Introduce about plastic machining guide,Qulity,Cost,Supplier,Certification,Market,Tips,FAQ
Plastic machining is the process of creating high-quality plastic components using various machining techniques. This plastic machining guide will provide you with valuable information regarding the quality, cost, suppliers, certifications, market trends, tips, and frequently asked questions related to plastic machining.
Quality is of utmost importance in plastic machining. The components produced should have precise dimensions, smooth finishes, and excellent performance characteristics. To ensure high quality, it is crucial to work with reputable suppliers who have the required expertise and machinery to deliver accurate and consistent results.
In terms of cost, plastic machining offers a cost-effective solution compared to other manufacturing methods, such as injection molding. Machining allows for flexibility in producing low to medium volume parts without the need for expensive tooling. However, costs may vary depending on the complexity of the component, material selection, and machining techniques employed.
When searching for a plastic machining supplier, consider their experience in the industry, capabilities, and adherence to quality standards. It is beneficial to work with suppliers who hold certifications like ISO 9001, which ensures compliance with international quality management standards.
The market for plastic machining is growing steadily due to the increased demand for high-performance plastic components across various industries like automotive, electronics, medical, and aerospace. With advancements in machining technologies, the versatility of plastics, and the need for customized solutions, the market is expected to witness further growth.
Here are a few tips to ensure successful plastic machining:
1. Select the appropriate plastic material with suitable properties for your application.
2. Optimize the design for machining to minimize waste and reduce production time.
3. Choose the appropriate machining techniques, such as CNC milling, turning, or drilling, based on the component’s requirements.
4. Regularly monitor and measure the quality of machined parts to maintain consistency.
Frequently Asked Questions (FAQ):
Q: What are the advantages of plastic machining?
A: Plastic machining offers flexibility, cost-effectiveness, and the ability to produce complex components with tight tolerances.
Q: What materials can be machined?
A: Various plastic materials, such as ABS, acrylic, polycarbonate, nylon, and PTFE, can be machined.
Q: How long does plastic machining take?
A: The time required for plastic machining depends on factors like component complexity, material selection, and batch size. It can range from a few hours to several days.
In conclusion, plastic machining is a versatile manufacturing process capable of producing high-quality plastic components at a reasonable cost. By understanding the quality, cost, suppliers, certifications, market trends, and following the provided tips, you can effectively navigate the world of plastic machining.
Types of plastic machining
Plastic machining is the process of shaping, cutting, and modifying plastic materials to create various components. It involves the use of tools and machinery to achieve precise and accurate results. There are several types of plastic machining methods commonly used in industries.
1. CNC Machining: Computer Numerical Control (CNC) machining is a highly efficient and precise method of plastic machining. It utilizes computer-controlled machines to carry out complex cutting, drilling, and shaping tasks. CNC machines are programmed with specific instructions, allowing for high levels of accuracy and repeatability across large production volumes.
2. Injection Molding: Injection molding is a common plastic machining technique used for mass production of plastic components. It involves melting plastic resin pellets and injecting the molten material into a mold cavity. The injected plastic then solidifies, taking the shape of the mold. Injection molding offers high production rates and can produce complex parts with minimal post-processing.
3. 3D Printing: Also known as additive manufacturing, 3D printing is a revolutionary plastic machining technique that builds components layer by layer. It uses computer-aided design (CAD) software to create a 3D model. The printer then deposits the plastic material, typically in filament or liquid form, layer by layer based on the model’s specifications. 3D printing allows for rapid prototyping and the production of highly intricate designs.
4. Laser Cutting: Laser cutting is a precision plastic machining method that uses a high-powered laser beam to cut through or engrave plastic sheets. The laser beam melts and vaporizes the plastic, creating a clean and precise cut. It is commonly used for creating intricate designs or shapes on plastics.
5. Routing and Milling: Routing and milling are traditional plastic machining methods that involve cutting, shaping, and drilling plastic materials using rotary cutting tools. Routing uses a rotating cutter to remove excess plastic material, while milling uses a rotating cutter to remove material from a workpiece’s surface.
6. Thermoforming: Thermoforming is a plastic machining technique used to create large, hollow plastic components. It involves heating a plastic sheet until it becomes pliable and then shaping it using a mold or vacuum. Thermoforming is commonly used in industries such as automotive, packaging, and signage.
In conclusion, plastic machining encompasses a range of methods that allow for the shaping, cutting, and modification of plastic materials. Whether it is CNC machining, injection molding, 3D printing, laser cutting, routing and milling, or thermoforming, each technique offers its own advantages and applications in various industries.
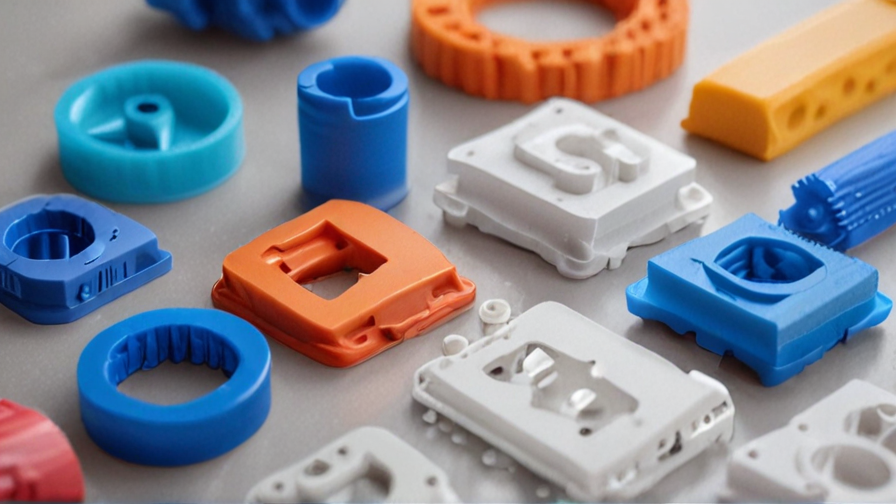
Pros and Cons of Using plastic machining
Plastic machining is a process that involves shaping and forming plastic materials through cutting, milling, drilling, or bending. It offers several advantages and disadvantages, which are summarized below:
Pros:
1. Versatility: Plastic machining allows for the production of complex and intricate components that are difficult to manufacture using other methods. It offers a wide range of design possibilities and flexibility in creating customized parts to meet specific requirements.
2. Cost-effective: Compared to other manufacturing processes like injection molding, plastic machining can be more cost-effective, especially for shorter production runs. It eliminates the need for expensive molds, which can significantly reduce upfront costs.
3. Quick turnaround time: Plastic machining offers faster production times, making it ideal for projects with tight deadlines. With shorter setup times and no need for mold development, manufacturers can quickly produce parts according to demand.
