unique opportunity to meet with manufacturers, explore new technologies, compare products, and build relationships with potential suppliers. Here are some key benefits of leveraging trade shows and expos for machining center sourcing in China.
1. Extensive Supplier Network: Trade shows and expos attract a large number of manufacturers and suppliers from various regions in China. This allows buyers to gain access to a wide range of machining center options and source from multiple suppliers at a single event.
2. Product Showcase: These events offer a comprehensive display of the latest advancements in machining centers. Buyers can evaluate the quality of the machines, examine their specifications, and compare them side by side. This helps in making informed decisions based on firsthand experience.
3. Face-to-Face Interaction: Trade shows and expos provide an ideal platform to meet with suppliers face-to-face. This direct interaction allows buyers to discuss their specific requirements, negotiate pricing and terms, and establish a rapport with potential suppliers. It also helps in building trust and understanding between both parties.
4. Expert Guidance: These events often feature industry experts who can provide valuable insights and guidance on machining centers. They can offer advice on selecting the right machine for specific applications, optimizing productivity, and improving overall efficiency.
5. Access to New Technologies: Trade shows and expos are where manufacturers introduce their latest technologies and innovations. Buyers can stay updated with new trends, discover cutting-edge features, and explore more advanced machining center options.
6. Networking Opportunities: Apart from meeting suppliers, trade shows and expos offer networking opportunities with other industry professionals, buyers, and even potential business partners. These interactions can lead to valuable collaborations, knowledge sharing, and growth opportunities.
To make the most of trade shows and expos, buyers should plan their visit in advance, conduct research on the exhibitors, schedule meetings with potential suppliers, and come prepared with clear specifications and questions. Additionally, buyers can take advantage of post-event follow-ups to continue negotiations, request for additional information, or obtain samples for further evaluation.
The Role of Agents and Sourcing Companies in Facilitating machining center Purchases from China
Agents and sourcing companies play a crucial role in facilitating machining center purchases from China. These intermediaries act as a bridge between buyers and manufacturers, helping to streamline the purchasing process and ensure a successful transaction.
One of the primary responsibilities of agents and sourcing companies is to identify reputable manufacturers in China that specialize in machining centers. They have a deep understanding of the local market, including the capabilities and expertise of different suppliers. By leveraging their network and market knowledge, agents can connect buyers with manufacturers that are best suited to their specific needs.
Agents also play a vital role in negotiating prices and terms on behalf of the buyer. They have experience in dealing with Chinese manufacturers and understand the cultural nuances that can influence negotiations. Additionally, they can assist with communication and language barriers, ensuring that both parties are on the same page throughout the purchasing process.
Sourcing companies go a step further by providing end-to-end support throughout the procurement journey. They conduct thorough due diligence on manufacturers to ensure they meet quality standards and have appropriate certifications. This helps buyers mitigate the risks associated with purchasing from unfamiliar suppliers.
Furthermore, agents and sourcing companies often provide inspection services, ensuring the quality and specifications of the machining centers before shipment. This minimizes the chances of receiving faulty or subpar products and gives buyers peace of mind.
Logistics and shipping are other areas where agents and sourcing companies add value. They navigate the complexities of international transportation, customs clearance, and documentation, ensuring that the machining centers reach the buyer’s location on time and in good condition.
In summary, agents and sourcing companies play a critical role in facilitating machining center purchases from China. They leverage their industry knowledge, connections, and expertise to connect buyers with reputable manufacturers, negotiate favorable terms, ensure quality control, and manage logistics. Their involvement simplifies the purchasing process and reduces the risks associated with sourcing products from China.
Price Cost Research for machining center manufacturers Companies in China, use temu.com and 1688.com
When it comes to the machinery industry, China is known for its prowess in manufacturing and exporting a wide range of products. The machining center segment is no exception, with several manufacturers competing in the market. Two popular online platforms for sourcing products from China are temu.com and 1688.com, which can provide valuable insights into the price and cost research for machining center manufacturers.
Temu.com offers a comprehensive database of Chinese suppliers, including machining center manufacturers. To conduct price and cost research, one can start by searching for machining center manufacturers on Temu.com. The platform allows users to compare prices, view product descriptions, and access supplier information. By analyzing multiple suppliers and their offerings, one can gain a better understanding of the average prices in the market, allowing for effective negotiations and cost comparisons.
