Introduce about prototype to production guide,Qulity,Cost,Supplier,Certification,Market,Tips,FAQ
Prototype to production guide helps companies navigate the process of transitioning a product from concept to mass production. It outlines steps to ensure quality, minimize costs, select reliable suppliers, obtain necessary certifications, and address market demands.
Quality is crucial in every step of the production process, from prototyping to final manufacturing. It is essential to test and iterate on prototypes to ensure they meet the desired specifications and performance standards. Quality control measures should be implemented throughout production to guarantee consistent, high-quality products.
Cost is a significant consideration when moving from prototype to production. It is important to optimize the production process to reduce expenses without compromising on quality. Selecting cost-effective materials and suppliers, streamlining manufacturing processes, and negotiating favorable contracts can help minimize costs.
Choosing reliable suppliers is critical to ensuring a smooth transition from prototype to production. Suppliers should have the capacity, expertise, and track record to meet production demands and deliver components on time.
Obtaining certifications is vital to demonstrate compliance with industry standards and regulations. Certifications can enhance product credibility, quality assurance, and marketability.
Understanding market demands and trends is crucial for successful production. Researching target markets, analyzing competitors, and adapting product features accordingly can help ensure market acceptance and competitiveness.
Tips for a successful transition from prototype to production include proper planning, clear communication with all stakeholders, thorough testing and validation, and continuous improvement throughout the production process.
FAQs about prototype to production may include queries about choosing the right manufacturing method, scaling production, managing supply chain logistics, and ensuring product sustainability.
In conclusion, a well-executed prototype to production process is essential for launching a successful product. By focusing on quality, cost optimization, supplier selection, certification, market research, and following helpful tips, companies can navigate this transition effectively and achieve commercial success.
Types of prototype to production
There are several approaches to take a prototype to production, depending on the complexity of the product and the resources available.
One common method is rapid prototyping, which involves creating a simple prototype to test the concept and gather feedback from users. Once the prototype is validated, it can be refined and optimized for production. This approach is often used for software and digital products, where changes can be easily implemented.
Another approach is iterative prototyping, where multiple versions of the prototype are created and tested to refine the design and functionality. This method allows for incremental improvements and ensures that the final product meets the requirements of the users.
For more complex products, such as hardware or physical goods, a proof-of-concept prototype may be created to demonstrate the feasibility of the product before moving on to production. This type of prototype is often used in industries such as automotive or aerospace, where extensive testing is required before mass production.
Once a prototype is ready for production, it can be manufactured using various methods such as 3D printing, injection molding, or assembly line production. The chosen method will depend on factors such as cost, volume, and timeframe.
Overall, the key to successfully taking a prototype to production is careful planning, testing, and iteration to ensure that the final product meets the needs of the users and the market. By using the right approach and resources, a prototype can be transformed into a successful and profitable product.
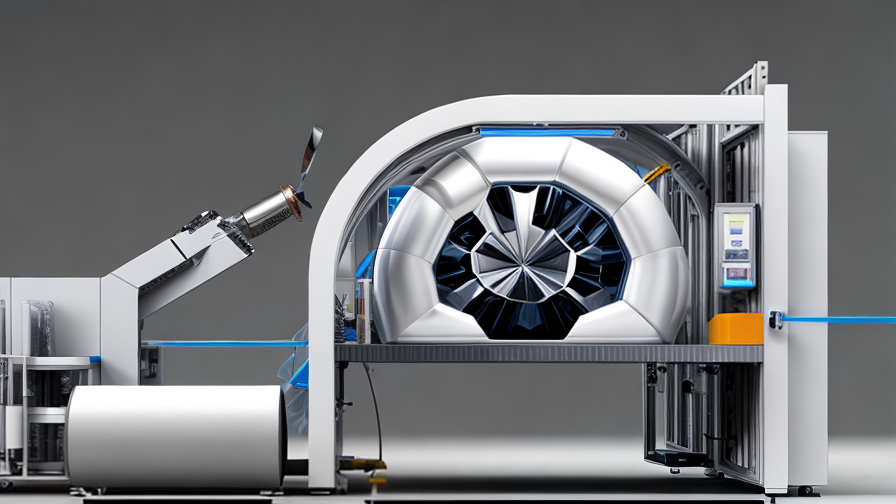
Pros and Cons of Using prototype to production
Pros of using prototype to production:
1. Cost efficiency: Prototyping allows for the identification and elimination of design flaws early in the process, reducing the likelihood of costly errors during the production phase.
2. Faster time-to-market: Prototyping helps to streamline the product development process, enabling companies to bring their products to market more quickly and efficiently.
3. Improved product quality: By testing and refining a prototype before moving into full-scale production, companies can ensure that the final product meets the highest quality standards.
4. Enhanced user feedback: Prototypes allow companies to gather valuable feedback from users early in the development process, enabling them to make necessary adjustments and improvements before final production.
5. Flexibility and creativity: Prototyping encourages a more iterative and creative approach to product development, allowing companies to explore different design options and make changes as needed.
Cons of using prototype to production:
1. Higher upfront costs: Developing a prototype can require significant time and resources, leading to increased upfront costs for companies.
2. Potential for production delays: If issues are not identified and addressed during the prototyping phase, they may lead to delays in the production process.
3. Limited scalability: Prototypes are often designed for testing and validation purposes, and may not always be easily scalable for mass production.
4. Intellectual property concerns: Sharing prototypes with external partners or customers may expose companies to risks related to intellectual property infringement or theft.