4. Material diversity: Plastic machining supports a wide range of plastic materials, including thermoplastics and thermosets, offering different mechanical and chemical properties. This versatility allows manufacturers to select the most suitable material for each application, ensuring performance and durability.
5. Precision and accuracy: Machining processes, such as CNC milling, offer high levels of precision, accuracy, and repeatability. This is important for applications that require tight tolerances and consistent performance, ensuring that parts function as intended.
Cons:
1. Material limitations: While plastic machining supports a broad range of plastic materials, it may not be suitable for all types. Some plastics may have poor machinability or may not withstand the stresses of machining processes, leading to material degradation or poor surface finish.
2. Cost for large-scale production: Although plastic machining can be cost-effective for smaller production runs, it may not be as economical for large-scale manufacturing. Injection molding or other mass production methods can be more efficient and affordable for high-volume production.
3. Waste generation: Plastic machining produces waste in the form of plastic chips or dust. Proper disposal or recycling of this waste is necessary to minimize environmental impact, adding an additional step to the process.
4. Limited part size: Plastic machining may have limitations in terms of the size of parts that can be manufactured. Machinery size and capabilities can impose restrictions on the dimensions of the components that can be produced.
5. Time-consuming for intricate designs: Highly complex designs can take longer to machine, especially if they require multiple setups or specialized tooling. The intricacy of the design can also increase the likelihood of errors or quality issues during the machining process.
In conclusion, plastic machining offers versatility, cost-effectiveness for shorter production runs, quick turnaround times, material diversity, and high precision. However, it may have limitations in terms of material suitability, cost for large-scale production, waste generation, part size, and time consumption for intricate designs.
plastic machining Reference Specifications (varies for different product)
Plastic machining is a manufacturing process used to shape plastic materials into desired products or components. It involves the use of various tools and techniques to remove material from the plastic workpiece and achieve the desired dimensions and surface finish. Reference specifications for plastic machining may vary depending on the specific product being manufactured, but there are some common factors to consider.
Firstly, the type of plastic being machined is an important consideration. Different plastics have different properties, such as hardness, strength, and thermal conductivity, which can affect the machining process. Reference specifications should include the specific type of plastic being used, as well as any special considerations or techniques required for machining that particular material.
Secondly, the dimensions and tolerances of the final product need to be clearly defined. This includes specifications for length, width, height, and any other critical dimensions. Tolerances determine the allowable variation in dimensions and ensure that the final product meets the required specifications. It is important to specify both the nominal dimensions and the tolerances to ensure accurate and consistent machining.
Surface finish requirements should also be included in the reference specifications. This includes specifying the desired smoothness or roughness of the machined surface. Surface finish is typically measured in units such as Ra (roughness average) or Rz (average maximum roughness depth), and the desired values should be clearly defined.
Other important considerations include any special features or details required for the product, such as holes, threads, or complex geometries. These features may require specific machining techniques or tools, and their specifications should be clearly outlined.
Additionally, reference specifications should include any specific quality or testing requirements. This may include dimensional inspections, material testing, or visual inspections to ensure the product meets the required standards.
In summary, reference specifications for plastic machining should include information about the type of plastic being machined, the desired dimensions and tolerances, surface finish requirements, special features or details, and any specific quality or testing requirements. By providing clear and detailed specifications, manufacturers can ensure that the plastic machining process produces high-quality and precise products.
Applications of plastic machining
Plastic machining refers to the process of removing material from a plastic workpiece using various machining techniques such as milling, turning, drilling, and grinding. This versatile method is widely utilized in various industries due to its numerous applications. Here are some key applications of plastic machining:
1. Prototyping: Plastic machining is commonly used in prototyping processes, allowing manufacturers to create functional prototypes for testing and validation before mass production. It enables engineers to refine designs and make necessary modifications quickly and cost-effectively.
2. Automotive Industry: Plastic machining finds its application in the automotive industry for manufacturing various components. It is used for producing engine parts, interior components, dashboards, panels, and even lightweight exterior body panels. Plastic machining ensures precise shaping and finishing, meeting the automotive industry’s stringent requirements.
3. Electronics and Electrical Industry: Plastic machining is utilized in the production of electrical and electronic components. It allows for the precise fabrication of insulating materials, enclosures, connectors, and housings required in the assembly of electronic devices, circuit boards, and electrical equipment.
4. Medical and Healthcare: Plastic machining plays a vital role in the medical and healthcare sector. It is used extensively in the production of medical devices, equipment, and prosthetics. Plastic machining enables the fabrication of components with intricate geometries, ensuring high precision, biocompatibility, and sterility.
5. Aerospace and Defense: Plastic machining is crucial in the aerospace and defense industry for manufacturing lightweight and high-performance components. It is used for producing aircraft interior components, missile parts, thermal insulation materials, and various other specialized components required in these sectors.
6. Consumer Goods: Plastic machining is employed in the production of various consumer goods. It enables the manufacturing of aesthetically pleasing and functional products such as toys, kitchenware, packaging materials, and consumer electronics.
7. Energy Sector: Plastic machining finds its application in the energy sector, particularly in renewable energy systems. It is used for producing components such as wind turbine blades, solar panel frames, and housing for energy storage systems. Plastic machining ensures the precise fabrication of these components, contributing to the efficient and reliable functioning of renewable energy systems.
In summary, plastic machining has a wide range of applications across multiple industries. Its versatility, precision, and ability to produce complex geometries make it an indispensable process for manufacturing various products, including prototypes, automotive components, electronics, medical devices, aerospace parts, consumer goods, and components for energy systems.
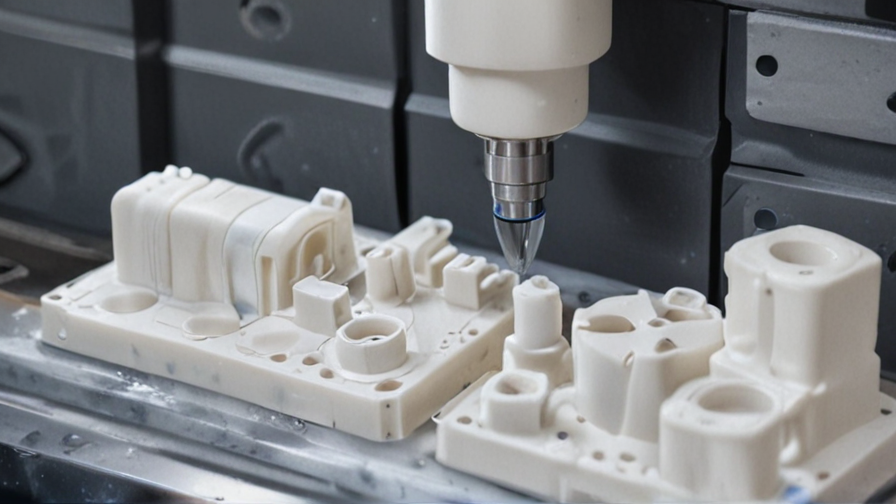
The Work Process and how to use plastic machining
Plastic machining is a process used to shape and create various parts and components from plastic materials. It involves the use of various machining techniques such as drilling, milling, turning, and cutting to achieve the desired shape and size.