1688.com also presents a vast range of manufacturers and products. This platform, owned by Alibaba Group, caters specifically to the Chinese market, providing further opportunities to explore and research machining center manufacturers. Similar to Temu.com, users can obtain information such as product specifications, prices, and supplier details. By leveraging the extensive supplier base on 1688.com, effective cost research can be conducted to identify price trends and potential cost-saving opportunities.
While conducting price and cost research on both platforms, it is essential to consider various factors that may influence pricing. These factors include the specification and quality of the machining centers, production volume, delivery time, payment terms, and after-sales support. It is crucial to communicate with suppliers directly for accurate quotes and additional cost-related information.
In conclusion, Temu.com and 1688.com are valuable online platforms for conducting price and cost research for machining center manufacturers in China. By leveraging the extensive supplier databases and comparing prices and products, businesses can make informed decisions and negotiate effectively to achieve the best possible prices while ensuring quality and efficiency in their supply chain.
Shipping Cost for machining center import from China
The shipping cost for importing a machining center from China can vary depending on several factors such as the weight and dimensions of the machine, the shipping method chosen, the distance to the destination, and any additional services required.
Generally, there are two main options for shipping: air freight and sea freight. Air freight is faster but more expensive, while sea freight is slower but more cost-effective, especially for heavy and bulky items like machining centers.
If you choose air freight, the cost will be calculated based on the weight and volume of the machine. Additionally, there may be additional charges for fuel surcharges, customs clearance, handling fees, and insurance. It is advisable to contact different freight forwarders for quotes and compare their rates.
On the other hand, sea freight is typically charged based on the cubic meter or the weight of the cargo. Additional charges may include container fees, customs documentation charges, and port handling fees. The cost can also vary depending on the type of container used, such as a full container load (FCL) or less-than-container load (LCL).
To get an accurate estimate, it is recommended to provide the freight forwarder with the exact dimensions and weight of the machining center, as well as the pick-up and delivery locations. They will be able to provide a detailed breakdown of the shipping cost, including any additional services required such as customs clearance and inland transportation.
It is important to note that in addition to the shipping cost, there may be other expenses involved in importing a machining center from China, such as import duties, taxes, customs broker fees, and any required certifications or inspections. Therefore, it is crucial to research and consider all of these factors when budgeting for the importation process.
Compare China and Other machining center Markets: Products Quality and Price,Visible and Hidden Costs
China has emerged as a major player in the machining center market, offering a wide range of products in terms of quality and price. Compared to other machining center markets, China provides a range of options that cater to different customer needs.
In terms of product quality, China has made significant advancements and its machining centers are now known for their high quality and precision. Chinese manufacturers have invested heavily in research and development, incorporating advanced technology and engineering practices into their products. Many machining centers manufactured in China now meet international standards, offering comparable quality to those produced in other markets.
When it comes to price, China is known for its competitive pricing in the machining center market. Due to lower labor and production costs, Chinese manufacturers are able to offer their products at a more affordable price compared to their counterparts in other countries. This makes China an attractive option for customers who are looking for cost-effective solutions without compromising on quality.
However, it is important to consider both visible and hidden costs when purchasing machining centers from China. Visible costs include the initial purchase price, while hidden costs may include import duties, shipping costs, and potential reliability issues. Customers should carefully evaluate these costs and factor them into their decision-making process.
Customers also need to consider the long-term maintenance and support costs when comparing China with other machining center markets. It is essential to ensure that spare parts and technical support are easily accessible to avoid any potential disruptions to operations.
In summary, China’s machining center market offers a wide range of high-quality products at competitive prices. However, customers need to carefully evaluate both visible and hidden costs, as well as long-term maintenance and support considerations when considering purchasing from China. Overall, China has become a significant player in the machining center market and provides a viable option for those seeking quality products at a lower price point.
Understanding Pricing and Payment Terms for machining center: A Comparative Guide to Get the Best Deal
When looking to purchase a machining center, understanding pricing and payment terms is crucial to ensure you get the best deal possible. Here is a comparative guide to help you navigate through this process effectively.
1. Research and Compare: Start by researching various manufacturers and suppliers to gather information on pricing and payment terms. Look for reputable companies that offer quality machinery at competitive prices.
2. Price Comparison: Obtain quotes from multiple suppliers and compare them based on the specifications, features, and performance of the machining centers offered. Ensure that you are comparing similar models to get an accurate comparison.