5. Uncertainty and risk: Prototyping involves a degree of uncertainty and risk, as companies may need to make adjustments and revisions to their designs based on feedback and testing results.
In conclusion, while there are clear benefits to using prototype to production, it is important for companies to carefully consider the potential drawbacks and challenges associated with this approach in order to ensure successful product development and launch.
prototype to production Reference Specifications (varies for different product)
When transitioning from prototype to production, it is essential to have reference specifications that outline the required criteria and standards for the final product. These specifications may vary depending on the nature of the product being developed. The purpose of these reference specifications is to serve as a guideline for the manufacturing process and to ensure that the final product meets the desired quality, performance, and safety standards.
Reference specifications typically include details about the materials to be used, manufacturing processes, dimensions, tolerances, and other critical parameters. For example, in the case of an electronic device, the specifications may specify the type and quality of components, the circuit design, the power requirements, and the expected performance metrics such as processing speed or battery life.
These specifications provide a clear framework for the production team, enabling them to streamline the manufacturing process and avoid any potential issues. They ensure that all stakeholders involved in the production, including engineers, designers, and manufacturers, are aligned in terms of the expected outcome.
Moreover, reference specifications also play a crucial role in ensuring regulatory compliance and product safety. Depending on the industry and product, there may be specific standards and certifications that the final product must meet. These specifications outline the mandatory requirements and serve as a checklist to ensure compliance during production.
Throughout the transition from prototype to production, the reference specifications act as a point of reference for quality control. They allow for testing and inspection procedures to be established, ensuring that each unit meets the predefined standards and functional requirements.
In conclusion, reference specifications are an essential tool during the transition from prototype to production. They provide the necessary guidance and criteria required to manufacture a quality product that meets industry standards, regulatory requirements, and customer expectations. By using these specifications, the production team can effectively and efficiently bring a prototype to full-scale production.
Applications of prototype to production
Prototyping is a crucial step in the product development process as it allows designers and manufacturers to test and refine their ideas before moving into full-scale production. Once a prototype has been successfully developed and tested, it can be used as a blueprint for manufacturing the final product.
One way that prototypes are used in production is to test the functionality and durability of a design. By creating a prototype, designers can identify any flaws or issues with the design early on and make necessary adjustments. This helps to prevent costly mistakes and rework later in the production process.
Prototypes can also be used to showcase a new product to potential investors or customers. By having a physical prototype to demonstrate, designers can gather feedback and gauge interest in the product before committing to mass production. This can help to ensure that there is a demand for the product and increase the likelihood of its success in the market.
Additionally, prototypes can be used as a guide for manufacturing the final product. By having a physical model to reference, manufacturers can accurately replicate the design and specifications of the prototype, ensuring consistency and quality in the production process. This can help to streamline production and reduce the likelihood of errors or variations in the final product.
Overall, the use of prototypes in the production process is essential for testing, refining, and ultimately bringing a new product to market successfully. By utilizing prototypes, designers and manufacturers can ensure that their final product meets the desired specifications and requirements, leading to a higher likelihood of success in the marketplace.
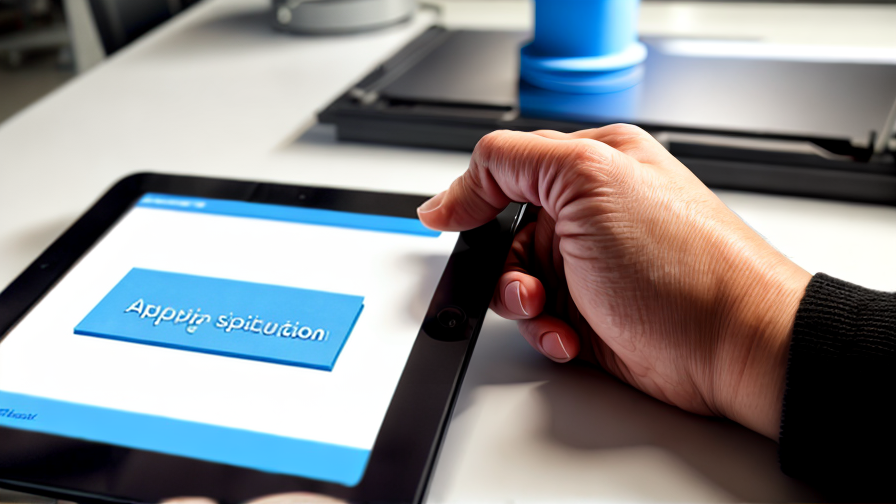
The Work Process and how to use prototype to production
The work process of moving from prototype to production involves several key steps to ensure a successful transition. The first step is to thoroughly test and refine the prototype to ensure that it meets the desired specifications and functionality. This may involve multiple iterations of testing and feedback from users.
Once the prototype has been approved, the next step is to prepare for production. This involves sourcing materials, setting up manufacturing processes, and creating detailed production plans. It is essential to consider factors such as cost, quality control, and scalability during this stage.
When transitioning from prototype to production, it is important to make any necessary adjustments to ensure that the product can be manufactured efficiently and cost-effectively. This may involve redesigning certain components or making modifications to the manufacturing process.
Using prototypes in the production process can help to streamline and improve the overall product development process. Prototypes allow for early testing and feedback, which can help to identify and address any issues before moving to full-scale production. Prototyping can also help to reduce costs and minimize risks by allowing for changes to be made early in the development process.
Overall, properly managing the transition from prototype to production is essential for ensuring the success of a product. By following a structured work process and utilizing prototypes effectively, businesses can improve the quality, efficiency, and ultimately, the success of their products.