The work process starts with the selection of the appropriate plastic material for the application. There are various types of plastics available, each with different properties such as strength, temperature resistance, and chemical resistance. The selection is based on the specific requirements of the project.
Once the material is chosen, the machining process begins. The first step is to create a design or blueprint of the desired part using computer-aided design (CAD) software. This allows for precise dimensions and specifications to be defined.
The next step is the preparation of the plastic material for machining. This involves cutting the material into the required size and shape to fit the machining equipment. The material is then secured using clamps or fixtures to ensure stability during the machining process.
Drilling is often the first machining technique used to create holes or cavities in the plastic. It involves using a drill bit to remove material in a circular motion. Milling is another common technique used to remove material from the surface of the plastic, creating flat or curved shapes. Turning is utilized to create cylindrical shapes by rotating the plastic material against a cutting tool.
Cutting is used to separate the plastic material into individual parts. This can be done manually or with the use of automated cutting equipment. It involves following the design specifications to accurately cut the plastic material.
After the machining process is complete, the finished parts undergo quality control and inspection to ensure they meet the required specifications. This may include measurements, visual inspection, and testing for functionality.
Overall, plastic machining is a versatile process used to create a wide range of plastic parts and components. It requires careful material selection, precise machining techniques, and quality control to achieve the desired results. By following these steps, plastic machining can be successfully utilized in various industries and applications.
Quality Testing Methods for plastic machining and how to control the quality
Quality testing methods for plastic machining include visual inspection, dimensional inspection, and performance testing. These methods help ensure the quality of the machined plastic components while controlling the manufacturing process.
Visual inspection is a simple yet effective method to identify any surface defects on the machined plastic parts. It involves examining the components under proper lighting conditions to detect any cracks, scratches, or deformities. This inspection ensures that the parts are visually appealing and free from any visual defects.
Dimensional inspection involves measuring the physical dimensions of the machined plastic components accurately. This method ensures that the parts meet the specified size and shape requirements. Various tools like calipers, micrometers, or laser measurement systems are used to measure dimensions such as length, width, thickness, and hole diameters. The measurements are compared against the component’s design specifications to ensure dimensional accuracy.
Performance testing evaluates the functional characteristics of the machined plastic parts. This testing determines if the components can withstand intended loads, pressures, or temperatures during their application. For example, a plastic valve may undergo a pressure test to ensure it can withstand the required pressure without leakage. Similarly, plastic components used in electrical applications may undergo electrical resistance or insulation testing to ensure their functionality and safety.
To control the quality of plastic machining, several measures can be implemented. Firstly, the use of high-quality raw materials is vital. Ensuring that the plastic materials used are of consistent composition and meet the necessary quality standards is crucial for producing reliable machined components. Secondly, robust machining processes should be established and followed consistently. This includes selecting appropriate cutting tools, maintaining proper machine parameters, and following recommended cutting strategies. This consistency helps in controlling dimensional accuracy and surface finish.
Regular calibration and maintenance of measuring equipment used for dimensional inspection is also necessary to ensure accurate measurements. Additionally, implementing proper documentation and tracking systems throughout the manufacturing process allows for effective quality control and traceability.
In conclusion, visual inspection, dimensional inspection, and performance testing are essential quality testing methods for plastic machining. By employing these methods and implementing measures for quality control, manufacturers can ensure that the machined plastic components meet the necessary quality standards.
plastic machining Sample Policy and Post-Purchase Considerations for plastic machining from China
Sample Policy:
1. Order Acceptance: The supplier should provide a clear confirmation of the order, including detailed specifications, quantities, and agreed-upon delivery dates. Any changes to the order should be communicated and agreed upon by both parties.
2. Quality Assurance: The supplier should have a comprehensive quality control system in place. They should provide samples or prototypes for approval before mass production. Additionally, regular inspections and testing should be conducted throughout the manufacturing process to ensure the final products meet the required standards.
3. Lead Time: A specific lead time should be agreed upon between the buyer and the supplier. This should include production time, packaging, and shipping time. The supplier should adhere to the agreed-upon schedule, providing regular updates on the progress of the order.
4. Packaging and Shipping: The supplier should pack the products securely to prevent any damage during transportation. The packaging should adhere to international shipping standards and clearly indicate the buyer’s and supplier’s details. The supplier should also provide accurate shipping documentation and tracking information.
Post-Purchase Considerations:
1. Inspection upon Receipt: Upon receiving the products, a thorough inspection should be carried out to ensure they meet the required specifications and quality standards. Any discrepancies or damages should be documented and reported to the supplier immediately.
2. Communication with the Supplier: Maintain regular communication with the supplier to address any concerns or issues that may arise. Promptly inform the supplier of any defects or problems encountered with the plastic machined parts. Open and transparent communication is key to resolving any post-purchase issues.
3. Resolution of Discrepancies: If any discrepancies or defects are found, notify the supplier promptly and provide supporting evidence. Ideally, resolve the issues through negotiation and reach an agreed-upon solution that satisfies both parties. This may involve replacements, repairs, or refunds.
4. Long-term Relationship: Establishing a long-term relationship with the plastic machining supplier can be beneficial for future orders. Regular feedback and reviews are essential for the supplier to improve their processes and provide better service in the future.
By following a well-defined sample policy and considering post-purchase aspects, buyers can ensure a smooth plastic machining process, maintain quality standards, and build a reliable and productive relationship with their Chinese supplier.
Sourcing plastic machining from China: Opportunities, Risks, and Key Players
China is a preferred destination for sourcing plastic machining due to its competitive costs, vast infrastructure, and skilled labor force. The country offers numerous opportunities for businesses looking to procure plastic machining services at affordable prices.
One of the key opportunities of sourcing plastic machining from China is the availability of a large number of manufacturers. China is home to many plastic machining companies, ranging from small-scale to large-scale operations. This vast pool of manufacturers provides buyers with an extensive range of options to choose from, ensuring competitive pricing and flexibility in terms of production capacity.
Moreover, Chinese manufacturers have expertise in various plastic machining techniques, including CNC machining, injection molding, and 3D printing. This allows buyers to find suppliers that best match their specific requirements and technical needs.
The cost advantage is another significant opportunity. China’s low labor and manufacturing costs enable businesses to save substantially on production expenses. The availability of raw materials and resources at competitive prices further contributes to cost savings. Consequently, outsourcing plastic machining to China can enhance the profitability and competitiveness of businesses in the global market.