3. Total Cost of Ownership: When evaluating pricing, consider the total cost of ownership rather than solely focusing on the initial purchase price. This includes maintenance, operating costs, and potential future expenses such as upgrades or spare parts. A higher-priced machine with lower operating costs might be more cost-effective in the long run.
4. Negotiation: Once you have collected quotes, don’t hesitate to negotiate with the suppliers. They might be willing to offer discounts, flexible payment terms, or additional services to secure your business. Be prepared to discuss your budget and requirements to drive the negotiation in your favor.
5. Payment Terms: While negotiating, discuss payment terms that suit your financial situation. Suppliers may offer options such as upfront payment, installment plans, or leasing arrangements. Evaluate the advantages and disadvantages of each option in terms of cash flow, interest rates, and ownership of the equipment.
6. Warranty and Support: Inquire about the warranty period and after-sales support provided by the supplier. A longer warranty and reliable customer service can save you money and time in case of any issues or repairs needed.
7. Financing Options: If the upfront cost of the machining center is a concern, explore financing options provided by the supplier or consider seeking external financing from banks or leasing companies. Compare interest rates, repayment terms, and any additional fees or charges associated with these financing options.
8. Trade-in/Resale Value: Consider the potential trade-in or resale value of the machining center. Opting for a well-known brand with a strong market presence may enhance the future value of the equipment if you decide to upgrade or sell it.
9. Professional Advice: Seek advice from industry experts or consultants who can provide insights on pricing and payment terms. Their expertise can help you negotiate better deals and avoid common pitfalls.
By following this comparative guide, you can make informed decisions regarding the pricing and payment terms for a machining center. Remember to consider both the upfront cost and the long-term value to get the best deal possible.
Chinese Regulations and Industry Standards Certifications for machining center,Import Regulations and Customs for machining center from China
China has various regulations and industry standards certifications for machining centers, which are important for both domestic manufacturers and foreign importers. These certifications ensure the quality, safety, and performance of the machines being produced and imported into the country.
One of the key certifications is the China Compulsory Certification (CCC), also known as the 3C certification. It is mandatory for a wide range of products, including machining centers, to be sold and used in the Chinese market. The CCC mark indicates that the product has met the safety and quality requirements outlined by the government.
In addition to CCC, there are industry-specific certifications and standards that machining centers in China may need to comply with. For example, the China CNC Machine Tool Accreditation (CMTBA) certification emphasizes the accuracy, precision, and reliability of CNC machine tools, including machining centers. This certification is highly regarded and helps build trust among buyers and users.
When importing machining centers from China, importers must also comply with various regulations and customs procedures. Firstly, it is essential to determine if a specific import license or permit is required for the specific type of machining center being imported. The importer should also ensure that the product meets the relevant safety and quality standards of the destination country.
Customs procedures include declaring the imported goods to customs authorities, paying applicable duties and taxes, and providing necessary documentation such as commercial invoices, packing lists, and certificates of origin. It is important to work with a freight forwarder or customs broker who can assist in navigating these procedures smoothly.
In summary, machining centers in China need to meet the required certifications such as CCC and CMTBA. Importers of machining centers must comply with applicable import regulations and customs procedures, ensuring that the products meet the safety and quality standards of the destination country.
Sustainability and Environmental Considerations in machining center Manufacturing
Sustainability and environmental considerations play a crucial role in machining center manufacturing. Machining centers are widely used in industries for various applications, including metal cutting, milling, drilling, and grinding. The manufacturing process of machining centers involves multiple stages, such as material extraction, component fabrication, assembly, and waste management. Considering sustainability and environmental factors throughout these stages can have significant impacts on reducing resource consumption, minimizing waste generation, and improving overall efficiency.
To start with, material extraction is a key stage that requires careful consideration. Opting for sustainable materials, such as recycled or eco-friendly alternatives, can help minimize the environmental footprint associated with resource extraction. Furthermore, efficient material utilization and waste reduction strategies, including recycling and reusing waste materials from other industries, should be implemented. This can help reduce overall material consumption and minimize waste generation during the fabrication process.
In the component fabrication stage, energy-efficient manufacturing technologies and processes should be adopted. Utilizing advanced machining techniques, such as high-speed machining and precision tooling, can significantly reduce energy consumption and improve productivity. Additionally, implementing energy management systems to monitor and optimize energy usage can further enhance sustainability.