Quality Testing Methods for prototype to production and how to control the quality
Quality testing methods for prototyping to production includes various approaches such as unit testing, integration testing, system testing, and acceptance testing.
Unit testing involves testing individual components or modules of the system to ensure that they function correctly. Integration testing is then used to test how these components work together in the system. System testing focuses on testing the system as a whole to ensure it meets all requirements and performs as expected. Acceptance testing involves testing the system with real users to ensure it meets their needs and expectations.
To control the quality of the product throughout the development process, it is important to establish quality control measures at each stage of the production cycle. One approach is to implement a quality management system that outlines quality standards, processes, and procedures that need to be followed. Regular reviews and audits can also be conducted to ensure that these standards are being met.
In addition, continuous monitoring and feedback from stakeholders can help identify any issues early on in the development process. This feedback should be used to make necessary adjustments and improvements to ensure that the final product meets all quality requirements.
Overall, by using a combination of testing methods, establishing quality control measures, and implementing feedback mechanisms, the quality of the product from prototype to production can be effectively controlled.
prototype to production Sample Policy and Post-Purchase Considerations for prototype to production from China
Sample Policy and Post-Purchase Considerations for Prototype to Production from China
As businesses increasingly turn to China for prototype manufacturing and production, it is essential to have a solid policy and post-purchase considerations in place to ensure a smooth transition from prototype to mass production. Here are some guidelines to consider for a successful prototype to production process:
1. Communication and Documentation: Establish open lines of communication with your Chinese manufacturing partner. Clearly communicate your expectations, technical specifications, and quality requirements. Maintain detailed documentation of the entire process, including design iterations, tests performed, and any changes made.
2. Quality Control: Implement a comprehensive quality control process. Conduct in-house inspections and third-party quality checks at every stage, from raw material procurement to final production. Set clear quality standards and request regular sample submissions from the manufacturer for evaluation.
3. Intellectual Property Protection: Protect your intellectual property rights. Ensure proper legal documentation is in place, including non-disclosure agreements (NDAs) and intellectual property (IP) protection agreements. Monitor and enforce your IP rights throughout prototype development and production.
4. Manufacturing and Supply Chain Management: Develop a reliable and efficient manufacturing and supply chain management plan. Understand the lead times, raw material availability, production capabilities, and shipping logistics of your Chinese manufacturer. Maintain regular communication to avoid delays and ensure timely delivery.
5. Post-Purchase Considerations: After production, perform thorough product inspections and quality checks to ensure compliance with agreed-upon specifications. Conduct on-site visits to monitor production processes and verify that all quality standards are being met. Address any issues promptly to maintain a good relationship with your Chinese manufacturer.
6. Continuous Improvement: Continuously evaluate and improve your prototype to production process. Collect feedback from customers, monitor performance metrics, and conduct regular supplier evaluations. Implement corrective actions to address any issues or inefficiencies encountered during the production process.
In conclusion, a well-defined policy and post-purchase considerations are crucial for a successful transition from prototype to production in China. By emphasizing communication, quality control, IP protection, supply chain management, and continuous improvement, businesses can minimize risks and maximize the benefits of manufacturing in China.
Sourcing prototype to production from China: Opportunities, Risks, and Key Players
Sourcing prototypes to production from China presents several opportunities and risks. China’s manufacturing capabilities, cost-efficiency, and flexible production processes make it an attractive choice for businesses looking to bring their products to market. The country offers a vast network of suppliers and manufacturers specializing in various industries. This enables businesses to find the right partner to develop their prototypes and scale up to production.
One of the main opportunities of sourcing from China is cost-effectiveness. Chinese manufacturers generally offer competitive pricing due to low labor and operational costs. This allows businesses to save on expenses during the prototyping and production stages, making their products more affordable in the market.
China’s vast manufacturing ecosystem also provides a wide range of options for businesses. Whether it’s electronics, textiles, plastics, or machinery, there are specialized manufacturers ready to cater to specific industry needs. This diversity allows for greater customization and product development possibilities.
However, sourcing from China also comes with its risks. Quality control can be a challenge, especially when working with new suppliers. It is essential to thoroughly vet potential partners and establish robust quality control processes to ensure the final product meets the required standards. Intellectual property protection can also be a concern, as China has been notorious for intellectual property infringements in the past. Taking necessary precautions and establishing legal safeguards is crucial to protect proprietary information.
Several key players assist businesses in navigating the process of sourcing prototypes to production from China. These include sourcing agents, trade consultants, and supply chain management companies. Sourcing agents act as intermediaries between businesses and manufacturers, helping to find reliable partners and reducing risks. Trade consultants offer guidance on navigating cultural differences, legal requirements, and market dynamics. Supply chain management companies provide end-to-end solutions, from prototype development to shipping and logistics.
In summary, sourcing prototypes to production from China offers opportunities for cost savings, diverse manufacturing options, and scalability. However, it is essential to manage risks related to quality control and intellectual property. With the support of key players in the industry, businesses can successfully navigate the process and leverage China’s manufacturing capabilities for their product development and production needs.
How to find and select reliable prototype to production manufacturers in China,use google search manufacturers and suppliers
Finding and selecting reliable prototype to production manufacturers in China can be a daunting task, but with careful research and evaluation, it is possible to find the right manufacturing partner. One of the most effective ways to start the search is by using Google to search for manufacturers and suppliers. Here is a step-by-step guide on how to do so:
1. Begin by conducting a general search using relevant keywords such as “prototype manufacturers in China” or “production manufacturers in China.”