However, there are risks associated with sourcing plastic machining from China as well. Quality control can be a concern, especially when dealing with unknown or unreliable suppliers. Language barriers and cultural differences may also hinder effective communication and collaboration, leading to misunderstandings or delays in production.
Shipping and logistics can pose a potential risk as well. The distance between China and other countries may result in longer lead times and higher transportation costs. Moreover, political instability or trade disputes can disrupt supply chains, causing uncertainties for businesses relying heavily on Chinese suppliers.
Key players in the Chinese plastic machining industry include Foxconn, Bourns, Zowee, and Shenzhen OKM Electronics Co., Ltd. These companies have established a strong reputation in the market and serve both domestic and international clients. Working with well-established players can mitigate risks and ensure a certain level of quality and professionalism.
In conclusion, sourcing plastic machining from China provides numerous opportunities, primarily cost savings and a wide range of suppliers with various expertise. However, risks such as quality control, shipping, and logistics must be carefully considered. Engaging with reputable key players can help mitigate these risks and ensure a successful outsourcing experience.
How to find and select reliable plastic machining manufacturers in China,use google search manufacturers and suppliers
When searching for reliable plastic machining manufacturers in China, using google search manufacturers and suppliers can be an effective method. Here are a few steps to follow in order to find and select the right manufacturer:
1. Start by conducting a search on Google using keywords like “plastic machining manufacturers in China” or “plastic machining suppliers in China.” This will help you identify a list of potential manufacturers.
2. Visit the websites of these manufacturers to gather more information about their services, capabilities, and product offerings. Look for testimonials, certifications, and case studies that demonstrate their reliability and expertise in plastic machining.
3. Check if the manufacturers have relevant experience in your industry or the specific type of plastic machining you require. Look for any previous projects they have worked on that are similar to your requirements.
4. Assess the manufacturer’s production capacity and capabilities. Make sure they have the necessary equipment, technology, and skilled workforce to handle your project efficiently and effectively.
5. Look for any quality management certifications and standards that the manufacturer adheres to, such as ISO 9001. This indicates their commitment to delivering high-quality products and services.
6. Read customer reviews and feedback on the manufacturer’s website or on external platforms. This will give you insights into their reputation and customer satisfaction levels.
7. Contact the shortlisted manufacturers and request a quote or discuss your specific requirements in detail. Assess their responsiveness, willingness to provide necessary information, and ability to understand your needs.
8. If possible, request samples or visit their manufacturing facilities to see their operations firsthand. This will help you evaluate their production processes, quality control measures, and overall professionalism.
9. Consider the manufacturer’s pricing, lead time, and terms of service. While cost is important, be cautious of unusually low prices, as they may indicate compromised quality or hidden costs.
10. Finally, make your decision based on a combination of factors including experience, reputation, quality, customer feedback, and overall cost-effectiveness.
By following these steps, you can narrow down your options and select a reliable plastic machining manufacturer in China that meets your specific requirements.
How to check plastic machining manufacturers website reliable,use google chrome SEOquake check if ranking in top 10M
When assessing the reliability of a plastic machining manufacturer’s website, there are a few steps you can follow. First, using Google Chrome and the SEOquake tool can be helpful in checking its ranking.
1. Use Google Chrome: Start by opening the manufacturer’s website in Google Chrome. This browser has built-in security features and is known for its reliability.
2. Install SEOquake: Install the SEOquake extension/plugin for Google Chrome. This tool provides valuable SEO-related information about a website, including its ranking and other useful metrics.
3. Check the Ranking: With the website open, click on the SEOquake icon in your browser’s toolbar. This will display an overview of the website’s SEO performance. Look for the “Alexa Rank” or similar indicator. If the website is ranked within the top 10 million, it generally suggests decent traffic and engagement.
4. Assess Other Factors: While ranking is a good starting point, it should not be the sole factor in determining reliability. Consider other aspects such as the website’s design, content quality, user experience, and the information provided.
5. Verify Contact Information: Reliable manufacturers usually provide clear and complete contact information, including a physical address, phone number, and email address. Look for this information on the website to ensure it is legitimate.
6. Read Reviews and Testimonials: Look for reviews and testimonials from other customers who have used the manufacturer’s services. This can provide insights into their reputation, customer satisfaction, and overall reliability.
7. Look for Certifications or Industry Affiliations: Reliable manufacturers often display relevant certifications or affiliations on their website. These demonstrate their commitment to quality standards and industry best practices.
In conclusion, using Google Chrome and SEOquake can help you gauge the reliability of a plastic machining manufacturer’s website through its ranking. However, it is essential to consider other factors such as website design, content quality, contact information, customer reviews, and industry affiliations.
Top 10 plastic machining manufacturers in China with each 160 words introduce products,then use markdown create table compare
1. Plastic Machining Co., Ltd.:
Plastic Machining Co., Ltd. is a leading plastic machining manufacturer in China. They specialize in producing high-quality plastic components for various industries. Their product range includes CNC machined plastic parts, plastic sheet fabrication, plastic injection molding, and custom plastic components. With advanced equipment and a dedicated team, they ensure excellent precision and reliable performance in all their products.
2. Plastic Tech Industries:
Plastic Tech Industries is another well-known plastic machining manufacturer in China. They offer a wide range of plastic machining services, including CNC milling, turning, drilling, and threading. Their products are made from different types of plastic materials such as PVC, ABS, PE, and POM, and they can meet various customization requirements from customers.
3. China Plastic Solutions:
China Plastic Solutions is a trusted manufacturer of plastic machined components in China. They provide a complete solution in plastic machining, including design, prototyping, and production. Their products range from simple plastic parts to complex assemblies, catering to diverse industries such as automotive, electronics, and medical.
4. Yitong Plastic Machining Co., Ltd.:
Yitong Plastic Machining Co., Ltd. is a leading supplier of plastic machining solutions in China. They offer CNC turning, milling, routing, and drilling services using state-of-the-art equipment. Their plastic machined components are known for their accuracy, durability, and cost-effectiveness.