Assembly and waste management are also critical stages where sustainability measures should be implemented. During assembly, focus should be placed on minimizing waste production by employing lean manufacturing principles and practices. This includes proper inventory management, improved production planning, and effective communication between different departments.
Proper waste management strategies should also be in place to ensure responsible disposal of manufacturing by-products and end-of-life materials. Recycling and proper disposal methods should be followed to minimize the impact on the environment.
Finally, sustainable transportation and logistics practices should be considered. Optimizing transportation routes, utilizing fuel-efficient vehicles, and implementing efficient packaging and handling procedures can reduce the carbon footprint associated with the transportation of machining centers.
In conclusion, sustainability and environmental considerations are essential in machining center manufacturing. By implementing sustainable practices throughout the various stages, including material extraction, component fabrication, assembly, and waste management, manufacturers can reduce their environmental impact, improve resource efficiency, and contribute to a more sustainable future.
List The Evolution history of “machining center”
The evolution history of the machining center began in the 1950s with the introduction of the numerical control (NC) technology. This technology allowed machine tools to be controlled by punched paper tape or magnetic tape, reducing the need for manual operation. However, these early NC machines were limited in terms of movement, positioning, and versatility.
In the 1960s, the concept of Computer Numerical Control (CNC) emerged. CNC machines utilized computers to control the movement and operation of machine tools. This advancement allowed for greater precision and flexibility in machining operations.
In the 1970s, the first machining centers were developed. These machines combined the capabilities of milling machines and drilling machines into a single platform, providing a more efficient and streamlined process. Machining centers were equipped with automatic tool changers, allowing for multiple tool setups without the need for manual intervention.
Throughout the 1980s, machining centers continued to evolve. High-speed machining centers were developed, employing advanced cutting tools and techniques to achieve faster machining speeds and higher productivity. This period also saw the integration of additional features such as automatic pallet changers and multiple-axis movements, enabling complex machining operations in a single setup.
By the 1990s, machining centers became more compact and modular, allowing for easy customization and adaptation to specific machining requirements. The introduction of simultaneous five-axis machining centers enabled the machining of complex geometries from multiple angles, revolutionizing the aerospace and automotive industries.
In the 2000s, with the progress of robotics and automation, machining centers incorporated robotic arms for workpiece handling, further enhancing productivity and reducing labor costs. Additionally, advancements in cutting tool materials and coatings improved machining performance and longevity.
Today, machining centers continue to evolve with the advent of Industry 4.0 technologies. Internet of Things (IoT) connectivity enables real-time monitoring and data exchange, optimizing production processes and assisting in predictive maintenance. Additionally, additive manufacturing capabilities are being integrated into machining centers, allowing for hybrid manufacturing where both subtractive and additive processes can be performed in a single machine.
Overall, the evolution of machining centers has been driven by the need for increased efficiency, accuracy, and versatility in the manufacturing industry. From the early days of NC technology to the integration of advanced robotics and IoT, machining centers have continuously pushed the boundaries of machining capabilities, revolutionizing the way products are manufactured.
The Evolution and Market Trends in machining center Industry
The machining center industry has witnessed significant evolution and market trends over the years. Initially, machining centers were manually operated, requiring skilled operators to complete tasks. However, with advancements in technology, the industry has embraced automation and computer numerical control (CNC) machines, which have revolutionized the production process.
One prominent trend in the machining center industry is the shift towards high-speed machining. Manufacturers are increasingly demanding machining centers that can deliver faster cutting speeds and higher precision, allowing for improved productivity and reduced production times. This trend has been fueled by customer demand for quicker turnaround times and increased competitiveness in the market.
Another key trend in the industry is the integration of advanced technologies, such as Artificial Intelligence (AI) and Internet of Things (IoT), into machining centers. AI-powered machining centers can optimize machining processes by analyzing data and making real-time adjustments to improve accuracy and efficiency. IoT integration enables remote monitoring and predictive maintenance, reducing downtime and enhancing overall equipment effectiveness.
Additionally, there has been a growing focus on sustainability and energy efficiency within the machining center industry. Manufacturers are actively seeking machines that consume less energy and generate fewer emissions, aligning with environmental regulations and sustainability goals. This trend has led to the development of eco-friendly machining centers that minimize waste and optimize energy consumption, thereby reducing the environmental impact.