2. Review the search results and visit the websites of different manufacturers to gather information about their services, expertise, and capabilities. Look for manufacturers that specialize in your industry or product type.
3. Go through their website thoroughly, paying attention to their experience, client testimonials, certifications, and any additional services they offer.
4. Look for manufacturers who have experience in both prototype development and mass production to ensure a smooth transition between these stages.
5. Narrow down your list based on your specific requirements, such as production volume, quality standards, pricing, and lead times.
6. Contact the shortlisted manufacturers to inquire about their capabilities, request samples, and ask any questions you may have. Their responsiveness and willingness to provide information will indicate their professionalism.
7. Ask for references from previous clients or inquire if they have worked on similar projects in the past. This will give you insights into the manufacturer’s track record and reliability.
8. Consider conducting a site visit or arranging a video call to get a better understanding of their facility, equipment, and manufacturing processes. This will help assess their quality control measures and ensure they have the necessary capabilities to meet your requirements.
9. Request quotes from the selected manufacturers and compare them based on pricing, lead time, quality control processes, and additional services they offer.
10. Finally, make a decision based on a combination of factors such as expertise, capabilities, reputation, communication skills, and pricing. It is advisable to start with a small order initially to evaluate their performance before committing to larger production volumes.
Remember, thorough research, due diligence, and clear communication are crucial while selecting a reliable prototype to production manufacturer in China.
How to check prototype to production manufacturers website reliable,use google chrome SEOquake check if ranking in top 10M
To check the reliability of a prototype to production manufacturer’s website, you can follow these steps:
1. Use Google Chrome: Open the manufacturer’s website using the Google Chrome browser. Chrome provides various helpful tools and extensions that can assist in evaluating the website’s reliability.
2. Install SEOquake: Install the SEOquake extension in your Chrome browser. SEOquake is a powerful tool that provides valuable SEO metrics and insights about a website.
3. Check Ranking in Top 10M: Once SEOquake is installed, go to the manufacturer’s website and activate the extension by clicking on the SEOquake icon in your browser toolbar. It will generate a toolbar displaying information about the website. Look for the Alexa rank, which indicates the website’s popularity based on its traffic. If the website ranks within the top 10 million, it usually indicates a fairly reliable and established presence.
4. Assess Key Metrics: Along with the Alexa rank, SEOquake also provides other useful metrics like the number of indexed pages, domain age, and social media engagement. These metrics can give you a good idea of the website’s credibility and online presence.
5. User Experience: Navigate through the website to assess its overall user experience. Ensure that the website contains legitimate contact details, such as a physical address, phone number, and email address. A reliable manufacturer’s website should also have clear information about their services, products, and any certifications or credentials they hold.
6. Additional Research: Conduct a quick online search about the manufacturer to gather additional information. Check for customer reviews or testimonials, as well as any news or industry-related articles about their reputation and reliability.
By following these steps, you can effectively evaluate the reliability of a prototype to production manufacturer’s website. Remember to use your judgment and consider multiple sources of information to make an informed decision.
Top 10 prototype to production manufacturers in China with each 160 words introduce products,then use markdown create table compare
1. **Flex Ltd:** Flex Ltd provides prototype to production services in a wide range of industries including medical devices, automotive, and consumer electronics. They offer services such as PCB assembly, product testing, and packaging.
2. **Jabil Inc:** Jabil Inc has a strong track record in turning prototypes into high-volume production runs for various industries. They specialize in precision machining, plastic injection molding, and rapid prototyping.
3. **Plexus Corp:** Plexus Corp offers end-to-end solutions from prototyping to manufacturing for sectors like aerospace, defense, and healthcare. They have expertise in complex system integration and supply chain management.
4. **East West Manufacturing:** East West Manufacturing focuses on producing prototypes and large-scale production for sectors like industrial equipment, telecommunications, and automotive. They have in-house design capabilities and quality control processes.
5. **Sanmina:** Sanmina provides prototype to production services for industries such as semiconductors, medical devices, and renewable energy. They offer custom manufacturing solutions and value-added services like supply chain management.
### Comparison Table:
| Manufacturer | Industries Served | Specialties |
|————————|——————————-|————————————————–|
| Flex Ltd | Medical devices, automotive | PCB assembly, testing, packaging |
| Jabil Inc | Various | Machining, molding, prototyping |
| Plexus Corp | Aerospace, defense, healthcare | System integration, supply chain management |
| East West Manufacturing | Industrial, automotive | In-house design, quality control |
| Sanmina | Semiconductors, medical | Custom manufacturing, supply chain management |
This comparison table provides a brief overview of the top 5 prototype to production manufacturers in China and their key strengths. Each manufacturer offers a unique set of services and specialties catered to different industries. Customers can evaluate these companies based on their specific requirements for taking their prototypes to production.
Background Research for prototype to production manufacturers Companies in China, use qcc.com archive.org importyeti.com
When searching for prototype to production manufacturers in China, qcc.com is a valuable resource. This website provides information on companies in China, including their production capacity, quality control measures, and certification status. By using qcc.com, it is possible to identify potential manufacturers that can help bring a product from the prototype stage to full-scale production.
Another useful tool for researching manufacturers in China is archive.org. This website allows users to access archived versions of webpages, which can be helpful in evaluating a manufacturer’s track record and reputation. By reviewing past versions of a manufacturer’s website, it is possible to gain insights into their history, capabilities, and customer feedback.
Importyeti.com is another valuable resource for finding prototype to production manufacturers in China. This website provides import and export data, which can be used to identify manufacturers that have experience working with international clients. By analyzing the import data on importyeti.com, it is possible to identify manufacturers that have a proven track record of delivering quality products to overseas customers.