5. Dajin Precision:
Dajin Precision is a professional plastic machining manufacturer with extensive experience. They specialize in producing high-precision plastic parts using advanced CNC technology. Their products are widely used in industries like aerospace, electronics, and telecommunications.
| Name | Products Offered |
|—————————–|————————————————————————|
| Plastic Machining Co., Ltd. | CNC machined plastic parts, plastic sheet fabrication, injection molding |
| Plastic Tech Industries | CNC milling, turning, drilling, threading |
| China Plastic Solutions | Design, prototyping, production, assemblies |
| Yitong Plastic Machining | CNC turning, milling, routing, drilling |
| Dajin Precision | High-precision plastic parts |
Background Research for plastic machining manufacturers Companies in China, use qcc.com archive.org importyeti.com
When it comes to finding plastic machining manufacturers in China, there are several websites that can provide background research and information about these companies. Three useful platforms for this purpose are qcc.com, archive.org, and importyeti.com.
qcc.com is a Chinese business information database that contains comprehensive company profiles, legal information, credit reports, and more. This platform can provide essential details about plastic machining manufacturers, such as their registration status, business scope, and financial performance. It allows users to search for specific companies, access historical data, and obtain an overview of their operations.
archive.org is a website that archives and preserves web content, including company websites. This platform can be utilized to track the historical development, changes, and updates made by plastic machining manufacturers over time. By accessing archived versions of their websites, users can gain an understanding of the company’s evolution, product portfolio, certifications, and capabilities.
importyeti.com is an import-export data platform that provides information about companies engaged in global trade. By searching for plastic machining manufacturers on importyeti.com, users can access data related to their import and export activities, including the countries they trade with, product categories, and volumes shipped. This data can give valuable insights into the manufacturers’ international presence, customer base, and production capacity.
By utilizing these three platforms, researchers can gather substantial information about plastic machining manufacturers in China within 300 words. This data can include company profiles, historical development, business scope, financial performance, import-export activities, and global trade relationships. This research can help users make informed decisions when selecting a suitable plastic machining manufacturer for their specific needs.
Leveraging Trade Shows and Expos for plastic machining Sourcing in China
Trade shows and expos provide excellent opportunities for plastic machining sourcing in China. These events allow businesses to network, explore new suppliers, and stay updated with the latest trends and technologies in the industry. Leveraging trade shows and expos can greatly benefit businesses seeking plastic machining services in China.
Attending trade shows and expos focused on plastic machining in China enables businesses to connect with numerous suppliers under one roof. These suppliers showcase their capabilities, products, and services, allowing businesses to evaluate them and make informed decisions. It eliminates the need for separate visits to multiple suppliers, saving time and resources.
Trade shows and expos also provide a platform to directly engage with suppliers. Businesses can discuss their specific requirements, negotiate prices, and assess the supplier’s expertise and quality standards. Face-to-face interactions foster trust and establish strong relationships, laying the foundation for successful collaborations.
Furthermore, these events offer in-depth insights into the latest trends and technologies in plastic machining. Exhibitors often showcase cutting-edge equipment, software, and materials used in the industry. This knowledge can help businesses stay competitive and meet the evolving demands of the market.
To make the most of trade shows and expos, businesses should prepare in advance. Researching participating suppliers, creating a checklist of requirements, and setting clear objectives will streamline the sourcing process. It is also essential to allocate sufficient time to visit the booths, attend seminars, and engage in meaningful conversations with potential suppliers.
Overall, trade shows and expos present a convenient and effective platform for sourcing plastic machining services in China. They allow businesses to connect with multiple suppliers, negotiate directly, gain industry insights, and foster strong relationships. Leveraging these events can help businesses find reliable suppliers, enhance their capabilities, and gain a competitive edge in the plastic machining industry.
The Role of Agents and Sourcing Companies in Facilitating plastic machining Purchases from China
Agents and sourcing companies play a crucial role in facilitating plastic machining purchases from China. These intermediaries act as a bridge between the buyers and suppliers, helping to streamline the procurement process and ensure smooth communication and transactions.
One of the primary functions of agents and sourcing companies is to identify reliable and high-quality plastic machining suppliers in China. They have extensive networks and knowledge of the market, enabling them to connect buyers with the most suitable suppliers based on their requirements. This saves buyers the time and effort of searching for suppliers on their own, especially if they are unfamiliar with the Chinese market.
Moreover, agents and sourcing companies assist in negotiating the best possible price and terms with the suppliers. They have the experience and expertise to navigate the complexities of international trade. They help ensure that buyers get the most competitive pricing for their plastic machining needs while maintaining the desired quality standards.
Another key role of agents and sourcing companies is to address any language and cultural barriers that may exist between the buyers and suppliers. They serve as translators and intermediaries, facilitating effective communication and understanding between the two parties. This avoids miscommunication or misunderstandings that could potentially jeopardize the purchasing process.
Furthermore, agents and sourcing companies often provide quality control and inspection services. They can visit the suppliers’ facilities to assess their manufacturing capabilities, quality control processes, and overall production standards. This ensures that the plastic machining products meet the required specifications and quality expectations before being shipped to the buyers.
Additionally, agents and sourcing companies handle logistics and shipping arrangements. They organize the necessary documentation, packaging, and transportation of the plastic machined products from China to the buyers’ location. This saves buyers the hassles and complexities of coordinating international shipping and customs procedures.
Overall, agents and sourcing companies play an indispensable role in facilitating plastic machining purchases from China. Their extensive networks, negotiation skills, language proficiency, quality control services, and logistics support contribute to a smooth and successful procurement process for buyers. By leveraging their expertise, buyers can confidently source plastic machining products from China while minimizing risks and maximizing value.
Price Cost Research for plastic machining manufacturers Companies in China, use temu.com and 1688.com
When it comes to plastic machining manufacturers in China, two popular online platforms for conducting price cost research are temu.com and 1688.com. Both platforms offer extensive listings of manufacturers specializing in plastic machining, catering to various industries and requirements.
Temu.com provides a user-friendly interface that allows buyers to search for plastic machining manufacturers based on specific criteria such as location, product type, and certification. The platform also features a message system for direct communication between buyers and suppliers, enabling price negotiation and gathering more detailed information. Temu.com provides the flexibility to compare multiple manufacturers to find the most suitable option.
1688.com, on the other hand, is a B2B platform owned by Alibaba, specifically targeting the Chinese market. It allows users to search for plastic machining manufacturers based on similar criteria like temu.com. However, compared to temu.com, 1688.com has a larger number of suppliers, providing buyers with a wider range of options to choose from.
To conduct price cost research on these platforms, buyers can enter specific keywords such as “plastic machining,” “CNC machining,” or “custom plastic parts” to generate a list of relevant manufacturers. By browsing through the listings, buyers can gather information on the manufacturers’ capabilities, certifications, lead times, and customer reviews.
In addition to these platforms, it is advisable to reach out to potential manufacturers directly to negotiate prices and discuss specific project requirements. This helps in obtaining more accurate cost estimates and establishing a beneficial working relationship.
In conclusion, temu.com and 1688.com are reliable platforms for conducting price cost research for plastic machining manufacturers in China. These platforms provide comprehensive listings of suppliers, allowing buyers to find suitable manufacturers based on their specific requirements. Utilizing these platforms, combined with direct communication with manufacturers, can help buyers streamline their sourcing process and achieve competitive pricing.