The market for machining centers has also seen a shift towards customization. Customers increasingly demand machines tailored to their specific requirements, resulting in a rise in the production of customized machining centers. Manufacturers are offering modular designs and flexible configurations to cater to diverse customer needs, ranging from automotive and aerospace industries to medical and electronics sectors.
Moreover, the machining center industry is witnessing increasing global competition. As emerging economies such as China, India, and Brazil invest heavily in industrialization, they are becoming major players in the machining center market. This has led to intensified competition among manufacturers, resulting in technological advancements and cost-effective solutions to gain a competitive edge.
Overall, the machining center industry has evolved significantly, driven by trends such as high-speed machining, advanced technologies integration, sustainability, customization, and global competition. Manufacturers must stay abreast of these trends to meet customer demands and stay competitive in an ever-evolving market.
Custom Private Labeling and Branding Opportunities with Chinese machining center Manufacturers
Chinese machining center manufacturers offer a wide range of opportunities for custom private labeling and branding. With their advanced technology and expertise in precision engineering, these manufacturers can provide high-quality machining centers that can be customized and branded to meet the specific needs of businesses and clients.
One key advantage of partnering with Chinese machining center manufacturers is their flexibility in accommodating custom requirements. These manufacturers have the capabilities to personalize machining centers according to the client’s specifications, including size, design, features, and functionalities. By leveraging their expertise, businesses can create machines that are tailor-made to their exact requirements.
In addition to customization, Chinese machining center manufacturers also offer private labeling and branding opportunities. Clients have the option to stamp their own logo, brand name, and other identifying information on the machines. This enables businesses to promote and establish their own brand identity in the market. With the machines carrying their brand, companies can increase brand visibility, enhance brand recall, and differentiate themselves from competitors.
Moreover, partnering with Chinese manufacturers for private labeling and branding provides cost-effective solutions. These manufacturers offer competitive prices without compromising on quality. By leveraging China’s manufacturing capabilities and cost advantages, businesses can increase their profit margins while offering high-quality machines to their customers.
Overall, Chinese machining center manufacturers present enticing opportunities for businesses seeking custom private labeling and branding options. With their expertise, flexibility, and cost advantages, these manufacturers can support businesses in creating unique and personalized machines, enhancing brand recognition, and achieving market differentiation.
Tips for Procurement and Considerations when Purchasing machining center
When it comes to procuring a machining center, there are several considerations that need to be taken into account. Here are some tips to help guide you in the procurement process:
1. Identify the specific requirements: Before purchasing a machining center, it is important to clearly define your requirements. Consider factors such as the type of materials to be used, the size and complexity of the parts to be machined, and the desired level of automation.
2. Research different types and models: There are various types of machining centers available, such as vertical machining centers (VMCs) and horizontal machining centers (HMCs). Research different models and their respective features to find the one that best suits your needs.
3. Quality and reliability: Look for a reputable supplier who offers high-quality machining centers. Consider the reputation of the manufacturer, read customer reviews, and check if the supplier has certifications or awards for their products.
4. Technical specifications: Pay attention to the technical specifications of the machining center, such as the spindle speed, tool capacity, and accuracy. Ensure that the specifications meet your machining requirements and future expansion plans.
5. Ease of use and training requirements: Consider the ease of use of the machining center, especially if you have operators with varying levels of experience. Training and support should be readily available from the supplier to ensure smooth operation and optimum performance.
6. Cost and long-term value: Determine your budget and compare prices from different suppliers. However, it is important to prioritize long-term value over the initial cost, as a reliable and efficient machining center may save you money in the long run through improved productivity and reduced maintenance costs.
7. Service and support: Choose a supplier that offers excellent after-sales service and support. They should provide technical assistance, spare parts availability, and maintenance services to ensure minimal downtime and maximum uptime of your machining center.
8. Future expansion and compatibility: Consider your future needs and plans for expansion. Ensure that the machining center you choose is compatible with other equipment in your facility and can accommodate potential upgrades or additions.
In conclusion, purchasing a machining center requires careful consideration of your specific requirements, quality and reliability of the equipment, technical specifications, ease of use, long-term value, service and support, and compatibility with future expansion plans. Taking these factors into account will help ensure that you make an informed decision and acquire a machining center that meets your needs and provides optimal performance.
FAQs on Sourcing and Manufacturing machining center in China
Q1: Can I trust Chinese manufacturers to source and manufacture a machining center?