By using qcc.com, archive.org, and importyeti.com, it is possible to conduct comprehensive research on prototype to production manufacturers in China. These tools provide valuable information that can help identify reliable and experienced manufacturers that can bring a product from the prototype stage to full-scale production.
Leveraging Trade Shows and Expos for prototype to production Sourcing in China
Trade shows and expos present excellent opportunities for sourcing prototypes to production in China. These events provide a platform for businesses to find reliable suppliers, establish connections, and gather information on new technologies and trends in the market. Leveraging trade shows and expos in China can greatly benefit companies seeking to take their product from prototype to production.
One advantage of attending these events is the ability to meet face-to-face with potential suppliers. The personal interaction allows for a better understanding of capabilities, product quality, and manufacturing processes. It also provides an opportunity to negotiate pricing and contract terms, ensuring a mutually beneficial relationship.
Trade shows and expos in China showcase a wide range of industries and products, allowing companies to explore various market segments and find the best fit for their prototype production needs. These events attract both established manufacturers and emerging businesses, offering a diverse pool of suppliers to choose from.
Furthermore, trade shows and expos facilitate networking and knowledge sharing among industry professionals. Engaging with experts in the field can provide valuable insights into production techniques, quality control measures, and cost-saving strategies. It allows businesses to stay up-to-date with the latest advancements in technology, materials, and manufacturing processes.
In addition to supplier contacts and industry knowledge, attending trade shows and expos often results in obtaining samples and product demonstrations. Evaluating prototypes firsthand helps ensure product specifications are met and any issues are addressed before moving to mass production.
To make the most of trade shows and expos in China, businesses should come prepared with clear objectives and a well-defined sourcing strategy. Researching the event, scheduling appointments with potential suppliers in advance, and bringing product specifications and requirements will enhance productivity during these events.
In conclusion, trade shows and expos serve as valuable platforms for prototype to production sourcing in China. They provide opportunities to meet suppliers, explore different industries, network with professionals, and obtain samples. By leveraging these events effectively, businesses can secure reliable partners and successfully advance their products from prototype to production.
The Role of Agents and Sourcing Companies in Facilitating prototype to production Purchases from China
Agents and sourcing companies play a crucial role in facilitating prototype to production purchases from China. These intermediaries serve as a bridge between buyers and manufacturers, ensuring a smooth and efficient process.
Firstly, agents and sourcing companies have extensive knowledge and experience in the Chinese manufacturing industry. They are well-versed in the local business practices, cultural nuances, and legal requirements. This expertise enables them to navigate the complexities of the Chinese market, ensuring that the buyer’s requirements are met effectively.
These intermediaries act as the buyer’s representative in China, saving them the hassle of traveling to China to find suitable manufacturers, negotiate contracts, and oversee production. They have a network of trusted suppliers and manufacturers in various industries, allowing them to source the right manufacturer based on the buyer’s specifications. This strategic supplier matching helps to reduce the risk of scams, poor quality products, or delays in production.
Agents and sourcing companies also streamline the communication process between buyers and manufacturers. They act as interpreters, ensuring accurate translation of technical requirements, expectations, and quality standards. This minimizes miscommunication and ensures that the buyer’s needs are clearly understood by the manufacturer.
Furthermore, agents and sourcing companies help buyers in conducting due diligence on potential suppliers. They verify the manufacturer’s credibility, reputation, and production capabilities. This includes performing factory audits, checking certifications, and inspecting the production facilities for compliance with quality and safety standards.
During production, these intermediaries play a vital role in quality control and management. They conduct regular inspections and monitor the production process to ensure that the buyer’s specifications are met. If any issues arise, they work closely with the manufacturer to rectify them promptly, minimizing disruptions and delays.
In summary, agents and sourcing companies facilitate prototype to production purchases from China by leveraging their expertise, network, and knowledge of the Chinese manufacturing industry. They assist buyers in finding suitable manufacturers, navigating the complexities of the market, ensuring effective communication, conducting due diligence, and managing the production process. By functioning as a reliable intermediary, they enhance the efficiency and success of purchasing from China.
Price Cost Research for prototype to production manufacturers Companies in China, use temu.com and 1688.com
When it comes to finding prototype to production manufacturers in China, two of the most popular platforms are Temu.com and 1688.com. These websites provide a wide range of options for sourcing manufacturers for various products.
On Temu.com, users can search for manufacturers based on their specific requirements and receive quotes from multiple suppliers. The platform also offers a secure payment system and quality control services to ensure the reliability of the manufacturers.
Similarly, 1688.com is a comprehensive online marketplace that connects buyers with suppliers in China. Users can browse through a vast array of products and manufacturers, compare prices, and negotiate deals directly with the sellers. The platform also provides a rating system and buyer protection services for added peace of mind.
When conducting price cost research for prototype to production manufacturers on these platforms, it is important to consider factors such as the quantity of products needed, the complexity of the manufacturing process, and the quality of the products. It is also advisable to request samples and compare prices from multiple suppliers before making a decision.
Overall, Temu.com and 1688.com are valuable resources for finding reliable and cost-effective manufacturers in China for prototype to production projects. By using these platforms effectively, businesses can streamline the sourcing process and secure competitive prices for their products.
Shipping Cost for prototype to production import from China
When importing a prototype from China to production, shipping costs can vary depending on several factors such as the size and weight of the items, the shipping method, and the final destination. Generally, air freight is the fastest but most expensive option, while sea freight is slower but more cost-effective for bulk shipments.