Shipping Cost for plastic machining import from China
The shipping cost for plastic machining imports from China can vary depending on various factors such as the weight and size of the shipment, the shipping method chosen, and the destination location. Generally, there are two main shipping methods for importing goods from China: air freight and sea freight.
Air freight is typically faster but more expensive compared to sea freight. The cost is calculated based on the weight of the shipment and the volume it occupies. It is important to note that air freight is more suitable for small and urgent shipments. The cost of air freight can range from $3 to $10 per kilogram, excluding additional charges such as handling fees, customs clearance, and insurance.
On the other hand, sea freight is a more cost-effective option for larger shipments. It is calculated based on the volume or cubic meters of the goods. The cost of sea freight can vary depending on factors such as the departure and destination ports, shipping route, and shipping company. On average, sea freight can range from $500 to $3000 for a 20-foot container and $1000 to $6000 for a 40-foot container, excluding additional charges mentioned above.
It is essential to work with a reliable freight forwarder or shipping agent who can provide accurate quotes and handle the necessary documentation, customs clearance, and transportation arrangements. They can also offer valuable insights regarding the most suitable shipping method based on your specific requirements.
Furthermore, it is recommended to consider insurance coverage to protect the goods during transit, especially for valuable or fragile items. Insurance costs can vary depending on the value and nature of the goods.
To minimize shipping costs, it is advisable to optimize the packaging and consolidate the shipments to reduce volume and weight. Negotiating rates with shipping companies and choosing the most cost-effective route can also help in reducing expenses.
In summary, the shipping cost for plastic machining imports from China varies based on factors such as shipment weight, size, shipping method (air freight or sea freight), destination location, and additional charges such as handling fees, customs clearance, and insurance. Working with a reliable shipping agent, optimizing packaging, and considering consolidation can contribute to lowering the overall shipping costs.
Compare China and Other plastic machining Markets: Products Quality and Price,Visible and Hidden Costs
China has emerged as a dominant player in the plastic machining market, but how does it compare to other markets in terms of product quality, price, and visible and hidden costs?
In terms of product quality, China has made significant strides in recent years. The country has invested heavily in research and development, which has helped improve the quality of its plastic machining products. Chinese manufacturers have also adopted advanced technology and equipment to ensure precise and consistent manufacturing processes. However, it is important to note that quality can vary across different suppliers in China, so due diligence is required when selecting a manufacturer.
When it comes to price, China has a competitive edge due to its lower labor and production costs. The country’s large pool of skilled workers and high production capacity allow for economies of scale, resulting in lower production costs. As a result, Chinese plastic machining products are generally more affordable compared to those from other markets. However, the price advantage is diminishing as labor costs in China continue to rise.
Visible costs, such as the cost of raw materials and manufacturing, are relatively transparent in China. Manufacturers often provide detailed cost breakdowns, enabling buyers to negotiate better deals. However, hidden costs can arise due to issues like intellectual property infringement and quality control. Intellectual property protection in China has been a concern for many companies, as unauthorized replication of products is a common issue. Quality control can also be challenging, especially when dealing with a large number of suppliers.
Compared to other plastic machining markets, China offers a wide variety of product options and has a vast supplier base. This allows buyers to have more choices and flexibility in terms of customization and order quantities. Additionally, China has established efficient logistics and distribution networks, which contribute to shorter lead times and faster deliveries.
In conclusion, China has significant advantages in terms of product quality, price, and supplier base in the plastic machining market. However, it is important to conduct thorough research and carefully evaluate potential suppliers to ensure consistent quality and minimize hidden costs.
Understanding Pricing and Payment Terms for plastic machining: A Comparative Guide to Get the Best Deal
Pricing and payment terms are critical factors to consider when seeking plastic machining services. Understanding these aspects can help businesses secure the best deal and establish a mutually beneficial relationship with a machining supplier. This comparative guide aims to provide insights into pricing structures and payment terms commonly used in the plastic machining industry.
Pricing for plastic machining services can vary depending on several factors such as the complexity of the parts, the type and quality of materials required, the quantity of parts needed, and the required machining processes. It is crucial to obtain detailed quotes from multiple suppliers to compare prices effectively. The quote should include a breakdown of costs, such as material costs, labor costs, and any additional services required.
When evaluating pricing, businesses should consider the supplier’s experience, expertise, and reputation, as well as the quality of their machined parts. Opting for the lowest price may result in compromised quality and potentially higher costs in the long run.
Payment terms are equally important when finalizing a deal with a machining supplier. Common payment options include upfront payments, milestone-based payments, and credit arrangements. Upfront payments are typically required for new customers or for initial tooling costs. Milestone-based payments involve dividing the project into stages, with payment due upon the completion of each stage. This option ensures that the supplier is incentivized to meet deadlines and quality requirements.
Credit arrangements are often available for established, reputable businesses. This option allows for payment within a specific timeframe, such as 30 days from the invoice date. However, businesses should note that credit arrangements may be subject to credit checks and interest charges.
Negotiating payment terms can help businesses secure more favorable arrangements. Important terms to consider include late payment penalties, order cancellations, and potential refunds or returns.
To get the best deal, it is advisable to build a strong relationship with the machining supplier. Consistent and reliable business dealings can lead to preferential pricing, payment terms, and better overall service.
In conclusion, understanding pricing structures and payment terms is vital for businesses seeking plastic machining services. By comparing quotes, considering quality factors, and negotiating favorable payment terms, businesses can secure the best deal and build a successful relationship with a machining supplier.
Chinese Regulations and Industry Standards Certifications for plastic machining,Import Regulations and Customs for plastic machining from China
China has implemented certain regulations and industry standards certifications for plastic machining, along with import regulations and customs procedures. These regulations and certifications are essential for ensuring the quality and safety of plastic machined products imported from China.
In terms of industry standards certifications, the most important one is the ISO 9001 certification. This certification ensures that the manufacturer has a quality management system in place, guaranteeing that their plastic machining processes meet the highest standards. Additionally, the ISO 14001 certification focuses on environmental management practices, ensuring that the manufacturer follows eco-friendly and sustainable manufacturing processes.
China also requires compliance with its own regulations, such as the “Regulation on the Administration of Registration of Production Enterprises Engaged in the Production of Plastic Products.” This regulation ensures that plastic machining companies in China are registered and authorized to produce plastic products, minimizing the risk of substandard or unsafe products being imported.
When it comes to import regulations and customs procedures, it is important to consider the following key aspects. Importers must accurately classify the plastic machined product according to the Harmonized System (HS) codes to determine the applicable customs duty rates and import restrictions. Importers may also need to obtain necessary import licenses, permits, and certificates for specific plastic machining products, depending on their nature and purpose.
Furthermore, importers should be aware of China’s labeling requirements, as products shipped to China should have clear and accurate labels in Chinese with important information such as product name, specifications, manufacturer’s information, and country of origin. Compliance with Chinese labeling regulations is necessary for smooth customs clearance.