Yes, Chinese manufacturers have gained a reputation for their expertise and efficiency in the machining industry. They have extensive experience in producing a wide range of high-quality machinery for various industries worldwide. However, it is essential to conduct thorough research and due diligence to select a reliable and reputable manufacturer.
Q2: How do I find a reliable machining center manufacturer in China?
To find a reliable manufacturer, you can start by researching online directories, trade platforms, and industry-specific websites. Evaluate the manufacturer’s reputation, years of experience, client testimonials, and certifications. It is recommended to engage in direct communication, visit their facilities, or even send a representative to ensure credibility.
Q3: How can I ensure the quality of the machining center I source from China?
To ensure the quality of the machining center, consider the following steps:
1. Request comprehensive documentation, including specifications, certifications, and quality control processes.
2. Ask for samples or prototypes to assess the quality firsthand.
3. Inspect the manufacturing facilities and ensure they meet international standards.
4. Consider sourcing from manufacturers with ISO certifications or other relevant industry certifications.
5. Implement a strict quality control plan and conduct inspections during the manufacturing process.
Q4: What are the advantages of sourcing and manufacturing a machining center in China?
Sourcing and manufacturing in China can provide several advantages, including:
1. Cost-effectiveness: China offers lower labor costs, making machinery more affordable compared to other regions.
2. Extensive manufacturing capabilities: Chinese manufacturers have advanced machinery, skilled labor, and well-established supply chains, allowing for efficient production at scale.
3. Wide range of options: China has a vast network of manufacturers offering a wide range of machining centers, enabling customization and meeting specific requirements.
4. Access to innovation: China’s machining industry is known for embracing new technologies and innovation, allowing you to access the latest advancements in machining centers.
Q5: What are the potential challenges in sourcing and manufacturing a machining center in China?
While there are several advantages, potential challenges include:
1. Language and communication barriers.
2. Intellectual property protection: Ensure proper agreements and protection measures are in place.
3. Quality control: Frequent inspections and strong agreements can mitigate risks.
4. Delivery and logistics: Plan in advance to address any potential delays or issues.
5. Cultural differences: Acknowledge and adapt to cultural differences to establish effective business relationships.
In conclusion, sourcing and manufacturing a machining center in China can be a cost-effective and beneficial option. However, thorough research, due diligence, and proper business practices are crucial to ensure a successful partnership with a reliable manufacturer.
Why contact sourcifychina.com get free quota from reliable machining center suppliers?
Sourcifychina.com, a sourcing platform for manufacturing in China, offers a unique advantage by providing users with a free quota from reliable machining center suppliers. There are several reasons why Sourcifychina.com offers this benefit.
Firstly, Sourcifychina.com has established strong relationships with a network of reliable machining center suppliers in China. These suppliers have been vetted and evaluated for their quality, reliability, and adherence to international manufacturing standards. By partnering with such suppliers, Sourcifychina.com ensures that users receive competitive pricing, high-quality products, and on-time delivery.
Secondly, offering a free quota from reliable machining center suppliers allows Sourcifychina.com to attract and engage potential customers. This benefit encourages users to explore the platform and take advantage of the services offered. By removing the barrier of initial costs, Sourcifychina.com enables users to experience the value and capabilities of their network of machining center suppliers without any financial commitment.
Furthermore, providing a free quota from reliable machining center suppliers helps users mitigate risks associated with manufacturing in China. Many businesses may be hesitant to engage with suppliers in China due to concerns such as product quality, communication issues, and cultural differences. Sourcifychina.com eliminates these uncertainties by pre-selecting reliable suppliers, establishing clear communication channels, and offering transparent pricing. This ensures a smooth and successful collaboration between the users and the machining center suppliers.
Lastly, Sourcifychina.com aims to empower businesses of all sizes and budgets to access reliable and cost-effective manufacturing solutions. By offering a free quota, the platform democratizes the sourcing process and provides smaller businesses with an opportunity to compete on a global scale. This inclusivity aligns with Sourcifychina.com’s mission to bridge the gap between international buyers and Chinese suppliers.
In conclusion, Sourcifychina.com offers a free quota from reliable machining center suppliers to provide users with a cost-effective, risk-mitigated, and inclusive sourcing experience. By leveraging their network of trusted suppliers and eliminating financial barriers, Sourcifychina.com aims to facilitate successful manufacturing partnerships between international buyers and Chinese suppliers.