For a typical prototype to production import, air freight costs can range from $3 to $8 per kilogram, with additional fees for fuel surcharges, customs clearance, and handling. Sea freight costs are usually calculated based on the volume of the shipment and can range from $300 to $1500 per cubic meter.
To keep shipping costs under $300, consider consolidating shipments with other orders to take advantage of bulk pricing, or negotiate with your supplier for lower shipping rates. You can also opt for a slower shipping method, such as sea freight, if time is not a critical factor.
It is important to work closely with your freight forwarder or shipping agent to ensure that all necessary documentation is prepared correctly, and that the shipment is compliant with customs regulations. By planning ahead and exploring different shipping options, you can minimize costs and ensure a smooth import process from prototype to production.
Compare China and Other prototype to production Markets: Products Quality and Price,Visible and Hidden Costs
China is often seen as a major player in the prototype to production market, but it is important to compare it with other markets in terms of product quality, price, and visible and hidden costs.
In terms of product quality, China has made significant progress over the years. While there may still be concerns about counterfeit products, many manufacturers in China have improved their quality control processes to meet international standards. Other prototype to production markets, such as the United States, Europe, and Japan, have a reputation for high-quality products. However, their higher labor and production costs can often lead to higher product prices.
Speaking of prices, China undoubtedly offers competitive prices for prototypes and production. The country’s large manufacturing base and economies of scale allow for lower labor costs and more affordable products. This is a major advantage over other markets, especially for price-sensitive industries and startups. On the other hand, countries like the United States or Germany might offer higher prices due to higher labor costs and more stringent regulations.
When considering visible and hidden costs, China and other markets have their own set of factors to consider. Visible costs in China include labor, materials, and transportation, which are often lower compared to other markets due to their vast supply chain infrastructure. However, hidden costs such as intellectual property theft and quality control issues can sometimes arise in China, leading to increased overall costs. In other markets, visible costs may be higher, but hidden costs are typically lower, as there tend to be more stringent regulations and intellectual property protection measures in place.
In summary, China offers competitive product quality and prices in the prototype to production market due to its large manufacturing base and lower labor costs. However, concerns about counterfeit products and hidden costs need to be considered. Other markets like the United States, Europe, and Japan are known for their high-quality products but have higher visible costs due to stricter regulations. Ultimately, the choice of a prototype to production market depends on the specific needs and priorities of the business.
Understanding Pricing and Payment Terms for prototype to production: A Comparative Guide to Get the Best Deal
When moving from prototype to production for a product, it is important to understand the pricing and payment terms to ensure the best deal. Prices for production units are often lower than prototype units due to economies of scale. It is essential to negotiate pricing based on the expected volume of units to be produced.
Payment terms for production units can vary, with options such as upfront payment, staggered payments based on production milestones, or payment upon delivery. It is crucial to negotiate payment terms that align with the financial capabilities of your business. For example, a start-up may prefer staggered payments to ease cash flow, while a more established company may be able to handle upfront payment.
When comparing quotes from different manufacturers, it is important to consider the total cost, including any additional fees or hidden charges. Some manufacturers may offer lower unit prices but have higher shipping costs or tooling fees. It is essential to factor in all costs to make an informed decision.
Additionally, it is crucial to establish a clear agreement on quality control standards and warranty terms. Ensure that the manufacturer agrees to meet your quality expectations and provides a warranty for the produced units.
In conclusion, understanding pricing and payment terms is essential when transitioning from prototype to production. By negotiating favorable terms, considering all costs, and ensuring quality standards, you can secure the best deal for your business.
Chinese Regulations and Industry Standards Certifications for prototype to production,Import Regulations and Customs for prototype to production from China
In China, the regulations and industry standards certifications for prototype to production vary depending on the industry and type of product being manufactured. Some common certifications include ISO 9001 for quality management systems, CE certification for products being exported to the European Union, and CCC certification for products being sold in China.
Import regulations and customs processes for prototype to production from China are also important to consider. Importers must be aware of tariffs, duties, and taxes that may apply to their products. They must also ensure compliance with safety and quality standards in their home country.
To navigate these regulations and certifications, it is recommended to work with a trusted sourcing agent or partner in China who has expertise in the specific industry and product category. They can help guide companies through the certification process and ensure compliance with all necessary regulations.
In conclusion, understanding and complying with Chinese regulations and industry standards certifications are essential for successfully transitioning from prototype to production in China. Working with knowledgeable partners and staying up to date on import regulations and customs processes can help companies navigate the complexities of manufacturing and importing products from China.
Sustainability and Environmental Considerations in prototype to production Manufacturing
Sustainability and environmental considerations play a crucial role in prototype to production manufacturing processes. As the world becomes increasingly aware of the negative impacts of industrial activities on the environment, it has become imperative for manufacturers to adopt sustainable practices throughout the entire production lifecycle.
One of the key aspects of sustainable manufacturing is resource efficiency. This involves minimizing the consumption of raw materials, energy, and water during production. By optimizing the efficiency of manufacturing processes, manufacturers can reduce waste and carbon emissions, leading to a smaller ecological footprint. This can be achieved through implementing lean manufacturing principles and utilizing advanced technologies that promote energy efficiency.
Another important consideration is the choice of materials. Sustainable manufacturers prioritize the use of eco-friendly and recyclable materials in their production processes. This reduces the consumption of non-renewable resources and minimizes the generation of waste at the end of a product’s life cycle. Additionally, utilizing materials with low environmental impact, such as biodegradable or renewable alternatives, can further contribute to sustainable manufacturing practices.