In conclusion, Chinese regulations and industry standards certifications play a crucial role in ensuring the quality and safety of plastic machined products imported from China. Importers also need to navigate the country’s import regulations and customs procedures, including proper classification, obtaining necessary licenses, permits, and certificates, and complying with labeling requirements. Adhering to these regulations and certifications is essential for a seamless and successful importation process.
Sustainability and Environmental Considerations in plastic machining Manufacturing
Plastic machining is a manufacturing process that involves shaping plastic materials into desired shapes and sizes. While plastic machining offers numerous benefits, such as cost-effectiveness, flexibility, and ease of customization, it is essential to consider sustainability and environmental factors in this process.
One crucial aspect is the choice of plastic materials used in machining. Opting for sustainable plastics, such as biodegradable or recyclable ones, can significantly reduce the environmental impact. These materials are designed to decompose or can be recycled at the end of their lifecycle, minimizing waste and resource consumption.
Reducing energy consumption during plastic machining is another important consideration. Implementing energy-efficient technologies and practices, such as using high-speed machining equipment and optimizing cutting parameters, can decrease energy usage. Additionally, using renewable energy sources, like solar or wind power, for the manufacturing process can further reduce the carbon footprint associated with plastic machining.
Another environmental concern is the disposal of waste generated during plastic machining. Proper waste management techniques should be implemented, including segregating recyclable and non-recyclable waste. Recycling plastic waste reduces the need for virgin plastic production and conserves natural resources. Moreover, implementing initiatives to minimize waste generation, such as optimizing material usage and reusing scraps, can also contribute to sustainability efforts.
Water conservation is another consideration in plastic machining. Implementing water-saving technologies, like closed-loop cooling systems or water filtration systems, helps minimize water usage and reduces the strain on local water resources. Proper wastewater treatment procedures should also be in place to ensure that discharged water meets environmental regulations.
Lastly, promoting a culture of sustainability and environmental stewardship within the plastic machining industry is crucial. This can be achieved through employee education and training programs, encouraging innovative solutions, and fostering collaboration with suppliers and customers to support sustainable practices along the supply chain.
In summary, sustainability and environmental considerations in plastic machining manufacturing involve choosing sustainable materials, reducing energy consumption, managing waste effectively, conserving water, and promoting a culture of sustainability. By incorporating these practices, the plastic machining industry can minimize its environmental impact and contribute to a more sustainable future.
List The Evolution history of “plastic machining”
Plastic machining has undergone significant evolution since its inception. In the early 19th century, the first plastic, celluloid, was introduced. However, machining techniques were limited, and the process mainly involved hand-cutting and shaping.
The mid-20th century brought about important advancements with the development of new plastics, such as polyurethane and acrylics. Machining techniques, including milling and lathe turning, were still primarily manual processes, requiring skilled craftsmen to shape the plastics into desired products.
The 1970s witnessed the introduction of computer numerical control (CNC) machining, revolutionizing plastic machining. CNC machines relied on programmed computer instructions to precisely control the machinery, allowing for increased accuracy and efficiency. This development dramatically improved the manufacturing capabilities by automating machining tasks and reducing human errors.
Advancements in technology and materials in the 1980s and 1990s further propelled the evolution of plastic machining. Improved computer-aided design (CAD) software enabled engineers to create intricate designs and simulate machining processes before implementation. This reduced prototyping time and enhanced precision.
With the turn of the 21st century, the advent of 3D printing revolutionized plastic machining. 3D printers enabled the creation of complex plastic parts layer-by-layer, which was previously difficult to achieve using traditional machining methods. This innovation expanded the possibilities in plastic manufacturing, offering faster production and customization options.
In recent years, the focus of plastic machining has shifted toward sustainable and eco-friendly practices. The negative environmental impact of plastic waste prompted the rise of bioplastics, derived from renewable resources like corn starch and vegetable oils. Machining techniques have adapted to accommodate these new materials, emphasizing recyclability and reducing the impact on the environment.
Today, plastic machining encompasses a wide range of processes, including CNC milling, turning, drilling, and 3D printing. The industry continues to evolve with advancements in automation, robotics, and the exploration of innovative composite materials. As technology progresses and sustainability concerns persist, the future of plastic machining holds great potential for further growth and innovation.
The Evolution and Market Trends in plastic machining Industry
The plastic machining industry has evolved significantly over the years, adapting to market trends and technological advancements. Plastic machining involves the process of shaping, cutting, or drilling plastic materials to create custom components or finished products.
One major trend in the plastic machining industry is the increasing demand for precision and tight tolerances. As industries such as aerospace, automotive, and medical require more intricate and complex plastic parts, the need for high-precision machining capabilities has grown. Manufacturers have responded by investing in advanced CNC (Computer Numerical Control) machines that offer exceptional accuracy and repeatability.
Another market trend in the industry is the emphasis on sustainability and environmentally-friendly practices. As the global concern for reducing plastic waste and pollution escalates, plastic machining companies are introducing eco-friendly materials and processes. These include the use of biodegradable or recyclable plastics, optimizing the use of resources, and reducing waste through improved production techniques.
The application of automation and robotics has also made significant strides in the plastic machining industry. Automation offers benefits such as improved productivity, increased efficiency, and reduced labor costs. Robotic systems can perform tasks such as material handling, part loading and unloading, and even inspection, greatly enhancing overall production efficiency.
Additionally, there is a growing trend towards the integration of digital technologies in plastic machining. This includes the use of simulation software to optimize machining processes, 3D modeling and virtual prototyping for design validation, and the implementation of data analytics for real-time monitoring and quality control. These technologies enable manufacturers to streamline the production process, reduce lead times, and enhance product quality.
In terms of market growth, the plastic machining industry is expected to witness steady expansion in the coming years. The increasing demand for plastic components in various industries, ranging from electronics to healthcare, is a major driving factor. Moreover, the rising adoption of lightweight materials, including plastics, in automotive and aerospace applications, is further propelling the market growth.
In conclusion, the plastic machining industry has undergone notable transformations to meet evolving market trends. The emphasis on precision, sustainability, automation, and digitalization has shaped the industry’s trajectory. With continued advancements in technology and increasing demand for plastic components, the future of the plastic machining industry appears promising.
Custom Private Labeling and Branding Opportunities with Chinese plastic machining Manufacturers
Chinese plastic machining manufacturers offer custom private labeling and branding opportunities for businesses looking to establish their own unique identity in the market. These manufacturers have extensive experience in producing high-quality plastic products and are equipped with advanced machining technology.