Furthermore, manufacturers must incorporate circular economy principles into their production processes. This involves designing products that are easily recyclable or compostable, and implementing recycling programs to ensure the appropriate handling of waste materials. By closing the loop and reusing materials, manufacturers can reduce the demand for virgin resources and minimize the overall environmental impact of their products.
The implementation of sustainable manufacturing practices also requires collaboration with suppliers and stakeholders throughout the supply chain. This includes selecting suppliers that adhere to sustainable practices and promoting eco-friendly transportation methods to reduce the carbon footprint associated with logistics.
In conclusion, sustainability and environmental considerations are essential in prototype to production manufacturing. By optimizing resource efficiency, using eco-friendly materials, embracing circular economy principles, and collaborating with stakeholders, manufacturers can minimize their environmental impact and contribute to a more sustainable future.
List The Evolution history of “prototype to production”
The evolution of going from prototype to production has seen significant advancements over the years. In the past, prototypes were primarily made by hand using basic tools and materials, and the transition to production was often lengthy and costly. However, with the advent of computer-aided design (CAD) and rapid prototyping technologies, the process has become much more streamlined and efficient.
Today, designers and engineers can create virtual prototypes using CAD software, allowing them to test and refine their designs before any physical prototypes are made. This not only saves time and money but also allows for more iterations and improvements to be made before moving to production.
Once a virtual prototype is finalized, rapid prototyping technologies such as 3D printing can quickly and cost-effectively produce physical prototypes for further testing and validation. These prototypes can be made from a variety of materials, allowing for more accurate representation of the final product.
Finally, when the prototype is approved, it can move into production much more seamlessly thanks to automated manufacturing technologies such as CNC machining and robotic assembly. This allows for high precision and consistency in the production process, resulting in higher quality products at a faster pace.
Overall, the evolution of going from prototype to production has seen a shift towards digital technologies and automation, making the process more efficient, cost-effective, and reliable than ever before.
The Evolution and Market Trends in prototype to production Industry
The prototype to production industry has undergone significant evolution and witnessed various market trends over the years. This industry involves the process of transforming a product design from the prototype stage to mass production. Companies in this industry bridge the gap between innovation and commercialization, allowing ideas and concepts to become tangible products for the market.
One significant evolution in this industry is the integration of advanced technologies in the production process. With the advent of 3D printing, rapid prototyping, and computer-aided design (CAD) software, the time and cost of developing prototypes have significantly decreased. These technologies have revolutionized the industry by enabling quicker iterations, enhanced customization, and improved accuracy in product development.
Another notable evolution is the increasing demand for sustainability and eco-friendly products. Market trends have shown a shift towards environmentally conscious products, leading to the rise of sustainable manufacturing practices in the prototype to production industry. Companies are now focused on minimizing waste, reducing energy consumption, and utilizing renewable resources in their production processes.
Furthermore, there has been a substantial growth in the outsourcing of prototype to production services. Companies are increasingly relying on specialized firms to handle their product development and manufacturing needs. This trend allows companies to focus on their core competencies while leveraging the expertise and capabilities of these external service providers.
In recent years, the prototype to production industry has also witnessed a surge in the development of smart and connected products. With the advent of the Internet of Things (IoT) and advancements in embedded systems, there is an increasing demand for products that can collect and communicate data. This trend has led to the integration of sensors, connectivity, and intelligent algorithms into a wide range of products, ranging from consumer electronics to industrial equipment.
Lastly, market trends have shown a growing emphasis on speed to market. With increased competition and shorter product life cycles, companies are under pressure to bring their products to market quickly. The prototype to production industry is responding to this demand by streamlining the production process, adopting agile methodologies, and utilizing efficient supply chain management practices.
In conclusion, the prototype to production industry has undergone substantial evolution and witnessed various market trends. The integration of advanced technologies, the focus on sustainability, outsourcing of services, development of smart products, and the emphasis on speed to market are some key aspects that have shaped this industry. As innovation continues to drive product development, the prototype to production industry will likely witness further evolution and adaptation to meet the demands of the market.
Custom Private Labeling and Branding Opportunities with Chinese prototype to production Manufacturers
Chinese prototype to production manufacturers offer excellent opportunities for custom private labeling and branding. With their expertise in manufacturing various products, they can help businesses turn their ideas into reality while maintaining the desired brand image. These manufacturers are well-versed in creating prototypes and can assist in refining product designs, ensuring they meet the brand’s specifications.
One advantage of partnering with Chinese manufacturers is their ability to provide a wide range of customization options. Whether it’s packaging, color schemes, logos, or product features, they can seamlessly integrate the brand’s image into the final product. This level of customization allows businesses to create unique and memorable products that stand out in the market.
Furthermore, Chinese manufacturers offer cost-effective solutions, making private labeling and branding more accessible for businesses of all sizes. By leveraging their efficient production processes, businesses can benefit from reduced manufacturing costs without compromising on quality. With access to advanced technology and skilled labor, Chinese manufacturers can deliver high-quality products that align with the brand’s vision.
Working with prototype to production manufacturers in China also ensures timely delivery and consistent production. They have established supply chains and logistical expertise to handle production volumes, ensuring that businesses can meet customer demands promptly. Additionally, the manufacturers prioritize quality control throughout the production process, maintaining product consistency and reliability.
By collaborating with Chinese prototype to production manufacturers, businesses can enjoy various benefits, including customization, cost savings, and reliable production. These opportunities allow brands to establish a unique identity in the market, resulting in increased customer loyalty and brand recognition. With their expertise and capabilities, Chinese manufacturers provide the necessary support to help businesses bring their private label and branded products to market successfully.