The private labeling option allows businesses to imprint their own brand name, logo, and other identifying features on the plastic products. This helps create a distinct brand image, enhancing brand recognition and customer loyalty. By leveraging the expertise of Chinese manufacturers, businesses can ensure that their products are not only of superior quality but also reflect their brand’s essence.
Furthermore, Chinese plastic machining manufacturers understand the importance of branding in today’s competitive market. They work closely with businesses to develop customized product designs that align with their brand identity. This includes choosing the appropriate materials, colors, and finishes that accurately represent the brand and its values.
In addition to private labeling, Chinese manufacturers also offer branding opportunities through packaging. They can create custom packaging solutions that showcase the brand’s logo, colors, and messaging. This not only enhances the product’s aesthetic appeal but also strengthens brand recognition on store shelves or e-commerce platforms.
By working with Chinese plastic machining manufacturers, businesses can take advantage of cost-effective production processes without compromising on the quality of their products. These manufacturers have a deep understanding of global quality standards and have implemented strict quality control measures to ensure customer satisfaction.
In conclusion, partnering with Chinese plastic machining manufacturers provides businesses with amazing opportunities for custom private labeling and branding. By making use of the expertise and advanced technology of these manufacturers, businesses can create unique products that reflect their brand identity and stand out in the market.
Tips for Procurement and Considerations when Purchasing plastic machining
When it comes to procurement of plastic machining, there are a few essential tips and considerations that can help ensure you make the right purchasing decisions. These factors can impact the quality, cost, and efficiency of the machining process, so it is crucial to keep them in mind:
1. Material selection: Understand the specific type and grade of plastic required for your machining needs. Factors to consider include strength, heat resistance, impact resistance, and chemical resistance. Each plastic material has unique properties and may require different machining techniques.
2. Quality and expertise: Look for suppliers who have extensive experience and expertise in plastic machining. Verify their certifications and quality control processes to ensure that they can deliver consistent and high-quality machined plastic parts.
3. Machining capabilities: Evaluate the supplier’s machining capabilities, including the types of machinery and equipment they have, their capacity, and their ability to handle complex geometries. Make sure they can meet your specific machining requirements.
4. Cost considerations: Compare quotes from multiple suppliers to ensure competitive pricing. However, keep in mind that the cheapest option may not always be the best. Consider the supplier’s reputation, quality, lead times, and customer service when making a decision.
5. Turnaround time: Discuss the supplier’s lead times and delivery capabilities. Ensure they can meet your project timelines and provide accurate updates throughout the machining process.
6. Customization options: If you require custom machining or specific tolerances, ensure that the supplier is capable of meeting your customization needs.
7. Sustainability and environmental impact: Consider the environmental impact of the plastic materials and machining waste. Look for suppliers who prioritize sustainability and offer recycling or repurposing options for the waste generated during the machining process.
8. Supplier support: Assess the supplier’s customer service, technical support, and after-sales service. It is crucial to choose a supplier who is responsive and can assist you in case of any issues or concerns.
By considering these tips and factors, you can make informed decisions when purchasing plastic machining services and ensure that the process meets your requirements effectively and efficiently.
FAQs on Sourcing and Manufacturing plastic machining in China
Q: What is plastic machining?
A: Plastic machining refers to the process of shaping plastic materials into specific parts or components using various machining techniques, such as milling, turning, drilling, and cutting. This process allows for the production of precise and complex plastic parts with tight tolerances.
Q: Why should I source plastic machining in China?
A: China is known for its expertise and capabilities in plastic manufacturing and machining. The country has a large number of skilled workers and advanced machining equipment, which translates into cost-effective production and high-quality plastic parts. Additionally, China offers a wide range of plastic machining capabilities, accommodating different design requirements and material types.
Q: What are the benefits of sourcing plastic machining in China?
A: There are several advantages to sourcing plastic machining in China. Firstly, the cost of manufacturing in China is frequently lower compared to other countries, allowing for cost savings on production. Secondly, China has a vast supplier network, which means you have access to a wide range of materials, finishes, and manufacturing techniques. Additionally, Chinese manufacturers often have quick turnaround times and can handle both small and large production volumes efficiently.
Q: How can I find a reliable plastic machining manufacturer in China?
A: To find a reliable plastic machining manufacturer in China, it is recommended to conduct thorough research and due diligence. Start by searching for reputable manufacturers online and review their websites and customer reviews. Verify their certifications, production capabilities, and quality control processes. It is also beneficial to request samples or visit their facilities if possible to assess their capabilities firsthand.
Q: What factors should I consider when sourcing plastic machining in China?
A: When sourcing plastic machining in China, factors to consider include quality control measures, production capacity, lead times, pricing, communication capabilities, and the manufacturer’s experience with your specific industry or material requirements. It is crucial to establish clear communication channels and have a detailed understanding of the manufacturer’s capabilities and limitations to avoid any misunderstandings during the production process.
In conclusion, sourcing plastic machining in China offers several advantages, including cost-effectiveness, a wide range of capabilities, and quick turnaround times. However, it is crucial to prioritize thorough research, due diligence, and clear communication to find a reliable and suitable manufacturing partner in China.
Why contact sourcifychina.com get free quota from reliable plastic machining suppliers?
Sourcifychina.com offers free quotas from reliable plastic machining suppliers for various reasons:
1. Cost-effective solution: Sourcifychina.com has established partnerships with reliable plastic machining suppliers in China. By connecting buyers with these suppliers, they offer a cost-effective solution for sourcing plastic machining services. The free quota allows buyers to understand the pricing structure and assess the affordability of the suppliers.
2. Supplier verification: Sourcifychina.com goes through a rigorous selection process before partnering with suppliers. They ensure that the suppliers have a proven track record of delivering high-quality plastic machining services. By providing a free quota, buyers can evaluate the supplier’s capabilities and ensure they meet their requirements.
3. Access to multiple suppliers: Sourcifychina.com has a wide network of plastic machining suppliers. The free quota allows buyers to explore multiple options and compare quotes from different suppliers. This ensures that buyers can make an informed decision based on pricing, quality, production capacity, and other parameters.
4. Streamlined communication: Sourcifychina.com acts as a bridge between the buyer and the suppliers. By providing a free quota, they facilitate direct communication between both parties. This enables them to discuss project details, specifications, and any specific requirements. It also allows buyers to establish a relationship with the suppliers, fostering better understanding and collaboration.
5. Transparency and trust-building: By offering a free quota, Sourcifychina.com demonstrates transparency in their approach. Buyers can see the pricing and other relevant details upfront, which builds trust between the parties involved. The free quota also indicates that Sourcifychina.com values customer satisfaction and aims to provide a reliable sourcing platform.
In summary, Sourcifychina.com offers a free quota from reliable plastic machining suppliers to provide a cost-effective sourcing solution, verify supplier capabilities, offer access to multiple suppliers, facilitate communication, and build trust with buyers.