Tips for Procurement and Considerations when Purchasing prototype to production
When transitioning from prototype to production in procurement, there are several considerations that should be taken into account to ensure a smooth and successful process.
1. Scalability: Prototypes are typically designed for limited production runs, so it is important to assess the scalability of the product. Consider if the manufacturing process can handle larger volumes without compromising quality or cost-effectiveness.
2. Supplier Evaluation: Evaluate your current suppliers and assess their capabilities to handle production requirements. Identify any potential risks and ensure that your suppliers have the necessary capacity, experience, and quality control measures in place.
3. Cost Analysis: Analyze the cost implications of scaling up production. Consider economies of scale, material costs, and any additional manufacturing processes required. Negotiate pricing with suppliers and explore alternative sourcing options to optimize costs.
4. Quality Control: Establish stringent quality control measures to ensure that the production units meet the desired specifications. Implement quality control checks at various stages of the production process to identify and address any manufacturing defects early on.
5. Lead Times: Prototype development may have had longer lead times compared to production. Consider lead times required for sourcing raw materials, production, and logistics. Work closely with suppliers to reduce lead times and ensure timely delivery.
6. Intellectual Property Protection: When moving from prototype to production, intellectual property protection becomes crucial. Review and update confidentiality agreements, trademarks, patents, and licenses to safeguard your product from unauthorized replication or infringement.
7. Supply Chain Management: Establish an efficient supply chain to ensure a steady flow of raw materials and components. Evaluate the reliability of suppliers and consider implementing buffer inventory to mitigate any potential disruptions.
8. Regulatory Compliance: Ensure that the product complies with all relevant regulations and standards for production and distribution. Understand the legal requirements associated with the product and seek necessary certifications or approvals.
9. Continuous Improvement: Even after transitioning to production, continuous improvement should be a priority. Monitor feedback from customers, conduct regular quality audits, and work closely with suppliers to identify areas for enhancement and optimization.
By considering these procurement tips and thoroughly evaluating each aspect of the transition from prototype to production, you can streamline the process, minimize risks, and ensure a successful and efficient transition.
FAQs on Sourcing and Manufacturing prototype to production in China
1. How can I find a reliable manufacturer in China for my prototype to production needs?
You can start by researching manufacturers online, attending trade shows in China, or using sourcing platforms to connect with reputable suppliers. It is crucial to conduct thorough due diligence, including checking references, visiting the manufacturer’s facilities, and discussing your project requirements in detail before making a decision.
2. What are the typical lead times for sourcing and manufacturing prototypes in China?
Lead times can vary depending on the complexity of the product, the availability of materials, and the manufacturer’s production capacity. Generally, sourcing and manufacturing prototypes in China can take anywhere from a few weeks to a few months. It is essential to communicate your timeline requirements with the manufacturer upfront to ensure they can meet your deadlines.
3. How can I ensure the quality of prototypes and production runs in China?
To ensure quality, it is essential to work with a manufacturer that has a proven track record of producing high-quality products. You can request samples, visit the manufacturer’s facilities, and perform quality inspections during the production process. It is also critical to communicate your quality standards and expectations clearly with the manufacturer to avoid any misunderstandings.
4. What are the potential challenges of sourcing and manufacturing in China?
Some potential challenges of sourcing and manufacturing in China include language barriers, cultural differences, intellectual property concerns, and distance. It is crucial to address these challenges by working with a reputable sourcing agent or manufacturer, developing clear contracts and agreements, and taking necessary precautions to protect your intellectual property.
In conclusion, sourcing and manufacturing prototypes to production in China can be a cost-effective solution for businesses looking to bring their products to market efficiently. By working with reputable manufacturers, communicating effectively, and addressing potential challenges, you can successfully navigate the process and achieve your production goals.
Why contact sourcifychina.com get free quota from reliable prototype to production suppliers?
SourcifyChina.com provides free quotas to connect businesses with reliable prototype to production suppliers for several reasons.
Firstly, SourcifyChina.com understands the importance of building trust and providing a risk-free experience for businesses. By offering free quotas, they allow businesses to assess the quality and capabilities of their suppliers before committing to a partnership. This helps businesses minimize the risk involved in supplier selection and ensures that they can find a reliable supplier who can meet their specific requirements.
Secondly, SourcifyChina.com aims to streamline the sourcing process and save businesses valuable time and resources. By offering free quotas, they encourage businesses to outsource their sourcing tasks to professionals who can efficiently identify and recommend suitable suppliers. This eliminates the need for businesses to spend significant time and effort searching for suppliers on their own, enabling them to focus on other core aspects of their operations.
Moreover, SourcifyChina.com recognizes the importance of providing access to a wide network of suppliers. By offering free quotas, they enable businesses to connect with a diverse range of prototype to production suppliers. This gives businesses the opportunity to explore various options and choose the supplier who best fits their requirements in terms of price, quality, lead time, and other factors.
Additionally, SourcifyChina.com aims to foster transparency and open communication between businesses and suppliers. The free quota allows businesses to discuss their needs and project details with the suppliers, ensuring that both parties have a clear understanding of the project scope and objectives. This helps establish a solid foundation for a successful partnership, laying the groundwork for effective collaboration throughout the production process.
In summary, SourcifyChina.com offers free quotas to reliable prototype to production suppliers in order to build trust, streamline the sourcing process, provide access to a wide network of suppliers, and foster transparency and communication. This benefits businesses by minimizing risks, saving time and resources, and facilitating a successful partnership with their chosen supplier.